To Issue 142
Citation: Whelton R, “Next-Generation Autoinjector Platform for High-Dose Drugs”. ONdrugDelivery, Issue 142 (Feb 2023), pp 90–95.
Richard Whelton introduces the new Congruence Autoinjector, a next-generation disposable autoinjector platform, which leverages a compressed-gas power source and has significant advantages over currently available legacy devices, including the ability to deliver higher viscosity and larger volume drugs, easier customisation and enhanced usability that addresses well-known user errors.
Autoinjector devices have evolved significantly since their introduction in the 1980s to address the needs of patient self-injection.1 However, fundamentally different delivery needs have emerged beyond what legacy autoinjector technologies are able to address. Of particular importance is the trend, primarily within biologics, towards high-dose formulations (above 250 mg), which tend to be highly viscous (50 cP+) and/or larger volume (2 mL+).
“Current delivery approaches … for high-dose formulations can introduce compromises to the patient experience and/or pharma operations.”
HIGH-FORCE DELIVERY TODAY HAS KEY TRADE-OFFS
Legacy, spring-based autoinjectors became prevalent when delivery was focused on small-volume, low-viscosity (water-like) drugs. To deliver larger volumes and/or higher viscosities, as is often required for high-dose formulations, springs need to be larger and bulky, meaning the autoinjector becomes bigger and noisier, with higher actuation and recoil forces. Insufficient force from springs can result in long injection-hold times and/or a compromise on needle size (lower gauge). Options with stronger springs have also been explored but with non-standard primary containers.
A new device category – wearable injectors – has emerged to address some of these issues. But the move away from the standard autoinjector format is a significant trade-off, given its generally high patient acceptance and the simplicity it offers to pharma operations. Overall, both current delivery approaches (larger autoinjectors and wearable injectors) for high-dose formulations can introduce compromises to the patient experience and or pharma operations.
Another approach is to use alternative power sources that can deliver higher forces in a standard autoinjector format – but here, too, key trade-offs have previously been made. For example, electromechanical autoinjectors come with high cost and sustainability concerns, causing them to be typically limited to reusable versions for chronic treatments requiring many injections. This means moving away from disposable devices, which are more convenient from a user standpoint, as well as impacting pharmaceutical operations’ end-product support. Compressed gas power sources have also been introduced but have included drawbacks such as high actuation forces, reliability issues and the use of gases with poor sustainability profiles. A potential source of these issues is the use of gas containers and gas sources originally developed for applications outside drug delivery.
WELL KNOWN YET UNADDRESSED USER ERRORS
Beyond the energy source to power an autoinjector for high-dose drugs, there are also user errors that are currently unaddressed by legacy technologies, and which are potentially more impactful and/or common with high-dose drugs. For example, a well-known user error is premature removal from the skin before dose completion,2 which can be caused by:
- Lack of clarity regarding end of dose
- Fatigue due to long hold times
- Patient startled by sounds at injection start or other accidental causes
- A painful injection site.
“There is a compelling need for a next-generation autoinjector platform that extends the capability of autoinjectors beyond
what is possible with legacy technologies.”
Currently, the injection cannot be paused once started, so this error typically results in expensive drugs being lost and the dose not being completed, which can affect clinical outcomes. Pharma companies may also have to bear the cost of replacing the lost or missed dose. The impact is greater for high-dose formulations, as they tend to be less frequently administered, more expensive and may involve longer hold times.
Another user error is when patients forget to let a drug warm up before injection. The colder temperature effectively increases the drug viscosity, which can jam legacy autoinjectors, which do not inherently have sufficient force to overcome the higher viscosity. The effective result with high-dose formulations is the waste of an expensive dose, as well as potential treatment delay due to the next dose not necessarily being on hand.
The standard user-error mitigation approach with legacy autoinjectors has been the use of indicators and patient training. However, it is known that these alone are insufficient, and a better approach would be innovative autoinjector designs that reduce or eliminate the negative consequences of these errors altogether.2 This would not only potentially reduce costs and improve treatment adherence but also enhance the patient experience by providing peace of mind.
