To Issue 166
Citation: Aranda E, González F, “Springs: The Key to Advanced Autoinjector and Pen Injector Performance”. ONdrugDelivery, Issue 166 (Oct 2024), pp 83–86.
Emilie Aranda and Fernando González discuss the crucial role of spring mechanisms and other metal parts in autoinjectors and pen injectors.
Demographic trends and the rise in various pathologies, such as diabetes and obesity, in European countries and the US indicate a growing demand for more sophisticated treatment options. Autoinjectors and pen injectors, with increasingly specialised user-focused characteristics, are prime examples of the types of treatments required.
One factor related to user centricity is the ease and convenience of administrating the medication with injectors. Three types of mechanisms can be used in these devices: springs, gas cylinders and electric battery activation. The dominance in the industry of the spring mechanism and other metal parts is clear.
WHY ARE SPRINGS THE PREFERRED MECHANISM?
There are several reasons why springs are the preferred mechanism for autoinjector manufacturing companies over other options:
“Springs can accommodate different types of injectable drugs because they can be adapted to different parameters, such as viscosity, thrust force, injection speed and administration time.”
- Mechanical precision: Springs can accommodate different types of injectable drugs because they can be adapted to different parameters, such as viscosity, thrust force, injection speed and administration time for introduction into the human body, regulating the characteristics required by autoinjectors or pen injectors.
- Durability: A spring preserves the mechanical energy characteristics of the device, ensuring that it maintains error-free technical usability from the time of manufacture.
- Deformation-release control: Springs can expand or compress in response to controlled stimuli, allowing the rate of drug release to be adjusted.
- Device sophistication: Springs are also involved in innovative applications such as retractable needles (needle shielding) or the use of prefilled cartridges in reusable devices, which will gain market share due to sustainability issues.
As a division of the RPK Group, RPK Medical leverages 50 years of global leadership experience to design, develop and manufacture innovative metal springs, stamping and bending components, and assemblies that integrate metal and plastic parts with special packaging and cleanliness requirements in its ISO 7 clean rooms worldwide.
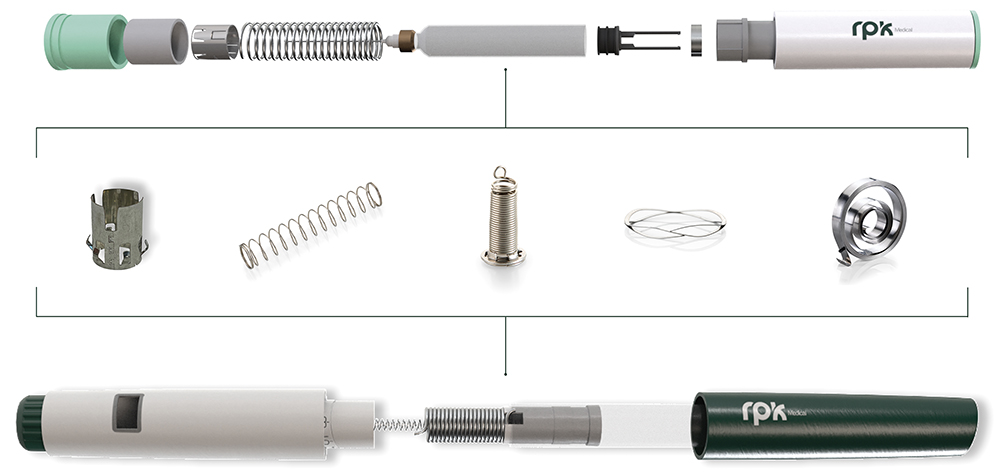
Figure 1: Springs, stamping and bending components, and assemblies for autoinjectors and pen injectors.
“RPK Medical’s components are essential for applications such as disposable autoinjectors, pen injectors, staplers, inhalers, pump sprays, wearable devices, safety syringes, catheters, airway products, blood collectors, cannulas and lancets.”
The company aims to transform lives by providing customised, technologically advanced solutions that meet the unique needs of its partners with precision and dependability. Serving original equipment manufacturers (OEMs), contract manufacturers and medical device engineers, RPK Medical’s components are essential for applications such as disposable autoinjectors, pen injectors, staplers, inhalers, pump sprays, wearable devices, safety syringes, catheters, airway products, blood collectors, cannulas and lancets (Figure 1).
What sets the company apart is its unwavering commitment to not only exceed its clients’ quality expectations but also to enhance the lives of patients and healthcare professionals. An example of this is its development of complex springs, assemblies and power packs for disposable autoinjectors, which are crucial for patients managing conditions such as allergies, diabetes and obesity. RPK Medical components help ensure that these devices deliver precise medication doses comfortably, safely and reliably, regardless of the drug’s viscosity.
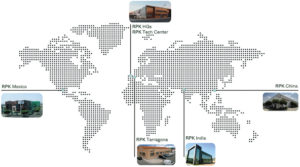
Figure 2: Global reach, local service.
