To Issue 168
Citation: Jamal H, Köhler C, “Bonding Technologies for Injection Devices – a Quick Overview”. ONdrugDelivery, Issue 168 (Jan 2025), pp 44–48.
Hisham Jamal and Carsten Köhler discuss some of the bonding technologies used for medical devices – highlighting their unique strengths, limitations and suitability.
Almost every medical device has some form of bonding involved in its assembling process – where two or more parts are joined together securely by means of adhesive, heat, mechanical or chemical bonds. The bonding process used must uphold the integrity of the device through all the stages that it goes through from manufacturing to end use and function, thereby ensuring patient safety and treatment efficacy.
Over the years, teamtechnik, BBS Automation, Kahle Automation and Hekuma (all companies part of Dürr Group and soon to be renamed as BBS Automation) have assembled billions of different medical devices on their assembly systems. And almost all of the devices have undergone some form of bonding in the assembly process – giving the team a detailed insight into the commonly used bonding technologies, their advantages and challenges in high-volume production automation.
This article takes a look at some of the bonding technologies – namely, adhesive-based overmoulding and solvent-based bonding – that teamtechnik has used extensively on its assembly machines, highlighting their unique strengths, limitations and suitability. The objective is to provide a comprehensive overview on the application of these bonding technologies, paving the way for future innovation and efficiency in the production of life-saving medical devices (Figure 1).
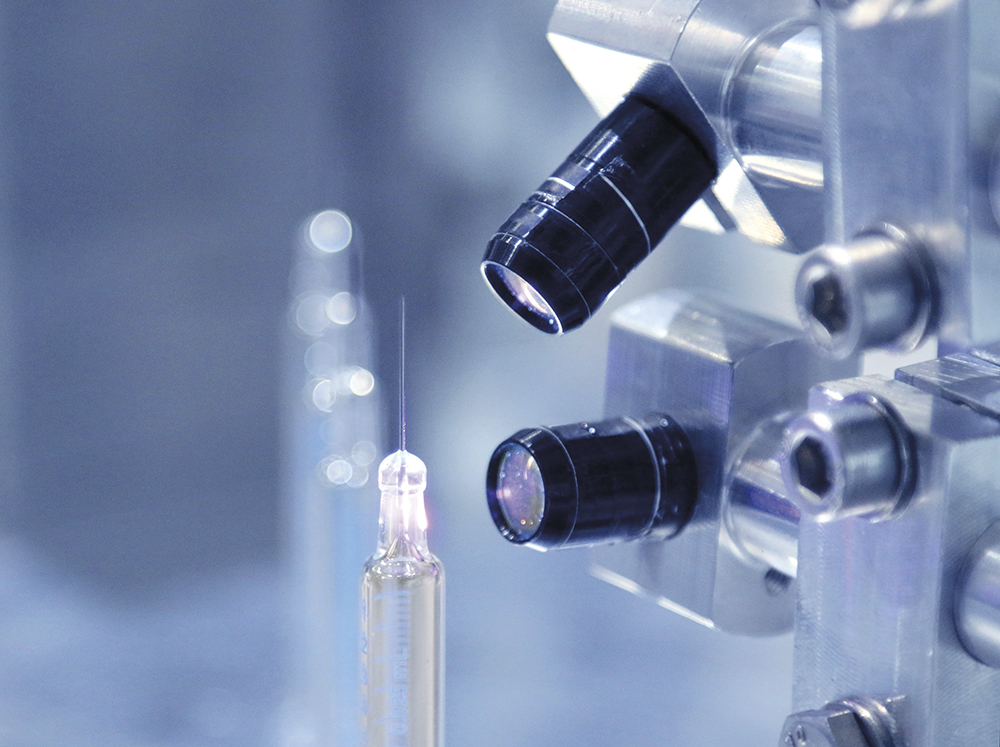
Figure 1: Glass syringe assembly – UV curing.
