To Issue 136
Citation: Jelgerhuis D, “From Simulation to Spring Satisfaction”. ONdrugDelivery, Issue 136 (Aug 2022), pp 36–38.
Drew Jelgerhuis discusses the power of simulation to enhance a drug delivery device design project, including faster development times and reduced costs.
“Simulation services are a great tool with which to test and evaluate designs and thus improve time to market and reduce overall costs before even making a prototype.”
Development engineers are constantly trying to understand how their design will perform under various conditions, environments and applications. Simultaneously, project managers are trying to reduce the project’s time to market and cut costs to beat the competition. Serving both these aims, simulation services are a great tool with which to test and evaluate designs and thus improve time to market and reduce overall costs before even making a prototype.
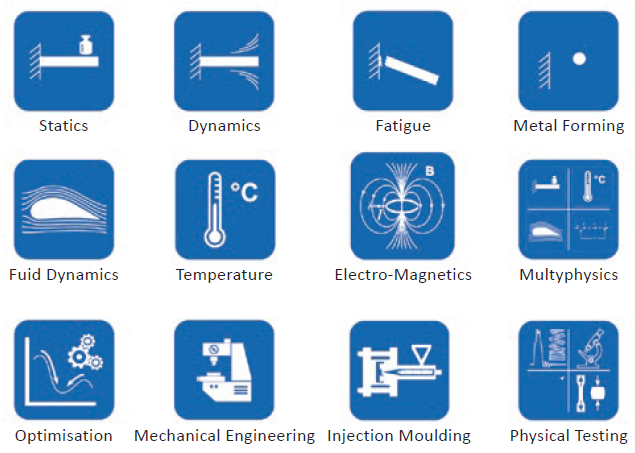
Figure 1: Scherdel’s simulation capabilities.
Scherdel Medtec is committed to providing the best engineering for your medical device components. The company’s simulation services include statics/dynamics, fatigue, metal forming, fluid dynamics, temperature, electromagnetics, multiphysics, optimisation, mechanical engineering and injection moulding (Figure 1). In addition to these simulation services, Scherdel supplements this analysis with a wide range of physical testing.
Scherdel’s simulation team performs hundreds of simulation projects every year, and the number of these numerical simulation tasks continues to grow year on year as the value of the results they offer improves with the continual advancement in software, algorithms and engineering knowledge. Over the past five years, the company has increased its number of simulation projects by over 30% annually. This is, in part, due to the significant value that it provides but also due to the growing number of types of simulation that Scherdel can perform.
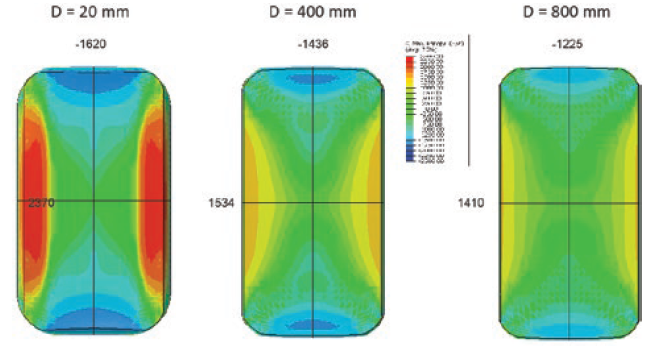
Figure 2: Simulating variation of a wire roller’s diameter.
