Citation: Quintata N, “AltaVISC: Expanding the Delivery Window for High-Viscosity & High-Volume Drugs”. ONdrugDelivery, Issue 166 (Oct 2024), pp 63–68.
Nelson Quintana discusses how Altaviz‘s AltaVISC delivery technology reaps the benefits of gas-powered drive systems over traditional spring-based systems for autoinjectors to offer a highly flexible platform technology for drug developers, allowing them to optimise their formulations within a wider range of delivery device specifications.
THE NEXT-GENERATION DELIVERY SYSTEM: ALTAVISC
Patient-centric approaches are driving researchers to carefully balance the connected elements of drug concentration, viscosity and delivery volume in their ongoing efforts to optimise pharmacological dosing levels. To ascertain whether they can successfully accomplish their goals, they also need to assess the limitations of the current drug delivery landscape. The pursuit of more patient-friendly, longer-acting therapies is driving the development of treatments with increased delivery volumes and viscosities.
With higher viscosity and larger volumes, standard spring-powered autoinjectors must employ bigger springs to deliver their therapies in a reasonable time, which results in increased impact forces, leading to syringe breakage in conventional prefilled syringes (PFSs). Additionally, companies are being forced to gravitate towards the use of high-performance polymer syringes as a substitute to glass syringes due to the need for increased toughness. Doing so comes with significant costs and regulatory challenges, as this restriction presents a major obstacle in the development of novel medications.
“There is an urgent need for a next-generation drug delivery technology that surpasses the capabilities of legacy technologies.”
The significant forces generated by larger springs also necessitates careful study of the delivery techniques for these high-volume and high-viscosity medicines. Furthermore, the loud impact noise generated during delivery can negatively affect the user experience, particularly for patients with a fear of injections. Therefore, there is an urgent need for a next-generation drug delivery technology that surpasses the capabilities of legacy technologies and is capable of supporting the current evolution of drug delivery development.
Companies are confronted with the question, “Is there an adequate delivery technology that can fulfil these requirements, support future formulation development, minimise the need to overhaul current devices and expand the therapies that can be delivered in standard glass primary containers?” The simple answer is yes – gas power. With a gas-powered AltaVISC drug delivery system, using Picocyl‘s Pico-Cylinder gas cylinders, one size truly can fit all.
OVERLOOKED BENEFITS OF GAS-POWERED DELIVERY SYSTEMS
The AltaVISC gas-powered delivery system marks a substantial leap in next-generation drug delivery technology, offering many advantages over conventional spring-powered devices (Table 1).1 By enabling both the use of smaller gauge needles, even for drugs with higher viscosities, and emerging therapeutic approaches, such as sequential administration and reconstitution, these gas-powered devices aim to reduce pain and enhance patient comfort. The consistent and controlled injection process that gas power provides ensures reliable and precise drug delivery.
Benefit | Specifics |
Handling of low to ultra-high viscosities | 1–5,000 cP as standard, however, viscosities up to 500,000 cP have been demonstrated. |
Payload volumes | Volumes up to 5 mL with standard syringes. Other volumes possible with custom syringes. |
Payload volumes | Ease of performance can be tuned for different viscosities to achieve different delivery times by just changing the pressure in the Picocyl gas cylinder. |
Standard syringe sizes | 1–2.25 mL and 5 mL ISO 11040 standard syringe sizes. |
Primary drug container performance expansion | Ability to use standard primary glass drug containers for a wider range of high-viscosity and high-volume formulations. Even higher viscosities and volumes can be delivered by switching to polymer syringes. |
Sustainability oriented | No large springs required, less need for performance plastics and uses inert gases that have no global warming potential. |
Easier customisation | Gas-powered engine can be implemented into various therapy delivery methods, such as on-body delivery systems and handheld infusion systems. |
Future-proof | Ability to handle extremely large-viscosity and large-volume ranges, as well as supporting emerging technologies, such as sequential and reconstitution therapies. Allows researchers to focus on formulations over delivery technology. |
Use of smaller needles | Ability to use standard needle gauges as well as smaller needle sizes due to increased gas-powered performance. |
Versatile gas-powered engine | The gas-powered engine can be implemented into other methods of drug delivery for maximum product development flexibility. |
Table 1: Benefits of the AltaVISC drug delivery system.