ADHESIVE BONDING
Adhesives are increasingly being used in medical device assembly to join similar or dissimilar materials together in a functional manner. This is particularly advantageous for needle bonding where a metal needle and a plastic housing are to be bonded together. Minimal or easy pre-treatment to prepare the surface for bonding, a cleaner manufacturing environment from lack of particles generated, and easy to automate by controlled dispensing, the process has made this bonding technology a preferred option in high-volume medical device assembly (Figure 2). The adhesives also act as a conductor, insulator, seal or tolerance bridge between the materials they are bonding, while maintaining property integrity of the materials. However, they are also subject to additional regulations when used in medical devices.
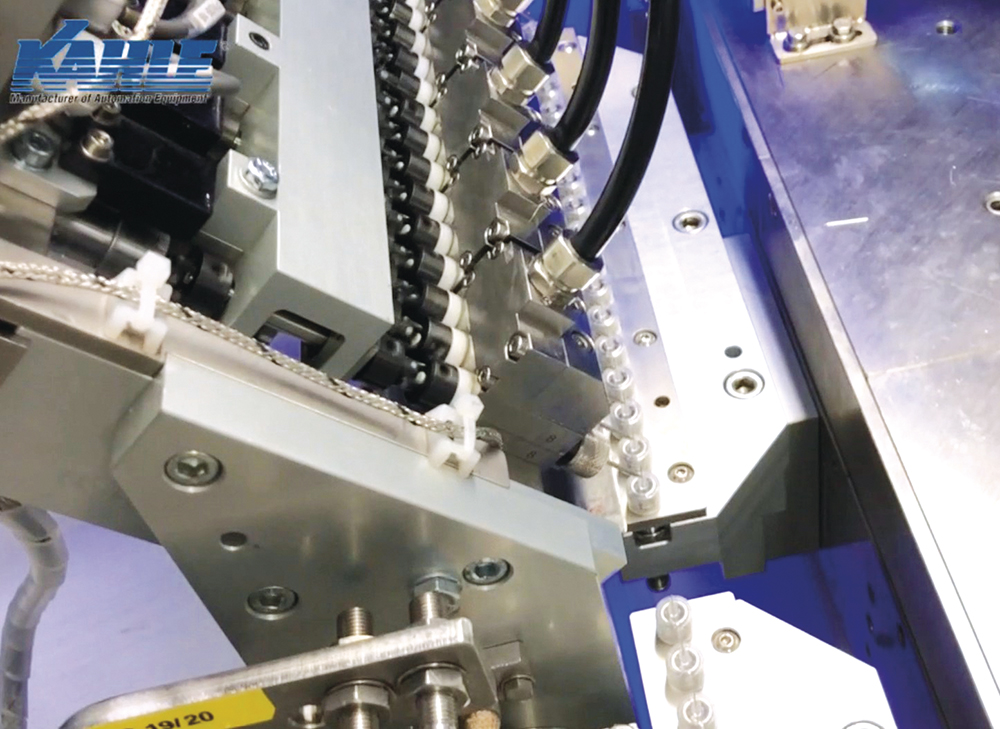
Figure 2: High-volume assembly line with adhesive dispensing.
“In medical device assembly, adhesives are governed by very stringent regulations to ensure their safety and efficacy.”
In medical device assembly, adhesives are governed by very stringent regulations to ensure their safety and efficacy. The US FDA regulates medical device adhesive under the Federal Food, Drug and Cosmetics Act, while the Medical Device Regulation (MDR) mandates the medical device adhesives to meet specific safety and performance criteria. For biocompatibility of the adhesive, both the MDR and FDA refer to the assessments outlined in ISO 10993.
At teamtechnik and Kahle, numerous assembly machines have been built for the manufacture of medical devices, such as cannulas, intravenous tube sets and glass syringes, among others, implementing adhesive bonding technologies. The following sections cover some specific cases.
