Citation: Köhler C, Tsavous U I, Vosshage G, “Fully Automated Assembly and Functional Testing for Pen Injectors and Autoinjectors”. ONdrugDelivery, Issue 125 (Oct 2021), pp 82–86.
Carsten Köhler, Umit Ismail Tsavous and Gerd Vosshage explain the company’s processes for the automated assembly and testing of pen and autoinjectors.
For more than a decade, teamtechnik has specialised in assembling and testing medtech injection systems. The company has gained know-how and experience from numerous customer projects that have enabled it to create, for example, measuring systems for pen and autoinjectors of unparalleled precision.
CUSTOMER REQUIREMENTS
Patient safety, product quality and the integrity of the production data are the highest priorities for pharmaceutical companies. During the manufacturing phase, it is important to employ trusted processes and production methods that comply with GMP principles.
The long service life of production systems demands regular optimisation and extensions. Accordingly, pharmaceutical companies place high value on modular machine designs and processes that allow for maximum flexibility. Standardised mechanical, electrical, software and subsystem interfaces enable a diverse combination of system components and also allow changes and qualifications to be performed independently of the overall system.
“Thus, teamtechnik analyses customer requirements accurately and develops customised system concepts, including qualification, following GMP requirements.”
Selecting the right vendor is another important factor for success. A good production system supplier engages closely with the requirements of its customers. Thus, teamtechnik analyses customer requirements accurately and develops customised system concepts, including qualification, following GMP requirements. Whether using standard components or high-end solutions, teamtecknik’s solutions are always tailored to the individual application.
INJECTORS
Pen injectors and autoinjectors are playing an increasingly important role in the pharmaceutical products market. Patients place great trust in the dosing accuracy and safety of these drug delivery devices. In particular, their ease of use is appreciated, even by patients with reduced physical strength or deteriorating manual dexterity.
Autoinjectors consist of a power pack and a holder for the prefilled syringe. The injection procedure is started manually by triggering the autoinjector on the body; a pre-tensioned spring force in the autoinjector ensures that the medicament is injected automatically.
Pen injectors normally consist of two assemblies: the dosing mechanism and a cartridge holder containing a carpule. The dosage quantity is adjusted by means of a rotary button at the end of the pen injector. The rotary button impels a dosage adjustment sleeve (graduated tube) inside the injector. A display window on this shows the set dosage quantity. When unscrewed, the rotary button moves around the dosage path and out from the pen. By manually turning the rotary button back, the medicament is injected and the dosage sleeve is reset to zero. Pen injectors can be used for multiple dosages until the carpule is empty.
To ensure that pen injectors can be used reliably in practical situations, they must undergo function checks during the production stage in which the torques, compressive forces and frictional resistance during triggering are accurately measured. For this purpose, teamtechnik develops and implements precision production systems with integrated measuring systems designed specifically for the customer’s products and measurement requirements – from solutions with configurable measurement technology through to high-end test systems for the most demanding requirements.
FUNCTION TESTS
The TEAMED platform from teamtechnik consists of standardised function modules that can be used to create custom assembly lines. teamtechnik developed the production system platform and has been using it successfully for many years. The platform is compatible with ISO 7 cleanroom requirements. The company has developed the know-how for automating demanding medtech processes in recent decades from its experiences project planning many assembly and test lines for medical products and for other markets. For example, teamtechnik is developing production systems for injection systems, contact lenses, inhalers and point-of-care products, as well as for individual assemblies for medical products.
Thanks to the tried-and-tested standard components used, the TEAMED platform enables short delivery times and highly reliable production processes to be achieved. Test benches for the testing of complete pen injectors, autoinjectors and dosing mechanisms are available both inline and offline. If the component being tested can be reset, the test bench can be installed inline for 100% testing. If the testing is destructive, finished systems are tested for fault-free functioning on the basis of random samples at the goods inward or outward stage.
The fully automated test process of the TEAMED injector test covers parameters including the quantity of medicament delivered, force and travel measurement of the piston movement, and the triggering moment of the adjusted dosing stroke. Additionally, the needle length, the condition of the injection needle, the force for removing the pen cap and the readout from a dial can be monitored and/or measured. Depending on the inspection scope, a testing cycle can last between 5 and 30 seconds.
