To Issue 165
Citation: Davies W, Milston H, “Sustainable Design for Healthcare Devices: Pathways Towards Net Zero”. ONdrugDelivery, Issue 165 (Sep/Oct 2024), pp 38–41.
Will Davies and Holly Milston consider sustainable pathways towards circularity in the medical device industry.
As pharmaceutical companies across the industry strive to implement and meet sustainability targets, every opportunity for device and system carbon footprint reduction should be explored. There are multiple pathways for sustainability improvements at every stage of a device’s lifecycle, with the ultimate goal being full circularity.
WHAT IS CIRCULARITY?
The circular economy represents the gold standard of device sustainability, aiming to capture and reuse all finite resources involved in the manufacture of a product indefinitely, minimising waste, resource use and negative external effects. It promotes the remanufacture of products and efficient recycling of materials, demanding that design attention is paid to every stage of the product’s lifecycle. However, it is not all thankless hard work – the circular economy can deliver additional tangible benefits, such as cost savings through reduced production volumes and increased product reliability.
CIRCULARITY FOR DRUG DELIVERY DEVICES
Even without the adoption of a fully circular product ecosystem, there are many opportunities for sustainability enhancement that can be made to a device at every stage of its lifecycle.
Figure 1 illustrates the lifecycle phases of a product, each of which can be progressively broken down to identify potential opportunities and design approaches for sustainability improvement, as this article aims to demonstrate.
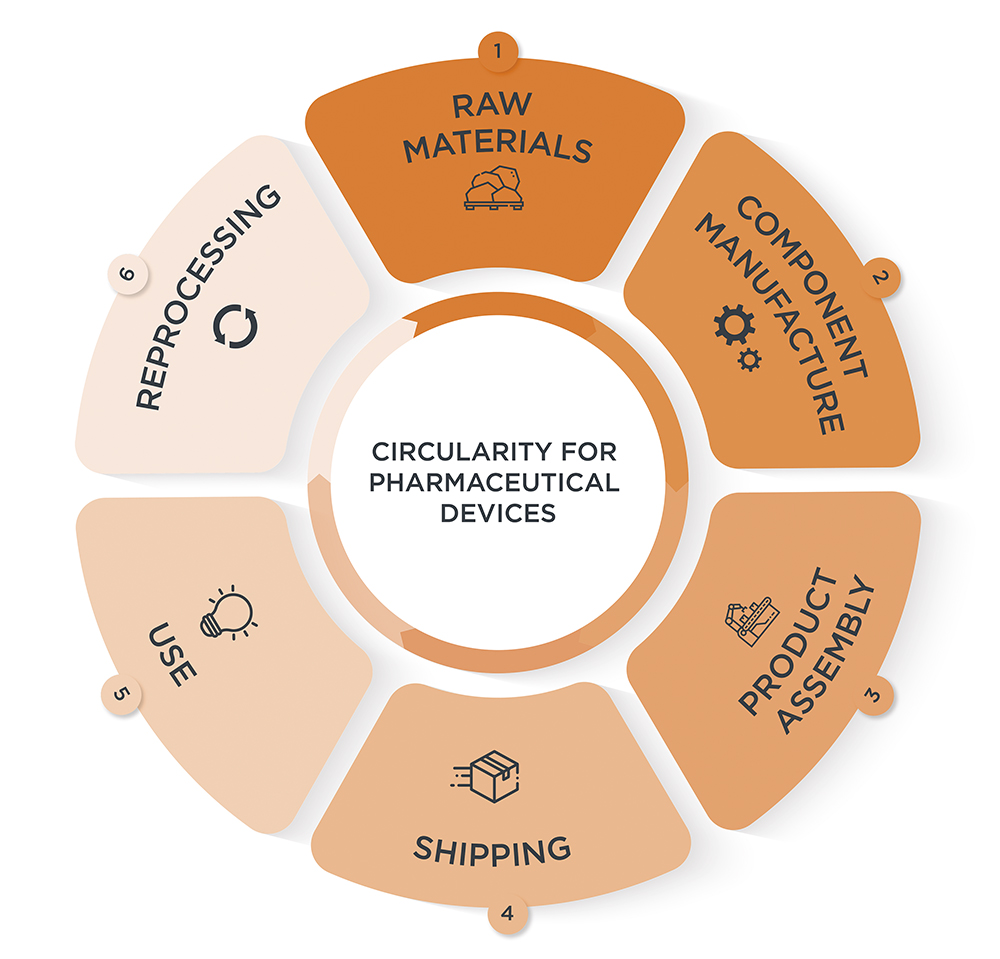
Figure 1: Circularity for drug delivery devices.