GLOBAL REACH, LOCAL SERVICE
Established in 1974, in Vitoria-Gasteiz, the Basque capital in the north of Spain, RPK Group has been at the forefront of wire forming, spring manufacture and small stamping for half a century. Its global presence was significantly bolstered more than two decades ago with the inauguration of its first plant outside Europe, situated in Mexico, which now stands as its second-largest manufacturing facility (Figure 2).
The company’s global footprint is a testament to its commitment to being a local partner, no matter where you are. With six state-of-the-art manufacturing facilities across Europe, North America and Asia,the company ensures it is always nearby to support clients throughout the process. It adheres to a local-to-local manufacturing model, producing the parts needed within each continent to serve the respective region efficiently.
FINANCIAL BACKBONE
RPK Medical is central to RPK Group’s sustainable growth strategy. It possesses the knowledge, capacity and experience necessary to thrive in the medical sector, which it has identified as a field with significant opportunities. It is particularly focused on Europe and North America, where it is seeing exponential growth in applications it excels at. Its three plants in Spain serve the European market, while its Mexico plant caters to North America and its China factory serves the Chinese and Asian markets. The company’s financial strength and strategic positioning enables it to invest in the necessary technologies and infrastructure to meet the increasing demands of OEMs and contract manufacturers.
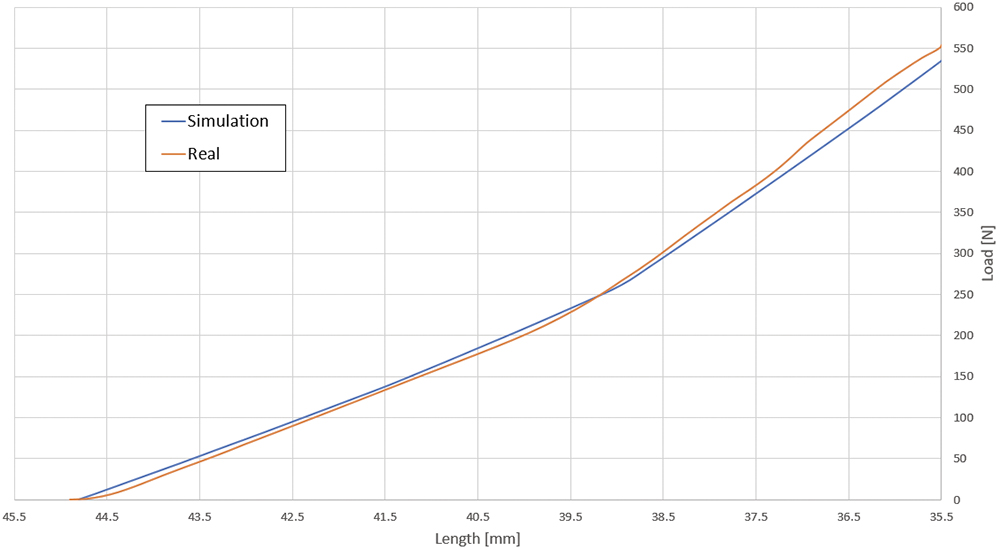
Figure 3: Differences between loads in reality and simulations.
MEDICAL DEVICE ENGINEERING AND PROCESSES
RPK Medical’s engineering excellence and comprehensive process coverage are what set it apart. Its team of engineers works closely with clients to create advanced technical solutions designed to enhance lives. The team understands that each project is unique, and that the company’s bespoke approach allows it to tailor its services to meet the specific needs of each client. The team takes a project from the initial concept through to final production, ensuring every step is meticulously managed and optimised. This commitment to customisation and excellence is what drives the company’s innovation and keeps it at the forefront of the medical device industry.
In all engineering processes for autoinjectors and pen injectors, RPK Medical simulates and contrasts the behaviour of the spring constant with reality – load behaviour throughout the displacement (Figure 3). This helps to ensure the autoinjector functions correctly by regulating parameters such as injection speed according to the drug’s viscosity, the force required to administer the precise dose and the stresses during its operation (Figure 4).
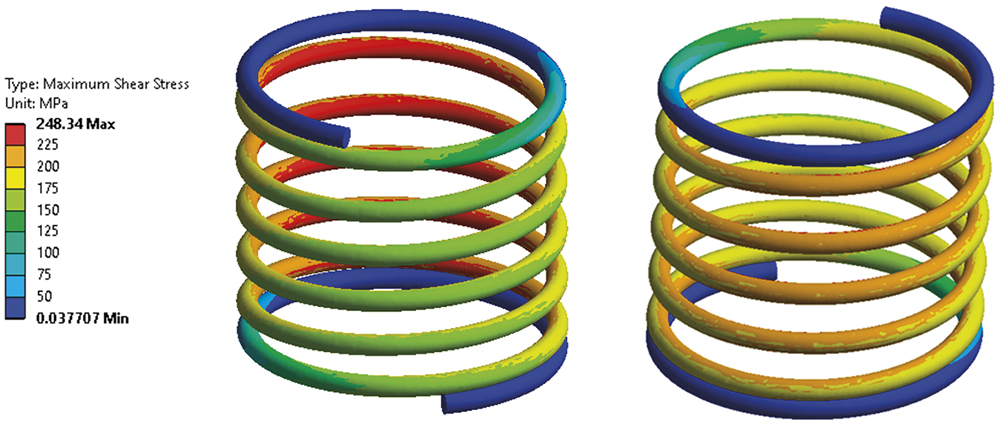
Figure 4: Spring stress simulations.
