To Issue 138
Citation: Tsavous U I, Köhler C, Nägele T, “Industrialisation of Customisable Product Platforms in Life Sciences”. ONdrugDelivery, Issue 138 (Oct 2022), pp 96–100.
Umit Ismail Tsavous, Carsten Köhler and Tom Nägele discuss customisation of product platforms in the life sciences field.
“The challenge for the machine builder is the flexibility to assemble and test all variants within the product platform.”
The desire to stand out from the crowd is not limited to the consumer market; in the life science industry, there is a strong need for individualised solutions. The drivers for this need are diverse, ranging from branding purposes to functional adaptation.
This desire for individualisation is in marked contrast to the needs of production facilities, both in terms of the level of investment required for production equipment and the organisation of production. To limit the impact of customisation on production, product developers create product platforms. In this concept, the function stays the same but the external appearance and size can change. The challenge for the machine builder is the flexibility to assemble and test all variants within the product platform.
In the past, production lines were adapted by means of shelves full of interchangeable parts. This resulted in loss of production time and the risk of machine failure during the changeover. To limit these effects, teamtechnik offers its customers a solution with automatic adaptation for different variants. This article outlines the concepts involved in the implementation of a flexible yet stable assembly system.
CUSTOMISABLE PRODUCT PLATFORMS
Sustainable energy consumption and efficient resource usage are more important than ever in today’s world. This is one of the reasons why product developers use customisable product platforms – to allow individualisation by focusing on the effective use of resources. Product platforms use as many common components as possible to design different product variants, which are then produced on the same assembly lines. In theory, there should be no limit to the number of possible variants of the product platforms that can be produced on a single assembly machine.
“Sustainable energy consumption and efficient resource usage
are more important than ever in today’s world.”
Systems from teamtechnik can be used to produce products based on platform design, such as autoinjectors, prefilled syringes (PFSs) and stopcocks. An autoinjector product platform, for example, supports several product variants, with each autoinjector consisting of ten or more components. The core function does not change between variants; only the external appearance and size are customised. The varying components are uniformly standardised in their basic concept and mainly differ in their colour and functional position. To generate product variants, the dimensions of the component variants are configured in relation to the individual PFS capacities. The PFS product range includes three basic diameters and several length variants, each consisting of a glass barrel and a needle. The glass barrel, needle diameter, needle tip and needle wall thickness form different variants of the PFS product platform.
Similarly to a PFS, the basic structure of a stopcock product platform consists of two basic components: body and handle. In total, more than 300 product variants can be implemented within one stopcock product platform. Each variant of the stopcock is based on a geometrically modified body. The connection points are almost identically designed for flexible handling in the assembly system. The body variants are essentially differentiated by their different connection ports. The bodies are equipped with an individual combination of connections, screw caps and O-rings, depending on the variant.
On teamtechnik machines, the production of product platforms is now a standard feature, with the required flexibility for today’s product variants as an integral part of these machine concepts.
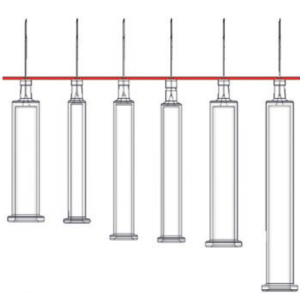
Figure 1: Zero level of PFSs.
MACHINE CONCEPTS
Developing a machine concept for customisable product platforms starts with an understanding of the assembly steps of the product. An essential aspect of this phase of concept development is the identification of the zero level. A machine type can be selected according to whether the product platform provides such a zero level (Figure 1). If a zero level exists, mechanically controlled machines can adapt easily to different product variants, however, without a zero level, the choice is limited to servo-driven stations, as too many positions are required.

Figure 2: TEAMED RTS.
For example, with teamtechnik’s platform TEAMED RTS (rotary transfer system) cam technology, a stopcock product platform is produced with over 300 variants (Figure 2). The synchronously controlled cams of the RTS are mounted on main shafts and driven by a single common servo motor. This synchronicity also contributes to low energy consumption during production. If further processes for the assembly and testing of a product are required, teamtechnik can use the TEAMED LTS (linear transfer systems) machine platform (Figure 3).
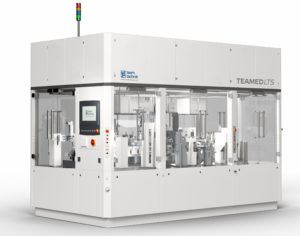
Figure 3: TEAMED LTS.
