To Issue 142
Citation: Yosef A, “Enabling Drug Development Through Drug Delivery Manufacturing“. ONdrugDelivery, Issue 142 (Feb 2023), pp 47–50.
Andrei Yosef looks at the role of manufacturing in the development of drug delivery devices and highlights the benefits of Eitan Medical’s Sorrel device, which enables pharma companies to experiment during clinical trials to ensure that drugs produced are safe and cost-effective.
“Pharmaceutical companies are increasingly turning to wearable drug delivery devices as the preferred method for bringing new medications to market.”
The past few years have seen growing recognition of the need for patient-centric drug delivery devices that support effective administration of new biologic medications with large molecules. This has inspired significant investment in this area by global pharma players.
The covid-19 pandemic has also highlighted the urgency of moving the point of care from the hospital to the home. Particularly in the case of biologic-based treatments, the preference has clearly become self-administration from home.
As a result, pharmaceutical companies are increasingly turning to wearable drug delivery devices as the preferred method for bringing new medications to market. This has placed the burden of responsibility on device manufacturers to respond with robust and reliable devices that are also easy-to-use and able to support digital connectivity.
Eitan Medical has been at the forefront of these changes. The Sorrel™ drug delivery platform is a solution for pharma partners that facilitates the transition to safe and reliable self-administration at home.
The key to developing the optimal solution has been to understand and address pharma partners’ needs, which often centre around flexibility – both of the device itself and the manufacturing capabilities of the device developer.
EMBRACING FLEXIBILITY
With the advancement of pharmaceutical technologies and investments in research and development, pharmaceutical companies are developing more complex large-molecule biological drugs, increasing the molecular weight and the volume of medication to be infused.
Drugs currently under development require subcutaneous delivery at higher volumes – 10–25 mL and even higher. Due to the physical properties of biologics, including their higher viscosity, these medications cannot be concentrated into a smaller dose to fit the capacity limitations of delivery devices currently on the market.
Combination drug delivery devices, including prefilled syringes (PFSs), autoinjectors and pen injectors, are generally favoured by pharmaceutical companies due to their flexibility, ease-of-use and reduced risk of patient error and injury. However, most of the devices currently available on the market are designed for small-volume drugs and can only deliver between 1 and 2 mL at a time – far below the required volume for newer large molecule biological drugs.
Eitan Medical’s Sorrel platform solution (Figure 1) is compatible with both vials and cartridges in a wide variety of volumes, ranging from 3 mL up to 50 mL. This allows pharmaceutical companies to develop drugs for self-administration in higher volumes. The flexibility in volume size that the Sorrel device offers is crucial for allowing pharma companies to experiment with drug volume, molecule size and viscosity during clinical trials, ensuring the drugs produced are as safe, clinically sound and cost-effective as possible.
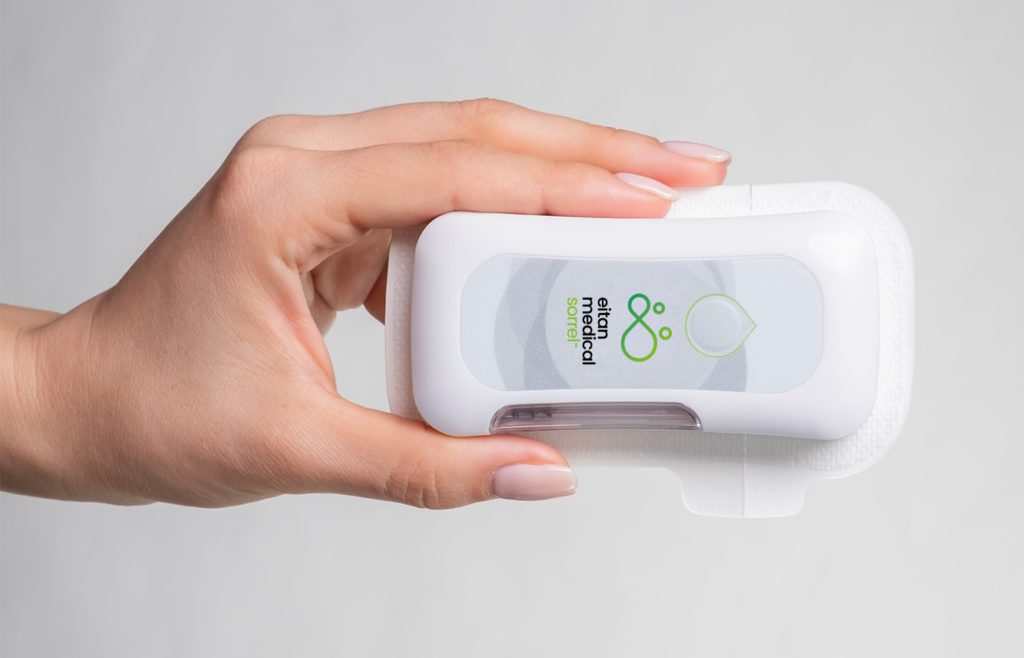
Figure 1: Eitan Medical’s Sorrel wearable drug delivery platform.