EPOXY BONDING
Small, smooth and cylindrical joining interfaces between needles and hubs pose a complicated challenge in needle and syringe assemblies. This is where epoxy bonding has been extensively used over the years. Apart from effectively bonding cannulas to hubs, it also acts as a seal and prevents fluids, such as blood or medicine, leaking.
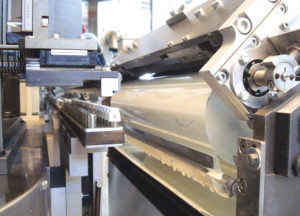
Figure 3: Epoxy glue dispensing.
Its low (per-volume) cost, high toughness post curing, and best thermal and chemical resistance has made epoxy curing a prominent bonding option in needle and syringe assembly. The higher flow (dwell) time of the epoxy adhesive, owing to its high-viscosity rates, does, however, pose a challenge for high-speed and high-volume production, as it can take quite some time for the epoxy adhesive to achieve full coverage of the joint. To overcome this, pre-assembly dispensing is often implemented, where the epoxy adhesive is dispensed on the cannula before it is set in its final position in the hub.
Another challenge that epoxy adhesives (Figure 3) pose to high-speed and high-volume production is their curing time, which can be up to 45 minutes, depending on the curing temperature. As epoxy adhesives are heat cured, setting up a high-temperature curing oven in clean rooms also poses another challenge for manufacturers when it comes to high-volume production. Finding a balance between the dispensing method, curing temperature and curing duration is essential in order to achieve an optimised production system.
“With lower viscosity and faster curing time, acrylic adhesives are increasingly being used in the assembly of medical devices.”
ACRYLICS
With lower viscosity and faster curing time, acrylic adhesives are increasingly being used in the assembly of medical devices, even replacing epoxy bonding at times. At teamtechnik, various assembly machines have been built for drug delivery systems and diagnostic devices where acrylic adhesives are used. These are adhesives where a photo initiator is present, which, upon exposure to light of a certain intensity and spectral output, will initiate a photochemical reaction that cures or hardens the adhesive.
With a rapid curing time of less than 10 seconds in the right curing environment, combined with the generally low viscosity levels, acrylic adhesives are an ideal bonding solution for high-speed and high-volume production automation for medical devices. The challenges here, however, lie in:
- Setting up the ambient environment for the curing process, as the presence of oxygen or humidity can inhibit surface cure, resulting in a somewhat sticky surface
- Using UV light sources with the right spectral output depending on the required cure depth, material opaqueness, etc.
Numerous assembly lines have been built by teamtechnick implementing UV-based glue technology for medical devices such as needles and syringes, pen needles, glass syringes (Figure 4), catheters, tubes and connectors, among others. After applying the adhesive on the bonding area and assembling the components, the device is then exposed to UV light. Depending on factors, such as material properties, opacity, depth of curing and others, UVA and/or UVC wavelength ranges are often used. While UVA ranging from 315 to 400 nm are typically used for most applications, the relatively new UVC LED technology is rapidly improving and gaining popularity in certain applications.
