Citation: Toole K, Hutton B, McLusky J, “Defining High-Viscosity, Large-Volume Drug Delivery Systems”. ONdrugDelivery, Issue 166 (Oct 2024), pp 47–50.
Farid Seddighi, Sigrid Saaler-Reinhardt and Daniel Primavessy discuss the critical importance of testing at an early stage of medical device development, presenting an overview of the results that confirm the technical performance and usability of the novel Gx Inbeneo® autoinjector.
Autoinjectors have become increasingly popular for the subcutaneous administration of biologic drugs, as they enable patients with chronic conditions to manage their therapy at home. Such a shift towards self-administration supports patient independence and may reduce the burden on the healthcare system. However, device failures or use errors can have serious implications for patient outcomes, making it even more critical to ensure autoinjectors are reliable, safe and easy to use.
To achieve this, functional and usability testing needs to be well planned and rigorously carried out. This is particularly critical when developing an innovative new concept such as the Gx Inbeneo® cartridge-based pre-pressurised autoinjector.1 Gerresheimer and its partner Midas Pharma have therefore implemented an extensive testing programme early in the development phase to confirm performance and usability.
A NOVEL PRE-PRESSURISED AUTOINJECTOR DESIGN
In response to the market growth of biologics and the increasing preference for self-administration, Gerresheimer and Midas Pharma developed a new cartridge-based autoinjector platform concept.
Most autoinjectors are spring driven and based on a prefilled syringe (PFS) with staked-in needle. This design incorporates a compressed spring held in place by a locking mechanism. The mechanism must retain the force of the spring throughout the shelf life of the combination device. It must then release the spring at the required moment and with appropriate force to effectively inject the drug. The moment of release in this design causes a pressure spike,2 which can place stress on the device’s components. This can be a particular problem with the higher spring force required to deliver drugs with large volumes or high viscosities and may lead to misfiring.3
To avoid these stress spikes, the Gx Inbeneo development team opted for a cartridge-based design with a novel “pre-pressurised” concept. The resulting autoinjector employs the primary prefilled cartridge in the autoinjector system to retain the spring force and a double-ended needle for activation. When the patient presses the autoinjector on their abdomen or thigh, the thinner end of the needle first pierces the skin. Subsequently, the thicker end of the needle pierces the cartridge septum, connecting the fluid pathway and commencing drug delivery automatically.
“The autoinjector design also decreases, or even dissolves, any gas bubbles present in the liquid drug, which might otherwise result in protein aggregation in sensitive, viscous biologics.”
This pre-pressurised concept bypasses the pressure spike in the drug delivery profile that occurs when a conventional spring-release mechanism is activated, resulting in a steady delivery profile from the start of the delivery until the drug delivery concludes. The autoinjector design also decreases, or even dissolves, any gas bubbles present in the liquid drug, which might otherwise result in protein aggregation in sensitive, viscous biologics.
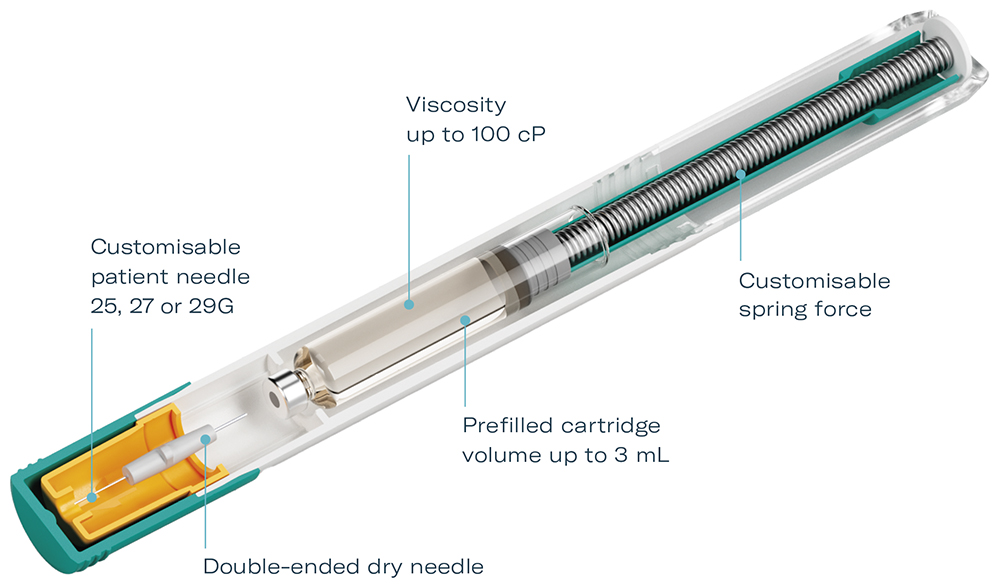
Figure 1: Gx Inbeneo cartridge-based autoinjector platform concept.