“The flexibility provided by the Sorrel device, coupled with its compatibility with any primary container, makes Eitan Medical an attractive partner for pharmaceutical companies.”
The flexibility provided by the Sorrel device, coupled with its compatibility with any primary container, makes Eitan Medical an attractive partner for pharmaceutical companies. While cartridges and PFSs are predominantly used for smaller-volume infusions (up to 2 mL), drug developers tend to prefer using vials as the primary container when it comes to larger volumes.
The ability of the Sorrel device to easily change between vials and cartridges has become a key asset for pharmaceutical companies, allowing them to directly integrate the device into their packaging line and reduce disruptions during the development and production processes. The devices currently on the market require pharma companies to change the primary packaging; when using Sorrel, no change is needed, saving time and money and reducing risk for pharma companies.
HEADING HOME
The recent experience of the covid-19 pandemic has resulted in a paradigm shift in terms of the way we think about care delivery, putting patient experiences and expectations at the forefront. At the height of the pandemic, the fear of contracting the virus led many to avoid hospitals and medical centres altogether. At the same time, hospitals became overloaded while caring for critically ill patients. This made home-based care a strong preference and, in many cases, a necessity.
“Connected devices ensure the safe and secure administration of medication, proofing of errors and troubleshooting of problems.”
Pharmaceutical industry recognition of at-home care trends and the recent awareness and acceptance from other parts of the healthcare ecosystem should add up to a compelling case for on-body wearable injectors. However, pharma companies still face barriers when bringing home-based solutions to market. To develop drugs that can be delivered at home, pharmaceutical companies need devices that offer high quality, ease of use and leverage connectivity. Medical device manufacturers need to recognise these needs and help support drug development by pharmaceutical companies.
Sorrel is an intuitive, independently operated device that reduces the need for patients to regularly visit infusion clinics, enabling them to minimise disruption to their lives while still receiving the treatments they need. Patients can simply attach a band-aid-like wearable drug delivery device to their body, turn it on and go about their day while receiving their treatment. Sorrel is single-use and fully disposable, creating an easy end-to-end experience for the patient.
REDUCING RISK
Medical device companies are also embracing connectivity opportunities in the Medical Internet of Things (MIoT) industry. Connected devices ensure the safe and secure administration of medication, proofing of errors and troubleshooting of problems. When patients are away from the direct care of a physician or nurse, connectivity expands this presence and ensures continuing quality of care.
Additional benefits of Sorrel are its prefilled and preloaded cartridge and vial configuration options. The Sorrel device is purposefully designed so that pharma companies can supply a fully prepared device requiring minimal steps by the patient to initiate administration. This minimises risk of patient errors and ensures high quality care throughout usage of the device.
However, as with any patient-facing device, scalability to meet demand is crucial for success. As the popularity of new drugs grows and they eventually become available on the market, pharma companies will require a device partner that can match demand with supply. Setting up in-house manufacturing capabilities is the best way to achieve this.
SCALING UP
When planning a manufacturing facility, high quality and high capacity cannot be an afterthought. These factors must be prioritised and initialised on day one of the development and planning.
The focus on high quality and high capacity must also be an essential part of the final design of the device. Drug delivery device manufacturers need to have the end-user in mind at every stage of development to ensure that the device offers the highest quality treatment to patients and the greatest value to pharma.