AltaVISC’s user-friendly design, featuring soft-start technology, simplifies the injection process, leading to a comfortable user experience and better therapy compliance. Furthermore, since the energy source is stored within the Pico-Cylinder until time of use, the need for costly, high-performance polymers to mitigate the strain inherent in the storage of high force springs is eliminated.
A significant advantage of gas-power technology is the integration and expansion of existing and future product pipelines into a single device configuration. This versatility minimises the impact on upstream and downstream processes, including tooling, inventory management, automation, validation and the complex procedures required for changeovers to accommodate varying viscosities and delivery rates.2 Remarkably, these adjustments can be accomplished with a simple modification of gas pressure within the Pico-Cylinder.
“A simple adjustment of gas pressure can tailor the autoinjector delivery time to mimic early-stage trial results, which can then minimise regulatory hurdles and setbacks.”
The versatility of the gas-powered drive system allows pharmaceutical companies to efficiently transition therapies developed during preclinical and early-stage trials to autoinjectors without needing to redo lengthy biocompatibility and stability studies. A simple adjustment of gas pressure can tailor the autoinjector delivery time to mimic early-stage trial results, which can then minimise regulatory hurdles and setbacks.
FAVOURABLE FORCE PROFILE OF GAS-POWERED DELIVERY
The inherent gentle start of gas-powered delivery ensures that the impact force never exceeds the delivery force and maximises the viscosity range of formulations that can be delivered using standard glass PFSs. The high forces needed for delivering large volumes or highly viscous fluids, which used to raise concerns about switching the drug container due to the risk of breakage, can now be reduced by using gas power to control the delivery process.
Primary glass PFS containers in spring-driven systems experience a force spike caused by the plunger rod accelerating into the stopper. In contrast, a gas-powered system offers a gentle soft-start and controlled delivery, thereby expanding the operational window of currently used primary drug containers and prolonging their useful life in a product offering. The floating low-mass plunger rod approach in the AltaVISC system reduces the gap to the stopper and the inertia of the plunger rod to limit the impact force on the syringe to below the force required to deliver the drug.
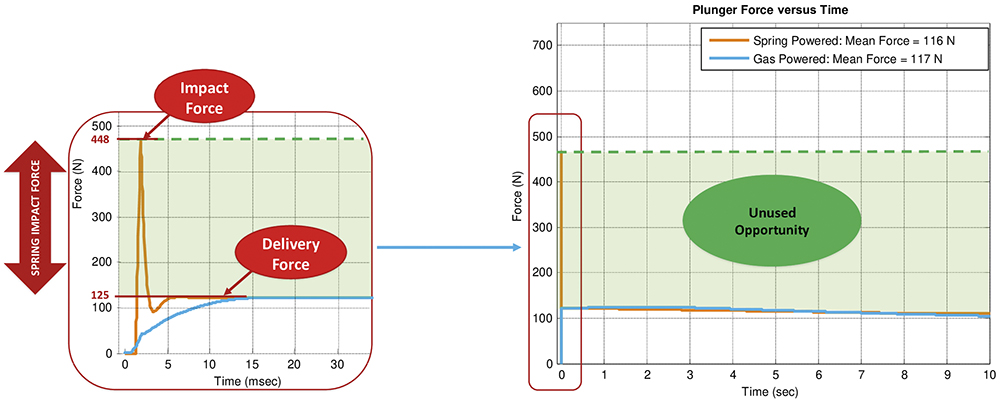
Figure 1: MATLAB simulation comparison of impact forces experienced between the AltaVISC drug delivery system and a traditional spring-driven system.
To illustrate the advantages of the AltaVISC soft-start technology, the MATLAB simulation shown in Figure 1 compares two delivery profiles – the AltaVISC system and a traditional spring-driven system, both configured to deliver 2 mL of 100 cP fluid through a ½” 27G needle.3 The simulation results indicate that, while the overall force required to deliver the drug is similar across technologies, the initial impact force of the spring-based system is four times higher than the delivery force. This spike in impact force increases the risk of syringe breakage and creates an unpleasant patient experience due to the force and noise generated when the plunger rod strikes the syringe stopper. Alternatively, the gas-powered system exhibits a smooth ramp up to the delivery force (blue line, left graph), minimising the stress on the primary container and thereby expanding the operational window of the delivery system as shown (green line, right graph).
