To Issue 163
Citation: Wild A, Montag A, “Using Efficient Proof-of-Concept Tests and Pilot Moulds for Device Development Success”. ONdrugDelivery, Issue 163 (Jul 2024), pp 18–21.
Andreas Wild and Andreas Montag discuss the value of early proof-of-concept testing and sample production for drug delivery device development projects, with an emphasis on how partnership and consultation can smooth and enhance this process, including for design for automation and design for manufacturing considerations.
This article was originally published in German in meditronic-journal.
The rapid development of the pharmaceutical industry requires innovative and efficient drug delivery devices to meet the needs of patients and the healthcare sector. These specialised devices play a crucial role in the administration of drugs to patients, as they have a significant effect on the efficacy, safety and user-friendliness of the delivered therapy. With increasing competition and stricter regulatory requirements, the industrialisation of drug delivery devices has become a critical factor for success in the market.
CHALLENGES IN INDUSTRIALISATION
The development of drug delivery devices is a complex task that requires specialised expertise. The process involves not only the design of the device itself, but also consideration of technical feasibility, cycle times, the design of injection moulding and assembly tools and assessment of costs. There are three often conflicting perspectives on design that need to be reconciled.
Functionality and Market Requirements
These requirements are, of course, the highest priority. All considerations regarding well-functioning production and assembly are rendered moot if the product does not fulfil the requirements of the market and the regulatory specifications for approval and, therefore, cannot be sold.
Injection Moulding Tool Requirements
The injection mould is a crucial element for producing precisely shaped parts. The requirements for injection moulding tools can vary depending on the specific requirements of the part to be produced. However, the following are some general requirements:
- Precision: The mould must be extremely precise to ensure that the manufactured parts meet the required specifications. This includes the exact shape, size and surface finish of the final product.
- Durability and Material Selection: The tool must be made from high-quality materials that can withstand the demands of the injection moulding process. Typically, tool steels, such as P20 or H13, or those with higher wear resistance are used to ensure a long mould life.
- Cooling: Effective cooling is critical to ensure that the material solidifies evenly and that shrinkage or deformation problems are minimised. The mould should have an efficient cooling system that ensures an even temperature distribution.
- Venting: The mould must have sufficient venting channels to ensure that gases produced during the injection moulding process can escape. This prevents the formation of air pockets or bubbles in the manufactured parts.
- Automation Capability: Modern injection moulding tools can be equipped with automation functions to optimise the production process. This can include the integration of demoulding systems or robots for part removal.
- Ease of Maintenance: A good mould design takes ease of maintenance into account. This means that the tool should be easy to disassemble, clean and maintain so as to minimise downtime and extend the life of the tool.
Requirements for Assembly
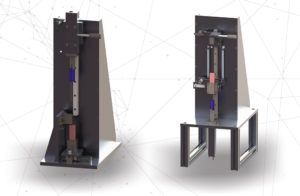
Figure 1: PoC testing applied to part joining direction.
In addition to joining tolerances, positioning tolerances suddenly come into play here (Figure 1). Additionally, it is important to consider the design of chamfers and joining aids, or surfaces and moulds for gripping, to provide counterforce during joining.
“In order to unite all interests, design for automation, DfA or DfM studies can be carried out with all interest groups at an early stage.”
PROOF-OF-CONCEPT STUDIES
The earlier this tension is analysed and resolved, the faster samples for proof-of-concept (PoC) studies or clinical trials can be created. In order to unite all interests, design for automation, design for assembly (DfA) or design for manufacturing (DfM) studies can be carried out with all interest groups at an early stage (Figure 2). The terms of these studies are often not standardised – each company defines them slightly differently. Regardless of which aspects are included in which area, it is ultimately a matter of addressing early on how a later marketable device can be manufactured in sufficient quantities with the simplest possible processes and low unit costs (Figure 3).
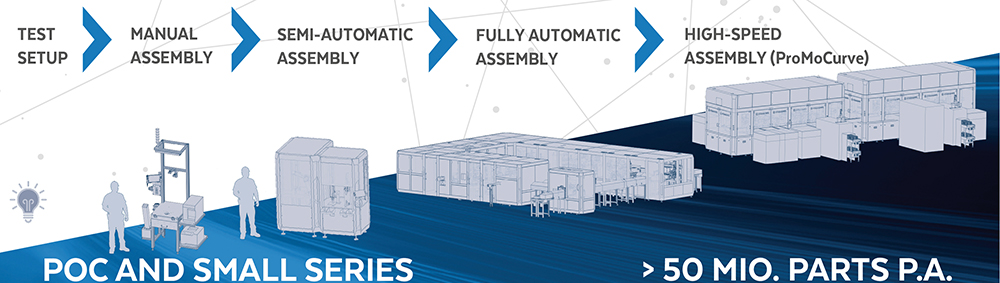
Figure 2: DfM as a start to series production.