Automation should be a precursive requirement to the device manufacturing infrastructure. Even if device manufacture is not initially automated, it is a vital factor in achieving scalability and ensuring that, as demand for a drug grows, the production of the administering device can match it. The thoughts and requirements on how to scale up manufacturing and fully test the disposable device should start from day one and be a part of the device requirements.
Eitan Medical has incorporated these concepts into its thinking when designing the manufacturing facilities at its headquarters (Figure 2). Sorrel is a simply designed, yet highly sophisticated device that does not compromise on quality. With in-house manufacturing capabilities, Eitan Medical maintains complete oversight of its independent manufacturing lines and cleanrooms. The recent addition of semi-automated lines is configured to scale as Eitan Medical expands globally and receives increased demand from its pharma partners.
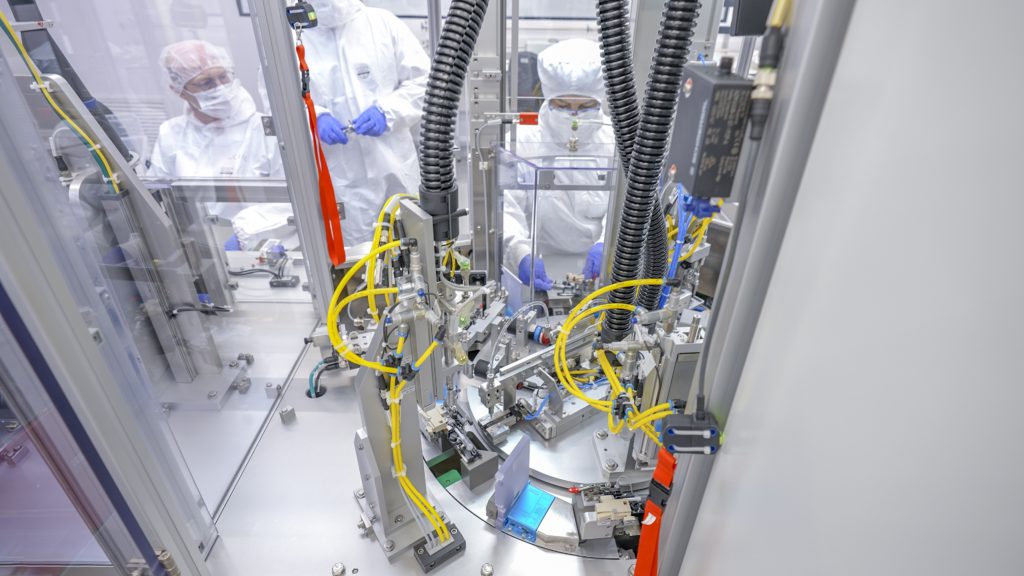
Figure 2: Eitan Medical’s on-site manufacturing facilities.
The company has ensured that its research and development, engineering and mass production teams have all been key participants in the discussion and development process from initial conception through to final production. The teams provide essential inputs, requirements and design features, and are all looking to the future of full automation.
Having all teams close to the manufacturing facility allows for rapid implementation of new features and innovations directly into manufacturing lines with minimal delays. This grants more control over the processes, facilitating quality assurance – a critical issue for pharma companies.
SHAPING MANUFACTURING TO MEET PHARMA DEMAND
Developing in-house manufacturing capabilities has also allowed Eitan Medical to dedicate manufacturing lines for specific pharma partners, allowing for flexibility to cater to each pharma partner’s needs. If requested, Eitan Medical can integrate customised tools and fixtures into production to suit the needs of specific drug manufacturers or end-users. Having multiple cleanrooms has also enabled the fulfilment of multiple customer orders simultaneously, ensuring that the company can collaborate with several pharma companies at any one time.
Uniquely, each single-use device is fully tested for function without affecting the device performance with the end user. Testing for reliability without affecting the product required unique tooling and processes, which was deemed critical to ensure quality and reliability.
