Citation: Cordier S, Brocco B, Chardonnet, Bauer E, “Machinability of ETFE-Film-Coated Prefilled Syringe Plungers with Vent-Tube Insertion”. ONdrugDelivery, Issue 163 (Jul 2024), pp 30–34.
Sebastien Cordier, Benjamin Brocco, Audrey Chardonnet and Edgar Bauer discuss the results of tests on the performance of Aptar Pharma‘s PremiumCoat® syringe plungers on high-speed fill-finish operations with vented insertion.
Injectables are the second most common administration route for medicines – and overwhelmingly dominant in vaccine and biologics delivery. However, the development and commercialisation journey are complex and require drug developers to consider a wide range of factors to ensure that the drug is efficient, stable over time and can be taken from the bench to commercial manufacturing scale. Among these factors, the choice of primary container system is vital, as the drug is in direct contact with both the container itself and the rubber closure component.
Over the past decade, drug developers have been striving to deliver improved outcomes for patients while also addressing previously unmet therapeutic needs, which has been made possible with the normalisation of biologic drug technologies such as monoclonal antibodies, recombinant proteins and nucleic acids. However, the nature of these large molecules makes them highly sensitive and consequently increases the uncertainties associated with their development, which pushes pharma companies to adopt risk-mitigation strategies.
Closure component developers have been collaborating with pharma companies to support biologic development and have introduced film-coated rubber solutions for vials and prefilled syringes (PFSs). Aptar Pharma’s PremiumCoat® solutions combine a state-of-the-art bromobutyl formulation with a market-proven ethylene tetrafluoroethylene (ETFE) film that is positioned at the drug/rubber interface, where it acts as a barrier that limits the transfer of extractables and leachables (E&L) into the drug product.1 The PremiumCoat® platform includes vial stoppers (13 mm and 20 mm formats), syringe plungers (1 mL* and 1–3 mL formats), a wealth of supporting data and a broad range of services to ensure that drugs remain stable and safe throughout filling, storage2 and patient administration.
“Besides ensuring their drug remains safe at all times, pharma manufacturers must ensure that their choice of components and container is compatible with their operation.”
Besides ensuring their drug remains safe at all times, pharma manufacturers must ensure that their choice of components and container is compatible with their operation, whether it is for vial or PFS filling. For PFS plungers, this machinability encompasses all the steps, from the movement of the components into the vibrating bowl to their travel through the railings and final insertion into the syringe barrel, using either vent-tube or vacuum insertion. When it comes to syringe components, drug fillers reported that, after vent-tube insertion, a market reference for ETFE-film-coated plungers displayed film damage, such as tears or ripples, which had the potential to impair the barrier effect of the film.
The compatibility of PremiumCoat® syringe plungers with both vent-tube and vacuum insertion methods has been previously demonstrated, showing that all three ribs of the plungers come into contact with the glass barrel to ensure container closure integrity while enabling easy drug delivery.3 To reinforce understanding of machinability, Aptar Pharma collaborated with Bausch + Ströbel (B+S), which performed a series of tests to further assess the compatibility of the PremiumCoat® 1–3 mL plunger with its widely used high-speed filling lines, without requiring equipment change.
“The plungers demonstrated optimal machinability in the vibrating bowls and through the distribution system.”
In this study, the plungers demonstrated optimal machinability in the vibrating bowls and through the distribution system. They could be inserted into the syringe barrels using the vented method without requiring excessive force, while also limiting the temperature increase of the vent tube, which is a known particle generation factor on such filling lines. Taken together, these data confirm that PremiumCoat® is ideally suited to enable high-speed fill-finish operations while preserving the integrity of the drug, making it an ideal solution for new drug development, as well as second- sourcing projects.
RESULTS
All subsequent tests were conducted on Aptar Pharma’s PremiumCoat® 1–3 mL syringe plunger, processed on an SFM5110 fill-finish machine that B+S equipped with a sorting bowl, selection and orientation devices, feed tracks and vent-tube insertion. The cycle time was set at 960 ms – the required cycle time to process syringes at a maximum capacity on all syringe filling and stoppering machines by B+S.
