Citation: Schou Christensen J, Berninger-Lund S, “How Digitisation is Delivering Competitive Advantage in Device Assembly”. ONdrugDelivery, Issue 123 (Aug 2021), pp 15–18.
Jens Schou Christensen and Sebastian Berninger-Lund present the business case for the wider implementation of digitisation and the greater use of data to deliver assembly line improvements.
“While much of the industry focus has been on the development and market launch of connected devices, there has also been a quieter digital revolution in manufacturing and assembly, where the increase in complexity of pharma partners’ requirements (including more personalised medicines, the ever-evolving regulatory landscape and cost) has caused production facilities to look again at the use of smart manufacturing technologies.”
It is suggested that by as early as 2040, smart home products will be adopted almost universally across Europe. So far, the pace of uptake in new technologies has been meteoric – in 1998 just 9% of UK households had internet access, whereas today the figure is more than 90%.1
This surge in demand for technology has transcended into the manufacture and assembly of drug delivery devices. Today, data and the digitisation of assembly equipment work hand in hand to deliver competitive advantage to pharma partners in terms of product quality, continuous improvement, de-risking maintenance and change management and, critically for the near future, the ability to deliver unique identities and traceability for every assembled device.
THE BUSINESS CASE FOR DIGITAL MANUFACTURING IS COMPELLING
Anyone working in drug delivery today will be very much aware of the advancements in connected devices and how the Internet of Things (IoT) is predicted to make a huge impact on patient adherence, as well as saving the whole healthcare industry billions of dollars as patients, healthcare professionals, payers and pharma partners take advantage of the data created to improve therapies and how they are delivered. While much of the industry focus has been on the development and market launch of connected devices, there has also been a quieter digital revolution in manufacturing and assembly, where the increase in complexity of pharma partners’ requirements (including more personalised medicines, the ever-evolving regulatory landscape and cost) has caused production facilities to look again at the use of smart manufacturing technologies.
A recent white paper from Bain & Company predicts some game-changing improvements following the implementation of digital manufacturing. Smart connected factories are estimated to produce savings of 20% or more, with a 14% increase in delivery reliability. There is also forecast to be a 17% reduction in costs related to poor quality and a saving of 15% in the cost of converting raw materials into drug products.2
For a few years now, some delivery device solutions providers have advocated the increased use of digitisation to deliver data-led enhancements, not just to monitor and improve product quality but also to drive overall equipment effectiveness (OEE), deliver predictive maintenance and use machine learning to continuously improve processes.
“Historically, actions such as root cause analysis would have taken many hours, a great deal of intellectual energy and costly iteration. Today, data, combined with expertise and experience, can effect big changes in performance in comparatively short timescales.”
USING DATA TO DELIVER QUALITY AND COST IMPROVEMENTS
The use of data to drive any kind of improvement is not a revolutionary idea, for example Six Sigma has been around since the mid-80s. However, in a recent survey conducted by Stevanato Group, 10% of respondents to an online study stated that no data was collected from their production operations, and an overwhelming 74% were only using data in a limited capacity to drive quality improvements, mainly in product quality, OEE and predictive maintenance. These respondents came from a range of functions within the pharma and life science industries.
Stevanato Group has been researching the positive impacts of a data-based quality checks, compared with visual or semi-automated checks. The company has noted the benefits both in terms of cost reduction and quality improvement. From a cost perspective, each machine is more productive due to fewer interventions during manufacture. While more or less the same number of validation systems are still required, manufacturing space has been optimised as fewer inspection stations are needed. Because the parameters for quality have been established, many problems can be addressed agilely in-line. In turn, the company is witnessing the need for a reduced overall manufacturing footprint and greater OEE.
In terms of product quality, the data enables the company to optimise product design, validate the process and recognise “hidden” anomalies to detect the root causes of any quality issues. This process creates an holistic cycle of continuous improvement, with data always circling back to improving product design and overall quality.