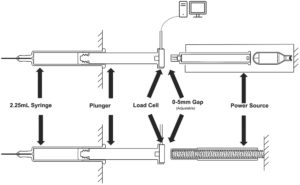
Figure 2: Impact test data acquisition fixture.
A fixture (Figure 2) equipped with a load cell and a data acquisition system (4.8 kHz) was developed to measure the actual forces applied directly to the syringe stopper, highlighting the significant difference between the AltaVISC gas-powered delivery system engine and a traditional spring-based system. The fixture also has the capability to add a gap in between the plunger rod and stopper to replicate current spring-powered devices.
To demonstrate the flexibility of soft-start technology, an impact test was performed with two vastly different viscosities (10 and 500 cP) with a 5 mm gap, as is commonly used in traditional spring-powered systems, using a 2 mL volume in a 2.25 mL syringe with a ½” 27G needle. As shown in Figure 3, even with a low viscosity of 10 cP delivered at 80 bar with a 5 mm gap, the impact force remains below the maximum delivery force. Similarly, with an ultra-high viscosity of 500 cP delivered at 350 bar with the same gap, no significant impact force is observed. These results demonstrate the robustness of the delivery system across a wide range of viscosities, maintaining controlled force levels under varying assembly conditions. This is of enormous benefit to glass-PFS-based devices.
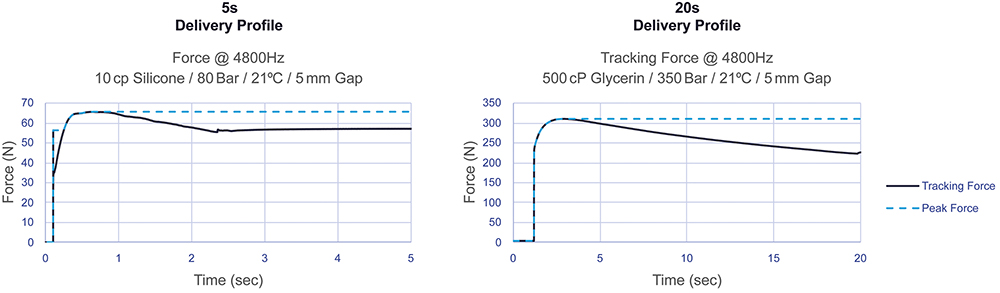
Figure 3: AltaVISC 5 mm gap impact profiles with high-viscosity fluid were generated by varying only the gas pressure.
In contrast, Figure 4 illustrates a 40 N spring-powered system delivering a 2 mL volume in a 2.25 mL syringe with a ½” 27G needle. Due to the inherent nature of spring energy release, the initial force exerted on the stopper significantly exceeds the force required to deliver the drug. This effect becomes more pronounced for higher-viscosity and higher-volume applications, which require stronger springs to meet the target delivery times. This relationship is a major contributor to syringe breakage in spring-powered systems and the need to consider alternative primary container materials, highlighting the limitations of spring technology for delivering high viscosity or high-volume drugs.
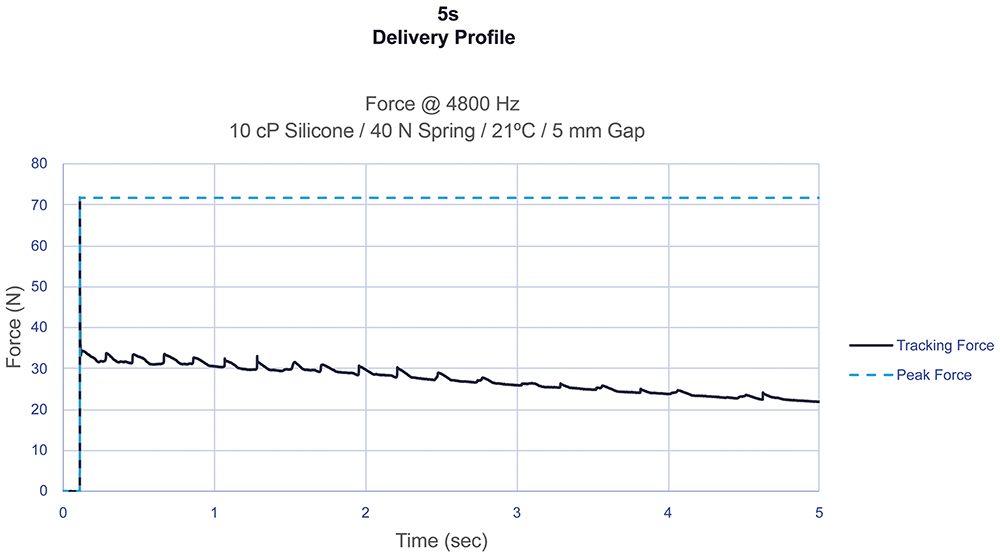
Figure 4: Spring-powered impact profiles with low-viscosity fluid.
