Citation: Scatena A, “Beyond Probability: Choosing Deterministic Methods for Reliable Container Closure Integrity Testing”. ONdrugDelivery, Issue 166 (Oct 2024), pp 58–62.
Antonio Scatena answers some of the most common questions regarding the container closure integrity testing methods used to detect leaks and defects – and discusses how the industry can meet the updated expectations set by regulatory bodies.
Container closure systems are critical for ensuring the integrity and safety of drugs. This is particularly important as modern developments focus on biologic drugs, which are increasingly complex and sensitive. Given the escalating costs of bringing such drugs to market, minimising the risk of failure at every stage of the development journey has become an essential endeavour for ensuring the success of drug development.
Primary packaging is in direct contact with the drug and plays an essential role in safeguarding its properties from the time of filling to patient administration. Although primary packaging manufacturers can provide data to de-risk the choice of container system, it is the responsibility of the drug developers to demonstrate compatibility with the drug formulation and container closure integrity (CCI) using methodologies that are fit for regulatory requirements.
“It is the responsibility of every drug manufacturer to demonstrate that their containers – such as vials, syringes and blister packs – meet the stringent regulatory compliance requirements.”
WHAT IS CCI TESTING AND WHY IS IT IMPORTANT?
CCI testing evaluates the ability of a container closure system to maintain a sterile barrier against potential contaminants to ensure the quality and safety of the drug contents throughout the product’s lifecycle. It is the responsibility of every drug manufacturer to demonstrate that their containers – such as vials, syringes and blister packs – meet the stringent regulatory compliance requirements set by bodies such as the US FDA, the EMA and other global health authorities to ensure patient safety.
For de-risking purposes, packaging suppliers can generate drug-agnostic data using deterministic or probabilistic CCI testing methods. This data can give drug manufacturers clear indications of a container solution’s expected performance.
PROBABILISTIC TESTING VERSUS DETERMINISTIC TESTING METHODS
USP Chapter <1207> “Package Integrity Evaluation – Sterile Products” defines probabilistic and deterministic CCI testing methodologies and outlines the differences between the two.
A probabilistic leak test method detects a series of sequential and/or simultaneous events, each associated with uncertainties described by probabilistic distributions, where the sample size must be determined based on the probability of the described event to occur. The lower the probability of a leak occurring, the larger the sample size required.
In contrast, a deterministic leak test method is one in which the leakage event is based on phenomena that follow a predictable chain of events that can be measured using physicochemical technologies and readily controlled and monitored to yield objective quantitative data.
“Specific differential pressure, partial pressure or electric potential can be capable of reproducibly detecting leaks at clearly defined and predictable detection limits.”
For example, deterministic methods can rely on the predictable establishment of a gas or electrical flux that inevitably occurs through an open leak. In such cases, specific differential pressure, partial pressure or electric potential can be capable of reproducibly detecting leaks at clearly defined and predictable detection limits.
In recent years, regulatory agencies have been challenging companies over their choice of CCI testing methods. They have questioned the sensitivity and reproducibility of probabilistic CCI testing methods and encouraged the use of deterministic methods for new products, as they offer more reliable and precise measurements of CCI. It is important to note that these bodies do not prescribe specific CCI testing methods but instead expect companies to provide a clear rationale for the methods chosen, emphasising the importance of rigorous validation and the fit between the method and the product-package configuration.
The use of controls in CCI testing is a critical area of focus. Regulators prefer to see controls filled with the actual drug product or the most representative simulant available – as opposed to water or empty containers – to ensure that the testing conditions closely mimic real-world scenarios and provide more accurate and relevant results.
Products stored under frozen conditions appear to be another concern – particularly as cold storage can cause temporary seal failures that may not be detectable when the container returns to ambient conditions. Regulators are interested in how test methods can detect these transient leaks to ensure the integrity of the container is maintained at all times during cold storage.
Shipping and transportation studies are another area of focus that regulatory bodies expect companies to consider – to ensure that the product remains intact from the factory to the patient. For example, pressure changes that occur during air freight are known to put unusual strain on containers and can cause leaks that would not be identified in regular conditions.
DOCUMENTATION COVERING CCI TESTING
As test methods evolve quickly and regulatory bodies have shown increased attention to drug safety over the years, there have been many updates to documentation governing CCIT testing.