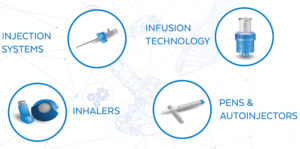
Figure 3: Areas of drug delivery device development where early and efficient PoC testing can be applied.
However, it is not only functional and manufacturing aspects that should be considered here. Against the background of the risk-based approach outlined by GMP guidelines, test characteristics and criteria can already be defined. The questions that often only arise during the design and building of a machine for series production are familiar ones to all device developers, for example:
- How is a correct joining process defined?
- What is a good surface?
- When is the product “damaged”?
If these questions are not only discussed in the initial concept studies, but also tested – and ideally specified and qualified – in advance with the help of PoC studies, a lot of preparatory work will have already been done for the smooth development of series production. This begins with the creation of the drawing for the injection moulded part and, therefore, with the production of the injection moulding tool for the first prototypes.
“External partners are often familiar with very different approaches due to their collaboration with several medical technology manufacturers and can certainly bring a breath of fresh air, new perspectives, additional experience and ideas.”
THE ADDED VALUE OF AN EARLY PARTNERSHIP
The industrialisation of drug delivery devices requires a multidisciplinary team that combines expertise in the areas of injection moulding, automation, production and assembly with knowledge of the functionality and market requirements of the device. While many manufacturers have this knowledge in-house and there are often colleagues with many years of experience in these areas, it is sometimes worth looking outside the box – external partners are often familiar with very different approaches due to their collaboration with several medical technology manufacturers and can certainly bring a breath of fresh air, new perspectives, additional experience and ideas.
The development of new products and the series production of existing products are often done simultaneously at most companies. In-house specialists for injection moulding, production, assembly and process are frequently involved in ongoing operations and cannot provide the time that a new product actually needs for its development. In such cases, the early involvement of an external partner can be invaluable.
The perspective on a production and assembly drawing can be very different across specialisms. Some tolerances may be seen as too tight or too wide from the point of view of assembly specialists. Whereas, from the point of view of plastics engineers, maintaining some tolerances can be considered complex against the background of shrinkage and thermal deformation during cooling. At the same time, the manufacture of a high-quality product often requires relatively tight tolerances with little clearance between the components. Last but not least, a controller will also speak up and urge compliance with costs. Such a conflict can only be resolved by having all the experts at the same table and, in a second step, real sample parts from a pilot mould. Pilot moulds offer several advantages:
- Rapid Prototype Production: A pilot injection mould enables the rapid production of prototypes or small series parts. This is particularly useful for validating design concepts or testing new products prior to mass production.
- Cost Efficiency: Compared with full production moulds, pilot injection moulds are generally cheaper to produce. This enables companies to carry out prototyping and test runs without having to invest heavily in expensive moulds.
- Flexibility and Adaptability: Pilot injection moulds are often easier to adapt and modify than production tools. This allows engineers and designers to respond quickly to feedback and requirements and make changes to the design or manufacturing parameters.
- Fast Time to Market: By using a pilot injection mould, companies can bring products to market faster. This is particularly important in industries with short development cycles or rapidly changing market requirements.
- Fault Detection and Optimisation: By producing prototypes with a pilot injection mould, engineers can identify potential problems at an early stage and rectify them before mass production begins. This helps to avoid production downtime and expensive reworking.
- Material and Process Development: Pilot injection moulds also make it possible to test and optimise different materials and process parameters. This is particularly useful when developing new materials or fine-tuning the injection moulding process for optimal results.
- Market Research and Customer Feedback: With prototypes produced using a pilot injection mould, companies can conduct market research and gather customer feedback before making major investments in mass production. This helps to ensure that the final product meets the requirements and expectations of the target patient group.
Overall, using a pilot injection mould provides a cost-effective and efficient way to produce prototypes, test products and accelerate time to market, resulting in accelerated product development and improved competitiveness.