One unique selling point of teamtechnik is the measurement technology, which is not offered by any competitor in this form. The measuring element is an analogue sensor whose output is read by special software. The software filters out the noise elements and then performs a high-precision oscillation analysis. This arrangement offers a resolution accuracy that no other large-scale measuring system on the market has yet achieved. In practice, this results in false reject rates of less than 0.1%. Even the combined false reject rate for both assembly and testing is less than 0.5%, which is far below the standard requirement of not more than 2.5%.
While competitors’ systems can also achieve these levels, thus far they have only done so under specific environmental conditions and with small unit volumes. teamtechnik achieves this precision even with fully automated large-scale production with high unit volumes. A further customer benefit is that the measurement technology is individually developed for the specifications and requirements of the project. Thus, teamtechnik supplies its customers with sensors and software that achieve exactly the required precision from simple, configurable measurement systems to high-end test systems for the highest demands.
All production data, along with the functional testing data, are stored in teamsoft, the comprehensive production control system from teamtechnik. From here they can be accessed at any time for more accurate analysis. The innovative test software teamsoft-TEST allows test cycles to be created in a web-based graphical environment and enables a test task to be divided into individual test modules that can then be reused and recombined for further new test tasks.
INLINE TEST STATION
One customer order for teamtechnik included an assembly line for dosing mechanisms followed by complete testing of the dosing mechanisms, inline within the assembly fully integrated (Figure 1).
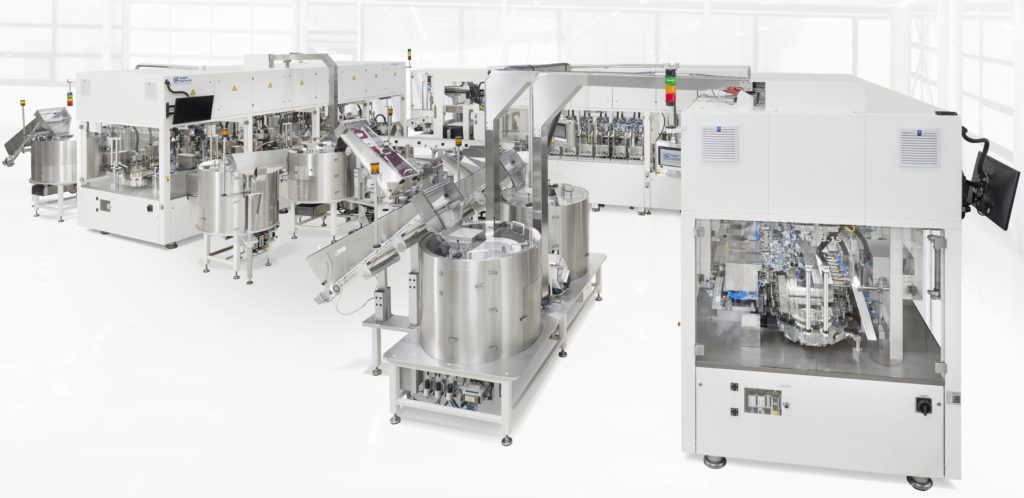
Figure 1: Integrated assembly and test line for a pen injector.
The solution created by teamtechnik offered an output of 25 dosing mechanisms per minute, producing three basic versions of the mechanism with sub-versions for different dosage quantities. The work steps are spread across 38 stations. All individual parts are fed in carefully as bulk material via teamtechnik feeder systems. Complex parts are monitored using camera systems and rotated to the correct rotation angle before being inserted into the assembly position, such as the graduated tubes for the rotational mechanisms of the dosing drive.
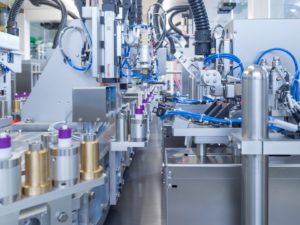
Figure 2: teamtechnik’s high-speed assembly solution for pen injectors.
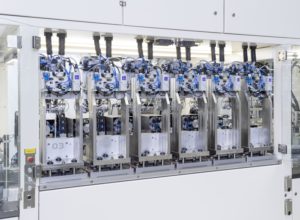
Figure 3: Process bench for six test modules.