Overall, there is a compelling need for a next-generation autoinjector platform that extends the capability of autoinjectors beyond what is possible with legacy technologies. What is needed is a true platform, designed to be suitable for the full range of current and future drugs – both standard and high-dose formulations – and that enhances usability and better meets key pharma needs throughout development and production, rather than forcing compromises.
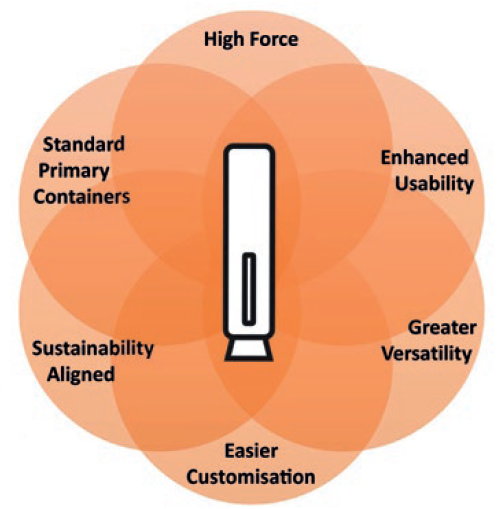
Figure 1: Key criteria for next-generation autoinjector.
CONGRUENCE’S APPROACH TO SOLVING UNMET AND EMERGING NEEDS
Congruence Medical Solutions designed the Congruence Autoinjector to be a next-generation platform, addressing key need-based criteria (Figure 1):
- High force capability – enabling drug delivery in situations where there is a large volume, high viscosity, cold temperature, fine injection needle or a combination of these factors.
- Enhanced usability – has the look and feel of widely used 1 mL disposable autoinjectors, while also addressing additional usability needs, especially for high-dose drugs.
- Greater versatility – suitable not just for high viscosity and large volume but also “standard” formulations to address a broad range of therapies in one platform.
- Easier customisation – for faster, low-risk device development.
- Uses standard primary containers – including glass prefilled syringes (PFSs).
- Sustainability aligned.
The team at Congruence has decades of drug delivery device experience, but the company itself is a new autoinjector player. Therefore, as the team set out to find the optimal way to solve the unmet and emerging needs, it was unburdened by pre-existing technology or design, and avoided attempting to force legacy technology into a novel solution.
A pivotal decision point was the power-source selection, as it has a significant influence on the capabilities and size of an autoinjector (Figure 2). Ultimately, the company chose to proceed with compressed gas. This power source enables high injection forces for injecting drugs in standard primary containers without the impact shock observed in spring-based systems at the start of injection, as well as enabling easier customisation and assembly and a more compact device format with quieter delivery.3
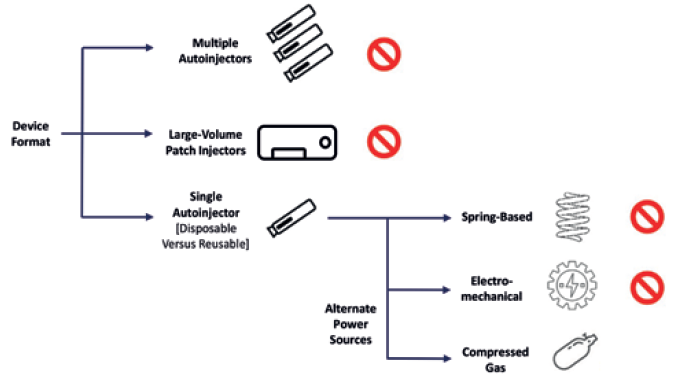
Figure 2: Key choices in injector design.
When using compressed gas as a power source, there are other options to consider, such as gas type and gas-container design. To mitigate environmental and sustainability concerns, the Congruence Autoinjector uses an inert gas. The device also uses a customised, proprietary gas container to provide the flexibility to include novel usability features that address the issue of gas leakage, thereby minimising the actuation force and other potential issues. The proprietary compressed gas source, combined with the proprietary autoinjector design, allows for further customisation opportunities that are not possible with currently available autoinjectors.