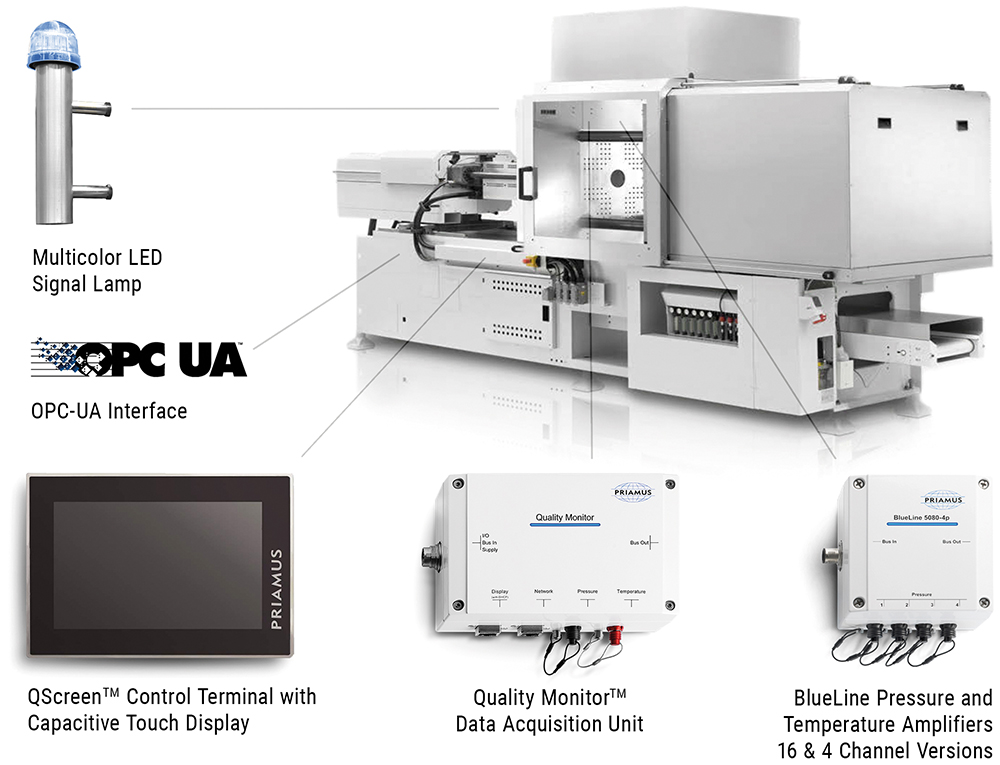
Figure 4: Otto Männer’s Quality Monitor™ system for the simple and reliable monitoring of the industrial injection moulding processes.
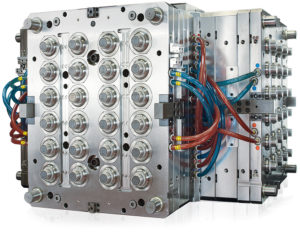
Figure 5: Foboha’s mould cube 24cavscrew cap.
For optimal results, a partner with experience in injection moulding, assembly and automation technologies can be involved in the design of the medical device right from the start. This way, design errors can be identified and rectified at an early stage. Working with an experienced partner also allows medical device manufacturers to draw on innovative ideas, outside experience and best practice in automation technology to ensure an optimised design (Figures 4 & 5).
At the same time, working with an experienced partner enables companies to focus on other aspects of drug delivery device development, namely the functionality, market acceptance and regulatory requirements of the product. For example, adapting to the new EU MDR is currently tying up significant capacity for almost all companies in the market. The personnel and expertise freed up by working with external partners can then focus their efforts on facilitating the authorisation of the drug delivery device and overcoming regulatory hurdles.
CONCLUSION
The considerations discussed in this article can have a significant impact on the quality, costs and lead time of the development of a drug delivery device. Especially when considering that the time from the first sketch to the first shot is most often several months, it is worth starting these investigations at an early stage, potentially with an experienced external partner. Rapid PoC and sample production are essential to speed up product development and minimise risks. An experienced partner can create prototypes and samples quickly and, if necessary, build fixtures for joining to validate the design in order to identify possible weak points for automated handling and joining at an early stage.
Once mutual trust has been built up between device developer and production partner in the development and PoC phase and matured to the point that the decision is made to continue working together on the path to series production, the jointly generated knowledge can very quickly be put to profitable use. This optimises the development process and shortens the time to market – the parameters for injection moulding are already known, the required joining accuracies have been established and test plans for subsequent installation qualification and operational qualification tests have already been written.
Ultimately, the decision to seek advice from a partner who is familiar with design for automation, DfM and DfA from the outset is of great importance for successfully industrialising drug delivery devices. It is an investment that pays off in the long term and helps medical technology manufacturers to develop innovative and high-quality solutions for patients.