To Issue 156
Citation: Schmidt P, “Fast, Standard-Compliant and Cost-Efficient Testing of Prefilled Syringes for Optimal Results”. ONdrugDelivery, Issue 156 (Jan 2024), pp 108–110.
Peter Schmidt presents ZwickRoell’s solutions for testing autoinjectors and wearables to ensure a systematic increase in productivity in the testing lab.
In 2022, approximately 50% of new drug approvals involved biologics – a trend that continues to rise. At the same time, the focus is shifting from filling aseptic vials to the use of prefilled syringes (PFSs). Among other things, these act as medication vessels in the form of autoinjectors or on-body delivery systems (OBDSs). ZwickRoell has developed modular testing systems to perform all the necessary tests for PFSs in accordance with ISO 11040-4/6/8, with the utmost efficiency and standard compliance.
“For PFSs and autoinjectors, ZwickRoell offers modular solutions that support standard-compliant, flexible, and time- and cost-efficient testing.”
PFS SOLUTIONS
New therapies based on biologics have already begun to change cancer treatments significantly, giving hope to many people who previously lacked effective treatment options. Currently, however, the only means of effective and accurate dosing of biologics is with PFSs, in contrast to tablets, capsules, suppositories, syrups or solutions.
For PFSs and autoinjectors, ZwickRoell offers modular solutions that support standard-compliant, flexible, and time- and cost-efficient testing. A wide variety of tests can be used for different applications with the same machine components because the PFS tools can be easily changed. Autoinjector testing machines enable operators to insert prefilled syringes easily into the fixture through special inserts and subsequently conduct the test.
ISO 11040: STANDARD-COMPLIANT TESTING FOR SECTIONS 4, 6 AND 8
ZwickRoell’s modular solution for PFSs covers the ISO 11040 standard requirements, especially for sections 4, 6 and 8. These describe important tests, including needle penetration force, flange breakage resistance, needle pull-out force, glide force and closure system liquid leakage. Due to the modular set-up, all tests can be performed on a single machine, increasing both time and cost efficiency.
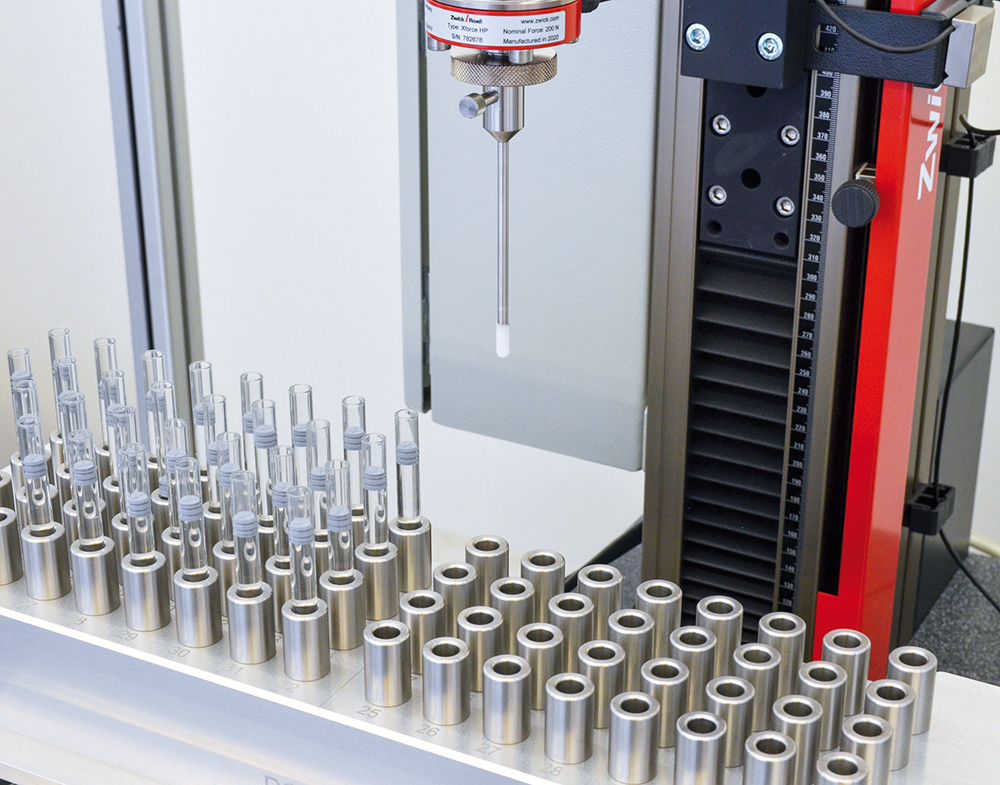
Figure 1: Sequential testing systems save time and significantly reduce operator influence.