As shown in Figure 1, the spring-powered system at 100 cP generates an impact force of approximately 448 N, despite this being at only one-fifth of the viscosity of the 500 cP test in Figure 3 using gas power. Notably, the impact force at 100 cP with the spring-powered system is 323 N higher than the total force of 125 N required to deliver the much higher viscosity of 500 cP with a gas-powered system (Figure 3). This comparison highlights the significant limitations of spring-powered systems compared with the gas-powered AltaVISC system.
A SINGLE FRAMEWORK TO MEET ALL DELIVERY REQUIREMENTS
The AltaVISC drug delivery system is a next-generation technology standard that supports the delivery of new therapies without sacrificing performance for the foreseeable future. Using the same system architecture, the AltaVISC system can meet a variety of different delivery requirements by simply altering the pressure inside the gas cylinder.
Figure 5 shows a tuned delivery time target at different viscosities achieved with only a Pico-Cylinder pressure change, illustrating the precise tunability and flexibility of the AltaVISC drug delivery system. In this experiment, 2 mL of glycerol with varying viscosities were delivered via an AltaVISC system using a 2.25 mL syringe and a ½” 27G thin-wall needle, targeting a distinct delivery time of 18 seconds. The device configuration remained the same, and performance adjustments were achieved solely by modifying the internal pressure of the Pico-Cylinder.
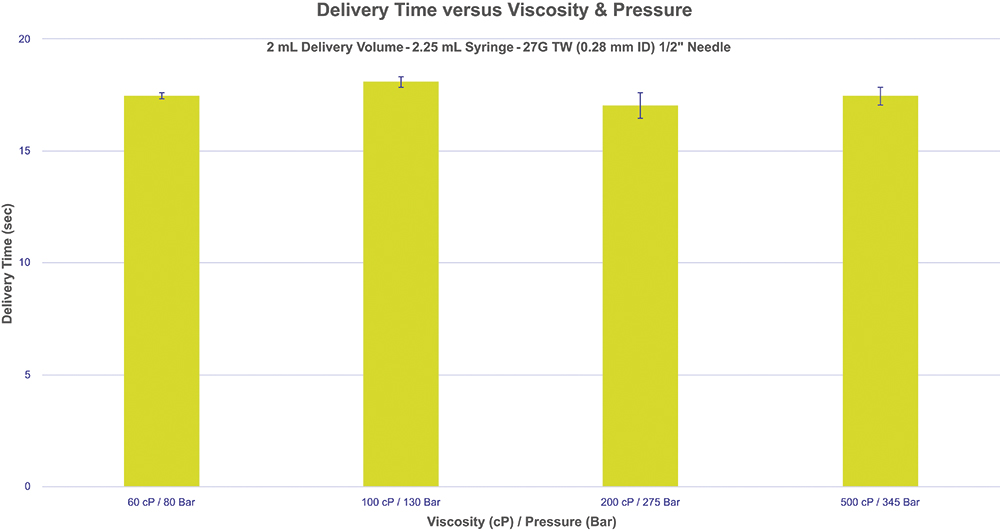
Figure 5: Delivery time target at different viscosities achieved with only a gas pressure change.