PremiumCoat® 1–3 mL Syringe Plungers Reach the Target Sorting Rate from 50% Machine Sorting Speed
The first step of the filling operation takes place when an operator feeds the sorting bowl with the plungers. The vibration of the bowl delivers the plungers into the feed tracks, passing through the plunger gates to ensure that all plungers are oriented appropriately.
To evaluate the machinability of the PremiumCoat® 1–3 mL syringe plunger on the sorting steps, the plungers were placed in the vibrating bowl and the vibrating bowl tested at sorting speeds from 30% to 70%. The number of plungers processed per minute was recorded at every 10% increment of sorting speed and the target rate of sorting defined at 350 plungers/min for a five-headed filling machine.
Figure 1 shows that, at 30% sorting speed, about 100 plungers are processed every minute. Although an increase of the sorting speed to 40% increased the sorting rate by 60%, the subsequent increase to 50% sorting speed multiplied the sorting rate by a factor of 2.8 to reach 480 plungers/min, well above the target sorting rate of 350 plungers/min. The sorting rate continued to increase proportionally to the sorting speed, to reach a value of 560 plungers/min at 70% speed.
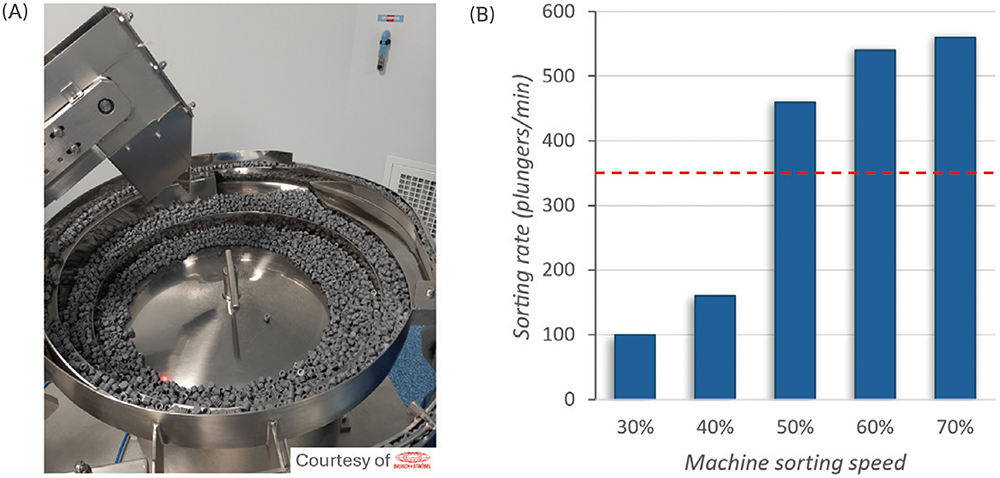
Figure 1: Sorting rate with PremiumCoat® 1–3 mL syringe plunger in vibrating bowls. Sorting bowl with PremiumCoat® 1–3 mL syringe plungers (A). Sorting rate of PremiumCoat® 1–3 mL syringe plungers, measured as a function of the sorting speed (B). The target sorting rate was defined at 350 plungers/min.
“During all operation, no issue was observed; the plungers distribution, feed track and plunger gates worked as intended with the stoppers.”
During all operation, no issue was observed; the plungers’ distribution, feed track and plunger gates worked as intended with the plungers. No plunger got stuck in the sorting bowl. These results indicate that the design of the PremiumCoat® 1–3 mL plunger and its physical properties enable easy machinability and high efficiency on filling lines, even when operating at 50% sorting speed with the machine used.