The double-ended needle has further advantages – as it is separated from the cartridge until administration, it eliminates the risk of large-molecule biologics or excipients clogging the needle during storage. The double-ended needle design further responds to the requirements of delivering biologics, as it enables higher viscosities to be delivered in less time than with a standard needle (Figure 1).
THE CRITICAL ROLE OF FUNCTIONAL TESTING
State-of-the-art functional testing is the backbone of the quality assurance process for medical devices. A malfunctioning or difficult-to-use device may lead to incorrect dosing and reduced efficacy of the treatment – and cause patient anxiety.
With the innovative new autoinjector design concept of the Gx Inbeneo, Gerresheimer and Midas Pharma went through an extensive and comprehensive testing programme as early as possible as of the pre-feasibility phase. They enlisted the support of Springboard to develop and execute tests covering a wide range of factors, from the mechanical performance of the device to the long-term stability of the biologic drug product it should deliver. The results of such tests provided crucial information to establish data-based specifications for all critical components of the device throughout the design output phase, thereby ensuring that the final design is robust. Detailed methodologies and results were published in a peer-reviewed journal.4
FUNCTIONAL TESTING METHODOLOGY AND RESULTS
Pressure Testing and Septum Stability
One of the key components of the primary cartridge is the septum, which acts as a seal to maintain the sterility and integrity of the drug product. In the Gx Inbeneo concept, the septum has to withstand the pressure exerted by the power spring during storage without leaking. In addition, the septum must not rupture when pierced during the injection process. Any breach could compromise the drug product and result in malfunction or incomplete dosing. It was thus identified as the primary failure mode of the device.
Gerresheimer and Midas Pharma conducted extensive tests on the septum stability of standard ISO cartridge materials from different suppliers under long-term pressure conditions to assess their performance over the device’s intended shelf life of at least two years. The septum was subjected to continuous pressure to simulate the conditions the device would experience during storage.
The septum exhibited an initial expected bulge growth within the first 14 days, and then almost came to a halt, clearly indicating a stable performance over the intended shelf life. The tests confirmed that a variety of septa could withstand the pressures exerted by the device without rupture, helping to maintain the integrity of the drug product and the safety of the patient (Figure 2).
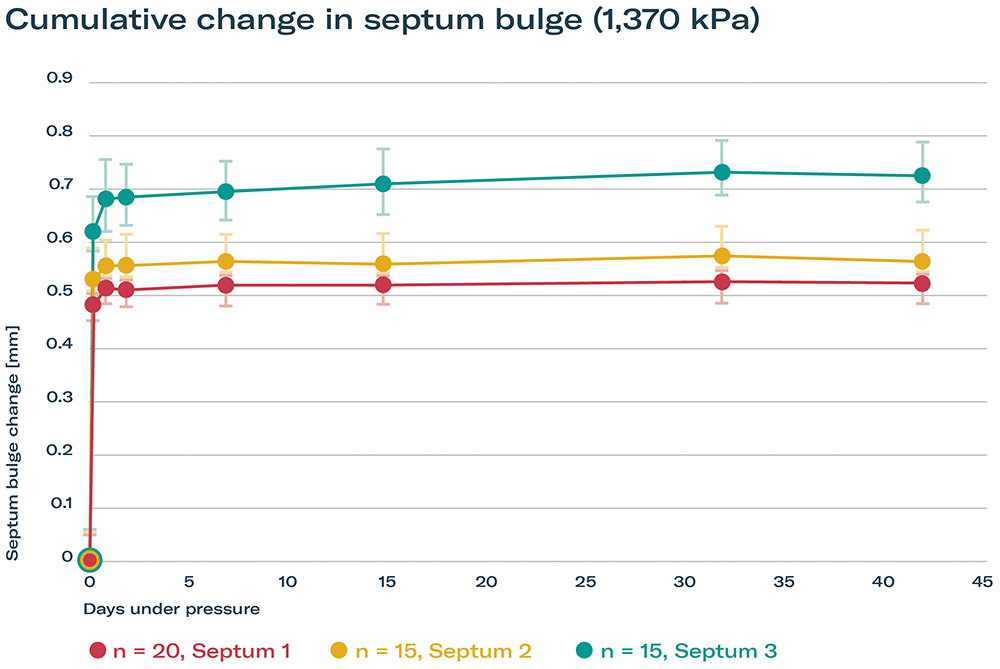
Figure 2: Septum stability over time under pressure.
