To Issue 137
Citation: Beckstoffer D, “Key Considerations When Specifying a Motion System for Wearable Injectors”. ONdrugDelivery, Issue 137 (Sep 2022), pp 58–60.
The reliable performance of a wearable drug delivery device is understandably paramount, so optimising the motion solution that drives it is crucial. Dave Beckstoffer discusses how best to achieve this and ensure the best match between the motion solution and the characteristics of the specified drug or drug range.
“The development of the motion system requires an engineering approach specific to the drug or drug range in question.”
For any medication that is intended for administration over a prolonged period, a wearable delivery system is an advantageous option, both in terms of convenience and comfort for the patient, and in reducing the burden on healthcare professionals. Crucial to the design of a wearable drug delivery device is the motion system, comprising the motor, gearbox and mechanical components that drive the drug delivery pump.
The development of the motion system requires an engineering approach specific to the drug or drug range in question. To optimise this process, as well as accelerate time to market and maximise cost efficiency, it is important for the drug delivery device original equipment manufacturer (OEM) to engage with the motion system designer at the earliest opportunity (Figure 1).
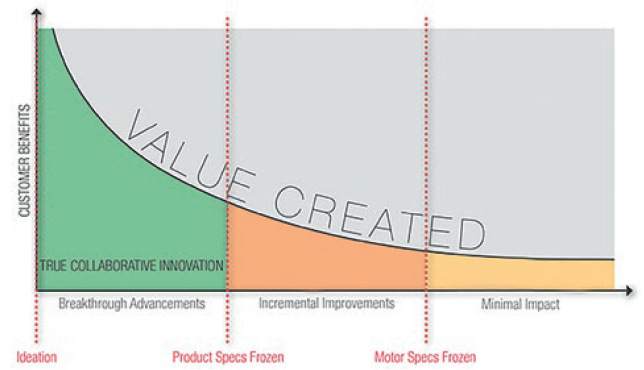
Figure 1: Engaging with a motion solution partner early in the development process can minimise the overall development time.
Through early integration with the project, the motion system can be designed according to the characteristics of the drug that will be administered, taking into account its optimum delivery requirements, as well as the practical needs of the patient who will have to live with the device. This evaluation should take place as the first stage of the motion solution selection and pump development.
MOTION SOLUTION SPECIFICATION FOLLOWS DRUG DELIVERY REQUIREMENTS
A fundamental step in motion solution design is to clarify the time span of drug delivery. A broad consideration at this stage is whether the delivery device is disposable or reusable. As well as considerations of patient comfort, the selection of a reusable or disposable device often comes down to economy. Motion systems selected for reusable devices will need to be more durable than their disposable counterparts. This naturally means that they are more costly.
Typically, it is more economical for drugs administered over a short time span – for example, a single dose over 24 hours – to use a disposable patch pump. Where the drug will be administered regularly over a period of months, or even years, then the total costs will be minimised by specifying a reusable pump. Reusable delivery systems may also be specified to administer more valuable drugs, where the importance of reliable performance is greater.
Another determining factor in how the motion system is specified is the process of a delivery cycle. This process can be divided into stages, from power up of the system, to engagement with the cartridge, through to the actual delivery. While each stage must be factored into a motion solution’s design, the overall time span of the full delivery cycle has the greatest focus.
The cycle may involve administering the drug over a series of intervals (20 seconds on and a pause of 40 seconds, for example) or simply consist of a single, uninterrupted delivery. Whatever the cycle requirements, it will impact specification of the motion solution’s speed, torque and feedback control capabilities. Similarly, understanding drug viscosity for the application dictates the force required to depress the plunger, and therefore the required torque output of the motor and gearbox.
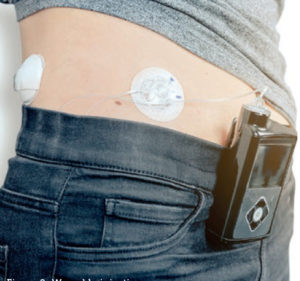
Figure 2: Wearable injection pump.
For the system designer, it is also important to understand the interconnection between the life requirement of the pump and the motion solution that will drive it. Reliability is critical for patient care and, while durability and lifetime must be guaranteed, clarifying such requirements with the delivery system OEM enables the motion system designer to target the most appropriate design characteristics at the most appropriate price point. For example, a wearable delivery device (Figure 2) might have an intended lifetime use of five years but, depending the anticipated frequency of use and number of cycles required, the motor might only need to last for 1,000 hours of pump activation on-time.
Motion system design also has to consider efficiency, which is key to minimising the battery size and weight for the wearer. The motion solution engineering team can help to optimise the specification by advising on the most efficient duty cycles. For example, if the pharmaceutical manufacturer requires drug delivery across a five-hour period, efficiency will be optimised if the delivery mechanism operates in pulses, compared with continual operation at a lower speed.
“Motion solution development for wearable injection devices depends on the specification of the drug and the patient delivery needs.”
MOTION TECHNOLOGY FOR WEARABLE SYSTEMS
To fulfil the requirements of wearable drug delivery systems, brush direct current (DC) motors are typically the optimal choice. Most importantly, a brush DC motor provides high power density and can fulfil the speed and torque requirements for virtually all drug types. They are compact and lightweight, enabling integration within a small footprint, which, as the motor design is energy efficient, helps to minimise battery size while maximising charge life. A coreless design (also known as “ironless”) increases efficiency still further by removing the potential of iron losses, which have a detrimental impact on energy use, thermal regulation and performance.