PremiumCoat® Did Not Cause Abnormal Heating of the Vent Tube During Filling Operations
Once the plungers have been distributed into the tracks, they are delivered to the vent tube for insertion into the syringe barrel. In principle, the plunger is forced through the vent tube, which has a smaller diameter than the plunger and the syringe barrel. Consequently, the plunger undergoes deformation and the friction between the plunger and the vent tube’s inner surface leads to an increase in temperature. An abnormal increase of the vent-tube temperature, beyond 60°C, could lead to the generation of rubber particles and jeopardise fill-finish operations.
The plungers were processed by the vent-tube insertion method at a 10 mm or 50 mm insertion depth – the 10 mm insertion depth being associated with a faster travel of the plunger through the vent tube. The temperature of the vent tube was tracked for 50 insertion cycles, over 60 seconds, using a high-resolution thermographic camera (Figure 2A).
The results in Figure 2B show that, after 30–40 cycles of vented insertion of PremiumCoat® 1–3 mL plungers, the temperature of the vent tube stabilised at 40°C and 45°C. The results are similar for both insertion depth and in every situation the temperature remained well below the maximum acceptable threshold of 60°C. The higher temperature reached for the 10 mm insertion depth can be explained by the fact that the travel speed of the plunger is faster, which would generate increased friction.
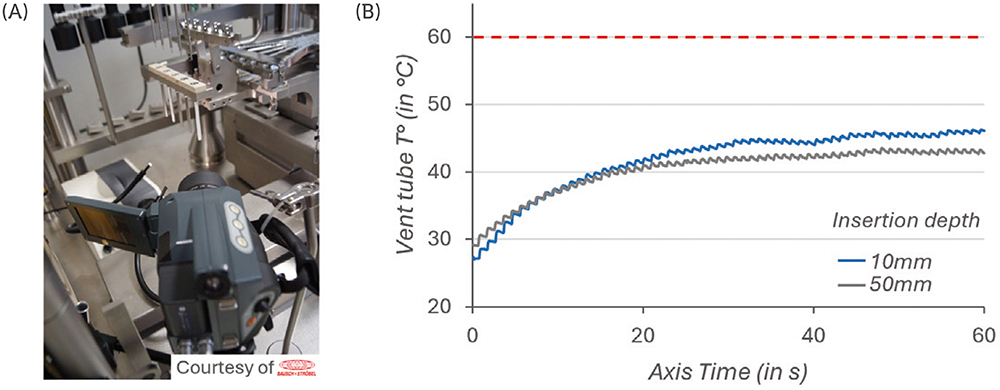
Figure 2: Measurement of the vent tube temperature during insertion cycles. Experimental set-up (A). Temperature of the vent tube measured throughout 50 successive insertion cycles (B). Two insertion depth settings were tested. The 10 mm insertion depth is associated with a faster insertion of the stopper than the 50 mm. The maximum acceptable temperature was defined at 60°C.
“These data demonstrate that PremiumCoat® plungers are well adapted for vent-tube insertion and that they are unlikely to generate particulate contamination on a fill-finish line.”
These data demonstrate that PremiumCoat® plungers are well adapted for vent-tube insertion and that they are unlikely to generate particulate contamination on a fill-finish line.
The Force Required to Pass PremiumCoat® 1–3 mL Plungers Through the Vent Tube During Insertion Is Well Within Machine Capability
The temperature increase observed during vented insertion is a direct consequence of friction between the rubber plungers and the vent tube. Although the results shown in Figure 2 seem to indicate minimal friction occurs, a complementary test was performed to directly measure the force required to insert PremiumCoat® plungers into syringe barrels using the vented method.
A force sensor was connected to the vent-tube insertion stem (Figure 3A) and the force was measured during a series of insertion cycles performed at 10%, 20%, 50% and 100% speed. The maximum acceptable insertion force was defined at 80 N.
