To Issue 148
Citation: Ball R, “Increase Production Success Through Tablet Design Techniques.” ONdrugDelivery, Issue 148 (May/Jun 2023), pp 12–15.
Richard Ball considers the important features of tablet design and discusses its importance to the mass production of tablets.
“Understanding how a tablet’s design will impact the production and delivery of the final product is critical to profitable manufacturing and market success.”
Tablets are the most widely used pharmaceutical dosage form. Manufacturers choose tablets for many reasons, such as cost-effectiveness, ease of use, portability, administration and dosing accuracy. With the need to produce tablets quickly and efficiently, one of the primary considerations for tablet manufacturers is design specification.
Good tablet design is critical to producing a robust mass-produced oral solid dose. Without it, anti-counterfeiting, tool strength, tablet coating, functionality and compressibility can all be affected. Good design also helps to prevent common tablet compression problems, such as sticking, picking, capping and premature tool failure. Therefore, planning design early in the development process is important to ensure a consistent and high-quality final product is produced.
IS YOUR TABLET IN GOOD SHAPE?
Understanding how a tablet’s design will impact the production and delivery of the final product is critical to profitable manufacturing and market success. The first thing that should be considered when designing a tablet is the shape.
Although unusual and intricate shapes can be used, most manufacturers stick to the basic round or oval-shaped tablets for manufacturing ease and consistency. These shapes are preferred because they are more streamlined and are typically easier to swallow than other designs (Figure 1). Markings used for brand identity are also simpler to apply. Importantly, these shapes are robust – an important factor when mass-producing tablets.
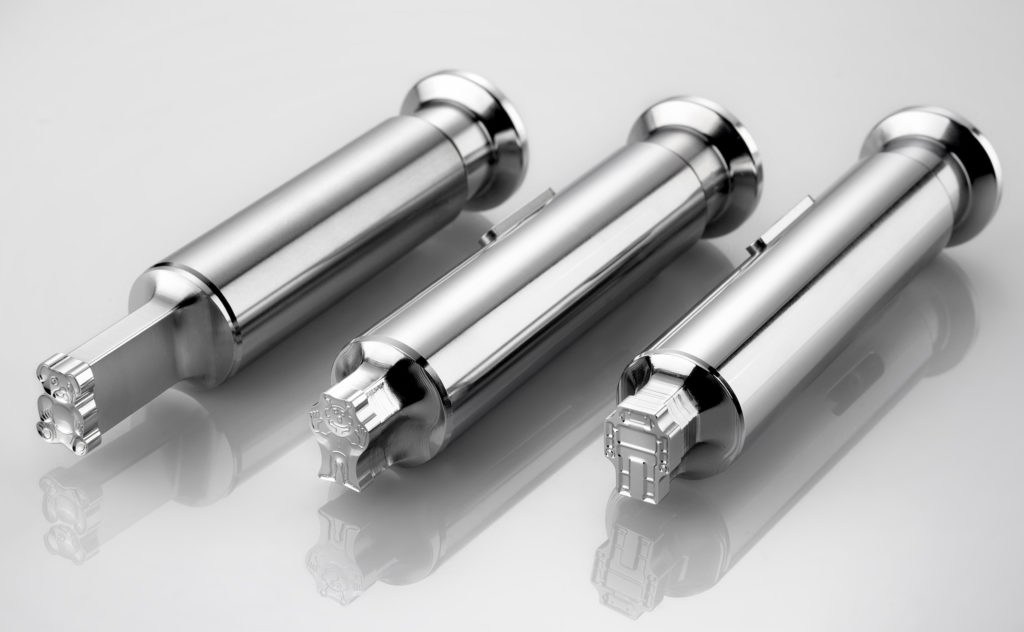
Figure 1: Designer shapes may look aesthetically pleasing, but they present a challenge during production and require specialised tool manufacturing capability.
Designer shapes may look aesthetically pleasing, but they present a challenge during production and require specialised tool manufacturing capability. Selecting an incorrect shape, or one that has been badly designed, can have a huge impact on the bottom line, as manufacturing problems will inevitably delay production.
When designing the shape, thought must also be given to the tablet size and volume. Too big and it is difficult to swallow, too small and important identification, such as embossing, cannot be added. Consideration should also be given to the type of press available for tablet manufacture, as this can limit the size of the tablet.
