To Issue 142
Citation: “Product Showcase: New Requirements for Injection Devices Make Advanced Testing Solutions Necessary”. ONdrugDelivery, Issue 142 (Feb 2023), pp 112–114.
With a drastic increase in administered vaccine doses in recent years, as well as the growing demand for biopharmaceuticals, needle-based injection systems with different injection volumes are becoming increasingly important. From disposable and prefilled syringes (PFSs) with active and passive safety systems to pens, autoinjectors and on-body delivery systems (OBDSs), there is currently a wide range of medical devices available.
“All injection products are subject to strict use and hygiene requirements and must be carefully and critically examined in accordance with corresponding standard requirements.”
These products are extremely important regarding patient treatment and must therefore adhere to high quality standards. Another reason for the increase in injectable products is the growing trend of patient at-home drug self-administration – an application which requires injection devices that are safe and easy to handle.
All injection products are subject to strict use and hygiene requirements and must be carefully and critically examined in accordance with corresponding standard requirements.
Intelligent test methods from ZwickRoell guarantee that the above-mentioned medical devices meet their intended purpose. ZwickRoell testing systems feature a high level of modularity, the option to choose between partial and full automation, and compliance with corresponding standards and several US FDA requirements.
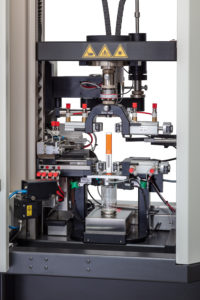
Figure 1: Testing system for multiple tests on autoinjectors.
TESTING SYSTEMS FOR AUTOINJECTORS
The latest FDA and ISO 11608-5 requirements specify autoinjector cap removal testing that is dependent on how it is described in the patient instructions for use (IFU) guidance. Most recently, this applies to cap removal before injection, which now often occurs in an upward motion. With its latest expansion stage, ZwickRoell offers a multifunctional testing system that can perform every required test on one autoinjector (Figure 1).
This also includes the removal of injector caps in both a downward motion and upward motion for any autoinjector currently on the market. A further improvement included in the new expansion stage is the measurement of injection defining results using a high-resolution optical measuring system. Both injection depth and injection time are optically measured and documented using new accuracy and resolution standards.
In addition, the system offers various unique benefits, for example, reliable installation of injector-specific interchangeable parts. The poka-yoke method is a multi-part safety concept. This includes clear coding and verification of interchangeable parts using a 2D scanner and checking if the interchangeable parts are correct and in place. If this is not the case, the test sequence cannot be started.
Daily checks for all implemented sensors include the load cell, laser sensors, microphone, scale and optical measuring system. Typically, these check tests are performed daily, before the testing machine is used or when a product is changed. The results provide assurance that the sensors being used are functioning properly.
A universal cap gripper allows for the removal of different types of injector caps. Reliable weight measurement results are guaranteed by avoiding antistatic influences on the scale.
“Daily checks for all implemented sensors include the load cell,
laser sensors, microphone, scale and optical measuring system.”
Optical measurement of the injection results and video recordings of the injection process are recorded by a single camera system integrated in the testXpert III testing software. Convenient expansion options are offered through fully automated feeding of specimens using robotic systems.
Another testing system – a combination testing machine for autoinjectors and PFSs (with or without a needle shield) – provides flexibility with a small footprint.
This system offers a high level of flexibility through tool-free expansion of testing options for tests on PFSs with or without a needle safety device. Typical results include breakaway force, glide force or injection volume.
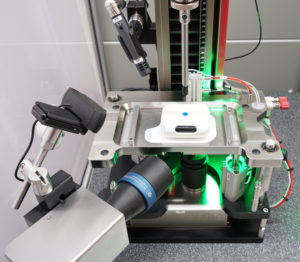
Figure 2: Testing OBDS systems to ISO 11608-6.
TESTING OF OBDS TO ISO 11608-6
The ISO 11608-6 standard describes testing of an OBDS. For higher drug volumes and/ or longer administration times, autoinjectors offer an additional injection method. For this application, the ZwickRoell testing system provides a wide range of testing options: testing of the actuation force, injection time, injection volume and needle/cannula length (Figure 2).
Additional features include recording of optical and acoustic signals of the OBDS. Furthermore, adhesive forces of the application surfaces can be determined in the upper test area. The high flexibility of this testing machine and the ability to implement specific customer requirements means additional test requirements can also be integrated for different OBDS types.
“Optical measurement of the injection results and video
recordings of the injection process are recorded by a single
camera system integrated in the testXpert III testing software.”
REQUIREMENTS ACCORDING TO FDA 21 CFR PART 11
The software is undoubtedly crucial for reliable test results. The testXpert III testing software guarantees optimised operating processes and seamless documentation. It covers every requirement related to injection-system testing. In addition, it fulfils requirements according to FDA 21 CFR Part 11.
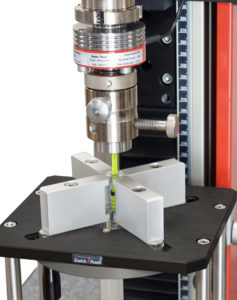
Figure 3: Universal syringe holder for various tests according to ISO 11040.
ZwickRoell deeply integrated these FDA requirements in the testXpert testing software more than a decade ago. Features are data integrity (data manipulation is not possible), user management with different access rights and lightweight directory access protocol (LDAP) access and audit trails included for test parameters.
In addition, ZwickRoell offers various qualification services. These include design qualification (DQ), installation qualification (IQ), operational qualification (OQ) and on-site services to perform these tests. A fully executed DQ, IQ, OQ service for an autoinjector testing system includes approximately 300 pages. This service is unique to ZwickRoell. Figure 3 shows ZwickRoell’s universal syringe holder for various tests according to ISO 11040.