RAW MATERIALS
Any product should comprise a minimum necessary quantity of material, as every gram of material represents an embodied value of carbon, energy and natural resources.
Design for Resource Reduction
- Metals: Metal recycling is now sufficiently developed such that mechanical properties can be well defined in the recyclate, although typically of lower quality than a virgin grade.
- Polymers: High-quality grades of recycled-content plastic are now available. Bio-based plastics are derived either directly from crops, such as sugar cane, corn or castor oil, or indirectly from biomass derived from agriculture or forestry (e.g. cellulose). Biodegradable materials are commonly used in medical applications, such as drug release and tissue engineering; these are generally bio-based polymers, such as PLA, PHB, PHA, PBS and PCL.
- Alternatives: A significant development in sustainable biodegradable materials is that of paper (or pulp) injection moulding, which provides a potential alternative to plastic injection moulding, facilitating complex geometries, thin walls and low component weights, while also being highly sustainable (Figure 2).
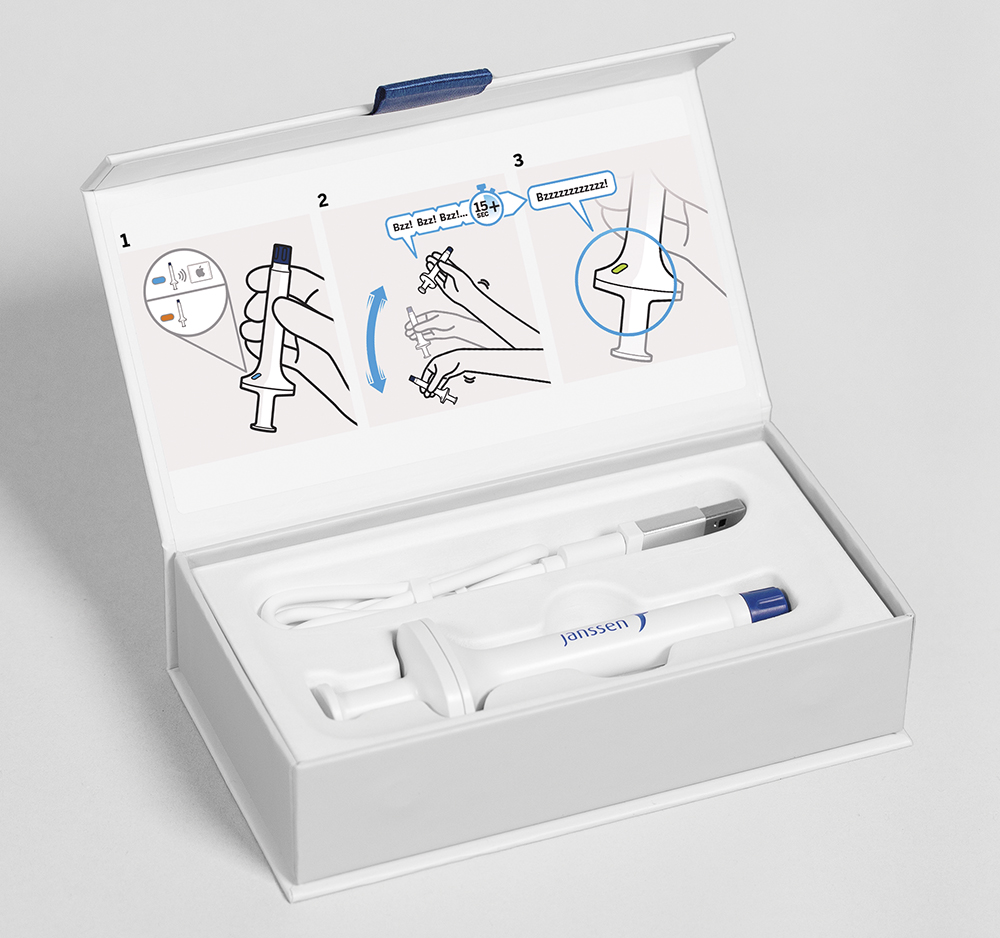
Figure 2: Premium yet sustainable product packaging, constructed of card outer and with a pulp-formed inner tray.