Glass Breaking Pressure
The primary packaging used in the autoinjector, typically made of Type I pharma-grade borosilicate glass, must be able to withstand the pressures exerted by the spring in the device during use. If the glass was to break or crack, it could lead to contamination of the drug product or injury to the patient.
Glass breaking has been empirically identified as a secondary failure mode of the autoinjector concept. The breaking pressure of glass cartridges from different suppliers were tested under increasing levels of pressure (Figure 3). The lowest glass breaking point determined in all experiments was still more than 3.5 times higher than the highest possible pressure in the autoinjector platform. Another interesting finding regarding container closure integrity from the secondary failure mode testing was that, at increasing pressures, the plunger stopper did not fail.
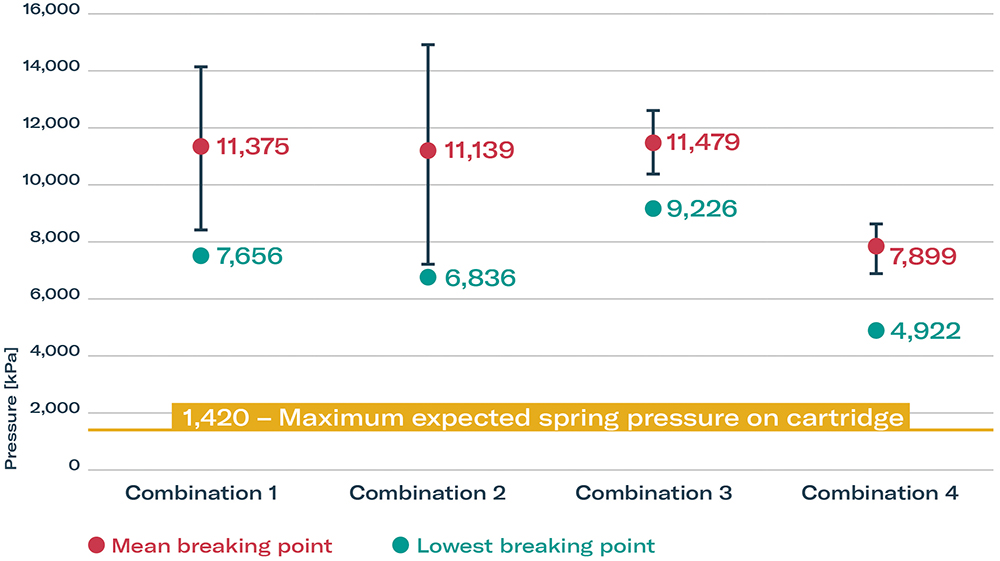
Figure 3: Cartridge glass breaking pressures.
“It was especially important to test if the continuous pressure on the rubber plunger stopper would negatively impact glide force or break-loose force.”
Glide and Break-Loose Forces
The smooth operation of an autoinjector also depends on the forces required to trigger the device and push the drug through the needle into the patient’s tissue. These forces, known as glide and break-loose forces, must be carefully controlled to ensure that the device is easy to use, while also delivering the drug at the appropriate rate. It was especially important to test if the continuous pressure on the rubber plunger stopper would negatively impact glide force or break-loose force.
The forces were measured repeatedly over time and under different environmental conditions to assess the consistency and reliability of the plunger stopper.
The forces remained within acceptable ranges throughout the testing period, even under pressurised conditions. This demonstrates that the autoinjector can reliably administer the drug without requiring excessive force or impacting the delivery of the drug.