Set-up Suggestions
ZwickRoell is the only manufacturer to offer three systems for testing autoinjectors and wearables to ensure a systematic increase in productivity in the testing lab, particularly with regard to the error-free functionality of injection systems and compliance with strict quality standards – the single-column zwickiLine 2.5 kN (Figure 1), the multifunctional AllroundLine 5 kN and the zwickiLine system for OBDSs.
Additionally, the company’s specialised customisation department addresses individual customer requests and devises application-based, tailor-made solutions, or presents suggestions for test equipment set-up options.
ZwickRoell believes that efficiency is an important topic for the pharmaceutical industry and its suppliers, such as manufacturers of syringes and autoinjectors, as well as service providers, such as contract development and manufacturing organisations and external testing service providers. Accurate and reliable solutions with significantly reduced user influence are essential and must be traceable in accordance with the US FDA 21 CFR Part 11 requirements.
ZWICKILINE: IMPLEMENTATION IN CLASS 5 AND CLASS 6 CLEANROOM TEST ENVIRONMENTS
In the pharmaceutical, medical and biotech sectors, cleanrooms are subject to strict regulations to eliminate the risk of contamination from germs and other harmful substances. ZwickRoell offers testing systems with ISO class 5 and 6 certifications; cleanroom compliance has been confirmed for zwickiLine materials testing machines, which can be used for production and testing in class 5 and 6 cleanrooms, according to DIN EN ISO 14644 1:2016-06, DIN EN ISO 14644-14 and VDI 2083 page 9.1. The test can be conducted without the need for time-consuming removal of specimens from the cleanroom. Additionally, the testing machine can be directly integrated into the production process within the cleanroom (Figure 2).
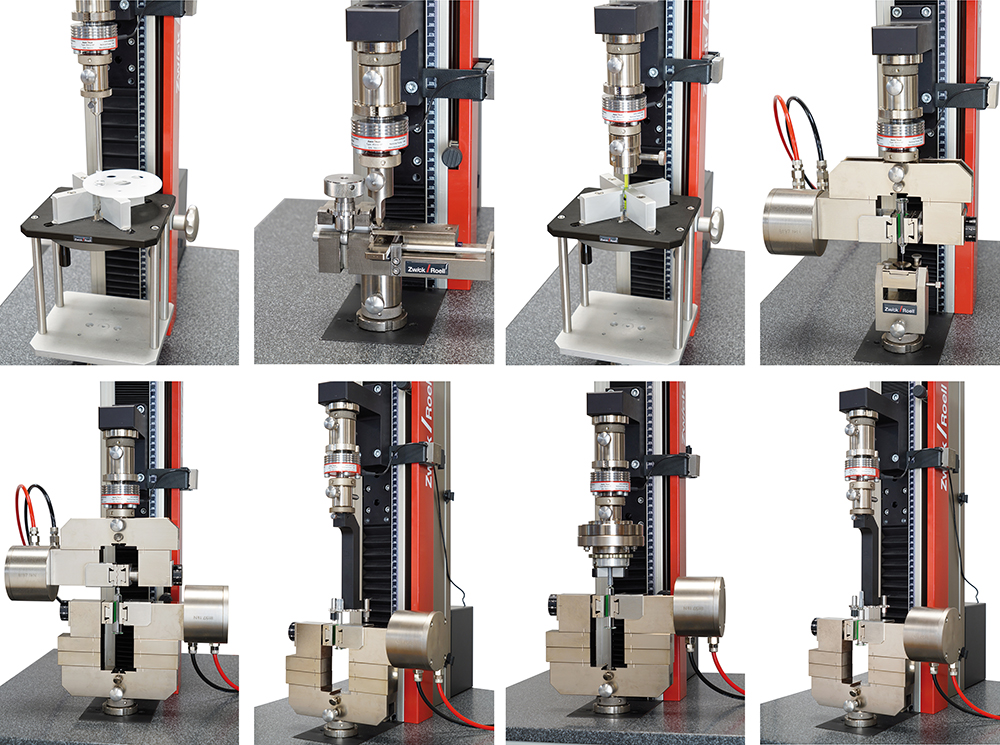
Figure 2: Simple, standard-compliant testing is guaranteed – test tools are easily interchangeable and standard requirements are preconfigured in the software.