Depending on a customer’s requirements, the drive can be built with mechanical cams or servo electric motion. Cam-controlled processes can achieve maximum cycle rates, whereas electric drives offer greater process flexibility. If individual flexibility for the component is required, this will lead to an asynchronously controlled LTS, with complete process versatility based on servo motion or robotic stations.
However, the variants of a product platform that can be produced on a teamtechnik machine platform are not dependent on the drive system employed. For example, an autoinjector product platform could be produced on a cam-driven RTS while an infusion set product platform would be produced on an asynchronously controlled LTS. Both machine concepts can produce a multitude of product variants without interchangeable parts (Figure 4).
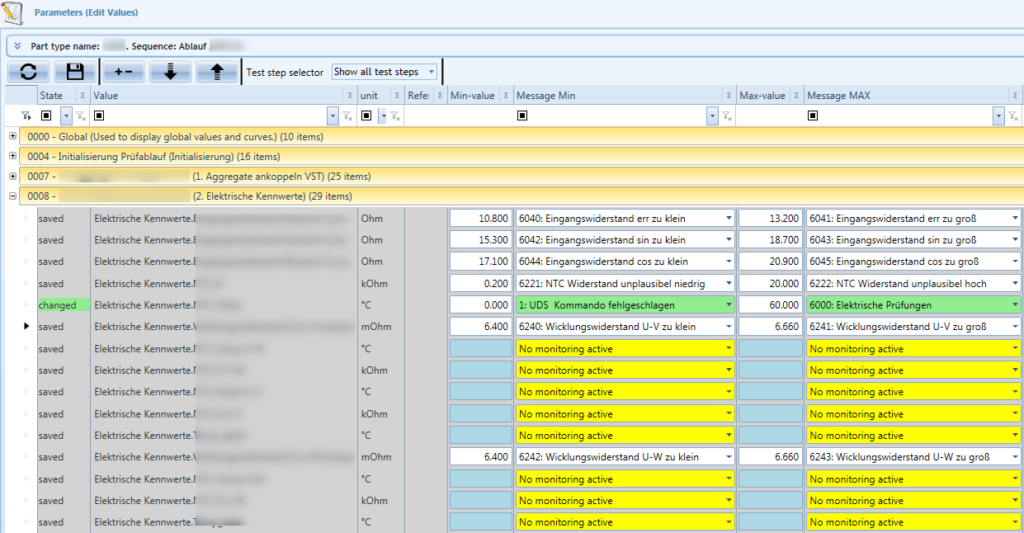
Figure 4: Variant parameters.
To be able to react to product variants with cam-controlled systems, adjustment units are integrated into the drive of the process stations, which require flexible parameter configuration.An adjustment unit consists of a servo axis for length adjustment, which is controlled by recipe through the human-machine interface (HMI). Consequently, the servo motor can be used to set individual product parameters for each variant. Another benefit of this approach is the limitation of asynchronous motion, as the motion profile is still driven by mechanical cams.
In an LTS for PFSs, a product-specific cam-controlled stroke can be configured according to the product recipe. In the event of a format change, the parameters of the servo motor are automatically adjusted. This product-based parameter adjustment eliminates time consuming production stops during a changeover.
PARAMETERS
teamtechnik systems can be easily adapted to new product variants and enable the continuous observation of settings between all components without the time-consuming adaptation of the mechanical parts or software. Flexible processes are used that can automatically decide which parameter sets certain products are manufactured and tested with. By deploying technology-driven and digitally integrated innovation strategies, the entire production line can be controlled and observed via the industrial computer HMI. The combination of assembly and testing tasks in the medical-technical field, as well as complex and precise process technologies such as micro dosing, force-displacement and torque testing, are among teamtechnik’s core competencies.
The system software architecture is structured, including flexible and adaptive interfaces, and independent of the mechanical principles applied. This is the basic prerequisite for efficient production and testing of the different product variants on a single production line. The monitoring and diagnostic systems used can detect critical process states of the assembly system and other connected sub-systems in real-time and automatically trigger optimisation routines
The standardised control, production control and testing software from teamtechnik supports secure process sequences and secure data access to ensure the complete traceability of production data. The test software collects the test data and reliably derives quality evaluations from it (Figure 5). The collected data can also be adapted to customer needs to ensure data processing and archiving on the equipment. The user interfaces are operator-friendly, ergonomically designed and oriented to the basic thought patterns of humans. The concept prevents errors and guides the production operator through all processes, even if the operator is not yet experienced in handling the system.