RPK TECHNOLOGICAL CENTER
The RPK Technological Center is testament to the company’s commitment to innovation. It is home to an in-house team of experts who specialise in projects that require highly complex technology. From the initial design and development stages to the procurement of necessary supplies, assembly, programming, commissioning, validation and industrialisation, the team manages every aspect with precision and expertise.
The knowledge generated at the RPK Technological Center is shared in real time with the company’s engineering teams around the globe. This seamless exchange of information ensures that the global operations benefit from the latest advancements and best practices, fostering a culture of continuous improvement and cutting-edge innovation.
ENGINEERS COMMITTED TO SUPPORTING CLIENTS
Each project is unique and has different characteristics. Springs and stamped and bent parts are key components, and often OEMs and contract manufacturers do not have a very detailed understanding of their value and potential. That is why RPK Medical’s engineering teams specialising in these components are invaluable for these projects. The company’s project managers and engineers help clients develop, design and carry out the industrialisation process of the springs and metal parts necessary for the correct functioning of a device under special cleanliness and packaging conditions right from the start of a project, highlighting the process in three stages (Figure 5).
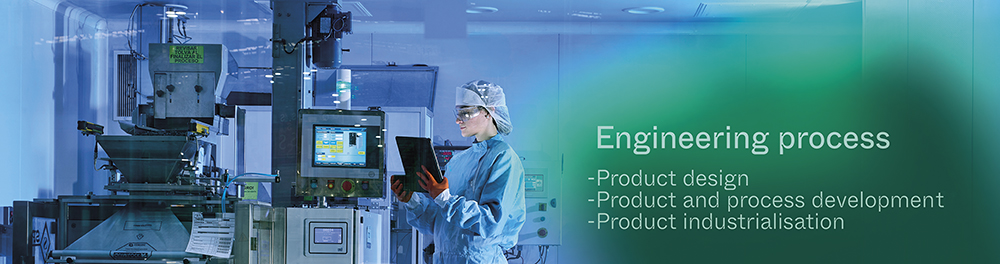
Figure 5: RPK Medical’s engineering process.
Product Design
RPK Medical excels in creating and designing unique solutions from scratch or enhancing the performance of existing parts to improve patient care and outcomes. Its product engineers, in co-ordination with the development team, devise production processes that meet or exceed client needs, ensuring the most efficient design process.
“The company’s expertise extends to special materials such asnitinol, allowing it to offer innovative solutions tailored to the most demanding applications.”
The company’s expertise extends to special materials such as nitinol, allowing it to offer innovative solutions tailored to the most demanding applications. This in-depth knowledge of materials, combined with its engineering capabilities, enables the company to deliver products that perform exceptionally under various conditions, such as components for two- or three-step injectors that provide clear, audible, visual and tactile feedback. The metal parts of the device are designed for high- and low-viscosity drug delivery.
Product and Process Development
Transforming ideas into market-ready products is at the core of what RPK Medical does. Its dedicated team manages every aspect of product and process development, from project management and engineering to the development of processes and machines. Its best-in-class approach includes prototyping, validation, ramp-up and the design and development of machines, tools and automatic assembly lines.
Advanced process and quality planning, finite element method and finite element analysis, rapid prototyping, in-house machine and tooling development, special packaging designs and full process design are all integral parts of the company’s comprehensive development services. These capabilities ensure that RPK Medical can take a client’s concept and turn it into a viable, manufacturable product.
Product Industrialisation
The transition from product development to industrialisation is a critical phase. RPK Medical’s extensive knowledge of process and machine optimisation, manufacturing and quality management ensures a smooth and accurate transition from prototypes to high-volume production.
Its global manufacturing capabilities, spanning America, Europe and Asia, allow it to support projects locally with the same high standards of technical and biological cleanliness. Its ISO 7 clean rooms, custom packaging solutions, such as tape and reel, and specialised processes, such as passivation, welding, deburring, grinding, shot peening, heat treatments and advanced surface coatings, ensure that every product meets the stringent requirements of the medical industry.
The company’s commitment to quality is further exemplified by its 100% unitary control system, which incorporates machine-integrated vision and control technology. This system ensures that every product is thoroughly inspected and meets the highest standards of precision and reliability. Additionally, its laboratories conduct rigorous testing, including environment, fatigue, relaxation, cleanliness and residual and dynamic tests, to validate product performance and durability.
In conclusion, the approach of RPK Medical is encapsulated in its philosophy: “Need. Develop. Do. Care.” This guiding principle drives the company to innovate, develop and deliver solutions that not only meet but exceed the expectations of clients. With its global reach, local service and unwavering commitment to quality, the company is a trusted partner in the medical device industry, dedicated to improving lives through engineering excellence.