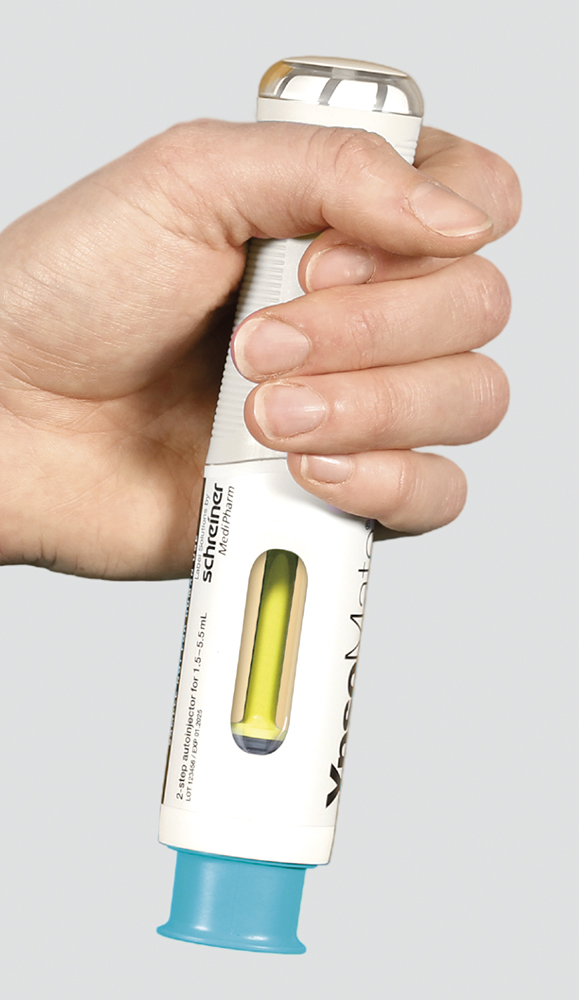
Figure 3: Sometimes, a purely mechanical solution may provide a preferential alternative to electronics; for example, drive systems or visual indicators, such as that employed by the YpsoMate 5.5 from Ypsomed.
COMPONENT MANUFACTURE
“Every unit of energy or resource consumed during manufacture is embodied in the final product.”
Every unit of energy or resource consumed during manufacture is embodied in the final product.
Design for Efficient Manufacture
- Facility power: Carbon emissions from power generation are embedded in products, making it important to select renewable energy sources.
- Plastic moulding: Minimise part size and complexity as smaller injection-mould presses and shorter cycle times consume less energy. Select efficient tools and processes, for example, gas-assisted injection moulding offers weight-saving and part-reduction benefits.
- Induction-heated tooling: Reduce material waste through precise and consistent heating, and increase production rates with faster cycles. The pinpoint accuracy and repeatability of induction-heated tooling minimises defects and operator variability, leading to higher-quality output and less resource-intensive manufacturing.
- Post-processing: Design with an increased lifespan in mind, as every post-process operation requires time, floor space and energy.
- Electronics and power sources: Electronics are so universal in today’s world of connected and smart products that it is easy to overlook how impactful the inclusion of electronic components can be. A simple printed circuit board may have an emissions footprint up to 20 times greater than the equivalent mass of plastic, with further negative effects, such as increased marine eutrophication (Figure 3).
PRODUCT ASSEMBLY
Assembly of a product also constitutes part of that product’s embodied energy. The faster and more efficiently that product can be assembled, the less power is consumed by the assembly plant per product.
Design for Assembly
- Facility power: As with component manufacture, the emissions are incorporated into the product, making it important to opt for a renewable power supply for assembly.
- Component assembly: Concentrate on assembly methods that are durable, reliable and have ease of disassembly. Permanent joining or trapping of dissimilar materials should be avoided. Screws, or other mechanical fasteners, can improve durability and repairability.
- Assembly and disassembly: These should be considered together. Jigs and fixtures should be designed concurrently with the device design to ensure maximum assembly and disassembly efficiency.
SHIPPING
The method and distance of product transportation from factory to point of use can have a significant impact upon its emissions footprint.
Design for Distribution
- Packaged product volume and mass: The smaller the packaged product, the more units can be transported per shipment. The lower the mass, the less energy and carbon are used to transport it.
- Modes of shipping: Plan supply chains and timescales accordingly. For international shipping, the lowest carbon method is by container ship. Cold-chain shipping drastically increases transport emissions, as it reduces the number of products per shipment due to additional insulation volume. Long-haul the impact of air freight is 100 times greater than that of container shipping. The worst option is cold-chain, short-haul air freight, which can far exceed the impact of all other measures combined.
- Last-mile emissions: These are often overlooked. A customer driving to a pharmacy to collect a device may be transporting two tonnes of vehicle with them. Consider a product-as-a-service business model that uses a driver who combines the delivery to the customer with other devices or customers as part of a shared journey.