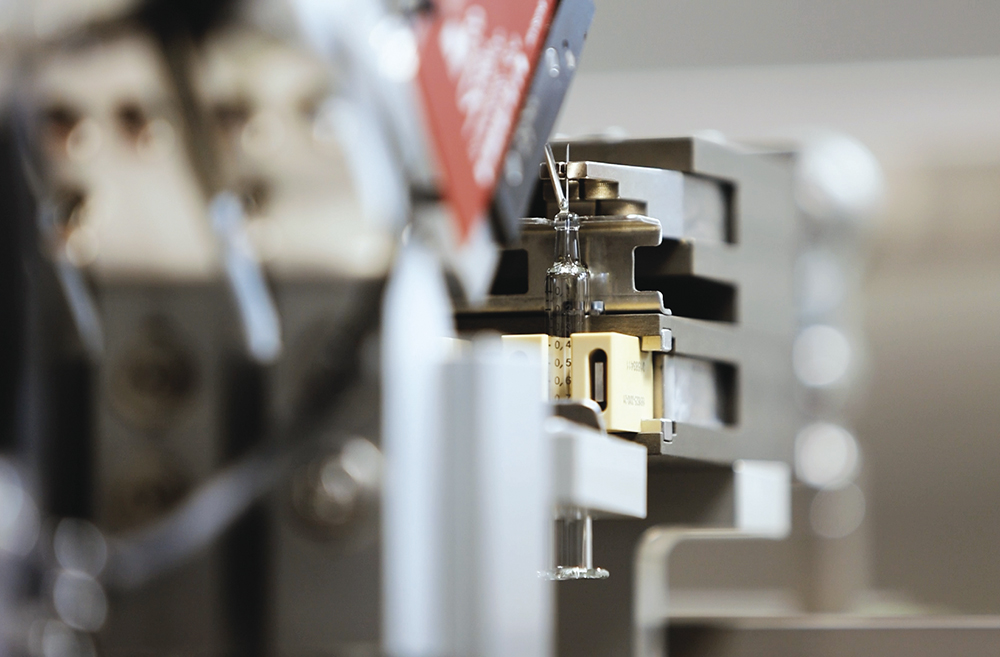
Figure 4: UV glue dispensing – glass syringe assembly.
The UVA with its higher wavelength helps to penetrate deeper, making it an ideal option for thicker curing or for applications on more opaque materials. The UVC on the other hand, with its lower wavelength and higher energy levels, is more effective for surface curing. In the applications that teamtechnick has implemented on its assembly machines, it uses either or a mix of both UV ranges to ensure effective curing with the desired surface finish.
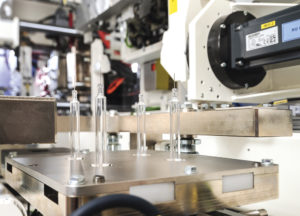
Figure 5: COP-syringe assembly line.
INSERT MOULDING FOR POLYMER SYRINGES
In recent years, polymer syringes – particularly cyclic olefin polymer (COP) – have been gaining popularity due to their high break resistance, glass-like transparency and inertness levels. This has made COP syringes a good alternative to glass syringes in many cases. COP syringes have also found their way into autoinjectors, replacing the traditional glass prefilled syringe.
Compared with glass syringes or other cannula and hub assembly methods where an adhesive is normally used, polymer syringes have a completely different approach to manufacturing where it is overmoulded. Overmoulding is a technique where the needle and syringe barrel are combined into a single integrated component. Here, a plastic syringe barrel is injection moulded around a pre-inserted needle, creating an integrated design that simplifies the assembly process, while enhancing reliability and ensuring a leak-proof seal (Figure 5).
“The key to a successful COP overmoulding process lies in being able to handle the injection-moulding parameters (such as mould design, tooling and pressure) just as well as preparation of the cannula.”
The key to a successful COP overmoulding process lies in being able to handle the injection-moulding parameters (such as mould design, tooling and pressure) just as well as preparation of the cannula (such as cannula handling and surface treatment). A strong understanding of this process, combined with state-of-the-art robotic technology for injection-moulding handling systems, has helped Hekuma develop multiple high-volume COP syringe manufacturing lines for customers.
SOLVENT BONDING
Solvent bonding is another technique used to bond needles and hubs together, particularly in the context of soft hubs. Here, a solvent is applied on the hub surface that temporarily softens or dissolves the surface of the material. A needle is then inserted into the hub.As the solvent evaporates, materials fuse together, creating a strong and seamless bond. The soft hubs are often made of flexible thermoplastics compatible with solvent bonding, and the needle, typically made from stainless steel, serves as the rigid component in the assembly onto which the soft hub is bonded.