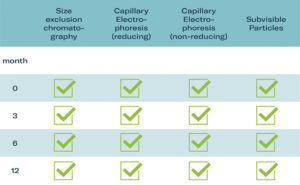
Figure 4: Drug-release testing after pressurised storage.4
Drug Product Stability
Biologic drug products, such as monoclonal antibodies, are often sensitive to environmental conditions, including pressure, temperature and exposure to certain materials. It is therefore critical to ensure that the autoinjector does not adversely affect the stability or efficacy of the drug product over time. Extensive tests were conducted on a commercially available monoclonal antibody (adalimumab) as a model for biologics to assess structural integrity and any agglomerates or degradation after being stored pre-pressurised in the device for an extended period. A range of analytical methods were used in drug-release testing under GMP conditions, including size exclusion chromatography and electrophoresis (Figure 4).
The tests showed no degradation or agglomeration of the drug product due to pressure or due to expelling the drug product through the device’s fluid pathway. This confirms that the Gx Inbeneo can safely store and deliver biologic drugs without compromising their efficacy or safety.
USABILITY TESTING AND PATIENT SAFETY
While functional reliability is essential, the usability of an autoinjector is equally important to ensure that a device meets the needs of the user, and that a therapeutic drug is administered correctly. device that is difficult to use or confusing to operate can lead to use errors, such as incorrect dosing, or even failure to administer the medication altogether. Such errors can have serious implications for patient therapy outcomes.
Gerresheimer places a strong emphasis on early usability testing, integrating a risk-based human factors and usability engineering approach into the design process. This ensures that devices are not only functional but also intuitive and easy for patients to use. This type of testing is essential for reducing the risk of use errors, enhancing patient safety and supporting therapy outcomes.
The developers of the Gx Inbeneo incorporated several features to optimise ease of use and secure delivery. To mitigate needle phobia, the needle is hidden and protected within the autoinjector until administration. Administration steps have been minimised so that the user only needs to remove the cap and press the autoinjector against the skin to begin injection. Correct cap removal and orientation of the autoinjector is indicated with arrows. To monitor the injection progress, the housing includes a visual indicator in addition to the central viewing window commonly seen in autoinjectors. The visual indicator enables observation of injection progress even if the patient’s hand is covering the viewing window.
These features were tested during a formative usability study. The study participants (n=34) included patients and healthcare professionals, both injection-naïve and experienced, and some with moderate dexterity issues. This ensured that all potential users were able to safely use the device. Study participants were observed to position the device correctly against the body for the full injection time. A total of 97% of the participants stated that they found it easy to track injection progress. Of these, 66% used the transparent top casing for monitoring.
THE IMPORTANCE OF TESTING FOR PATIENTS AND PHARMA COMPANIES ALIKE
Such comprehensive testing of an autoinjector ensures that it is safe and easy to use – and can reliably deliver the correct dose of a biologic drug product. Drug product stability testing further helps to confirm that an autoinjector will not negatively impact the drug product, ensuring that the efficacy of the therapy is maintained. This overall approach supports patient adherence, which is critical for managing chronic conditions and achieving positive health outcomes.
With their commitment to extensive functional and usability testing early in the development processes, Gerresheimer and Midas Pharma have demonstrated that the novel Gx Inbeneo platform concept can safely and effectively deliver viscous biologics. Armed with this knowledge, pharmaceutical companies can have confidence that the Gx Inbeneo is suitable for their biologic formulation, which may help reduce time to market. As the use of biologics continues to grow, the rigorous testing of autoinjectors will remain a cornerstone in safeguarding patient health and supporting successful therapeutic outcomes.
REFERENCES
- Primavessy D, Saaler-Reinhardt S, Maksymowicz K at al, “Gx Inbeneo® – Developing an Autoinjector that Responds to the Challenges of Biologics”. ONdrugDelivery, Issue 152 (Oct 2023), pp 32–36.
- Veilleux J-C, Shepherd JE, “Pressure and stress transients in autoinjector devices”. Drug Deliv Transl Res, 2018, Vol 8, pp 1238–1253.
- “Simponi (golimumab) 50 mg and 100 mg: important changes to the injection instructions for the SmartJect Pre-filled Pen”. Direct Healthcare Professional Communication, MSD, Aug 2023.
- Primavessy D, Piening M, Nightingale A at al, “Investigation of long-term pressure on primary packaging materials and a biologic drug product for injection with a novel autoinjector concept”. Drug Deliv Transl Res, 2024, online only.