USP Chapter <1207> (revised in August 2016) emphasises a lifecycle approach that covers selection, development, validation and the entire lifecycle of the product package. ASTM International – the global organisation that develops and provides standards for various industries and applications – has proposed method F2338-09, which provides a comprehensive standard for non-destructive leak detection via vacuum decay and is often cited by the FDA.
In Europe, GMP Annex 1 was recently revised to mandate CCI testing for all fusion-sealed containers of 100 mL or less, emphasising validation and a lifecycle approach. Additionally, USP Chapter <382> (effective from December 2025)addresses functional suitability, highlighting maximum allowable leakage limits and inherent package integrity, referring to USP <1207> for detailed guidance.
EXAMPLES OF DETERMINISTIC TEST METHODS
There are three main deterministic CCI testing methods that are performed at Gateway Analytical.
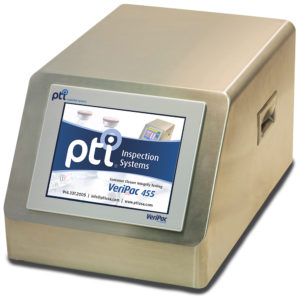
Figure 1: Vacuum decay inspection system used at Gateway Analytical.
Vacuum Decay
The vacuum decay methodology (Figure 1) works by measuring the level and change of vacuum over time. It is suitable for a wide variety of standard packages, such as vials, ampoules and prefilled syringes, but also flexible packages such as intravenous bags, lyophilised products, pouches and ophthalmic squeeze droppers.
The main advantages of the vacuum decay test are that there is no sample preparation involved – the testing is rapid and non-destructive, and it can be used to detect leaks caused by defects as small as 2 μm. Additionally, it is easy to quickly change between different container configurations, which is advantageous if you have multiple products to test within a short period of time.
However, there needs to be awareness of the properties of the product before using this method as it is unsuitable for products with a high viscosity or large molecules, as they may clog up the defect paths, thus preventing detection of the leak. This could also be the case for solidified products or debris that end up in the leak path and block leak detection. Additionally, in the case of a significant leak, liquid may be accidentally drawn by the system, which could damage the instrument.
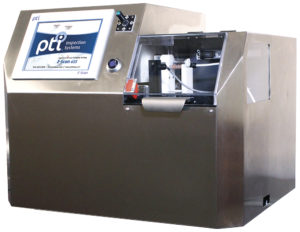
Figure 2: Example of HVLD equipment at Gateway Analytical.
High Voltage Leak Detection
The high voltage leak detection (HVLD) method (Figure 2) is an alternative method to vacuum decay that is well suited for products with large molecules or high viscosity. This method works by spinning the filled container and measuring the resistance differential as the instrument probes move up and down the body of the container, which assists in approximating the location of any defects.
As with vacuum decay, this test method can switch between different products quickly, requires no sample preparation and is sensitive to CCI defects down to 2 μm. While the test is typically non-destructive, products sensitive to electrical current may be affected during testing.
The main drawback of this method is that at least a 50% fill volume is required within the container to ensure that the inner walls are coated with liquid while the instrument is spinning. The product must also be more conductive than the packaging, and the operation of the equipment requires expertise.
Laser-Based Gas Headspace Analysis
Laser headspace analysis (Figure 3) works by using frequency modulation spectroscopy (FMS) and is often coupled with gas ingress to measure the partial pressure of carbon dioxide or oxygen gas concentration in the headspace of a product-package system. The technology supports rigid, cylindrical containers, such as vials, and can be used from ambient to cryogenic temperatures.