In terms of the core usability and functionality of the Congruence Autoinjector, the team chose to include base features aligned with what is typically expected in currently available autoinjectors as a minimum (Figure 3). It is a two-step autoinjector, requiring the user to simply remove the cap, place on the skin and push down to activate automatic needle insertion. There are standard visual and audible indicators across the start, progression and end of dose, including a large, clear drug viewing window. The needle is hidden at all times, and at the end of the dose a proprietary passive needle-safety shield deploys and locks.
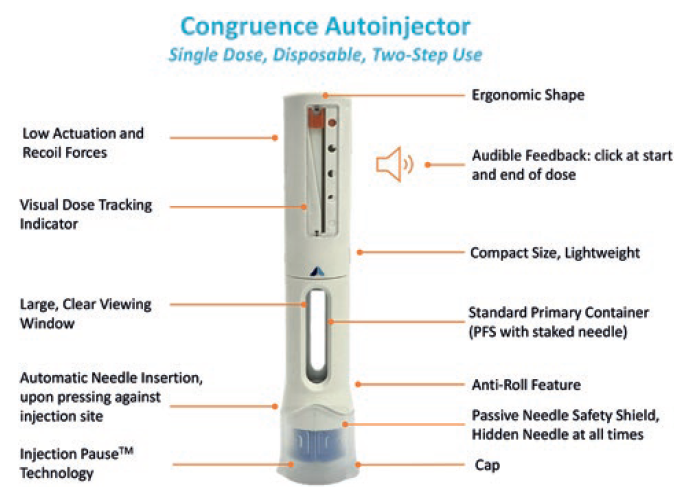
Figure 3: Congruence Autoinjector overview.
HIGH INJECTION FORCE CAPABILITY IN A COMPACT SIZE
The Congruence Autoinjector can deliver a range of injection forces, from low to very high, and is readily adjustable. It is capable of rapid drug delivery even in situations with a large drug volume, high viscosity, cold temperature, fine injection needle or a combination of these factors. As an example, one embodiment of the Congruence Autoinjector has been shown to deliver 2.25 mL of 100 cP solution in 15 seconds from a glass PFS for biologics (SCHOTT’s syriQ BioPure®) with a 27G staked needle.
Crucially, the Congruence Autoinjector can deliver high forces while incorporating standard primary drug containers, including glass syringes. Therefore, pharma companies do not need to deal with the arduous and expensive process of validating and using novel primary containers. Furthermore, the proprietary compressed gas source design enables very low, imperceptible actuation (3N) and recoil forces, as confirmed in a Congruence user study.4
In comparison with many large-volume and high-viscosity autoinjectors, the Congruence Autoinjector has an ergonomic shape and compact size. With a 2.25 mL PFS incorporated, the dimensions for one embodiment are 14.1 cm height and 2.4 cm width – which is the same or smaller than most conventional, commercially available 1 mL autoinjectors, and likely smaller than most 2.25–5 mL autoinjectors incorporating legacy technologies. A Congruence user study showed the 2.25 mL Congruence Autoinjector form factor was well accepted by patients and healthcare professionals (HCPs) – equivalent to commercially available 1 mL autoinjectors (Figure 4).4 It is therefore suitable for injections using either a 2.25 mL PFS or 1 mL long PFS.
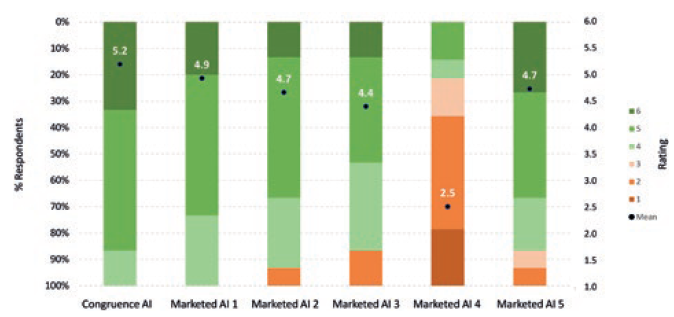
Figure 4: Acceptability of Congruence Autoinjector 2.25 mL form factor and mock-ups of marketed large-volume autoinjectors (6 = completely acceptable; 1= completely unacceptable) (n=15).
The compact size also aligns with sustainability objectives – it results in fewer device materials, lower transportation weight, smaller packaging and a reduced cold-chain footprint. Sustainability can be further enhanced through manufacturing and material strategies.