“If the tablet is to be coated, the profile must be correct for the manufacturing process to be successful.”
THE RIGHT PROFILE
Once a shape has been decided on, the next design consideration should be the tablet’s profile. There are different profile designs to accommodate specific requirements, including flat-faced, bevelled edge, single or double radius, ball and pill. The final decision is influenced by several factors including, but not limited to, the formulation, coating process, tablet thickness, friability, tablet hardness, packaging, swallowability and functionality. Embossing and branding requirements can also affect what profile is chosen.
If the design is to be heavily embossed, it is important to avoid tablet profiles with a deep cup, such as a ball or pill. Deep cup profiles can cause a softer core in the tablet, which, in turn, can lead to picking and erosion (Figure 2). It will also reduce the available space for the embossing itself. Using a shallower profile with a reduced cup depth is recommended, as it will allow for a larger embossing area.
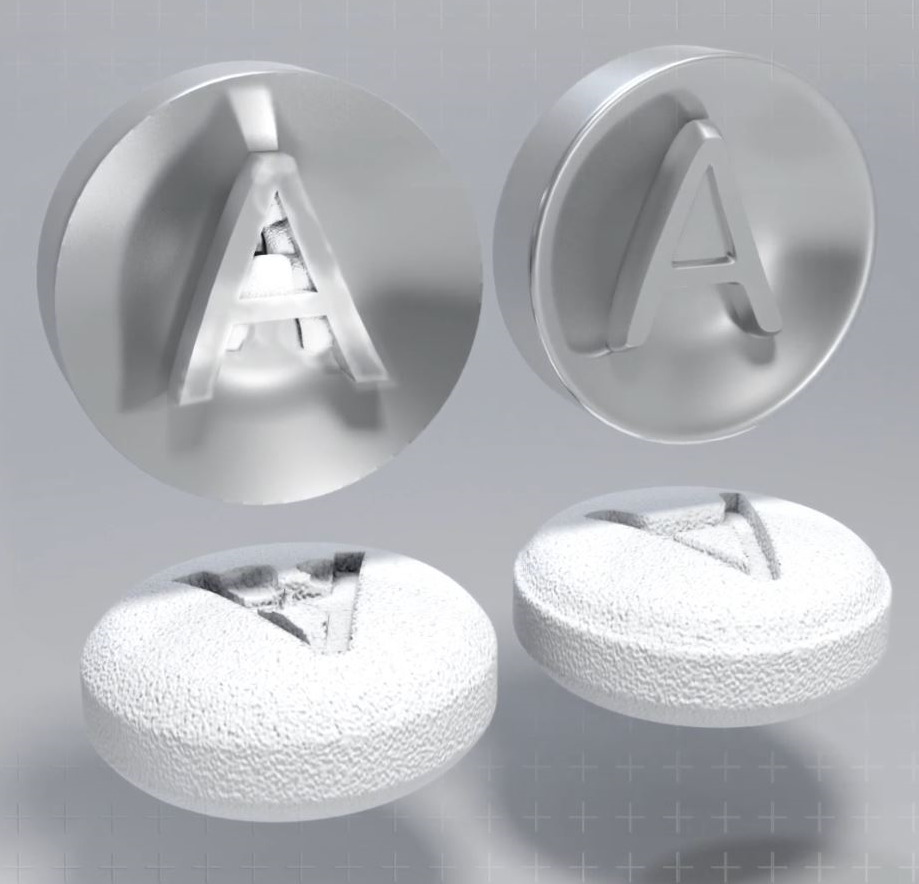
Figure 2: Good tablet design prevents common tablet compression problems, such as picking, where the compressed granule adheres to the detail on the punch face making any embossing detail indecipherable.
“The scoring or breaklines enable a tablet to be split evenly; therefore, it must be appropriately functional, as unequal breaking can result in variations in the administered dose.”
If a tablet design specifies the profile to have a deep curve, it can often cause wear on the areas of tooling with the steepest gradient. In addition, the action of compression abrades the punch tip face, removing material over time, which can lead to problems such as delamination, resulting in the tablet splitting apart. By designing in a flatter tablet profile or a double radius, formulators can help reduce the granule’s frictional action across the punch surface.
