To Issue 168
Citation: Barichello E, “Container Selection for a Highly Sensitive Drug Product: A Success Story”. ONdrugDelivery, Issue 168 (Jan 2025), pp 22–25.
Enrico Barichello discusses Stevanato Group’s collaboration with a leading pharmaceutical company to identify a suitable container for a high-concentration monoclonal antibody. The partnership addressed key challenges and contributed to maintaining the drug’s stability and integrity throughout its lifecycle.
In the pharmaceutical industry, the selection of primary containers for new drug products is a critical step that can significantly impact the drug’s stability, efficacy and patient safety. The process involves a complex analysis of various factors, including the interaction between the drug and the container, the performance of the container under different conditions and the integration of the container into a drug delivery device such as an autoinjector.
These devices are designed to simplify self-administration of injectable therapies, giving patients greater autonomy in managing chronic conditions while reducing reliance on healthcare professionals and clinical visits. Despite their ergonomic exterior, autoinjectors are the result of a sophisticated design and manufacturing process.
A key element of these systems is the glass primary container, often in the form of a prefilled syringe (PFS). The syringe plays a critical role in maintaining the drug’s efficacy and safety until administration. When the device is activated, the syringe must withstand mechanical stress and handle the viscosity of the drug formulation. Failures, such as syringe breakage, can harm patients and disrupt manufacturing, especially when defects are worsened by high-viscosity or large-volume drugs.
“Integrating glass syringes with drug delivery devices presents several critical challenges that can impact both product performance and patient safety.”
THE CHALLENGES OF INTEGRATING GLASS SYRINGES WITH DRUG DELIVERY DEVICES
Integrating glass syringes with drug delivery devices presents several critical challenges that can impact both product performance and patient safety. One of the primary concerns is dimensional accuracy, which includes specific design features such as the syringe’s length, the rigid needle shield and the needle’s position and angle. Variations in these dimensions can lead to inconsistent injection depths, affecting the delivery efficacy and potentially resulting in missed doses.
Another significant challenge is functionality, which encompasses factors such as activation force, injection time and the break-loose and glide force of the syringe. If the required activation force is too high, the injection may not start, causing a missed dose. Similarly, if the injection time is too slow, patients might remove the device prematurely, leading to under dosing. Additionally, while the plunger must move during device use, unintended displacement during handling and shipping can compromise product integrity and sterility, posing risks to patient safety. This highlights the importance of an optimised design and a robust validation strategy.
Drug stability is also a critical parameter, particularly concerning the use of silicone oil, as well as the materials that come into contact with the drug. Excess silicone particles can lead to protein aggregation, resulting in a loss of drug efficacy or even immunogenicity. Moreover, additional materials in contact with the drug can increase the levels of extractable and leachable compounds, which may degrade the drug over time.
Lastly, the physical quality of the syringe is crucial, including its cosmetic appearance and resistance to breakage. Accumulation of physical defects can increase the risk of breakage, which not only poses a safety hazard but also increases the potential for missed doses.
Addressing these challenges requires a comprehensive and collaborative approach, leveraging advanced technologies and rigorous testing to ensure the optimal performance of the drug delivery system.
A SUCCESS STORY: STEVANATO GROUP TACKLING THE MOST COMPLEX CHALLENGES
A leading pharmaceutical company approached Stevanato Group with a specific challenge: it needed a new staked-needle PFS to be used in a disposable autoinjector for its high-concentration monoclonal antibody (mAb) product. mAbs are among the most sensitive drugs on the market, requiring advanced containment solutions and delivery systems. These drugs are particularly sensitive to interactions with the container and silicone particles, which can jeopardise drug stability and integrity.
During a benchmarking and stability study, the client had encountered out-of-specification injection times with other syringes in the market, a critical parameter that directly affects both the patient experience and drug delivery system efficacy. If not addressed, these out-of-specification results could lead to serious consequences, including project delays and potentially the need to change the primary container. This would not only delay commercialisation but also pose safety risks to patients.