“Use-related emissions can be reduced through design enhancement, system change and influencing user behaviour.”
USE
Use-related emissions can be reduced through design enhancement, system change and influencing user behaviour.
Design for Sustainable Use
- Circular use: Design the entire ecosystem of the product to make it easy and intuitive for the user to return the product after use.
- Physical durability: This is one of the key contributors to a product’s sustainability. The longer a product is in service for, the fewer resources are consumed in the manufacture and disposal of replacement products. Emotional durability also promotes the physical durability of a product by increasing the emotional value of a product to the user.
- Resource reduction: Consider the reduction of power and waste during use, for example, energy-efficient components, effective thermal management and minimising single-use packaging elements.
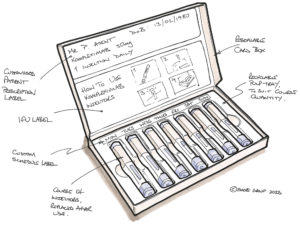
Figure 4: Packaging concept for a circular autoinjector model.
REPROCESSING
“End of use” does not need to mean “end of life”; try to avoid the manufacture of replacement devices.
Design for End of Use and Reprocessing
- Design for return: Make it easy and intuitive for the user to collect and return used devices (Figure 4).
- Design for disassembly: Design the product from the outset to be easy to disassemble into constituent components or modules. It should generally be assumed that the product will be recycled, or even remanufactured, at end of life and that the design should encourage this, especially as recycling processes and technology continue to develop.
- Design for remanufacture: Identify key components or sub-assemblies (modules) as candidates for remanufacture. Use lifecycle-tracking technology to monitor the device, module or component reuse, and do not exceed design service lifetimes.
- Design for recycling: Recycling is less preferable to reuse, but better than landfill or incineration.
DESIGNING FOR A SUSTAINABLE FUTURE
The ultimate route to net zero is for manufacturers to adopt circular economy models, which – particularly in the pharmaceutical industry – is a long and complex road that is likely to require regulatory change as well as business model reinvention. However, designers have the tools that allow them to be instrumental in developing products and services that will transition smoothly to circularity and have a significantly reduced environmental impact in the meantime. The imperative is clear, and constantly evolving design, manufacturing and material technologies and methodologies can be implemented today to bring the goal closer step by step (Figure 5).
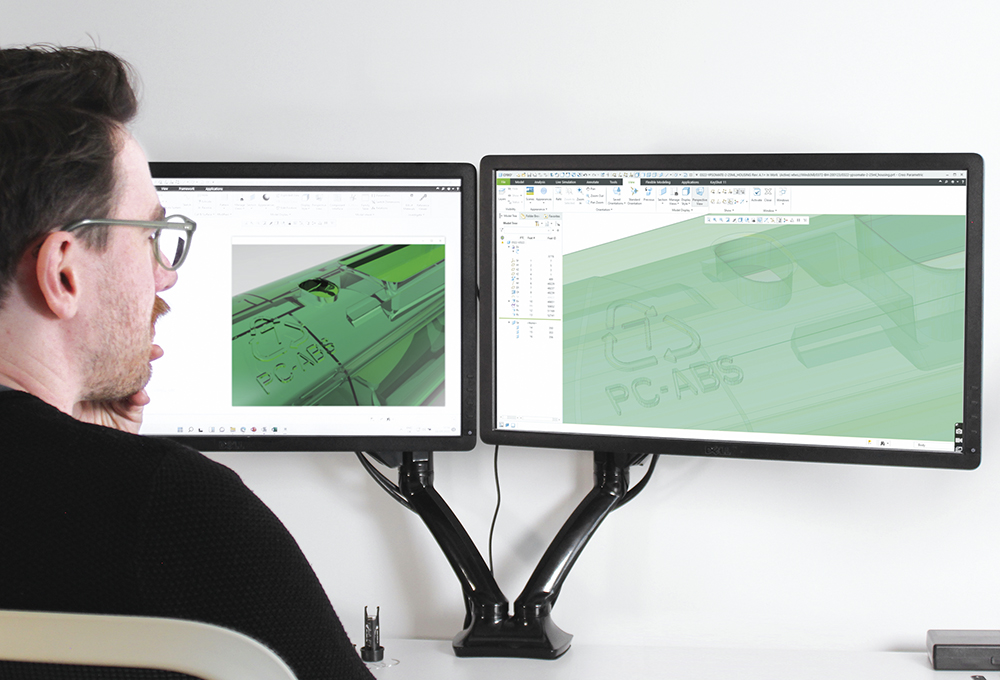
Figure 5: Designing for a sustainable future.