As a result of a brush DC motor’s simple design, relative to other motor types, it is both reliable as a drive mechanism for wearable drug delivery systems and straightforward to control. Its speed is typically controlled by pulse width modulation (PWM), which regulates the voltage delivered to the motor by the OEM’s control device, while its torque is typically generated in a linear relation to speed. To control the torque and speed relation to suit the demands of the time cycle and drug viscosity, the brush DC motor is typically paired with a spur gearhead (Figure 3). This design is efficient and can achieve the gear reduction required to suit a range of viscosities. Importantly for the patient, the design also enables quiet operation, with fewer moving parts compared with a planetary design.
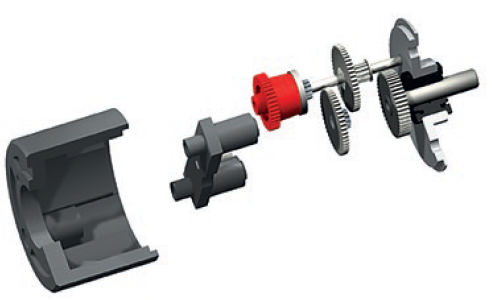
Figure 3: Spur gearhead exploded view.
The accuracy of speed and torque control that can be achieved with a brush DC motor and spur gearhead is ideal for wearable drug delivery solutions, even for pulse duty cycles. An encoder (Figure 4) can provide feedback as required to ensure accuracy and, dependent on the need for redundancy, the motion designer can also advise the OEM on safeguards that protect against current spikes.
The extent of control required is a balance between performance and cost, which is another advantage of brush motor technology. Alternatively, a brushless DC motor (BLDC) might be necessary when dealing with the very high torque requirements that are needed to deal with the highest viscosities, or when very high gear ratios are needed for the most precise control. However, these requirements are rare. The higher cost of a BLDC motor, combined with the additional cost needed for brushless electronic commutation, means that this technology is generally not cost effective for a wearable drug delivery device.
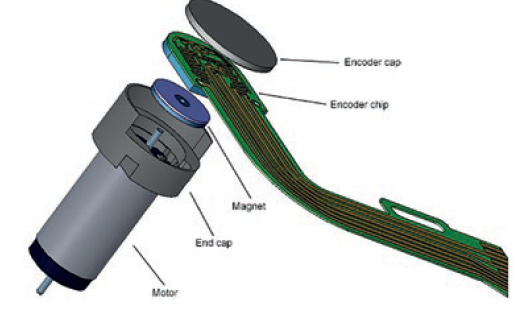
Figure 4: Encoder exploded view.
SPECIFIC DESIGN NEEDS
General customisation for wearable injection systems means reducing the voltage requirement down to 3V to take into account their low-power and high-efficiency needs. However, specific customisation for each project is nearly always required for the motor and gear combination relative to the torque range. Some delivery devices are designed to administer one particular drug, meaning that the motion solution needs to be optimised for a specific set of characteristics. Alternatively, an OEM might develop a wearable delivery device that can handle a range of drug types and suit a variety of pharmaceutical manufacturers. In this case, the motion solution needs flexibility to cover the force and cycle time requirements of various drug specifications, particularly regarding viscosity. As such, expertise in motion solution development is a key part of achieving a balance that accommodates both the lowest and highest viscosity ranges, while also maintaining the optimum efficiency of the average.
Whether the motion solution is developed for a single drug or designed to deal with many, the specialised design integration of the motor (Figure 5), gearbox and encoder demonstrates the advantage of designing an integrated motion solution sub-assembly, rather than treating each component individually. This approach will optimise performance specific to the drug or drug range requirements, with all components developed in synchrony towards a unified objective. It also reduces the dependence on internal design expertise to integrate separate components, as well as reducing the resources needed for manufacturing and assembly processes.
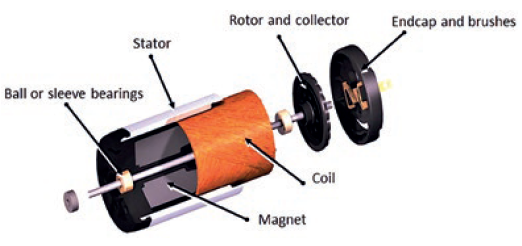
Figure 5: Brush DC motor exploded view.
When engaging with a motion solution partner, it is advantageous to do so as soon as possible in the development process in order to minimise the overall development time. As the motion solution specification criteria are extensive, the sooner the designer is involved, the more efficient the design revision process is.
This approach provides greater awareness, sooner, over any limitations or compromises, and it can also uncover unforeseen advantages to improve or speed up the design. While a period of two years from concept to design confirmation is typical, working in partnership from the outset with experienced engineers can speed up this process. This approach increasingly applies to disposable pumps as well as reusable designs. Disposable devices are starting to move away from commoditised components to a designed motion solution because it can be more cost effective in the long term. As an increasing number of drugs are administered by wearable systems, including higher-cost medications, sub-optimal delivery as a result of low-cost motors and gearboxes can negatively impact patient outcomes, as well as product value.
Motion solution development for wearable injection devices depends on the specification of the drug and the patient delivery needs. The drive mechanism is integral to the effectiveness of delivery for the patient and, for this reason, a partner in development will help the OEM arrive at the best solution. With the right partnership, it can also help the OEM get there faster.