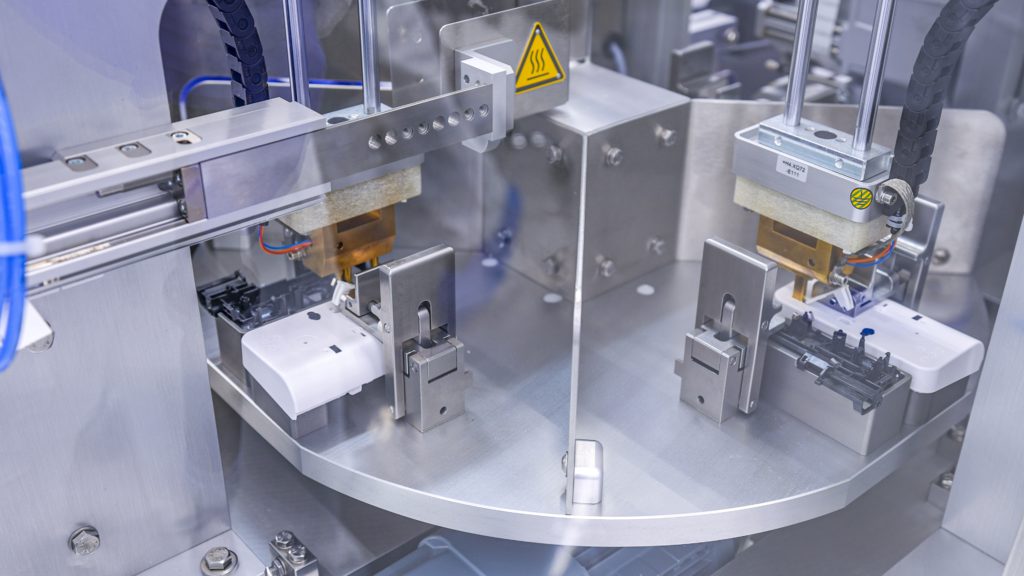
Figure 3: Eitan Medical’s separate testing stations.
The assembly lines in the manufacturing facility contain separate testing stations (Figure 3), which are fully automated and operate seamlessly. These testing stations provide clear data on device performance, including key performance indicators and certified key performance indicators, which would not otherwise be obtainable for testing a single-use device.
Finally, by integrating semi- and fully automated functions (Figure 4) into the manufacturing lines, Eitan Medical has been able to limit the risks of human error during production – an especially important issue for medical devices that must perform for every patient and for every treatment.
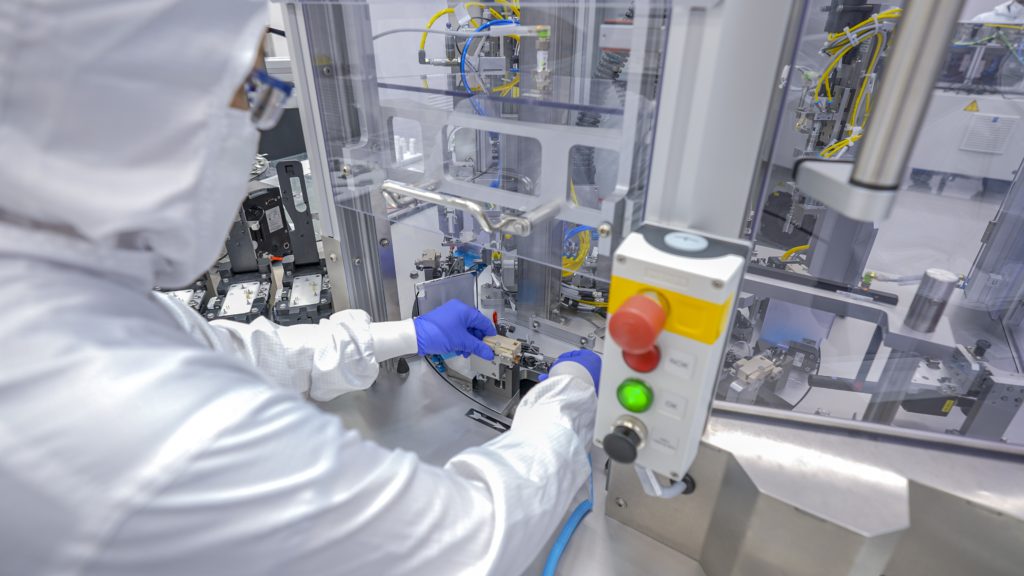
Figure 4: Eitan Medical’s semi-automatic manufacturing lines.
Demand is growing from pharmaceutical companies for a solution that is patient centric, innovative and suited to the latest drug development trends. As this demand grows, the ability to scale up production and tailor Sorrel to pharma partners’ needs will become increasingly valuable and ensure that Eitan Medical can act as a trusted partner with the highest quality devices and development services.