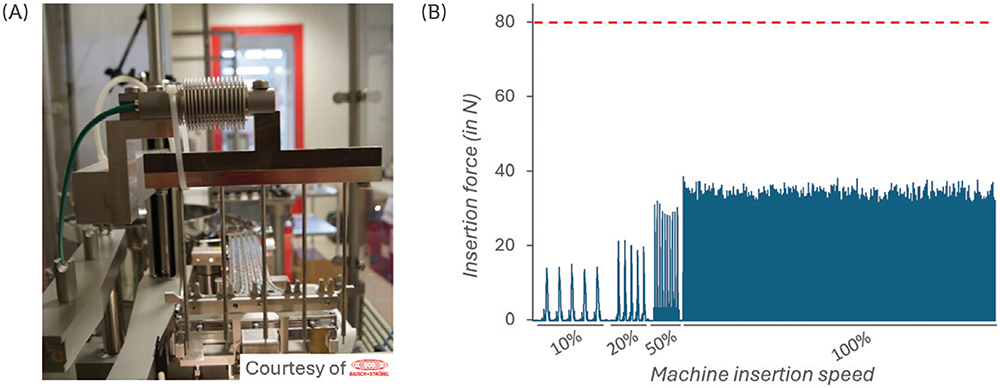
Figure 3: Measurement of the force during vented insertion of PremiumCoat® 1–3 mL plungers. Experimental set-up, with the force sensor positioned at the insertion stem (A). Insertion force measured at 10%, 20%, 50% and 100% insertion speed (B). The maximum acceptable insertion force was defined at 80 N.
The data shown in Figure 3B show that the force measured during insertion is directly correlated to the insertion speed, as could be expected. Most importantly, even when operating at 100%, the force required to insert PremiumCoat® plungers into the vent tube does not exceed 40 N, which is well below the defined limit of 80 N.
CONCLUSION
“The consequence of identifying processability issues when upscaling production to industrialisation can be costly and may require restarting the validation process with an alternative packaging solution.”
Choosing the right primary packaging can be a daunting task, as issues could be encountered as early as during compatibility testing, but also much later in the development and industrialisation process. The consequence of identifying processability issues when upscaling production to industrialisation can be costly and may require restarting the validation process with an alternative packaging solution.
PremiumCoat® solutions have previously been proven to help protect drugs from E&L,1 maintain long-term container closure integrity down to -60°C for PFSs4 and -80°C for vials,2 enable autoinjector integration and facilitate drug delivery.3 This dataset completes the picture by demonstrating that PremiumCoat® plungers also perform well on all relevant parameters associated with high-speed fill-finish operations using vented insertion, helping drug manufacturers secure industrialisation for drugs and derisk drug development.
In addition to the data supporting the performance of PremiumCoat® on various parameters, Aptar Pharma and Gateway Analytical offer a wide range of cGMP-compliant development and analytical services to help drug developers reach market faster. Additionally, because the success of a drug does not stop at drug filling, Noble’s complete range of human factors, user experience, training and onboarding solutions helps drug developers to ensure that their drug gets delivered appropriately and guarantee the best outcome for patients.
*Available from BD
Discover more about Aptar Pharma’s injectables offering including PremiumCoat®, here.
REFERENCES
- Suman J, Cordier S, Verger E, “Combining a State-of-the-Art Bromobutyl Formulation With a Proven ETFE Film for Exceptional Chemical Performance”. Drug Development & Delivery, Jan/Feb 2022, Vol 22(1), pp 34–38.
- “Cold storage and container closure integrity – demonstrated performances of ETFE-Coated components”. ONdrugDelivery, Issue 147 (May 2023), pp 6–11.
- Cordier S, Guillemot L-H, Cardonnet A, “Exploring How the Functional Properties of the PremiumCoat® 1-3mL Plunger Facilitate its Implementation on Filling Lines & Enable the Delivery of Sensitive Vaccines & Biotech Drugs”. Drug Development & Delivery, Oct 2021, Vol 21(7), pp 34–39.
- “Evaluating syringe plunger functional performance to secure Pre-Filled Syringe & Auto-Injector integration and machinability on filling lines: PremiumCoat® 1-3 mL syringe plunger”. Poster Presentation, Aptar Pharma, PDA Universe of Pre-Filled Syringes and Injection Devices Conference, Gothenburg, Sweden, 2023.