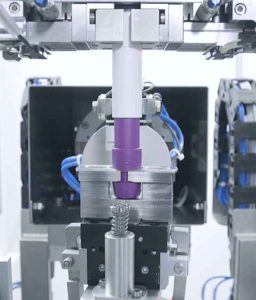
Figure 4: All function tests on the dosing mechanism are performed in one process position.
Figure 2 shows the high-speed assembly solution from teamtechnik for pen injectors.
The subsequent inline test is performed on a number of identical measuring stations in parallel. Each measuring station consists of a measuring module and a handling unit for loading and unloading the measuring module. The measuring modules are assembled on a separate base frame that is decoupled from the assembly line. The modules are mounted on vibration dampers as a further measure for preventing outside interference from affecting the sensitive measurement technology.
teamtechnik installs the measuring modules on a separate precommissioning bench. Only after test approval is received, based on certified calibration standards, are the individual test modules approved for installation in the test bench. This approach enables rapid commissioning of the production system. For example, the first test module can act as a development module that the customer can use to test pre-series pens or dosing mechanisms before the series assembly line is ready for operation. The development module can then later be integrated into the inline measuring station.
Figure 3 shows a process bench for six test modules.
The test spectrum for dosing mechanisms includes:
- Testing multiple pen types with different dosage settings
- Torque measurement function test when setting the dosage
- Pen injector disassembly function test
- Injection force measurement
- Presetting of dosing mechanism at final assembly.
All function tests are performed in one process position (Figure 4). This means that the test objects are clamped into the test bench just once and are then successively tested in this position. On the one hand, this does away with time-consuming additional handling procedures while, on the other hand, resulting in more accurate measurements, since the same reference zero point is used throughout.
During the dosage setup, the torque and the angle of rotation are measured, recorded and evaluated. The torque is measured using a torque sensor in the measuring module, while the angle of rotation is measured using a shaft encoder on the gripper unit. A unique feature is the dynamic torque and force test combined in a single process, which has proven more realistic and precise than static tests. This method enables a resolution of up to 0.001 nm in the torque test and a resolution of up to 0.01 N for the ejection force.
In the “pen disassembly” function test, the rotary button is pulled from the pen in a tensile test and the path and the necessary tractive force are measured. After this, the injection force is determined when the pen is pressed out. Here, the pen is pressed vertically from below at constant speed, while a constant counterforce from above simulates the pressure in the cartridge container. The teamtechnik measurement method enables the dosing stroke to be defined precisely to up to 0.04 mm and the ejection force precisely up to 0.3 N. Finally, the dosing spindle is pre-adjusted to a defined distance from the housing before the dosing mechanism is uniquely labelled and removed from the measurement device.
“teamtechnik has developed a stand-alone offline test bench designed to meet the measurement specifications of the customer, based on the TEAMED platform.”
OFFLINE TEST SYSTEM
If the test object is a non-resettable product (such as a ready-forsale autoinjector), offline testing is used. Here, small fractions of the production batch are randomly tested. This also calls for an extremely reliable measurement with minimum tolerances because any measurement errors will prevent approval of the batch and could cause significant economic damage. For this application, teamtechnik has developed a stand-alone offline test bench designed to meet the measurement specifications of the customer, based on the TEAMED platform (Figure 5).