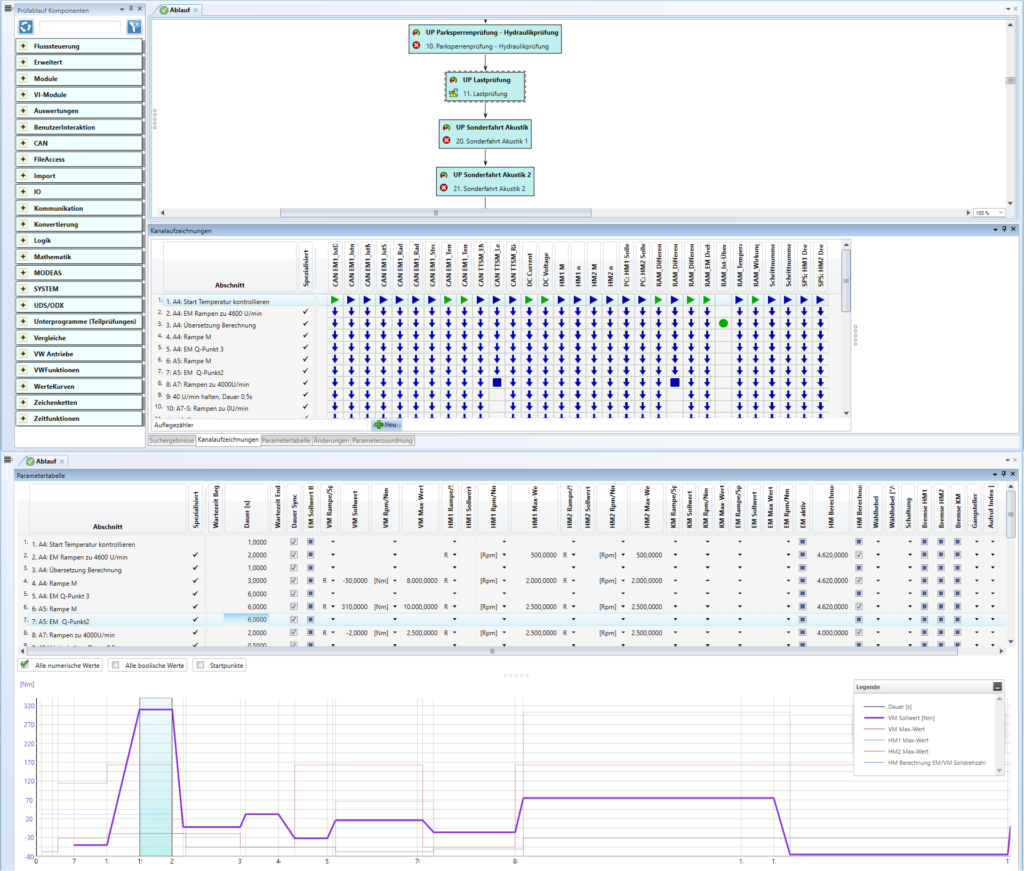
Figure 5: Test parameter collection.
“For the production of customisable product platforms, the qualification strategy is an integral part of the concept design.”
With virtual commissioning, the control software of the real assembly system is connected to a simulation model via appropriate interfaces for testing. This allows many parameters and device interfaces to be tested and optimised prior to system commissioning. The simulation model makes it possible to vastly reduce commissioning times and error planning, as well as the associated implementation-finding. The use of virtual commissioning allows demanding assembly and testing tasks to be completed reliably in a short time. These software solutions, especially for the automation of assembly and testing requirements, are already implemented in teamtechnik systems.
Choosing the right concept is crucial for the desired results to be achieved effectively. Having access to a complete, configurable and user-friendly package, with implemented interfaces, development, assembly, measurement technology, testing technology, feeding technology and qualification according to GMP specifications, is a great advantage for teamtechnik’s customers. With the implementation of regular audits, its customers can ensure more transparency while maintaining the required quality standards.
QUALIFICATION
In the production of medtech products, large quantities of consumable products are continuously manufactured and tested. During production, compliance with quality requirements is extremely important. For the medical industry, these requirements and tech accompanying qualification processes are elementary components of the quality management system. Standardised GMP assembly platforms are only released for production if an error free qualification process has been carried out by experienced qualification engineers. The aim is to meet the necessary quality and legal requirements and to verify that the system functions as specified prior to the design and build of the system. Especially for custom build equipment, the engineering team needs to respond individually and carefully to customer requirements for each project.
