To Issue 137
Citation: Resker T, “Using Magnetic Sensors for Metering Drug Volume in Wearable Injectors”. ONdrugDelivery, Issue 137 (Sep 2022), pp 61–63.
Tim Resker discusses the application of tunnelling magnetoresistive sensing technology to on-body injectors, including the vital function of accurately measuring the delivered dose, as well as other functions, such as powering on the device.
“TMR magnetic sensors provide the size, low power consumption and sensitivity required to sense small, low-cost magnets, and are available in various sensing frequencies to ensure accurate capture
of shaft rotations.”
The ongoing development of new drug therapies, Internet of Things technologies and an increasing preference for self-care among patients are driving a marked increase in the use of wearable, on-body drug delivery systems. However, along with that rise in popularity have come new challenges for medical device design engineers. For instance, one fundamental requirement of a wearable drug delivery device is the accurate measurement of the volume of drug to be injected into the patient. The answer to this device design problem depends on the mechanism used to create pressure during the injection process. Two common mechanisms for “pumping” the drug inside an on-body injector device are:
- An impeller-driven pump
- A motor-driven plunger.
Let us look more closely at these two mechanisms and observe how a tiny solid-state magnetic sensor integrated circuit (IC) based on tunnelling magnetoresistive (TMR) technology (Box 1) can address the requirements of accuracy, cost, size and extremely low power consumption. It is then possible to determine what kind of engineering knowledge is necessary for implementation.
The first mechanism to examine is the impeller-driven pump. The impeller is driven by a tiny motor and generates pressure to inject the drug. The volume of drug injected by this mechanism can be calculated using the number of rotations of the impeller. To count rotations, a very small magnet can be placed on the shaft of the impeller and a very small, low-power but highly sensitive magnetic sensor can be used to detect the number of rotations of the magnet, thus providing the desired metering data (Figure 1).
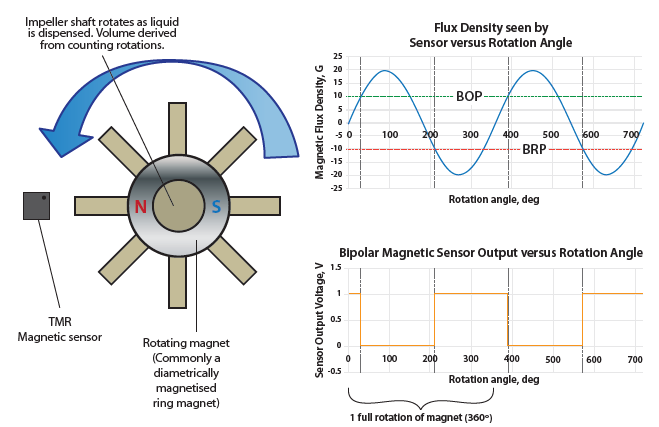
Figure 1: By detecting and counting the number of magnet rotations, the TMR sensor enables accurate measurement of drug injected by a device.
TMR magnetic sensors provide the size (1.45 mm2), low power consumption (1.9 μA for a 500 Hz sensor) and sensitivity (10 Gauss) required to sense small, low-cost magnets, and are available in various sensing frequencies to ensure accurate capture of shaft rotations. For example, RedRock® TMR magnetic sensors are commercially used in volume metering applications that have similar requirements around cost, size and accuracy, such as water utility meters and soap dispensers.
The second conventionally used mechanism for pumping a drug is a motor-driven plunger. Here, metering is achieved by sensing the travel distance of the plunger. Again, small, low-power, highly sensitive TMR magnetic sensors can be used to accurately measure that distance of travel. This is accomplished by placing a magnet on the plunger so that the TMR sensor can detect the change in magnetic flux density as the magnet moves and correlate that to distance travelled.
BOX 1: TUNNELLING MAGNETORESISTANCE
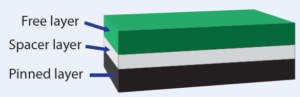
Figure 2: MTJ structure.
A tunnelling magnetoresistance sensor is comprised of a magnetic tunnelling junction (MTJ) element and complementary metal oxide semiconductor circuitry. An MTJ element is a multilayer, thin-film stack composed of a sandwiched structure of a free layer, a spacer layer and a pinned layer (Figure 2). The spacer layer (made of dielectric oxide material) separates the ferromagnetic free layer and pinned layer from one another. The electrons moving within the free layer and pinned layer planes are unable to cross the spacer layer to the opposite side. However, if magnetic flux is applied to the MTJ, the magnetism direction of both ferromagnetic layers can be switched between anti-parallel and parallel orientation. In the parallel magnetism orientation, electrons can make a quantum leap to tunnel through the spacer layer, whereupon a tunnelling current will be observed across the MTJ structure and the relative resistance of the MTJ will be changed between high resistance and low resistance.