Table 1 indicates one reason why the Congruence Autoinjector is so compact. It shows the relationship between syringe size (or, more specifically, syringe cross section) and delivery force required. For larger drug volumes, larger syringe sizes are needed, which in turn results in higher injection forces. For a spring-based autoinjector, this would mean different, larger springs are progressively required, whereas for the Congruence Autoinjector, the same compressed gas source provides an increased injection force as syringe cross-section increases.
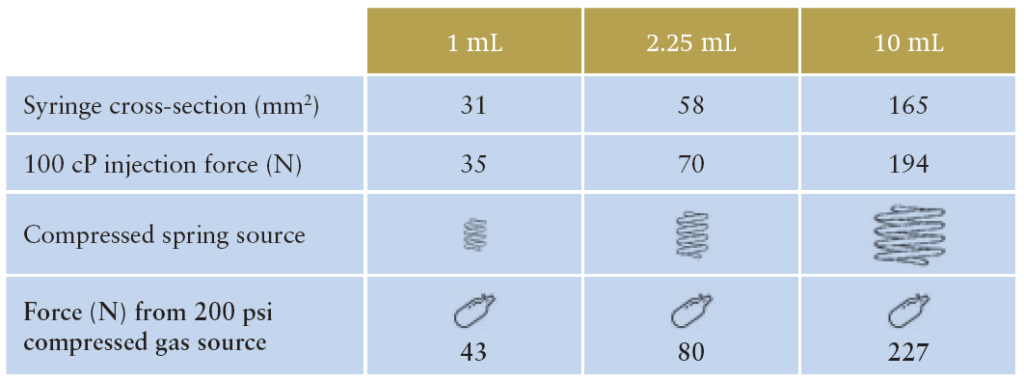
Table 1: Force (N) from 200 psi (example) compressed gas source by syringe size.
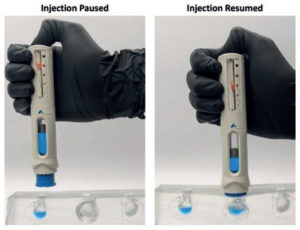
Figure 5. Congruence Injection Pause™ technology and novel visual dose progress indicator address premature removal from skin, increasing potential for full-dose delivery.
NOVEL FEATURES ENHANCE USABILITY
The Congruence Autoinjector truly addresses key user errors, including premature removal from skin before dose completion – both its potential impact and frequency – as well as cold-drug injections.
The unique Injection Pause™ feature and a novel Visual Dose Progress Indicator work in combination to mitigate the impact of premature removal (Figure 5). The Injection Pause™ feature pauses the injection if the device is removed from the skin before dose completion, ensuring that no drug is lost. The visual dose progress indicator shows the amount of dose remaining, enabling patients to have a more informed conversation with their HCP. They can also continue the dose to completion if desired, as the Injection Pause™ feature allows needle reinsertion and injection resumption. The needle always remains hidden, and the passive needle-safety shield locks only once the full dose is delivered.
Reduced incidence of premature removal and incomplete dosing is addressed in several ways, alongside mitigation of cold-drug injection. The visual dose progress indicator ensures that the user knows how far an injection has progressed, which is even more crucial with cold drugs as the injection time can change, the quiet injection reduces the potential for patients to be startled or concerned, and the high injection force reduces the chance of the device jamming due to cold-drug injection.
In an initial Congruence user study, these novel features were well received by patients and HCPs (Figure 6).4 Any concerns regarding reinsertion with the same needle are mitigated by the fact that there are examples of other approved therapies involving needle reinsertion.5,6 Furthermore, any perception of risk (valid or otherwise) was viewed by participants as being outweighed by the significant benefits – especially the extra confidence that the full dose would be received at the right time, as well as an overall better injection experience. The potential to reduce drug (and device) waste was also seen as sustainability aligned and reducing the cost burden on pharma companies to replace lost doses.
