To Issue 159
Citation: Willoughby A, Tank P-S, “Reusable Versus Single-Use Devices: Trade-offs in Improving Sustainability”. ONdrugDelivery, Issue 159 (Apr/May 2024), pp 24–27.
Alastair Willoughby and Prem-Sagar Tank, explore various device trade-offs for both sustainability and cost in reusable injection devices, and consider how this compares with single-use devices.
As autoinjector requirements become increasingly diverse and pharma companies continue to look for faster routes to market – with lower costs and improved sustainability – there is an increasing trend towards devices with a reusable element. These devices work alongside a disposable element, which can range from something approaching the simplicity of a prefilled syringe (PFS) to a more complex assembly incorporating a primary container and additional features, such as needle safety and skin sensing.
Providers of reusable devices make a wide range of claims regarding their benefits over other delivery routes, in particular single-use autoinjectors. These include reductions in:
- Carbon footprint per injection
- Waste and plastic
- Manufacturing footprint and associated costs
- Shipping footprint and associated costs
- Cold chain requirements
- Time to market.
“The challenge of creating a reusable platform device that is optimised for both cost and sustainability is significantly harder than developing a single-use device with a specific purpose in mind.”
These benefits are potentially true, but it is important to compare them fairly. While a single-use autoinjector may not be the best solution for a frequent, chronic treatment, it may be more suitable when dosing is irregular or where it requires other variations in dosing patterns throughout the treatment journey. These factors all need to be considered when evaluating the benefits of single-use versus reusable products.
Another key factor that needs consideration is, of course, cost. The challenge of creating a reusable platform device that is optimised for both cost and sustainability is significantly harder than developing a single-use device with a specific purpose in mind.
WHERE IS THE “SWEET SPOT” FOR REUSE?
Finding the “sweet spot” for reusability often depends on the context of use. Taking a single-use autoinjector as a baseline to compare against, different reusable devices will have different break-even points in terms of cost and sustainability. For example, a daily-use device with a 12-month use cycle would have a different break-even point compared with one used weekly for three months.
To better understand this break-even point, device manufacturers need to consider whether patients are realistically going to maintain use of a reusable product throughout their treatment cycle. While this may be true in chronic-use situations, should patients need to alter their dosing or delivery route during their treatment, they may not use the full life of the device. As a result, the claimed benefits of device reusability may not materialise.
When evaluating whether reusability saves on carbon footprint or cost in the long term, device manufacturers also need to understand the carbon costs of different scenarios. Generally, the overall sustainability of a reusable system will depend on a balance between the complexity of the disposable elements and the reusable element, as well as the number of uses over its lifetime. Modelling tools can be an effective way to identify where this “sweet spot” lies for reuse.
SUSTAINABILITY AND COST ANALYSIS
An effective tool for understanding the sustainability of a device is lifecycle analysis (LCA), which is used to determine the carbon footprint of a product throughout its life.
To illustrate LCA in action, an example analysis was conducted based on the following questions:
- What are the sustainability implications of adding complexity to a reusable element?
- How does this compare with a single-use autoinjector?
The aim was to identify which scenarios would lead to a lower carbon footprint compared with manufacturing multiple single-use devices. Using LCA modelling tools built upon SimaPro, the analysis involved comparing the carbon footprint of four different systems:
- A simple, single-use autoinjector
- A purely mechanical, reusable device, paired with a disposable element based on a standalone PFS needle safety system
- A more complex electromechanical system with connectivity holding the PFS in a cassette format
- A PFS with a plunger rod. This represents the lower bound for the single-use device and both disposable elements.
These systems are shown in Figure 1, illustrating the disposable and reusable elements, as well as the composition of these carbon footprints.
