To Issue 133
Citation: Deacon B, Vaes M, Burke P, “Glass-Filled Celanex® MT® PBT Hits Sweet Spot for Biologics and Reusable Devices”. ONdrugDelivery, Issue 133 (May 2022), pp 34–38.
Bryan Deacon, Marnik Vaes and Peter Burke, introduce a medical-grade glass-filled engineering polymer, Celanex® MT® PBT 2406MT GF20, which fills a gap in the materials market between standard engineering thermoplastics and expensive high-performance polymers.
Two major driving forces in modern injectable drug delivery include the rise of biologics and the increasing push towards industry-wide sustainability. Both these forces exert their own pressures and present their own challenges to drug delivery device design. A breadth of discussion has taken place within the drug delivery device design community on how best to approach these challenges but sometimes overlooked is the question of what engineering materials are available to make these approaches reality.
“A clear and present need exists for a middle ground between regular thermoplastics and high-performance polymers that is at present only met by expensive custom-made compounds.”
When it comes to biologics, the key factor is viscosity – a category of drug that has become more prevalent in the pharmaceutical pipeline. As such, delivery device designers have had to grapple with the challenges that high-viscosity drugs present to traditional autoinjectors. In many cases, this means dealing with greater injection forces so as not to necessitate a larger needle and therefore increased pain for the patient – forces that must be stored in the device, usually as a compressed spring, prior to its actuation.
On the other hand, the industry’s drive towards sustainability has invigorated interest in reusable devices. For designers developing reusable drug delivery devices, two key concerns are the longevity and reliability of the device – a reusable pen injector must deliver its last dose as accurately as its first, which requires the device be resistant to wear and creep over its lifetime, and therefore better materials will facilitate longer-lasting devices.
CELANEX® MT® PBT 2406MT GF20
Both sets of challenges expose a current gap in the materials market. New-generation delivery devices may place their components under substantially higher loads than their predecessors and, in such cases, standard engineering thermoplastics currently widely used across the drug delivery sector, such as polyoxymethylene (POM) and polybutylene terephthalate (PBT), may not be up to the task of reliably containing the stored forces required for biologic-containing autoinjectors or engineering reliable, long-lasting reusable devices. However, using available high-performance polymers would result in an overly expensive and likely over-engineered end product. A clear and present need exists for a middle ground between regular thermoplastics and high-performance polymers that is at present only met by expensive custom-made compounds.
Property | Unit | Test Method |
Celanex MT PBT 2406MT GF20 |
Density | kg/m3 | ISO 1183 | 1470 |
Melting temperature, 10°C/min | °C | ISO 11357-1/3 | 255 |
MVR, 265°C/2.16 kg | % | ISO 1133 | 17 |
Moulding shrinkage, parallel | % | ISO 294-4, 2577 | 0.3-0.5 |
Moulding shrinkage, normal | % | ISO 294-4, 2577 | 0.7-0.9 |
Water absorption, 23°C-sat | % | ISO 62 | 0.4 |
Humidity absorption, 23°C/50% RH | % | ISO 62 | 0.15 |
Tensile modulus | MPa | ISO 527-2/1A (Test speed 1 mm/min) |
7800 |
Tensile stress at break | MPa | ISO 527-2/1A (Test speed 5 mm/min) |
125 |
Tensile strain at break | % | ISO 527-2/1A (Test speed 5 mm/min) |
3 |
Charpy notched impact strength, 23°C | kJ/m2 | ISO 179/1eA | 10 |
Izod impact (notched), 23°C | kJ/m2 | ISO 180/1A | 10 |
Izod impact (unnotched), 23°C | kJ/m2 | ISO 180/1U | 47 |
Table 1: Material properties of Celanex MT PBT 2406MT GF20.
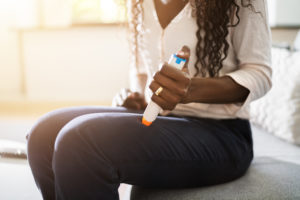
Figure 1: Glass-filled Celanex MT PBT provides a broad range of advantages to drug delivery device design, including the full support of Celanese’s MT polymers service package.