APPROACH AND KEY OUTCOMES: A COMPREHENSIVE ANALYSIS FOR CONTAINER SELECTION
To address the challenges (Figure 1) posed by high-concentration mAbs, Stevanato Group leveraged the capabilities of its Technology Excellence Centers (TECs). The TEC team conducted a thorough analysis to identify the most suitable primary container. The first step in this process, supported by the company’s analytical services, was to gain a deep understanding of all the components involved in the container closure system. This included examining the materials used in the syringe, the specific silicone used for lubrication and the design of the needle and plunger. Each of these elements can interact with the drug product in unique ways, potentially affecting its stability and efficacy.
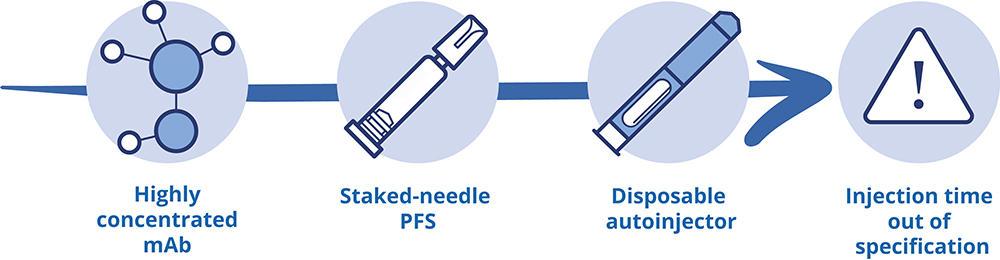
Figure 1: Initial challenges of the case study.
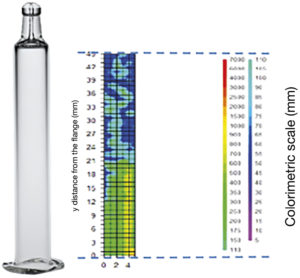
Figure 2: Example silicone layer (tested with Bouncer) showing depletion when in contact with the drug product.
A key part of this analysis was assessing the interactions between the drug and the container components using both the drug product and a placebo. By simulating the conditions under which the drug would be stored and used, the TEC team observed how the drug interacted with the container components. This step was essential in identifying potential issues, such as changes in drug stability or the formation of silicone particles. The investigation revealed that the thickness of the silicone layer inside the syringe was a contributing factor. It was found that the silicone layer depleted or thinned when in contact with the drug, due to the wettability effect, particularly with the use of standard sprayed-on silicone oil. Traditional siliconised syringes, for example, were found to have higher levels of silicone particles, which could interact with the drug and compromise its stability (Figure 2).
To solve this problem, the client decided to restart the packaging selection process. This time, they included the use of Alba® syringes, which have a cross-linked silicone coating (Figure 3).
