Citation: Lindner R, Schulze M, Jaworski W, “Led-Generated UV for Adhesive Curing in Medical Devices”. ONdrugDelivery Magazine, Issue 101 (Oct 2019), pp 40-43.
Roland Lindner, Matthias Schulze and Bill Jaworski discuss how the needs around adhesive use in the manufacture of medical devices such as glass syringes have evolved and how ATS sortimat has developed a new process to meet industry demands.
Syringes first emerged many years ago, in the times of medieval Arabia and the Byzantine Empire, roughly around 1000 AD. The devices continued to evolve but it was not until 1843 that British surgical instrument maker, Daniel Ferguson, received a patent for his “elegant little syringe” with a hand-made hollow needle that was screwed into a glass body of the device.1
With continued developments in materials and production technology, glass syringes are now mass-produced medical devices. In 2016, the glass syringe market grew to more than US$6 billion (£3.8 billion) and continues to grow at an annual rate of 8.4%.2 Much of the current demand can be attributed to the rise in chronic diseases, an aging global population, an increasing number of treatments requiring injectable delivery, and an increase in use of prefilled syringes with self-injection devices. The sterile, prefilled disposable syringe with a fixed cannula for direct injection or for use with autoinjectors has become an industry standard.
CURRENT ADHESIVES & MEDICAL DEVICE JOINING PROCESSES
Ultraviolet light (UV)-cured adhesives are used in almost all medical devices where various components are bonded and joined. These relatively fast curing adhesives use UV wavelength light, and thus do not require the use of solvents for curing. Since the adhesives are able to tolerate steam sterilisation conditions, they are very applicable for sterile and consumable medical devices including tube sets, pen needles, autoinjectors and glass syringes (for the bond between the syringe hub and needle shaft).
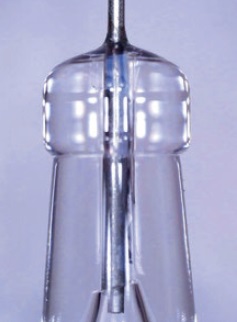
Figure 1: UV-cured adhesive bonding needle to syringe.
These adhesives were initially developed to be cured with UV light produced by mercury vapour lamps (Figure 1). An alternative light source, light-emitting diode (LED) technology, has also continued to evolve. With better availability and more attractive costs, many medical device manufacturers are asking whether UV LED lamps could, or indeed should, be used in place of mercury vapour lamps.
COMPARING MERCURY VAPOUR & LED
Mercury vapour lamps are the current industry accepted standard for the generation of light for bonding stainless steel needles onto glass syringes. They generate a spectrum of light, including frequencies in the ultraviolet range, when the mercury vapour inside the lamp body is excited by a massive electron flow. Though these light sources tend to be more efficient than standard incandescent lamps, they do have various disadvantages including but not limited to short lamp life, high maintenance requirements, heat generation, energy consumption, and health and safety concerns related to the use of mercury and creation of ozone.
LEDs are solid-state devices that convert electrical energy directly into light. The past 40 years have seen significant evolution of LED technology, increasing the performance life and decreasing operating costs. Light source prices can vary but the pricing of LED lamps in general has dropped as the application and use of LED lamps have grown. Compared with mercury vapour lamps, LEDs have a long performance life resulting in lower maintenance costs and reduced service frequency. They also have a lower energy consumption and produce less heat. Overall, there is a lower total cost of ownership.
Another benefit is that solid-state LED lamps require no start-up or cool down period. It is generally accepted that they generate their desired spectrum and reach a steady state performance within milliseconds. Comparatively, mercury vapour lamps require a warm-up period to hit their steady-state performance characteristics. Though both light sources will exhibit performance decay during their lifetime, an LED light source tends to decay at a slower rate than its mercury vapour counterpart. Table 1 provides a summary comparison of the two UV light sources.
Mercury-Vapour UV Lamp | LED UV Lamp | |
Technology maturity | Mature | Established technology but emerging application |
Power consumption | High | Low |
Heat generated | High | Low |
Lamp life | Low | +10x |
Performance decay (stability) | Faster | Slower |
Maintenance burden | High | Lower |
Warm up / time to steady-state | Not instantaneous | Virtually instantaneous |
Table 1: Comparison of mercury vapour lamp and LED for UV light generation.
THE DEMISE OF MERCURY VAPOUR LAMPS
“In close partnership, ATS sortimat and Henkel have worked together to establish a process using LED lamps that will allow the curing of Loctite AA3345® without a change in the adhesive’s formulation.”
The 2013 Minamata Convention on Mercury was established to protect human health and the environment by reducing the release of mercury. This treaty has the goal of eliminating the manufacture, import and export of products containing mercury by 2020. This means that adhesives requiring UV curing will no longer be able to rely on mercury vapour lamps. Bottom line? Regardless of preference, alternative UV-generating light sources must be developed, proven to be equivalent to the current curing method, and adopted.