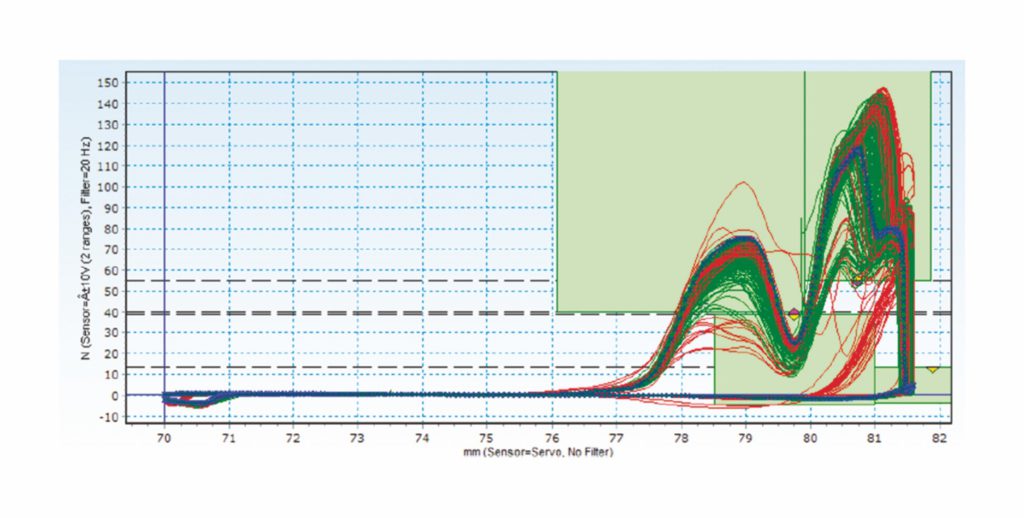
Figure 1: An example of data measuring an assembly process and driving improvements in performance – raw data (snap).
The data in Figure 1 demonstrates how the snap process of two annular rings can be analysed. The x axis indicates the position of the gripper, with the y axis showing the force implemented for placement. The measure is to establish if the anticipated forces needed for the snap of the two components matches what is, in reality, needed to engage correctly. The green lines mark items assembled correctly, with the blue line representing the average and the red lines showing incorrectly assembled components. The curves of the green lines can be seen to follow the correct path, entering the left-hand green box before descending into the lower box and then rising again into the upper green field on the right.
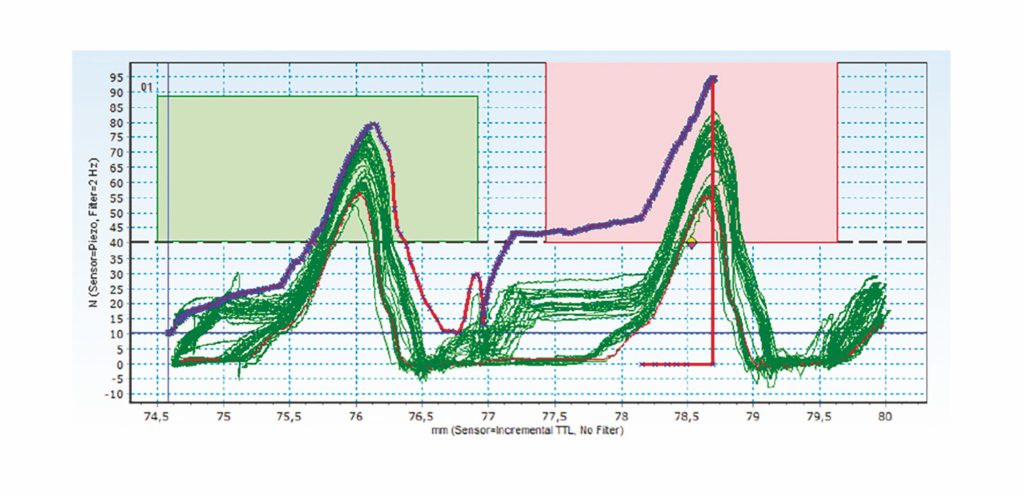
Figure 2: Showing how data-driven quality checks can reduce risk through effective and accurate measurement – example on raw data (click).
Figure 2 demonstrates a similar methodology, but in this case, instead of a linear movement, rotation is measured using torque. Without such a system, a rotation would be made to deliver an expected number of clicks, however, we can now actually measure that all the clicks were done and make the set point the number of clicks rather than the amount of rotation.
“Stevanato Group’s philosophy is simple – you cannot improve what you cannot measure, and you cannot measure what you cannot see.”