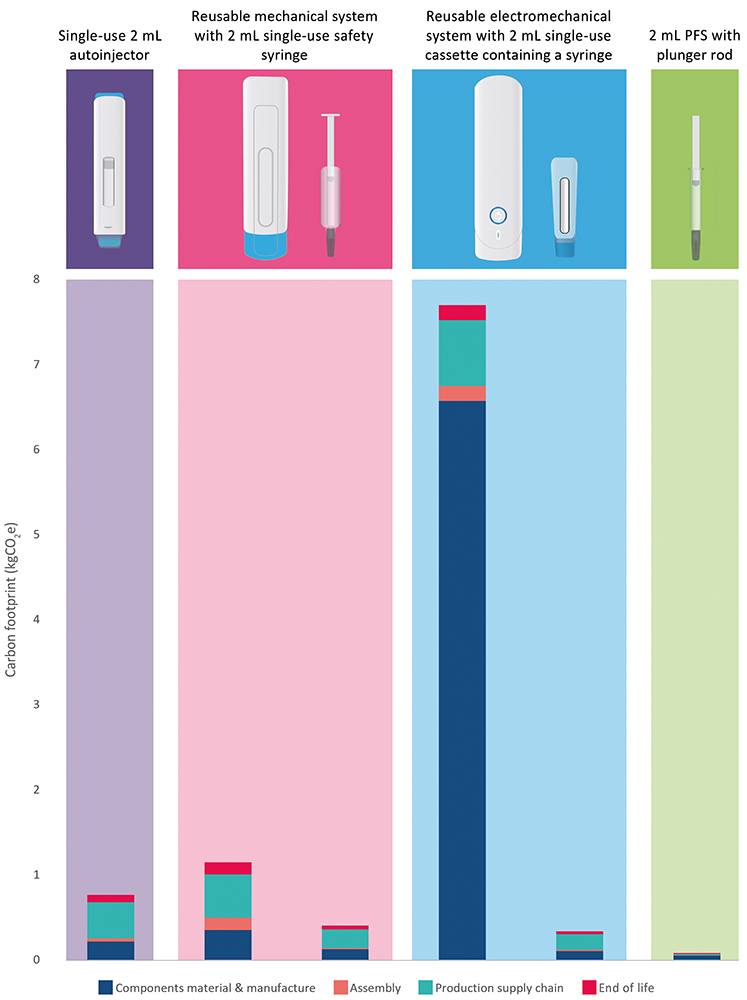
Figure 1: LCA results of three injector systems, plus lower bound comparison.
To ensure fair comparisons, it was assumed that all of the products were manufactured and transported along standard routes, using standard fossil-based plastics, East Asian manufacture and transport to Europe. LCAs are generally based on several reasonable assumptions such as these; however, these decisions can significantly impact the results. It is worth noting that LCAs should be conducted and refined throughout the development process, including sensitivity analysis around any assumptions. This can help to better understand how easily the carbon footprint can be reduced through choices such as design elements, manufacturing location and transport method.
While these figures may seem to indicate a clear preference for a single-use device, it is important to also consider the “functional unit” before drawing any conclusions. The functional unit is an LCA term that effectively describes a certain use scenario. For example, in this context it may describe the number of device combinations required to deliver the intended therapy for an average patient, such as a single reusable element paired with a number of disposable elements throughout a prescribed therapy.
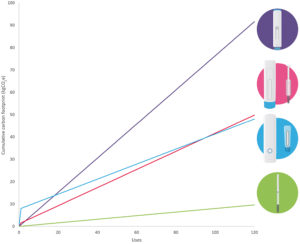
Figure 2: Carbon footprint of injection systems over 120 doses.
REUSABLE VERSUS SINGLE-USE – WHICH IS MORE SUSTAINABLE?
To better understand the results of this LCA, it is important to consider the impact of the various areas explored, including device use and packaging. The results shown in Figure 2 portray the cumulative carbon footprint for up to 120 uses.
Use Impact
Based on this assessment it appears that, over the long term, both the complex and simple reusable devices are preferable relative to a single-use autoinjector. However, if a patient is only using the device for a limited number of cycles (< 20), then a simple reusable device – or a single-use autoinjector for even lower volumes – may lead to a lower carbon footprint compared with a complex reusable device. The exact embodiment of the disposable element will have a significant impact over the long term, as this ends up being the dominant contributor to the carbon footprint.
Packaging Impact
In many scenarios, drug formulations need to be stored in a cold environment to maintain their efficacy and prolong shelf life. The refrigeration of cold chain consumes more energy than storage and transport without refrigeration. The larger the package, the more space is taken up. This, in turn, reduces the number of devices held within a given volume with a given energy usage, thereby increasing the carbon footprint of the product.
The impact of disposable elements on cold chain transport falls outside the scope of the analysis covered in this study. However, it can be estimated that the volume and mass of the packaged devices could both be reduced by 50% between a single-use autoinjector and a reusable solution. Applying changes such as this can significantly increase the number of devices in a given shipping volume or for a given mass – leading to carbon footprint reductions.
“Ensuring that packaging solutions have low-carbon materials – but are also compact to maximise packing density – is key to fully realising the potential benefits of reduced carbon footprint.”
It is important to note that factors such as these should be incorporated in the LCA, considering the efficiency of the cold chain transport as a whole – in particular in latter stages where fewer materials and devices are transported. In these situations, while mass reduction has a positive impact, there will still be a significant overhead per device. Ensuring that packaging solutions have low-carbon materials – but are also compact to maximise packing density – is key to fully realising the potential benefits of reduced carbon footprint.