To meet this need, Celanese has developed Celanex® MT® PBT 2406MT GF20 (Table 1), a medical-grade glass-filled PBT with polyethylene terephthalate (PET). Celanex MT PBT 2406MT GF20 is a tribologically modified PBT+PET grade polymer that is reinforced with 20% glass fibre for additional strength and stiffness. The PET improves the outer shell, reducing the material’s coefficient of friction and providing an appealing high-quality finish. Furthermore, Celanex MT PBT is readily available to order in quantities suitable for large-scale production. As part of Celanese’s MT® line of polymers, glass-filled Celanex MT PBT is suitable for Class I, II and III medical devices and comes with the full support of Celanese’s technical expertise (Figure 1).
Glass-filled Celanex MT PBT fits in the sweet spot between standard engineering thermoplastics and high-performance polymers, achieving improved strength, stiffness, creep resistance and tensile modulus compared with unfilled POMs and PBTs and providing a more affordable, general-use option than specialist performance polymers. At present, glass-filled Celanex MT PBT is unique in this category within the medical-grade space, offering:
- Low friction with multiple materials
- Excellent creep resistance
- Retention of elongation suitable for snap-fit assembly
- High strength and stiffness
- Excellent suitability for gamma sterilisation
- High wear-resistance with no running-in required
- Low breakaway force
- Soundless sliding and elimination of stick-slip for improved patient comfort during delivery
- Good chemical resistance
- Smooth, appealing surface finish
- Full technical support from Celanese, including full 3D Moldflow® characterisation.
“The requirements for stored force are pushing the limits of standard POMs and PBTs. Glass-filled Celanex MT PBT, on the other hand, has been specifically designed with this consideration in mind.”
DESIGN FOR CREEP
Creep, or cold flow, refers to the tendency of materials to slowly deform when held under high stress for extended periods. As such, creep becomes a serious consideration when designing autoinjectors for biologics. In order to deliver these viscous formulations without increasing the size of the needle, these autoinjectors require greater force to push the drug through the needle than is typically required. As such, greater force needs to be stored within the device prior to actuation, usually in the form of a compressed spring. This means that the device components are going to be under greater stress and therefore more susceptible to creep and the loss of some of that stored force, which can compromise device reliability and potentially patient safety.
In practice, the requirements for stored force are pushing the limits of standard POMs and PBTs. Glass-filled Celanex MT PBT, on the other hand, has been specifically designed with this consideration in mind, and as such is a significantly stronger material that is much better able to resist creep when exposed to the stored force required to deliver biologics (Figure 2). Because of this resistance to creep, glass-filled Celanex MT PBT enables designers to confidently include high stored forces in their designs and minimise any force requirement on the device’s user, and therefore design devices that are easier to use and more patient friendly – a key consideration when taking ageing populations into account.
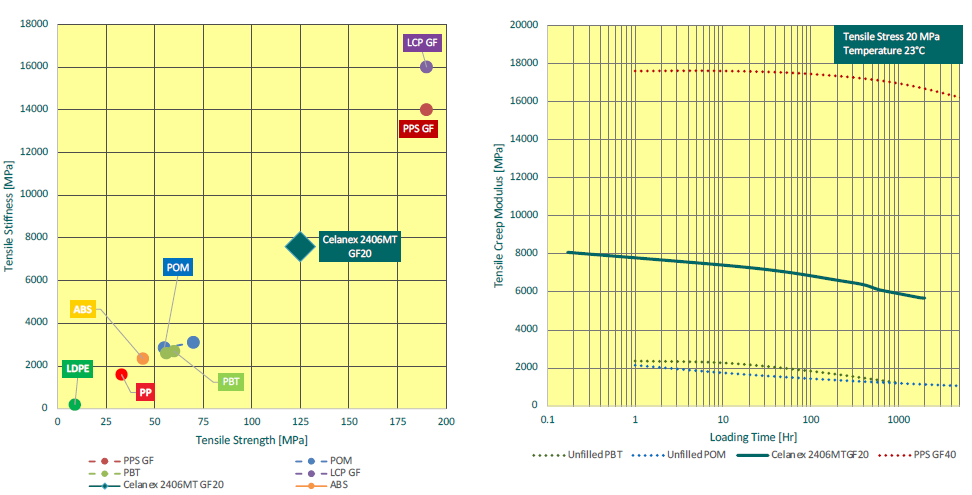
Figure 2: Glass-filled Celanex MT PBT provides a significant increase in tensile creep performance compared with commonly used engineering thermoplastics, bridging the gap between those and high-performance materials.