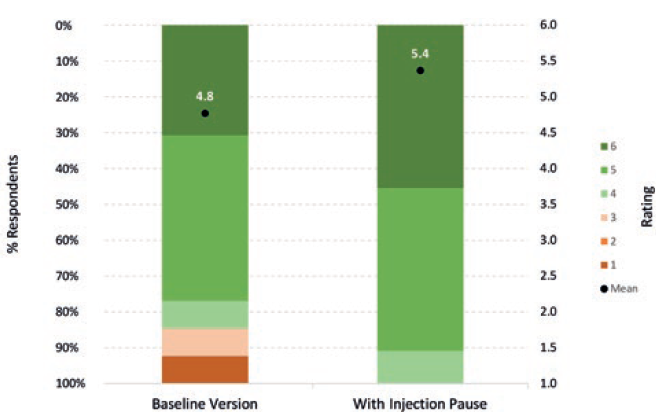
Figure 6: Acceptability of Congruence Autoinjector – with and without Injection Pause™ technology (6 = completely acceptable; 1= completely unacceptable) (n=15).
“The Congruence Autoinjector platform addresses a broad range of
possible viscosity and volume requirements, as well as minimising customisation time and cost.”
SINGLE PLATFORM WITH GREATER VERSATILITY
An ideal self-injection device platform should accommodate a wide range of drug-specific requirements, such as drug volume and viscosity, without the need for significant changes. This also means that pre-existing device design, test data and manufacturing capabilities should be usable, thereby minimising integration costs, time to market and risk (for customised products). This is very useful if the drug formulation changes during development, if a drug has different dosing options or if a pharma company wants to leverage the device across a drug portfolio.
The Congruence Autoinjector platform addresses a broad range of possible viscosity and volume requirements, as well as minimising customisation time and cost, including for parameters such as:
- Drug viscosity: 100+ cP
- Syringe size and type: ISO 11040 compliant standard glass syringes – 1 mL long, 2.25 mL and 5 mL; plus different fill volumes (design is agnostic to fill volume). Cartridges also possible for 5 mL+
- Target injection time: typically <15s
- Standard needle gauges
- Same form factor for 1 mL and 2.25 mL is possible.
- The combination of proprietary power source and specific autoinjector design is key to enabling the range and speed of these customisations. In addition, the autoinjector can be adapted to accommodate different external look and feel options.
LOOKING TO THE FUTURE
The Congruence Autoinjector platform marks a significant update for the autoinjector category, with an ability to address the delivery needs of the full range of current and future drugs, including high-dose formulations (Table 2). Congruence plans to continue to work with its customers to meet their specific needs with customised versions of the device that will enable patients to receive critical therapies.
Property | Congruence Autoinjector Specification |
Key needs addressed | Viscous, large volume |
Device type | Autoinjector |
User profile | Caregivers, patients, HCPs |
Administration route | Subcutaneous, intramuscular |
Primary container format | 1 mL long, 2.25 mL or 5 mL standard prefillable syringe; drug cartridge option possible |
Primary container material | Glass or polymer |
Usage | Single dose; disposable |
Dosage type | Fixed |
Dose volume | 0.3–2.25 mL (5 mL or higher if required) |
Viscosity | 100+ cP |
Injection time | Customisable (typically <15 s) |
Priming & dose setting | N/A |
Needle attachment | Pre-attached (staked-in) |
Needle safety | Integrated, passive needle shield |
Injection feedback | Audible & visual indicators, drug viewing window |
Premature removal safety | Injection Pause™ technology |
Table 2: Congruence Autoinjector specifications summary.
REFERENCES
- Whelton R, Green P, “Autoinjectors: Historical achievements and compelling needs driving next-generation devices”. ONdrugDelivery, Issue 138 (Oct 2022), pp 14–17.
- Calawa B, “Staying Dry: How To Limit Wet Injections In Auto-Injector Design”. Med Device Online, Nov 2015.
- Welch W, “Advancements and Evolution of Power Sources in Drug Delivery”. ONdrugDelivery, Issue 133 (May 2022), pp 57–60.
- Congruence Autoinjector User Study, Aug 2022 – data on file with Congruence Medical Solutions.
- “IMLYGIC® (talimogene laherparepvec) Suspension for intralesional injection”. Amgen package insert, Jun 2022.
- “DARZALEX FASPRO® (daratumumab and hyaluronidase-fihj) injection, for subcutaneous use”. Janssen package insert, Nov 2022.