LED CURING DEVELOPMENT
In the 1980s Henkel (Düsseldorf, Germany) developed its Loctite AA3345® adhesive, which was primarily designed for bonding glass to metal. It is a UV-cured adhesive that has been widely adopted by medical device manufacturers globally. Loctite AA3345® is compliant with ISO 10993, which evaluates the biocompatibility of medical devices and furthermore is used in many medical devices that have been approved by the US FDA. As a result of the anticipated prohibition of mercury vapour lamps as a UV curing source, Henkel has been exploring alternative light sources in order to avoid the timely exercise of developing a new adhesive formula.
sortimat® Assembly Technology, a division of ATS®, has a long-standing relationship with Henkel having designed and built many glass syringe assembly machines that use Loctite AA3345®. In close partnership, ATS sortimat and Henkel have worked together to establish a process using LED lamps that will allow the curing of Loctite AA3345® without a change in the adhesive’s formulation.
In order to establish equivalency in adhesive performance between mercury vapour lamp curing and UV LED curing, ATS sortimat developed a design of experiment (DOE), which included a detailed experiment plan and an assembly system to be used as the test platform for the acquisition of data. The goal was not only to demonstrate adhesive performance but also to arrive at a stable process and technology solution that could be used in automation for our clients (Figure 2). This effort has been going on for several years with a committed team at ATS sortimat, and the results are now the subject of a pending patent application filed by ATS.
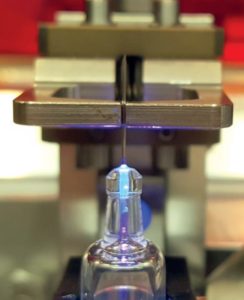
Figure 2: LED UV curing of adhesive on glass syringe with stainless steel needle.
THE AUTOMATION TECHNOLOGY
The Discovery™ Line conveyance system has been ATS sortimat’s proven platform for glass syringe assembly lines with an installation base throughout Europe and North America and many years of successful operation. It was no surprise that this was assumed to be the ideal platform for the adhesive study. However, during the initial phase of the project, it was quickly discovered that a more flexible platform would be required for the new LED curing technology in anticipation of variations in processing and curing times. Because of this, the machine platform for the tests was changed to the ATS SuperTrak® chassis.
The ATS SuperTrak® conveyance system is a high-speed, flexible system that can operate in an asynchronous manner to accommodate the varying processing speeds of different assembly steps. This platform is well-suited for the development of the LED curing process and technology with the added benefit of higher output rates for glass syringe production. With the ATS SuperTrak® platform, production rates of 500 parts per minute are achievable for glass syringe production. ATS sortimat’s experience with the assembly of glass syringes and needles also provided insights to the types of in-process verification, process checks and other non-machine related tests that would be useful for manufacturers. In combination with the assembly technology, these process step checks will build confidence that the LED cured process is repeatable, stable and equivalent to mercury vapour cured process.
During the course of this process and technology development, there was extensive collaboration between ATS sortimat and Henkel to analyse the various trial results and ensure thorough understanding of the adhesive properties during LED curing. Additionally many of the experiments were conducted or results were verified through a technical research institute (DIK Prüfgesellschaft mbH) that brought additional expertise and impartial verification to the effort.
Testing included pull force after sterilisation, surface inspection, and monomeric residue (an indicator of extractables). Preliminary results are promising with pull-force results greater than 100 N on a 25-gauge needle in a glass barrel, and a completely dry surface after curing.
EXPERIENCE AND EXPERTISE TO ENABLE SYSTEM SUCCESS
ATS sortimat has designed and delivered many purpose-built syringe assembly systems, addressing unique customer needs and requirements, and adapting technology approaches as necessary to accommodate advancements in science, processes, and products. The exploration of LED UV curing as an alternative to mercury vapour UV light curing is just the most recent undertaking for ATS in response to a regulatory challenge in the medical device industry.
With ATS sortimat’s most recent developments utilising Loctite AA3345® adhesive and collaboration with Henkel, glass syringe manufacturers can be confident in an alternative UV curing mechanism, LED generated UV light. LEDs can improve maintenance burden, provide in-process feedback and will meet the requirement to reduce reliance on the chemical element mercury.
The process development work in this space has provided ATS sortimat with a vast knowledge bank around the UV light adhesive-curing process including, but not limited to, an understanding of dispensing characteristics, dispensing volumes, curing rates and in-process verification feedback. This has provided ATS sortimat with more refined expertise to support our clients and their own specific process for glass syringe and needle assemble or in other medical devices that require UV cured adhesives.
ATS® and SuperTrak® are trademarks of ATS Automation Tooling Systems Inc. sortimat® is a trademark of ATS Automation Tooling Systems GmbH. These trademarks may not be used without permission.
REFERENCES
- Stepanky P, “In the Hands of Doctors”. Published by ABC-CLIO, 2016.
- Shenoy R et al, “Syringe Market: Global Forecast to 2021”. Research Report, Markets & Markets, 2016.