FRICTION CHARACTERISTICS
When designing any mechanical device with moving parts, friction is going to be a major factor.1 In injection devices, the primary source of friction will be the slide of the plunger during delivery – a function that should be as smooth as possible to ensure that injection speed is consistent across devices and to minimise pain for the patient.
“Another advantage of glass-filled Celanex MT PBT is that it is backed by Celanese’s wealth of technical expertise, which the company makes readily available to partners to assist them in getting the most out of their materials.”
Glass-filled Celanex MT PBT is tribologically modified to guarantee smooth low-friction sliding. This key material property results in a number of benefits, including reliability, wear resistance and noise reduction. For single-use disposable autoinjectors, consistency in first-time actuation across devices is highly desirable; a material that needs to be run-in to achieve consistent actuation is inherently less suitable, as its first-time use will be less predictable. Glass-filled Celanex MT PBT is designed so that no run-in is required – the first actuation is as smooth as any other, making it an ideal material for ensuring consistency across single-use devices.
Of course, this property is even more valuable for reusable devices. Whether a reusable injector is refillable or designed with a replaceable cartridge, device reliability is critical – a worn-out device could potentially pose a risk to patient safety. The low friction of glass-filled Celanex MT PBT is a twofold advantage for reusable devices, providing the aforementioned lack of run-in and consistent smoothness from the first actuation to the 1,000th, as well as leading to decreased wear and degradation of the device as it is used, resulting in increased reliability and longevity. Furthermore, the low friction of glass-filled Celanex MT PBT eliminates the slip-stick phenomenon, meaning that actuation and sliding is silent, improving the experience of using the device.
Only One Component Required to Reduce Friction
Investigation by Celanese has demonstrated that glass-filled Celanex MT PBT has as consistently low coefficient of friction in interactions with other materials, often significantly lower than those other materials have with themselves (Figure 3). This means that the benefits of glass-filled Celanex MT PBT can be achieved by using a single component rather than needing to make the whole device out of it. As such, glass-filled Celanex MT PBT is ideal as a tool in the design toolkit and doesn’t mandate a wholesale rethinking of materials and parts to incorporate.
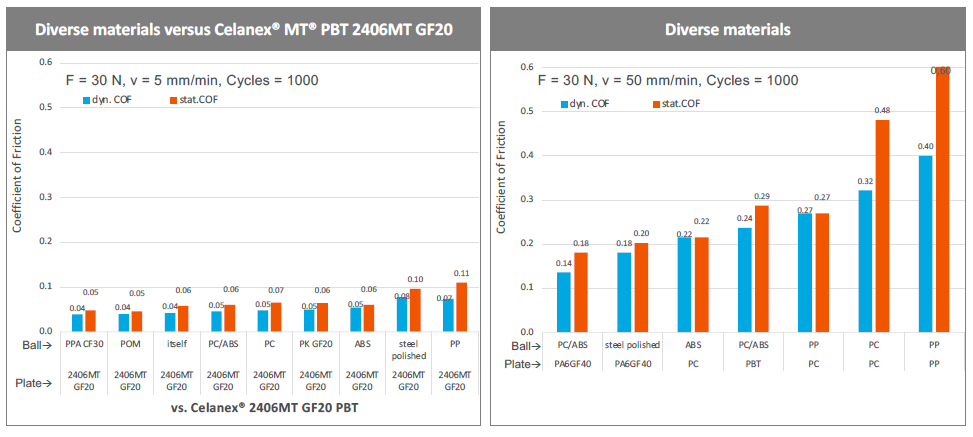
Figure 3: Glass-filled Celanex MT PBT has a reduced coefficient of friction for a diverse range of materials, meaning that only one component needs to be made of glass-filled Celanex MT PBT to achieve its low-friction advantages.