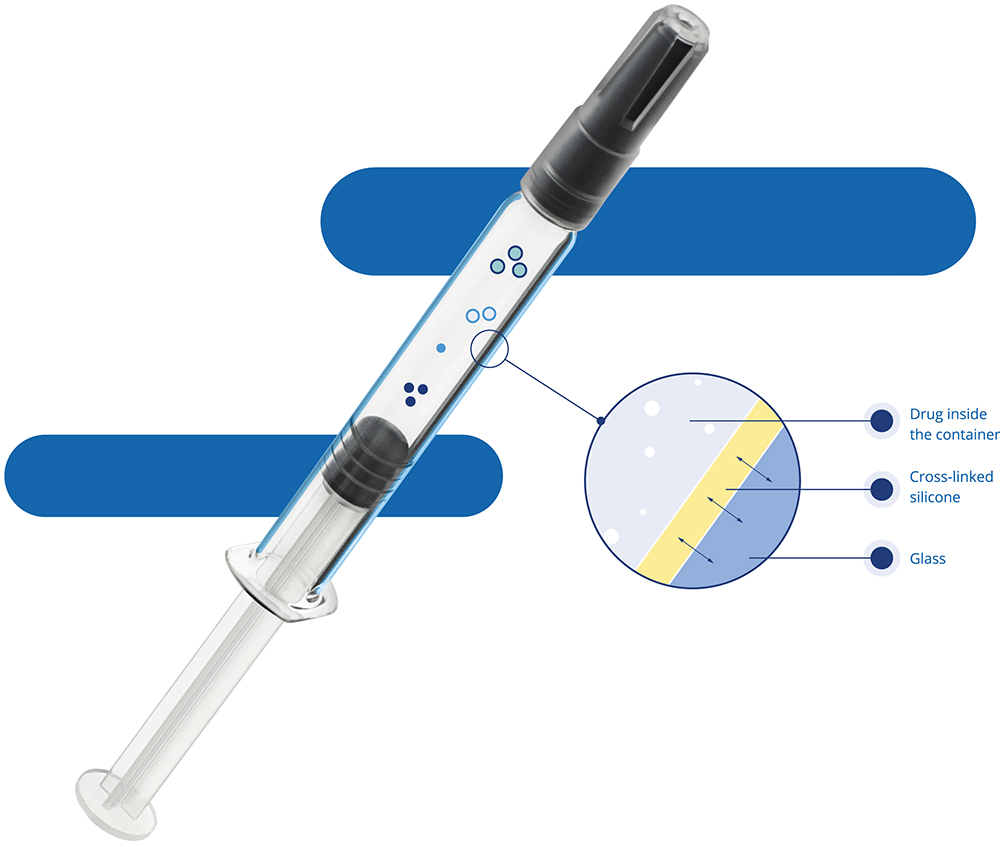
Figure 3: Alba® syringe featuring cross-linked silicone oil.
“The results showed that the cross-linked silicone coating used in Alba® syringes significantly reduced silicone migration, providing a more consistent and durable performance.”
The new syringes were filled with the drug product and stored at 40°C under accelerated ageing conditions for 1.5 months and three months to simulate one year and two years of shelf life at 5°C. The tests conducted included silicone thickness and distribution, glide forces, injection time and particle analysis. The results showed that the cross-linked silicone coating used in Alba® syringes significantly reduced silicone migration, providing a more consistent and durable performance. This helped minimise the depletion of the silicone layer (Figure 4).
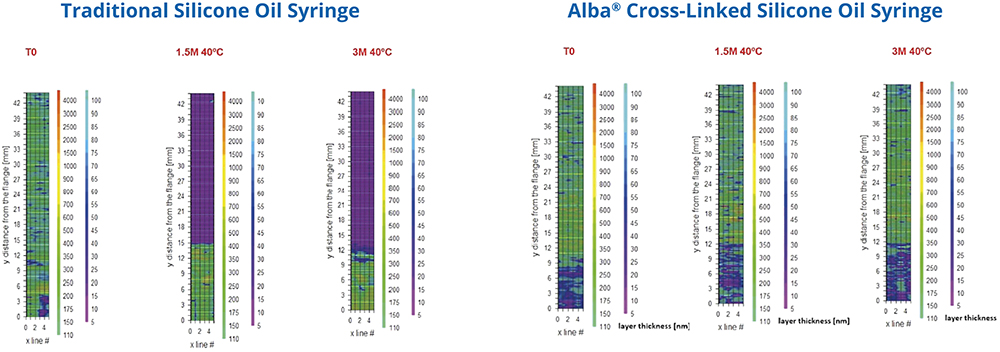
Figure 4: Higher stability of Alba® syringe compared with traditional silicone oil syringe.
In addition to reducing silicone particle levels, Alba® syringes also demonstrated consistent and predictable glide force over time, compared with the standard sprayed silicone oil category. This was shown through a boxplot analysis of extrusion force, which revealed stable performance over an accelerated ageing period of three months at 40°C/75% RH (Figure 5).
