To Issue 128
Citation: Kingsley M, Jarman-Smith M, Billings T, “Material Selection for Next-Generation Connected Medical Electronics”. ONdrugDelivery, Issue 128 (Dec 2021), pp 16–18.
Miriam Kingsley, Marcus Jarman-Smith and Thomas Billings highlight the growing array of applications for high-performance polymers in electronic and connected medical devices and how proper material selection is crucial, providing a guide to successful material selection, going on to showcase its APTIV™ PEEK polymer film, which is well suited to meet the specific demands of next-generation connected medical devices.
“Increasingly, designers are looking to high-performance polymers for answers. Without a doubt, PEEK is one of the highest performing polymers, and one that can support multiple KERs.”
Consumer demands for the latest electronic devices, coupled with emerging radio frequency (RF) technologies, such as 5G, are creating constant pressure for more innovation. To stay ahead of the competition, products must offer more functionality, more durability, and faster and more powerful performance, all at an acceptable cost.
Crucial to this is choosing the right material. High-performance polymer technology provides the versatility and high performance necessary. Now it is possible to have the design freedom to meet today’s challenges and deliver the next generation of electronic drug delivery devices. Material selection is critical for medical device designs. This includes drug delivery – whether the device is implantable or not. There are, in fact, quite a few materials available on the market that are successfully used in drug delivery devices, and selecting the right materials can be a bigger challenge than originally thought.
MEETING MULTIPLE ENGINEERING REQUIREMENTS
Designers often define multiple key engineering requirements (KERs) when looking at developing components for next-generation drug delivery devices. For example, we know that demands for higher structural integrity, reliability, mobility and connectivity are all shaping the way that electronic components are designed. Increasingly, original equipment manufacturers (OEMs) are specifying high-performance polymer solutions to reach new levels of device performance and enhance the user experience. Some of the unique drivers for change include:
- Increased connectivity: Devices are now expected to deliver an enhanced user experience with seamless connectivity, improved interactivity and high reliability.
- More chips for smarter and smaller devices: Semiconductor fabricators are under constant pressure to produce higher performance chips in a faster cycle and with fewer defects.
- Energy efficiency and sustainability: Device manufacturers are challenged to enhance the lifespan of their products and make the manufacturing process more efficient in terms of energy consumption and waste.
Traditional materials, such as commodity polymers and metals, can be used for some applications, but what happens when there are multiple engineering requirements for components that have complex designs and need to operate with precision over a long lifetime?
Increasingly, designers are looking to high-performance polymers for answers. Without a doubt, poly-ether-ether-ketone (PEEK) is one of the highest performing polymers, and one that can support multiple KERs. PEEK has been used to achieve improved safety and durability, greater design freedom and patient comfort, and increased cost efficiency in the production of medical devices.
“Providing all the benefits of VICTREX PEEK polymer in a thin film, APTIV films can give provide the versatility and high performance needed to address complex demands and design next-generation electronic devices.”
WHEN TO SELECT HIGH PERFORMANCE POLYMERS
- High-temperature environments: VICTREX™ PEEK polymers can withstand continuous-use high temperatures and harsh chemicals; surviving anodising, wave soldering and other harsh fabrication processes.
- Mechanical strength: Superior bond strength, high strength and stiffness, good metal adhesion, allowing more design freedom with better structural integrity.
- Weight reduction: Replacing metal with VICTREX PEEK can help pack more performance into a lighter package.
- Miniaturisation: The development and production of smaller and smarter chips with more data storage and increased functionality is an ever-present trend driving the semiconductor industry.
CHOOSING THE RIGHT POLYMER FORM
PEEK-based films, fibres, coatings and composites incorporate all of the outstanding properties of VICTREX PEEK polymer in multiple formats, enabling customers to meet increasing performance demands and providing design freedom to drive innovation. Regulatory compliant implantable and non-implantable biocompatible grades enable safe, long-lasting solutions for drug delivery devices.
In addition to natural, unfilled PEEK, the polymer is also available compounded with fillers, including glass fibre and short and continuous carbon fibre, each with different characteristics for different environments.
PRODUCT SHOWCASE: APTIV™ FILMS
Providing all the benefits of VICTREX PEEK polymer in a thin film, APTIV films can give the versatility and high performance needed to address complex demands and meet the design requirements of next-generation electronic devices, including connected drug delivery devices. APTIV films have been used in over four billion mobile devices for acoustic performance and reliability.
• APTIV films can meet specific needs of different electronics applications, with a range of thicknesses from 3–360 μm ultra-thin for wear and insulation.
• APTIV films have around three times the lifespan of other polymers, such as polyarylate (PAR) or polyetherimide (PEI) films (Figure 1)
• Lower moisture absorption versus polyimide – APTIV Films provide more stable electrical properties, especially at higher (RF) frequencies.