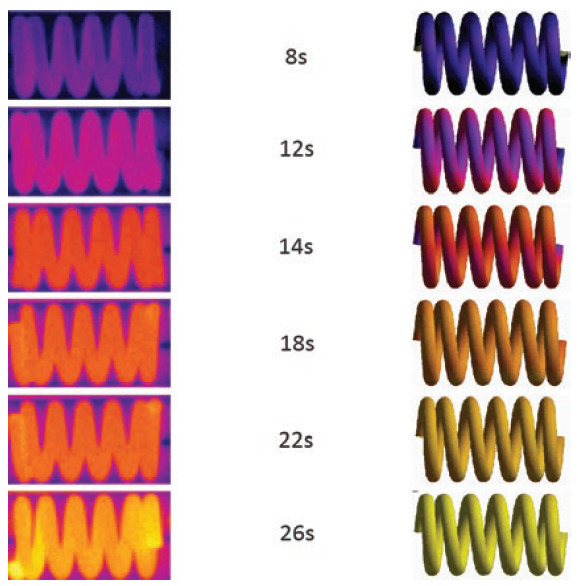
Figure 3: Simulation showing yellow/purple conduction.
Taking a simple compression spring as an example, Scherdel can simulate the wire drawing process to determine the stress levels throughout the wire before even beginning to form it into a spring. Controlling the variables from the first process can help determine and improve the performance of the simulation after the final process. For example, by simulating the diameter of the wire roller, it is possible to understand the effects on the internal stress (Figure 2). This saves expensive and time-consuming experimenting.
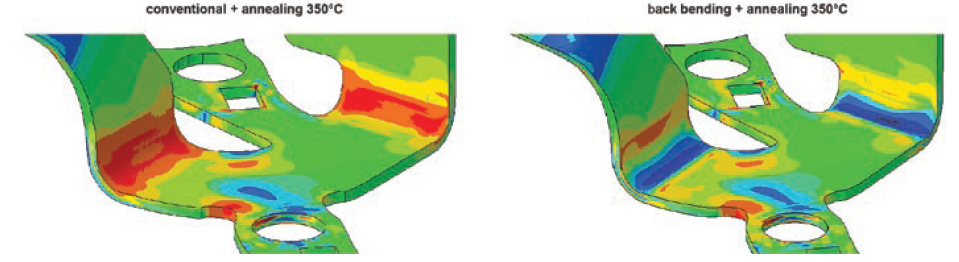
Figure 4: Annealing dispersion using temperature simulation.
Progressing into the coiling and conductive heating process, Scherdel can then determine and optimise the process for best results based on the specifications of the given spring (Figure 3). The next process may involve annealing, which Scherdel can simulate in its temperature simulation (Figure 4). Another process often used in the manufacture of springs is shot peening, where Scherdel’s manufacturing simulation can provide analysis of the process to optimise it for distribution and wear reduction.
The process of precision stamping presents many opportunities to use simulation to test various methods of manufacturing processes to improve the robustness of a given component. One such example is elucidating the difference between processes and the improvement in critical bending areas.
Another process that can be simulated for compression springs is stroke stress (Figure 5). This circumvents the need to make springs and test them over millions of cycles, and avoids the subsequent lab tests required to understand the stresses present.
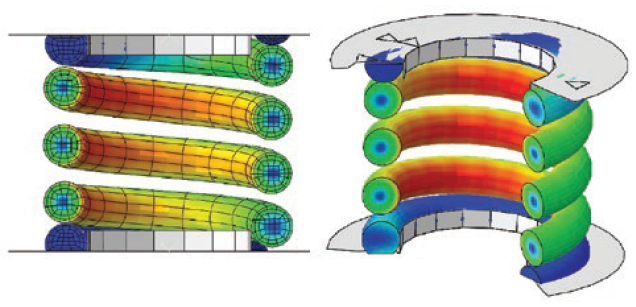
Figure 5: Stroke stress simulation.
The benefits that result from numerical simulation are as follows:
- Deviation between simulation and testing is less than 10%
- First-time-right prototypes are made a reality
- Simulation speeds up development times
- Simulation finds better solutions
- Simulation is always faster than trial and error with prototypes
- Simulation provides greater insight
- Simulation costs are investigations in fault prevention
- Co-ordinated use of simulation and testing is the fastest way to new products.
Scherdel Medtec has world-class software, engineers and the experience to tackle design challenges and shorten development cycles while improving the quality of the product and saving prototype and testing money in the project’s budget.