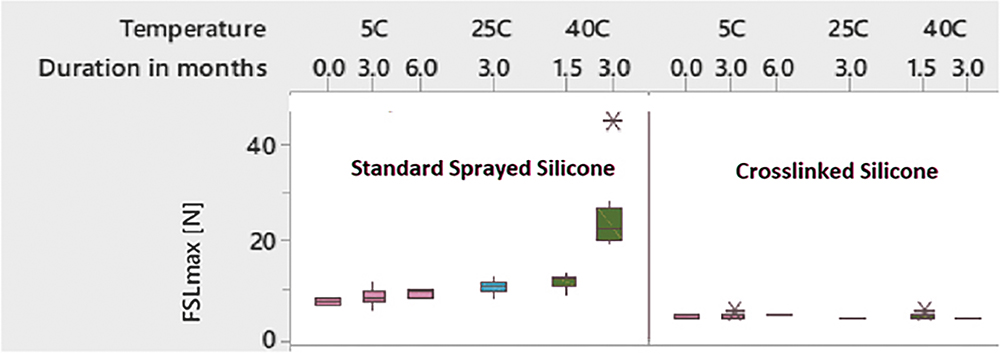
Figure 5: Lower extrusion forces over time and temperature ranges tested.
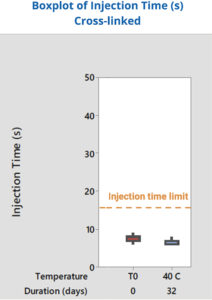
Figure 6: Injection time within specification.
Another crucial part of the analysis involved investigating the integration of the syringe with the drug delivery device. This required evaluating how the container would perform when assembled into the autoinjector and whether it would meet the necessary specifications for injection force and time. Because Alba® syringes demonstrated a stable, predictable glide force, they also successfully met the injection time requirements – in this case, less than 15 seconds – over time. This consistency ensured that the syringes adhered to the specified injection times, addressing the client’s primary concern (Figure 6).
KEY BENEFITS OF ALBA® SYRINGES AS DEMONSTRATED BY TECs’ ANALYTICAL CAPABILITIES
The comprehensive analysis revealed that Stevanato Group’s Alba® syringes were the optimal solution for the client’s high-concentration mAb formulation. Alba® syringes are designed with advanced technology that improves upon standard silicone by cross-linking it for exceptional stability and resistance to breakdown. This innovative approach provides multiple key benefits:
- Consistent Extrusion Force: The cross-linked silicone coating ensures a consistent and predictable glide force for the syringe, which is critical for the performance of autoinjectors. This consistency helps to maintain the specified injection time, addressing the client’s primary concern.
- Reduced Silicone Migration: The cross-linked silicone oil layer on the inside of the syringe barrel significantly reduces silicone migration. This minimises the risk of drug-container interactions and the formation of silicone particles, which can compromise drug stability.
COLLABORATION AND DATA-DRIVEN SUPPORT
Stevanato Group’s success in this project was not only due to its advanced technology but also its collaborative approach. From the early stages of the project, the company worked closely with the client to understand their specific needs and challenges. This collaboration involved regular face-to-face visits, which allowed Stevanato Group to strengthen the relationship with the client and gain a deep understanding of their requirements.
Stevanato Group’s TECs provided comprehensive data-driven analysis to support the client’s decision-making process. This included detailed performance data and insights into how the drug interacted with the container components. This is particularly important for the integration of the syringe in delivery devices such as autoinjectors. Stevanato Group’s TECs can help clients decide on the appropriate tests and take care of the development, optimisation and validation of the method, based on their specific drug product requirements.
The success of this leading pharmaceutical company highlights the importance of collaborating as early as possible with container suppliers that have strong analytical capabilities in the development of new drug products.