During the first series of tests, five syringes were tested for each viscosity level (60–500 cP) to demonstrate that an 18 second delivery time can be consistently attained by adjusting the Pico-Cylinder gas pressure, regardless of the viscosity. This flexibility expands the allowable formulation parameters, allowing scientists to concentrate fully on optimising formulation development. The data also illustrate the various combinations of gas pressures and viscosities that can be fine tuned to achieve a desired delivery time, optimising both user experience and the syringe’s performance window.
“By overcoming the limitations and risks associated with spring-powered systems when increasing viscosities and volumes companies can now explore the use of smaller needle gauges, which were previously deemed unfeasible.”
This performance also underscores a significant advantage of gas-powered systems. By overcoming the limitations and risks associated with spring-powered systems when increasing viscosities and volumes, companies can now explore the use of smaller needle gauges, which were previously deemed unfeasible. This advancement not only broadens design possibilities but also reduces patient discomfort by eliminating the need to increase needle gauge due to the constraints of spring-powered systems.
The AltaVISC delivers high-viscosity and high-volume drug formulations using small-gauge needles – regardless of the viscosity or volume of a therapy, meaning that the user experience is always at the forefront of consideration. Smaller gauge needles can help improve pain tolerability, precision and control, as well as minimise the psychological effects on users. Companies now have the additional flexibility of choosing which needle gauge size is the best fit for their subcutaneous or intramuscular delivery approaches.
HIGH-PERFORMANCE WITHOUT SACRIFICING THE USER EXPERIENCE
Human factors and user experience are crucial in advancing high-performance drug delivery systems, ensuring that products are tailored to the needs, capabilities and limitations of users, thereby enhancing usability, safety and overall performance. A prevailing concern in the industry is the reluctance of companies to be early adopters of innovative technology. To help address this, the development of the cutting-edge AltaVISC framework emphasises human factors and user experience engineering, ensuring that devices are not only safe but also user friendly and effective, while maintaining a familiar workflow for users of legacy spring-powered autoinjectors.
“The AltaVISC system effectively combines the benefits of a high-performance gas-powered engine with the ease of use found in legacy spring-powered autoinjectors.”
By preserving consistent user workflows across various products, Altaviz facilitates seamless transitions between devices, minimising the need for extensive retraining, particularly for those accustomed to spring-powered systems. The AltaVISC system effectively combines the benefits of a high-performance gas-powered engine with the ease of use found in legacy spring-powered autoinjectors, successfully addressing challenges associated with higher viscosity and higher-volume applications. The soft-start mechanism of the gas powered drug delivery system facilitates the ability to reduce needle size thereby reducing pain while also further improving the patient experience by eliminating the jarring impact force and noise associated with spring driven systems.
THE FUTURE OF HIGH-VISCOSITY, HIGH-VOLUME DRUG DELIVERY
Currently, there is a significant lack of information regarding the user experience with high-volume, high-viscosity drug delivery applications, particularly in understanding the thresholds of volume, viscosity and delivery time that an end user can tolerate. This gap in knowledge largely stems from the absence of high performance devices that are both configurable and capable of successfully meeting these demanding parameters. The introduction of the AltaVISC drug delivery system addresses this need, enabling the industry to begin collecting critical usability data that will help guide the development of new therapies.
The AltaVISC framework represents the future of drug delivery systems. This evolution in flexible and customisable next-generation technology can help companies to get to market sooner by allowing the focus to be on formulation development and not worry about the suitability of current delivery limitations or having to find a suitable technology.
At the core of the AltaVISC system is the gas-powered Pico-Cylinder. Released to the market in 2017, with over 10 million units in the field without a single failure, the Pico-Cylinder has a five-year shelf life ensuring a reliable delivery for even the most critical applications. Coupled with the Pico-Cylinder power source, the AltaVISC drug delivery system is poised to lead the future of drug delivery technology.
REFERENCES
- Whelton R, Green P, “Autoinjectors: Historical Achievements and Compelling Needs Driving Next-Generation Devices”. ONdrugDelivery, Issue 138 (Oct 2022), pp 14–17.
- Welch W, “Advancements and Evolution of Power Sources in Drug Delivery”. ONdrugDelivery, Issue 133 (May 2022), pp 57–60.
- McCawley M, Lavin A, “Gas-Powered Autoinjector Platform Enables Biologics Drug Delivery”. ONdrugDelivery, Issue 138 (Oct 2023), pp 50–54.