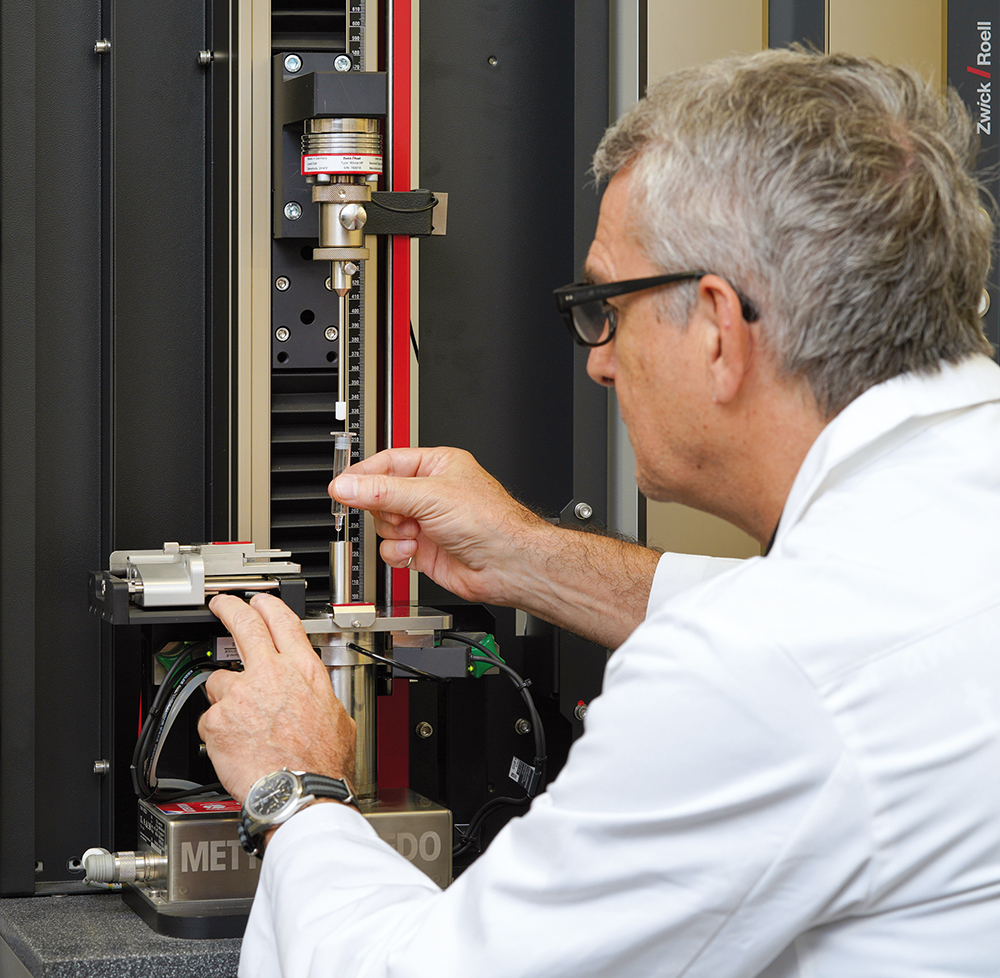
Figure 3: PFSs are tested using a simple syringe insert on the zwickiLine autoinjector testing machine.
SERIAL, PARALLEL AND AUTOMATED TESTING SOLUTIONS
Comprehensive validation is required for FDA and European Commission approval of new syringes and combination products. Sequential, serial and parallel testing systems can be adapted to customer-specific requirements. This ensures that specimens are fed to the machine in a uniform manner, enabling reproducible test results (Figure 3). The standard deviation is reduced by the testing systems delivering reliable results and minimising possible result distorting operator influences. This improves both the measurement accuracy and reproducibility of the test results, which ultimately helps customers to run cost-efficient tests.
SUPPORT FROM USER REQUIREMENT SPECIFICATIONS TO FINAL QUALIFICATION
ZwickRoell offers comprehensive support with all aspects of PFS testing. This ranges from the preparation of user requirements and customer-specific specifications to design qualification, project implementation, and the final installation qualification and operational qualification processes. The company also offers a unique qualification service that covers static testing systems with or without torsion drive, complex systems (such as autoinjector testing systems) and serial and parallel testing systems (carousel, XY table), as well as fully automated systems with robots. Customers can choose between standardised qualification documents or individualised documents tailored to their specific user requirement specifications.
Previous article
NAVIGATING ISO 11608 WITH AUTOMATED EQUIPMENT FOR CUSTOMISED PEN AND AUTOINJECTOR TESTINGNext article
DRUG DELIVERY TRENDS FOR 2024