For the production of customisable product platforms, the qualification strategy is an integral part of the concept design. To reduce the number of qualification tests at the end of the build phase, the impact of each of the different possibilities must be considered. In the case of fully flexible station concepts, the required test routines can be much more demanding than with mechanically driven systems. This is a strong incentive to choose a mechanically controlled machine platform. As described earlier, in many cases, the degree of flexibility mechanically driven systems offer is more than sufficient and only dependent on the correct analysis of the product. Finally, it is important to select the right approach at the beginning with the resulting quality routines in mind.
The qualification process should begin in the concept phase of the project and then accompanies the design throughout each phase of development, such that the assembly system is released into production in a qualified condition with the confirmed quality and process reliability. In the design phase, the product properties are analysed and, based on this, the assembly and testing processes are then developed. Because each product has individual physical, technological and chemical properties, it is a basic requirement for teamtechnik to understand the product properties in detail (Figure 6).
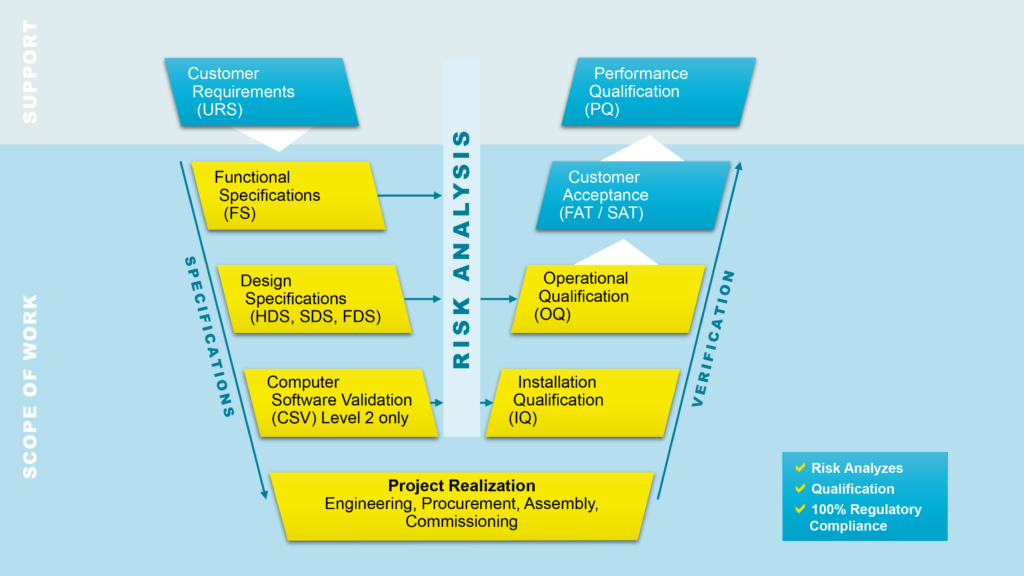
Figure 6: V-model based on GAMP 5.
teamtechnik’s assembly system platforms can have a modular structure and can be qualified as individual modules. If these processes are combined into one system, only the overall line functionality is qualified. After completion of the initial qualification, future changes may only be made using change control. This ensures that all changes are carried out in a co-ordinated manner and clearly documented. The quality-relevant test stations of the assembly system are regularly checked, in what are often referred to as daily checks. The actual values are compared with the target values several times using a functional sequence with external test standards to verify that the quality requirements continue to be met. The system includes a specific production mode to allow these daily checks to be performed easily. The external test standards required for verification must be calibrated in defined cycles. This is necessary because even the smallest measurement error can have a drastic impact on product quality, and thus on patient safety. Calibrating test standards provides further assurance of quality.
SUMMARY
The concept of customisable product platforms is driving the development of specific assembly systems. The flexibility required to produce the different product variants needs to be assessed and addressed individually. This ranges from simple solutions on flexible workpiece holders up to robotic cells. In this assessment, the call for fully flexible processes is often voiced. However, for reliability and efficiency of production, a more individual solution may prove to be the best option.
Even a rigid machine concept, such as a cam-driven machine platform, can be equipped with the flexibility to handle a large variety of products from the same platform. This combines the benefits of flexible product adjustment with the robustness and efficiency of the cam drive. The promotion of fully flexible systems is often driven by uncertainty about what products may be introduced at a later stage. In cases like these, a detailed discussion between the machine builder and the product developer is essential to find the right balance between flexibility and production requirements.
However, the mechanical concept is only part of the production system for customisable product platforms. The concept and configuration of the HMI supports the user, enabling them to control and adjust the production system for the different product variants. Intuitive management and storage of the product variant settings enables production personnel to manage the changeover between variants efficiently. The final piece of the system is the qualification and confirmation of the data integrity. Only with stable interfaces and data storage capability can medical products be reliably manufactured to the highest standards of quality.