MANUFACTURING WITH GLASS-FILLED CELANEX MT
Glass-filled Celanex MT PBT is well suited to medical device manufacturing. The material is suitable for injection moulding and for various sterilisation methods, including gamma sterilisation. Another significant factor is that glass-filled Celanex MT PBT has an ideal retention of elongation for snap-fit design for convenient assembly.
It is important to note that working with glass-filled polymers is not equivalent to working with standard thermoplastics – you can’t simply switch one for the other with no change to processes. As such, another advantage of glass-filled Celanex MT PBT is that it is backed by Celanese’s wealth of technical expertise, which the company makes readily available to partners to assist them in getting the most out of their materials.
Sustainability Advantages
Glass-filled Celanex MT PBT can be used as part of a more sustainable approach to drug delivery device development and manufacturing. Due to the material’s higher strength and stiffness compared with standard thermoplastics, components can be designed to be thinner and more lightweight whilst maintaining structural integrity, meaning that less material is required overall. Furthermore, because only a single component in contact needs to be made of glass-filled Celanex MT PBT to take advantage of its low co-efficient of friction, it is ideal for use in combination with other low-carbon footprint materials, such as Celanese’s ECO-B polymers,2 as part of a broader move towards sustainable devices.
FULL MT SUPPORT
Celanese offers global support to partners working with the company’s MT-grade products. The company has extensive data available for Celanex MT PBT 2406MT GF20, including full 3D Moldflow characterisation, creep tests, friction tests up to 1,000 cycles and sterilisation tests. Celanese offers the expertise to enable partners to optimise their transition to glass-filled Celanex MT PBT and take full advantage of the benefits it can provide.
Celanese’s MT-grade polymer services package includes consulting and support services, from initial concept, through part design, all the way past commercial launch of a device or combination product. The package details Celanese’s commitment to the medical device industry, with the highest levels of quality assurance, regulatory data and support, notification of change, supply security and manufacturing controls, including:
- Long-term supply assurance
- Change notification commitment
- Certified biocompatibility (USP Class VI / ISO 10993)
- Food contact compliance (US FDA and EU)
- Animal- and latex-free formulations
- FDA Drug & Device Master File listing
- Production aligned with GMP principles
- Additional analytical and individual batch testing
- Expanded certificate of inspection
- Support in regulatory approval process.
CONCLUSION
The current gap between standard thermoplastics and high-performance polymers naturally leads to devices using materials that result in them being either over- or under-engineered. Until now, designers seeking a material in this space have had to rely on expensive custom compounds. To meet the need for a mid-range material in the medical-grade space, Celanese has developed Celanex MT PBT 2406MT GF20, a tribologically modified PBT+PET polymer with 20% glass filling, providing an excellent balance of properties for use across the medical sector.
Glass-filled Celanex MT PBT offers excellent creep resistance, low friction against itself and a diverse range of other materials for superior lubricant-free slide characteristics and no running-in so that the first actuation is as smooth and quick as the 1,000th. The material is ideal for handling the stored forces required to deliver viscous biologic formulations, as well as offering the wear resistance and consistency desirable for long-lasting reusable devices, all while remaining suitable for snap-fit assembly and providing a smooth, high quality surface finish.
Celanese offers full global support to partners to help them take full advantage of their materials. The company has a wealth of data and expertise available, including full 3D Moldflow characterisation, so that partners can make optimal use of glass-filled Celanex MT PBT in their device designs. Glass-filled Celanex MT PBT currently occupies a unique position on the market, being the only medical-grade material to hit the sweet spot between standard thermoplastics and high-performance polymers readily available for large-scale production, making it a natural choice for designing devices that are more robust, reliable and patient friendly.
Celanex and MT are registered trademarks of Celanese. Moldflow is a registered trademark of Autodesk.
REFERENCES
- Markgraf K, Johnson W, “New Material Developments for Medical Devices: Polymers with Improved Tribology”. ONdrugDelivery, Issue 57 (Apr 2015), pp 40-42.
- Norfleet K, Haley R, “Hostaform® POM ECO-B – Proven, Versatile, Easy and Environmentally Sustainable”. ONdrugDelivery, Issue 117 (Mar 2021), pp 12–16.