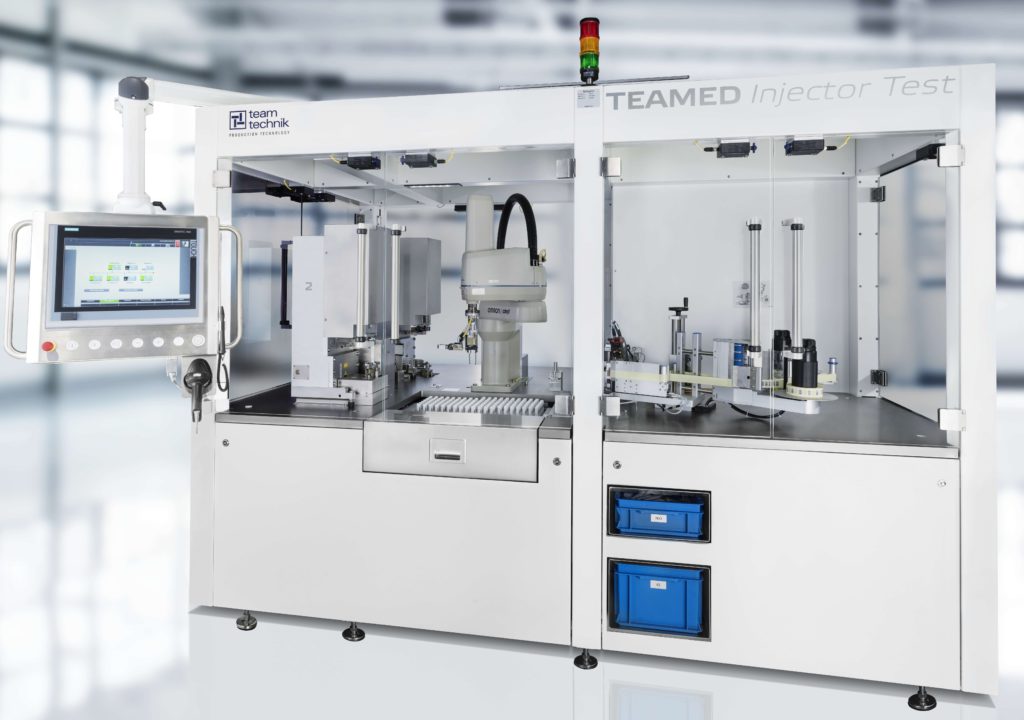
Figure 5: The offline TEAMED test bench is a testing system for batch approval and quality assurance.
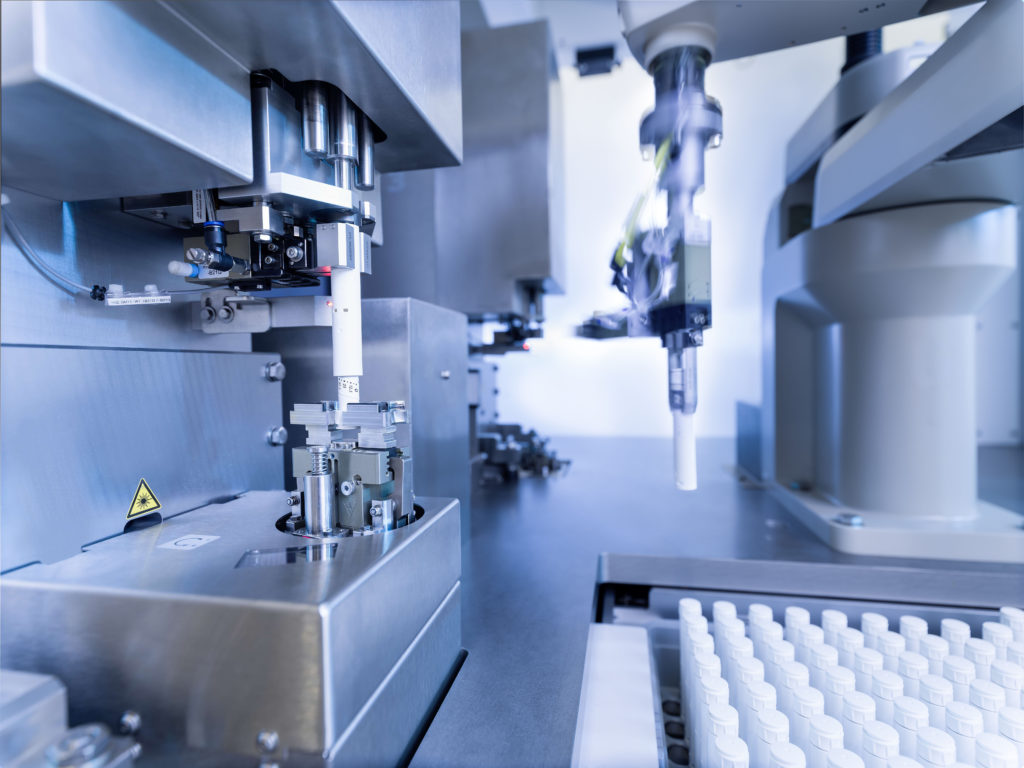
Figure 6: teamtechnik achieves dynamic torque and force testing in a single process.