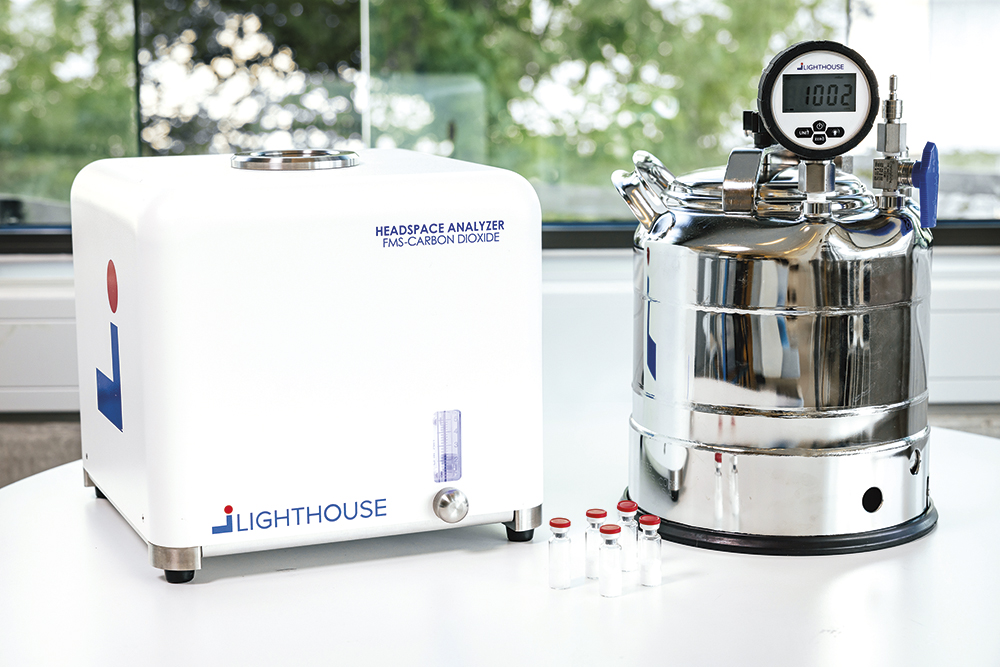
Figure 3: Laser headspace analysis system used to perform non-destructive CCI testing.
The main advantage of this methodology is that it can be used to detect transient leaks and temporary defects that occur during storage, even if those transient defects resolve during a temperature change – for example, when going from -80°C back to room temperature. The ingress of the gas has already occurred and can be measured. Similarly to the other two methods, this is a rapid and non-destructive test that can detect defects down to 2 μm and requires no sample preparation.
However, samples with a high fill volume may not be compatible with this method if the headspace is insufficient to allow for the laser to pass through. Additionally, the nature of the packaging itself may limit the feasibility of laser headspace analysis – for example, when using amber-coloured glass.
HYPOTHETICAL EXAMPLES
A hypothetical scenario is an aqueous, electrically conductive small-molecule product filled in a clear, rigid, cylindrical 2R glass vial with a volume of 1 mL. The vial is half full, with at least 3 mm of empty headspace that is atmospheric air. In this situation, all three methodologies would be viable options.
Now, taking the exact same scenario outlined above, but instead using a large-molecule product, vacuum decay would not be advised because the large molecules may obstruct the leak path and prevent detection. If the fill volume of the sample is increased, laser headspace analysis may no longer be appropriate because of the lack of headspace. Therefore, HVLD is the only suitable method for such a situation, thanks to the nature of the container, the electrical conductivity of the solution and adequate fill volume.
“All the CCI testing methodologies discussed here are equivalent in terms of efficiency and time; it comes down to pondering the advantages and weaknesses of each method in a given situation.”
FACTORS TO CONSIDER
All the CCI testing methodologies discussed here are equivalent in terms of efficiency and time; it comes down to pondering the advantages and weaknesses of each method in a given situation. The complexity of the method development depends on the combination of product and container closure system characteristics. Working out the recipe may take more or less time, depending on the situation, but one method does not necessarily take longer than another.
When it comes to choosing the correct CCI testing for a product package configuration, there are some key factors to consider. First, it is necessary to know the key specifications of the packaging: the outer diameter, height, additional components and the forces needed to combine them. This means providing information such as technical drawings and any items or equipment that are specific to the packaging.
In addition, it is necessary to know about the product characteristics, storage conditions and fill volume, such as the storage temperatures, molecule size, viscosity, conductivity and whether the sample produces any specific gas, which can usually be determined from the raw materials or safety data sheets.
If there are any specific requirements from regulatory bodies – such as a specific defect size or range, whether to demonstrate detection of transient leaks or the need to detect headspace or liquid leaks – Gateway Analytical can assist throughout the method development and feasibility studies of the test methodologies.
Find our more about Gateway Analytical’s CCI testing by clicking here.