The difference of relative resistance is the “TMR ratio” (Figure 3). The TMR ratio can reach approximately 40% at room temperature, and it is comparatively larger than other magnetoresitive technologies. This feature, which is an implementation of quantum physics, makes the ingenious TMR sensor possible, with higher sensitivity, lower power consumption and more stable characteristics.
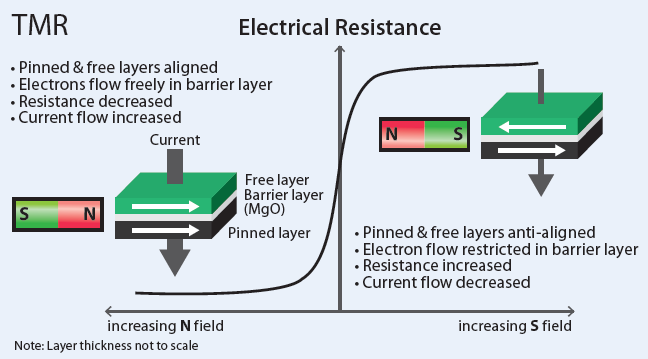
Figure 3: Tunnelling magnetoresistance mechanism and TMR ratio formula.
For this function, TMR sensors have an analogue voltage output that changes ratiometrically to the magnetic field change. The high sensitivity of TMR sensors provides high-resolution distance measurement down to a scale of 1 mm. While most analogue sensors require a higher sensing frequency and generally have a slightly higher power consumption than their digital output counterparts for a given frequency, overall power consumption can be reduced by TMR sensors that have a magnetic field strength threshold that activates the analogue output. This means that the power consumption can be extremely low until the plunger and magnet are pushed back as the injector is initially filled with the drug, at which point the analogue sensing is activated to measure the plunger movement forward to inject the drug (Figure 4).
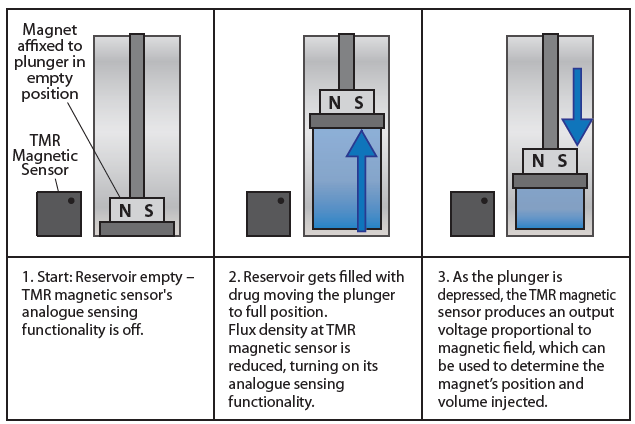
Figure 4: The TMR sensor can detect the change in magnetic flux density as the magnet moves and correlate that to distance. For this function, TMR sensors have an analogue voltage output that changes ratiometrically to the magnetic field change. The high sensitivity of the TMR sensors provides high-resolution distance measurement down to a scale of 1 mm.
“Although TMR is an ideal solution to the challenges of wearable device design, integrating a TMR magnetic sensor and magnet into
the wearable drug injector design requires specialist engineering knowledge.”
In addition to enabling accurate metering of the delivered drug volume, TMR magnetic sensors can be useful for other functions, such as powering on wearable medical devices. In this case, the TMR sensor detects the presence of a magnet located in the product packaging or in a component of the device, such as the applicator. Proximity sensing is another common use case for TMR sensors and applies to any situation where the proximity of a mechanical component relative to another component needs to be sensed in a reliable, low-cost manner with very little power consumption. For powering on and other proximity sensing use cases, a very low sensing frequency can be used, resulting in an average current consumption of less than 1 nA.
Although TMR is an ideal solution to the challenges of wearable device design, integrating a TMR magnetic sensor and magnet into the wearable drug injector design requires specialist engineering knowledge. Some medical design engineers shy away from using a new technology due to fears of extensive prototyping, testing and validation, which can make a project longer and costlier. However, Coto Technology offers engineering support for this exact purpose – vastly simplifying the process and ultimately speeding up time to market. Coupled with and enhanced by experienced medical design assistance and simulation capabilities, Coto’s RedRock® TMR sensor “comes with” the specialised knowledge of the sensors, magnetics and simulation tools that are able to provide design verification.