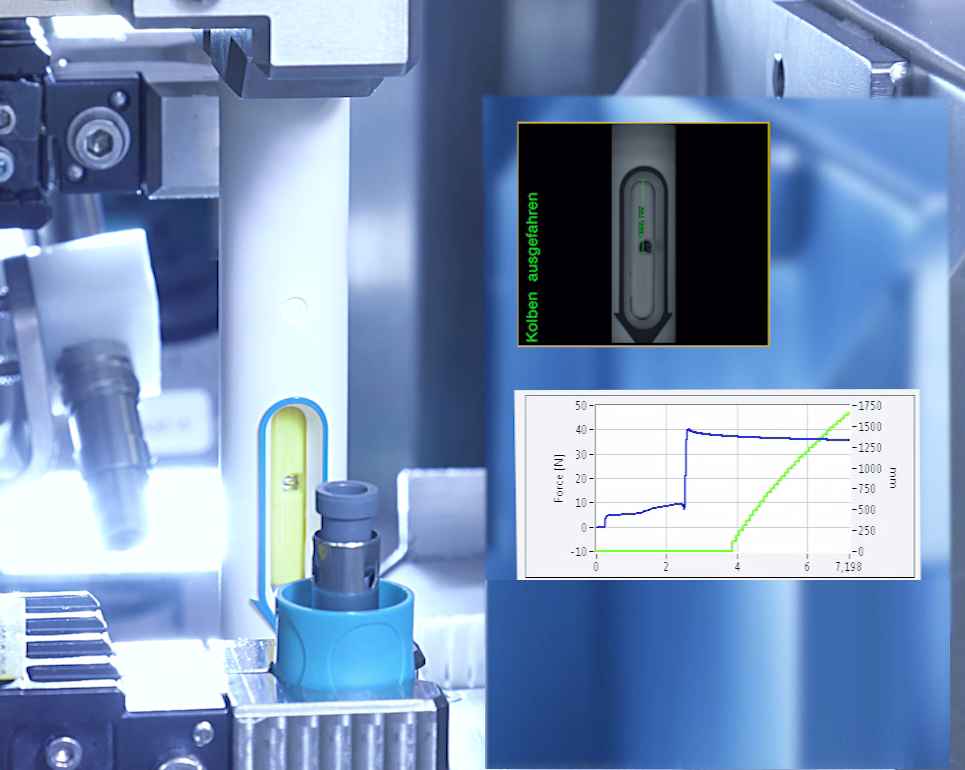
Figure 7: Triggering the set dosing stroke and piston monitoring.
As with the inline solution, all function tests are performed in a single process position and, in some cases, the same tests are run. These might include torque measurement when setting the dose, with dynamic torque and force testing in the same process (Figure 6), measurement of the injection quantity and the needle length, or camera-aided reading of the dosing scale.
To obtain the most accurate user handling simulation, multiple separate tests are performed on the offline test bench. The protective cap is removed fully automatically from the pen and the process is recorded in a force-displacement diagram. The dosing process is evaluated using a force-displacement diagram. Also, a camera takes multiple images per second during the injection process. The evaluation software can, for example, superimpose force-displacement curves on each other to visualise and better analyse the scatter of the measured values (Figure 7).
QUALIFICATION PROCEDURE
By using a multi-stage qualification process, teamtechnik ensures product quality, patient safety and data integrity. GMP summarises all the requirements and regulations that a machine and production system manufacturer must satisfy, such as VDI directives, machinery directives, ISO standards and the specific quality requirements of the product. In computer systems within the scope of GMP, the standards and guidelines of national and international organisations must be complied with. For the automated production of medical products in particular, the EU GAMP-5 guideline defines the foundations of all qualification tests.
The qualification process begins with the conception phase of the system and applies to the development, assembly, software, test systems and feeder technology equally. A GMP-compliant production system is given operational approval once the experts from teamtechnik have completed the qualification process without errors. The customer can then be confident that the teamtechnik assembly line satisfies all requirements for manufacturing pharmaceutical products.
SUMMARY
Quality, safety and cost efficiency are the driving forces in the growing market for medical products. System solutions from teamtechnik are a benchmark for the assembly and testing of medtech products. In particular, the high-precision measurement technology for fully automated injector function tests remains unmatched in the high-volume segment.
These measuring systems are fully aligned with customer requirements and deliver practically 100% dependable results. This does more than just secure product quality and customer satisfaction for complex medical injectors. teamtechnik TEAMED injector tests also protect manufacturers of medical products from the costly barring of product batches as a result of critical measurement values being taken inaccurately and thereby failing the batch.