If the tablet is to be coated, the profile must be correct for the manufacturing process to be successful. The coating should be uniform and should not crack under stress. The coating solution is usually sprayed onto the uncoated tablets as they are agitated in a pan or fluid bed. As the solution is applied, a thin film is formed, which sticks to each tablet. The liquid portion of the coating solution is then evaporated by passing air over the surface of the tumbling pans. A single application may be enough to form the coating or it may develop in layers through multiple spraying cycles. This puts stress on the softer centre. Typically, the centre of a tablet is softer than the outer diameter, so when the tablet comes into contact with the coating pan and other tablets, core erosion can occur. This weakness, caused by mechanical stress during coating, can be reduced by using double-radius profiles and avoiding shallow concaves or flat profiles.
If a tablet design includes a shallow profile with hard, sharp edges, the coating process can damage the exposed perimeter of the tablet. Because the tablet cannot roll effectively in the coating pan, chipped edges and cracks within the coating are commonplace. By choosing a double radius with a balanced profile, the tablet edge will be stronger and it will roll with ease to ensure a uniform coating is achieved.
BRIDGING THE GAP
Inadequate design of branding or markings on the tablet can cause bridging. Here, the coating builds up in the embossing detail on the tablet surface, due to it not flowing easily into the contours of the design, and making the embossing indistinct. The effect of this can bridge over and create a void underneath, or in-fills the design and leaves too much coating material in the marking, resulting in poor definition.
Bridging happens for a number of reasons, but the most common causes are inadequate adhesion of the film coating, poor marking design and inappropriate coating procedure. The spray rate and drying time can also have an influence. If all these factors are not carefully considered, the adhesion characteristics of the coating will be affected. Additionally, bridging is likely if the angle of the marking design is too acute or deep. If the stroke or section of the embossing is too wide or too shallow, in-filling may occur.
TAKE A BREAK
An important consideration when designing a tablet is the breakline. The scoring or breaklines enable a tablet to be split evenly; therefore, it must be appropriately functional, as unequal breaking can result in variations in the administered dose. The level of inaccuracy can be related to the breakline design, formulation and tablet hardness (Figure 3).
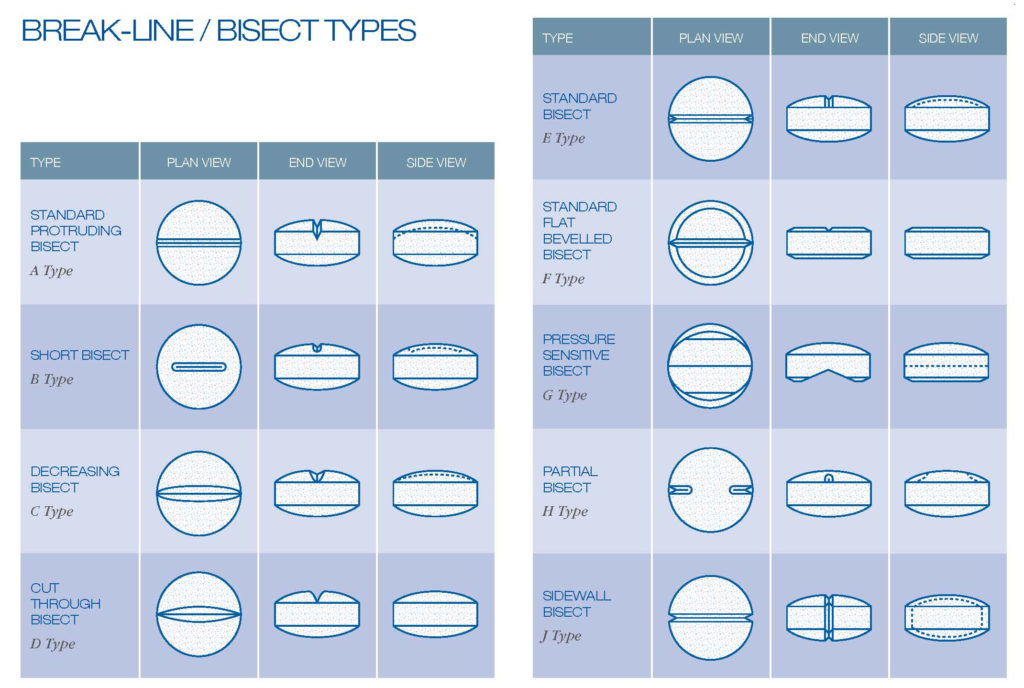
Figure 3: Scoring or breaklines enable a tablet to be split evenly; therefore, it must be appropriately functional as unequal breaking can result in variations of the administered dose.