USING DATA TO DRIVE ASSEMBLY PERFORMANCE
There is no better analogy for the state of play in device assembly today than the iceberg. While due diligence is given to key performance indicators (KPIs), much of the performance under the surface is not enhanced or even captured, leaving much room for improvement.
Stevanato Group’s philosophy is simple – you cannot improve what you cannot measure, and you cannot measure what you cannot see. As such, the first step in driving assembly performance is to go beyond the KPIs – going below the water line to capture and store all the data possible. Stage two is about finding new ways to optimise performance – deep diving into why events occur, and where to look for the root causes of poor performance.
One example is the novel ability to use video capture to identify the cause of defects. At any time, a user can double click into specific event data to access a video file of the last ten seconds of the process, enabling them to see what went wrong and when (Figure 3).
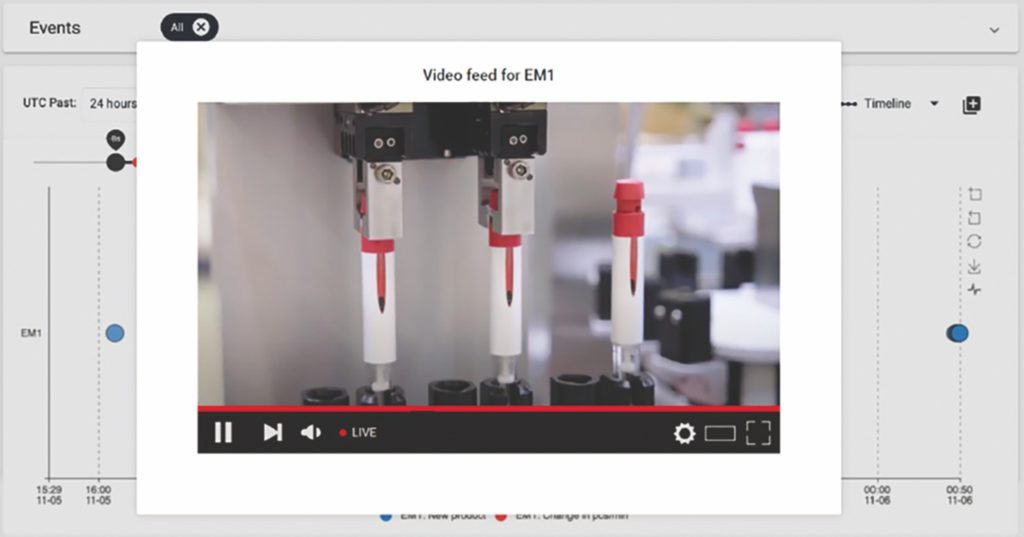
Figure 3: Live streaming of the process to establish cause of defects in quality.
Historically, actions such as root cause analysis would have taken many hours, a great deal of intellectual energy and costly iteration. Today, data, combined with expertise and experience, can effect big changes in performance in comparatively short timescales.
Stevanato Group has gone one step further and implemented machine learning – allowing its intelligent machines to find new ways to optimise processes, based on the data generated. The company also employs predictive maintenance tools, which use data to identify patterns in breakdowns and address them before they happen. One example is the installation of air pressure sensors – by monitoring the stability of air pressure and the reaction time of the sensors, patterns can be identified that may affect overall performance. This approach combines data with the experience and expertise of the company’s engineers and delivers several benefits – business interruption is mitigated, shut down/maintenance days are reduced and overall cost minimised.
“The advantage of digitisation is clear – extended data insight leads to more, and better, data. Using smart data enables design, development, validation and continuous improvement to happen in a comparatively low-touch yet high-impact way, without the associated business interruption costs of revalidating machines.”
WHY YOU NEED A DIGITAL TWIN
For decades, industry was used to working with 2D drawings, and then, in the 1960s, along came 3D – a transformational moment. Now, thanks to Digital Twin, we can work in 5D. Digital Twin is best described as “a digital replica of a living or non-living physical entity.” Integrating IoT, AI, machine learning and software analytics, Digital Twin is viewed as a game-changer in the simulation and emulation of mechanical and automated performance. Why a game-changer? Essentially, it is now possible to create, manipulate and iterate the whole assembly process digitally, and only when the perfect parameters for success are determined is an investment made in the physical model. The return on investment from such an approach is substantial – no more downtime, no more trial and error – right-first-time modelling.