The evaporation of the solvent also typically occurs quickly in the right environment, leading to rapid bonding and very fast curing times. This makes this technology a preferred choice in high volume- production processes where speed is of paramount importance (Figure 6). A point to consider here is the need for a good ventilation/exhaust system where the solvents are used.
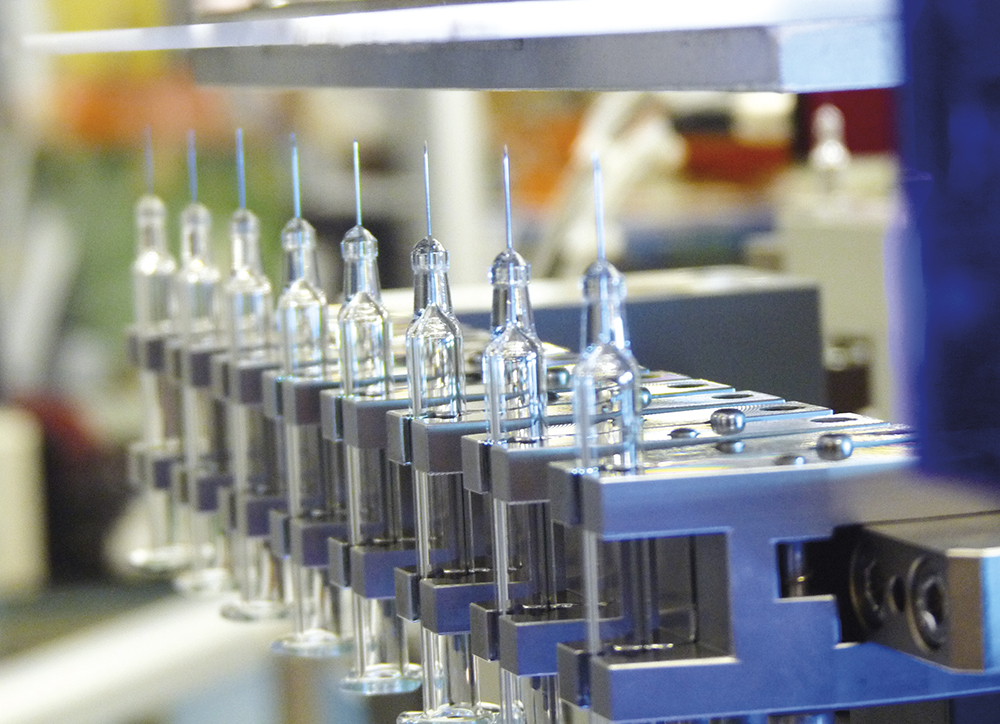
Figure 6: Glass syringe assembly line.
CONCLUSION
As the medical device industry continues to evolve, the need for innovation and adaptive assembly solutions becomes increasingly crucial. Adhesive-based, overmoulding and solvent-based bonding technologies have been in use for many years now, and they continue to innovate and offer unique advantages to enhance the high volume production of medical devices while improving their efficiency, reliability and safety. Table 1 summarises the features of the different bonding technologies discussed in this article.
Bonding Technology | Curing Medium | Curing Time | Products Commonly Used |
Epoxy | Heat | 10–20 mins | Needles & Syringes |
Acrylics | UV Light, Heat (depending on initiator) |
<10 seconds | Needles & Syringes, Catheters, Tubes & Connectors |
Insert Moulding | Air Cooling | <1 min | Needles & Syringes |
Solvent Bonding | Air | <5 seconds | Catheters, Tubes & Connectors |
Table 1: Summary of bonding technologies discussed.
By carefully considering the strengths, limitations and specific requirements of each technique, manufacturers can select the most appropriate bonding methods for their specific needs. And with its expertise in implementing these technologies on billions of devices, teamtechnik continues to support manufacturers to enable the development and production of high-quality and reliable medical devices that meet the demanding requirements of the healthcare industry, thereby improving patient outcomes and enhancing lives.