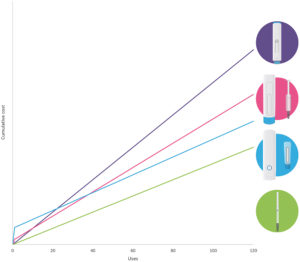
Figure 3: Cost of injection systems over 120 doses.
THE COST FACTOR
While sustainability considerations are important, businesses must also consider the cost of their devices and the ongoing cost of supplying patients. Using similar assumptions to the LCA, a cumulative cost model can be generated that indicates different break-even points, as shown in Figure 3. When comparing the three injectors with the baseline cost of the PFS, it became clear that a high proportion of the overall cost is driven by the PFS, through a combination of cost of goods and the cost of handling the filled container.
The LCA also showed that a proportion of the carbon footprint is driven by manufacturing, filling and handling of the primary container. As with all calculations, the inclusion (or exclusion) of these steps could have a large impact on the conclusions drawn from the analysis. Due to the single-use nature of the disposables, these factors must be minimised to significantly reduce cost or carbon impact. This is the best way to achieve a genuinely sustainable product, and a low-cost, low-impact primary container could provide significant benefits in the long term.
“There are several factors that can impact the sustainability of a product, including both development and user challenges.”
DEVICE FACTORS THAT IMPACT SUSTAINABILITY
When developing a reusable platform, the goal is often to create a device that is as simple as possible, while also creating a wide functional window. In practice, this can lead to over-designed products that are not only uncompetitive in terms of cost but also have a higher carbon footprint.
The question for device manufacturers is: how can you make a product that meets user needs, while making it as sustainable as possible?
There are several factors that can impact the sustainability of a product, including both development and user challenges. These include:
- Delivering high-volume and high-viscosity drugs: This requirement increases the required delivery force, meaning the device needs to provide and withstand higher forces, potentially increasing the materials and complexity of the mechanism.
- Specification of reliability in a reusable device: Devices need to be well engineered to cope with multiple use cycles. However, it is also important to ensure that they are not over engineered. One option may be an end-of-life specification and higher conditioning to mimic longer-term use conditions. Additionally, many cycles of user interaction and potential misuse must also be considered – ensuring users are guided appropriately and that components are robust enough.
- Design for end of life: It is important to consider how to dispose of both the reusable and disposable elements, each of which bring their own opportunities and challenges. The larger footprint associated with the reusable elements, assuming they remain uncontaminated, means that there is more potential for take-back schemes to help reclaim materials and give them a new life. As already discussed, there may be more carbon associated with the disposables over a number of doses. While there are challenges in handling contaminated sharps, steps could be taken to make their disposal more sustainable, such as employing novel waste streams into the take-back schemes.
- Ensuring a simple and clear user interaction: Two-step autoinjectors set a high standard to improve on. This means it can be a challenge to create a reusable device with similar simplicity. Considering user interactions and appropriate design cues from an early stage can reduce frustration and potential misuse with the final product.
- Appropriate feature set: Having a reusable element can lead to feature creep, adding more functionality with small incremental additions each time. While adding screens and connectivity may have benefits for some user populations, this can also significantly change the cost and sustainability models of the product.
MAKING DEVICES MORE SUSTAINABLE
To address these factors, there are several steps manufacturers can take. It is useful to build an understanding of the market and ensure that any market trade-offs are considered with respect to cost and sustainability metrics throughout the development process. For example, patients with chronic therapy may prefer reusable devices, while patients with occasional therapy may be more accepting of single use devices.
It is important to be clear on what the requirements are for a successful product and what the “stretch goals” are – the impact of these additional goals on baseline costs and sustainability metrics should be considered. For example, the requirement to deliver a wider range of volumes and viscosities may increase cost and complexity.
When it comes to the development stage, it can be useful to create a modular product with the potential to interchange elements to increase or reduce functionality. This might involve designing the device so that it can work with a low- or high-force spring, for example. Doing so may lead to cheaper and more efficient production, resulting in a more sustainable product.
CONCLUSION
Reusable elements can help reduce the carbon footprint of frequently delivered drugs relative to single-use autoinjector systems. However, this is not necessarily the case for all use scenarios, particularly for shorter dosing regimens. Ultimately, device manufacturers should consider the cost and impact of meeting wide user and product needs versus providing a sustainable device at an appropriate financial cost.