In a recent customer study, Stevanato Group asked respondents about their experience level with Digital Twin. Just 4% are actively using an implemented Digital Twin in daily business, with a further 14% at early stages. A total of 72% of respondents currently have no experience of Digital Twin – something Stevanato Group is keen to address, given the game-changing metrics associated with it.
It is fair to say that the definition of Digital Twin is still open to interpretation, depending on personal and corporate perspectives. While Stevanato Group certainly sees it as a twin of physical entity, others see it as an umbrella for all kinds of engineering processes and tool improvements.
From a design perspective, it enables software and mechanical engineers to align and work in parallel without the ambiguity or misinterpretation often associated with written specifications. Software engineers can begin their processes much sooner and programming time can be reduced as a result of the early alignment with mechanical engineering functions. As a result, this design solution is much easier to implement and can be reviewed by the customer to ensure it replicates the physical machine experience as much as possible.
At the design review phase, the Digital Twin can aid the selection of the right assembly concept from day one. Using animated design instead of 3D design to interrogate better the configuration of the equipment (its location, interaction with other machines, etc) before it is manufactured, saving considerable time and cost over conventional methods of design review.
In terms of process, the Digital Twin can help engineers understand and analyse the process more deeply and make improvements more quickly. In addition, it is a very powerful communication tool to enable wider understanding across teams.
Digital Twin also brings benefits in many areas of production, particularly filling, where the imperative is to limit the amount of people on the floor to reduce particulates entering the facility. Even by accessing the Digital Twin remotely, customers can quickly identify and resolve any problems, often without having to visit the production facility themselves.
The Digital Twin delivers benefits in terms of training and development too. The operator can use the Twin like the real machine, replicating the human-machine interface in a virtual environment. This enables the operator to interact with the products inside and outside the machine, and provide feedback in the design phase that will enable more efficient productivity in the final machine.
SOLVING A TWIN CHALLENGE FOR A PHARMA PARTNER
Stevanato Group recently participated in the successful delivery of a Digital Twin project in partnership with an automation group to support a pharma partner’s pen injector assembly line. In this case, the client faced a twin issue – how to develop the assembly equipment at the same time as the product development was taking place. How to manage a design change on the product and, as a result, on the equipment was a key challenge. This twin issue was resolved using Digital Twin.
Right now, the project is installed and working, with the expectation that Digital Twin will deliver direct benefits in terms of reduced development time and cost, improving product quality and increasing OEE. There are anticipated softer benefits too in terms of providing a platform for training.
NOW IS THE TIME TO ACCELERATE YOUR JOURNEY TOWARDS INDUSTRY 4.0
It is no understatement to suggest that the healthcare industry is undergoing a transformative change. The pandemic has brought into sharp focus the need for more agile approaches to meet patient demand, at the same time highlighting the need for rapid scale-up in productivity while maintaining the integrity of the drug product.
Beyond covid-19, pharma partners are developing even more complex, specialised (and therefore expensive) molecules that require ever greater diligence in the quality of container. Personalised medicines create other challenges for assembly, where smaller batches with a greater level of serialisation will be needed. Lower volume batches do not sit comfortably with a pricing model predicated on high volume output, so the cost of production will become an even greater focus. All these considerations lead to the road towards the use of smart manufacturing technologies.
The advantage of digitisation is clear – extended data insight leads to more, and better, data. Using smart data enables design, development, validation and continuous improvement to happen in a comparatively low-touch yet high-impact way, without the associated business interruption costs of revalidating machines.
The net effect of this smart data is a highly optimised assembly function where process is improved, quality is enhanced, OEE is increased and unnecessary cost is mitigated.
According to Bain & Company, the biggest challenge in embracing this approach is integrating data, with 85% of pharma executive respondents citing effort as the biggest implementation issue.2 The market influences driving digitisation are growing daily, and while there is no question there is an investment in hours required, with the right partner, the long-term benefits far outweigh the short-term efforts.
REFERENCES
- “Digital economy and society statistics – households and individuals”. Eurostat, Sept 2020.
- Lesmeister F, Ghosh P, “Digital Manufacturing Is (Finally) Coming to Pharma”. Bain & Company, April 8, 2020.