“Applying the correct blended land will increase tablet strength and performance, resulting in higher production yields.”
If a breakline must be included in the tablet’s design, there are several factors to consider. First, is the tablet big enough to be easily separated? The breakline may need to penetrate the tablet wall while maintaining optimised radii and angles. If the radius at the bottom of the breakline is too large, it can negatively affect breakability.
Will the identification design and embossing work with the breakline? Maximising the tablet face area will help to avoid picking when the compressed granule adheres to the detail on the punch face, making any embossing detail indecipherable. Additionally, it is important to ensure that any embossing is not too close to the land edge or exceeds the cup depth, as this can cause problems during the tableting process.
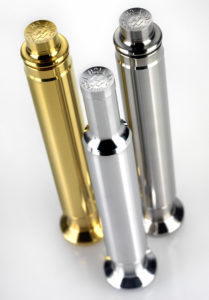
Figure 4: Tooling must have the strength, durability and performance to stand up to the high demands of tablet compression.
If a breakline is designed on both sides of the tablet, alignment is crucial, particularly when using round tooling. An anti-turn key should be installed on the upper and lower punches and the press should include key guides in the upper and lower turret. A breakline feature can protrude above the punch tip edge, so the upper and lower punches must be set correctly for effective tablet ejection and take‐off, as well as avoiding press components.
The upper and lower tip gap should also be considered, if adding a protruding breakline, to prevent the upper and lower punch from coming into contact. Where the breakline protrudes more than the gap setting, it will be necessary to manufacture the nominal length of the tooling to the top of the protruding breakline. This should be carefully considered during the design stage, as it can result in failure and damage to the upper and lower punches.
USE THE CORRECT TOOLING
Tooling must have the strength, durability and performance to stand up to the high demands of tablet compression (Figure 4). An important factor to consider is a blended land (Figure 5).
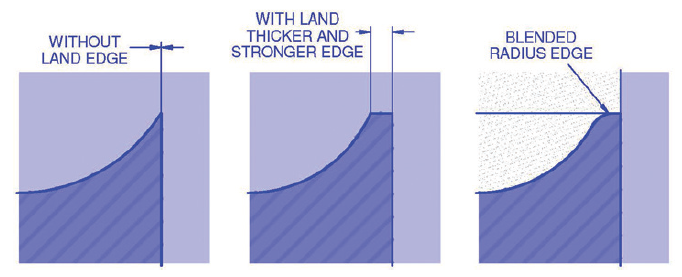
Figure 5: If a blended land is applied incorrectly a range of issues can ensue during
compression, including chipping of the tablet land during take-off, capping, the buildup
of coating on the tablets edge and, in extreme cases, punch tool breakage.
The land on a tablet is the flat lip or ridge around the perimeter of the tablet face perpendicular to the tablet’s edge. If a blended land is applied incorrectly, a range of issues can ensue during compression, including chipping of the tablet land during take-off, capping, the build-up of coating on the tablet’s edge and, in extreme cases, punch tool breakage.
Applying the correct blended land will increase tablet strength and performance, resulting in higher production yields. To correctly blend the land, a reputable tool manufacturer will ensure that the flat area on the tip edge is maintained while applying a radius (blend) to the intersection between the flat perimeter of the punch tip and the concave cup that forms the tablet profile. It is important to remember that a correctly selected and applied blended land provides benefits in handling, loading, setting, tooling strength and the visual appearance of the tablet.
DESIGN WITH CARE
Tablet design is crucial and should not be underestimated; get it wrong and it will have a huge impact on tablet production. To work successfully, the tablet manufacturer must consider important design factors, such as tablet shape, profile and breakline style.
There are many other elements to consider when designing a tablet, including factors not discussed here. Everything, from tooling material and coating to branding typefaces and anti-counterfeiting techniques, must be considered. The list is long; therefore, consulting with an expert tablet designer and tool manufacturer should be done early in the design process. This ensures that the tablet design is robust and can be cost effectively and efficiently mass-produced.