• More ductile and less brittle compared with liquid-crystal polymer – APTIV Films have similar high (RF) frequency electrical and mechanical properties, but are more ductile and less brittle (e.g. in injection-moulding processes).
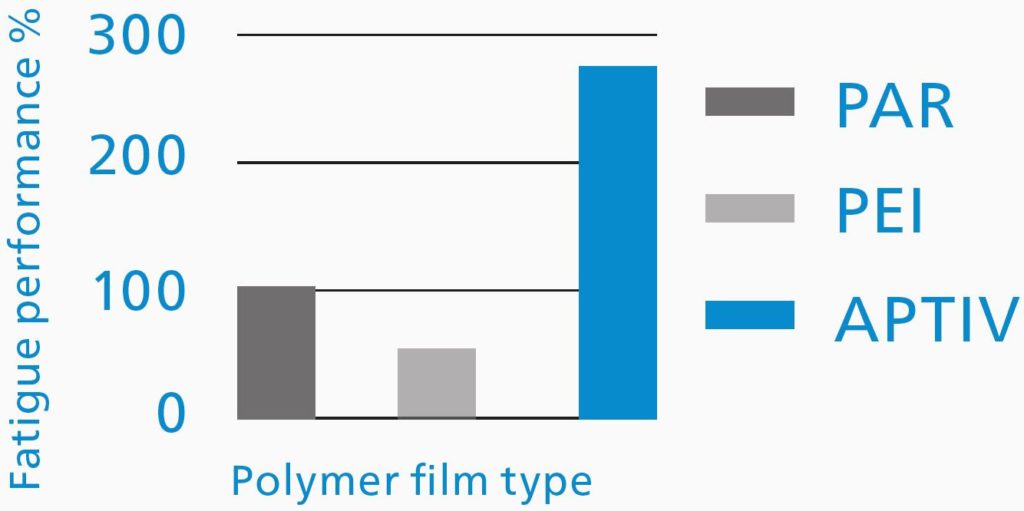
Figure 1: APTIV films have around three times the lifetime of other polymers such as PAR or PEI films.
APPLYING HIGH-PERFORMANCE POLYMER ADVANTAGE IN DRUG DELIVERY APPLICATIONS
There are limitless applications, such as insulin pens, wearables and inhalers, that can take advantage of the light weight and high durability of high-performance polymers, from battery insulations to gears and pumps, but let us focus on two:
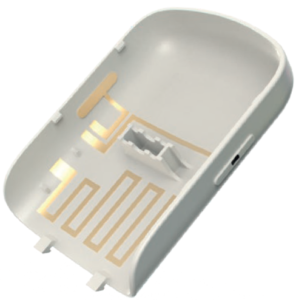
Figure 2: Structural electronics integrated into a PEEK enclosure, eliminating the need for a PCB. This enclosure is designed by Tricas (Bromsgrove, UK) to maximise the potential
of VICTREX PEEK. (Image © Copyright 2021 Victrex plc)
1) Integrated Structural Electronics and Flex Circuits
Integrated structural electronics is a space-saving concept that uses laser direct sintering into a compatible material. Figure 2 shows the concept of a casing for a wearable patch pump where the electronics are sintered directly into the casing to create an antenna to communicate wirelessly via Bluetooth. This eliminates the need for a printed circuit board (PCB), thereby increasing the available space within the device so that it can hold larger volumes of drug or be further miniaturised. PEEK has good dielectric properties with a very low dissipation factor, with only small amounts of electrical energy absorbed by the
PEEK material. The stable dielectric properties (Dk, Df) over a wide range of temperatures, humidities and RFs enable internet of things and bluetooth support. This makes PEEK radio transparent and allows the design to have an antenna on the inside for connecting to a smartphone or other device. The advantage of adding antenna tracks directly onto the surface of the material is that these antennas have great operational stability. They are not in a separate component with its own assembly tolerances, but instead are part of the device’s casing with a consistent thickness of material between them and the outside world.
2) Precision Sensors and Capacitive Switches
For many years PEEK films, such as Victrex’s APTIV film, has been used to create tactile switches and touch sensors. Again, the dimensional stability of PEEK makes switches reliable, able to retain their strength even after repetitive depressions. In the patch pump concept, the touch sensor could be used to dispense the drug precisely, using pressure to dictate the strength or volume of drug to be released. By applying PEEK film behind an LED, the capacitive switch could be made into a smart switch, perhaps by blinking to notify the user of changes to temperature, battery life or connectivity. As designers are faced with new challenges, high performance polymers, such as PEEK, offer additional choice and options for new solutions.