To Issue 140
Citation: Pillitteri S, Neveu A, Zellnitz-Neugebauer S, “Powder Characterisation for DPI Performance in Capsule-Based Inhalers”. ONdrugDelivery, Issue 140 (Nov 2022), pp 77–81.
Salvatore Pillitteri, Aurélien Neveu and Sarah Zellnitz-Neugebauer discuss the analysis of three powder blends of salbutamol sulphate with distinct lactose grades, using tapped density and rotating drum methods.
Respiratory diseases are commonly treated with orally inhaled drugs – via dry powder inhalers (DPIs), for example. DPIs typically consist of the micronised API in the size range 1–5 μm, blended with a larger inactive carrier material.1 But such small API particles often have poor flowability and high cohesion, which makes handling difficult.2,3 Moreover, they rarely exhibit the expected performances in terms of aerosolisation and absorption. Consequently, their properties must be improved with the addition of larger carrier particles to reach the required performance.
“When the aeration increases, the powder increases its volume, due to the integration of air in the powder during the flow.”
Lactose is often used, and the large variety of available grades allows for designing the DPI according to the requirements.1 However, it remains difficult to predict the behaviour of the blend. The fine particle fraction and the fine particle mass (FPM) are quantities measured via impaction to evaluate the in vitro aerosolisation performance of the API. Since this measurement is cumbersome and time consuming, simple methods to evaluate DPI performance based on bulk powder characterisation are necessary. Therefore, different studies have focused on the investigation of measurement methods for DPI characterisation.3
In this study, Granutools and Research Center Pharmaceutical Engineering (RCPE) characterised three powder blends of salbutamol sulphate (SBS) with distinct lactose grades using tapped density (GranuPack, Granutools) and rotating drum (GranuDrum, Granutools) methods. Their usability has been evaluated by correlating the bulk powder properties with the in vitro performance when the mixtures are delivered with a capsule-based inhaler.
MATERIALS
Three binary powder blends were analysed in the study. Three lactose grades were used to compose the different blends: DuraLac® H, FlowLac® 90 (both MEGGLE, Wasserburg, Germany) and Respitose® SV003 (DFE Pharma), shown in Figure 1. Each was mixed with 2% of micronised SBS (DV0.5 = 1.43 ± 0.04 μm) in a low-shear tumble blender (TC2, Willy A Bachofen Maschinenfabrik, Basel, Switzerland) for 90 minutes at 62 rpm.
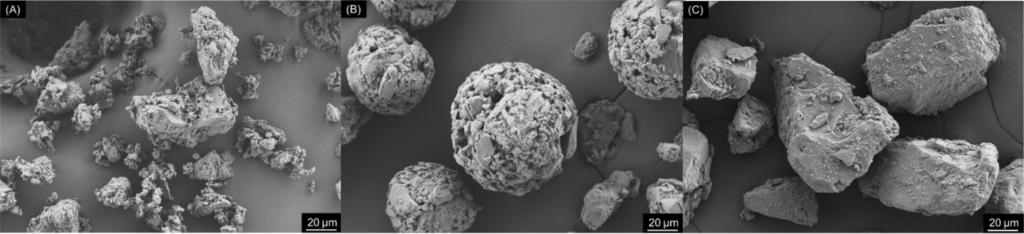
Figure 1: Scanning electron microscopy images of the different grades of lactose: (A) DuraLac® H, (B) FlowLac® 90 and (C) Respitose® SV003.
“Fine particles have the ability to fill the voids between larger ones,
which tends to increase the density.”
EXPERIMENTAL METHOD
The bulk properties of the blends were characterised by two instruments from Granutools: the GranuPack and the GranuDrum.
GranuPack
The GranuPack conducts an automated tapped density measurement characterising the packing dynamics of a powder. It consists of a steel cylindrical cell, 26 mm in diameter and 100 mm in length, in which a narrower tube, open on both sides, is initially inserted. Once the powder is poured inside (about 35 mL), the narrower tube is moved upward at a low and constant velocity of 1 mm/s. This initialisation protocol allows a reproducible initial granular pile and reduces operator errors.
After initialisation, the cylindrical cell containing the powder performs a succession of free falls, called “taps”. After each tap, the powder densifies and the bulk density is measured. In this study, each measurement lasted 1,500 taps. The initial and final tapped density, ρ(0) and ρ(1,500), were obtained and the Hausner ratio Hr=(ρ(1500))/(ρ(0)) was calculated. This number characterises the flowability of the powder. The larger it is, the lower the flowability. A high Hausner ratio can come from strong particle interactions, indicating high cohesion, since these interactions tend to decrease the initial density.
GranuDrum
The GranuDrum carries out an automated powder flowability measurement. It consists of a cylinder with transparent sidewalls, called a drum, half filled with approximately 55 mL of powder. The drum can rotate at different speeds, from 2 to 60 rpm, and a charge-coupled device (CCD) camera takes 40 pictures of the powder interface, each separated by 1 s. The powder interface is detected by an algorithm and averaged over the 40 pictures. The fluctuations around the average interface define the dynamic cohesive index (σf), related to the cohesiveness of the powder. The larger this index, the more cohesive the powder and consequently the lower its flowability.
Information about σf at different speeds is useful for highlighting rheological behaviours. For example, if σf decreases when the rotation speed increases this indicates shear-thinning and, conversely, σf increasing with increasing rotation speed points to shear-thickening. In addition to the measurement of σf, GranuDrum can measure powder aeration index during the flow. This index is the ratio between the estimated volume of the powder’s volume and the volume at the lowest speed. When aeration increases, the powder increases due to the integration of air.
Aerosolisation performance was quantified in vitro with a next-generation impactor (NGI) by Pinto et al and a Cyclohaler® capsule-based inhaler.3 For three airflows (100, 60 and 28 L/min), FPM was measured by filling about 40 mg of blend in a capsule and discharging it into the NGI. In this study, each measurement was repeated three times.
Name | ρ(0) (g/mL) | ρ(1,500) (g/mL) | Hr |
DuraLac® H | 0.586 ± 0.009 | 0.843 ± 0.003 | 1.439 ± 0.018 |
Respitose® SV003 | 0.679 ± 0.002 | 0.784 ± 0.002 | 1.156 ± 0.003 |
FlowLac® 90 | 0.644 ± 0.003 | 0.744 ± 0.005 | 1.155 ± 0.003 |
Table 1: Parameters obtained with the GranuPack for three powder blends: initial density ρ(0), final density ρ(1,500) and Hr (three tests, mean±SD).
RESULTS AND DISCUSSION
Table 1 presents the results obtained with the GranuPack. The DuraLac® blend had the lowest initial density ρ(0), followed by the FlowLac® blend and then the Respitose®. However, the DuraLac® blend had the highest final density ρ(1,500), resulting in a higher Hausner ratio than the other two. This indicates that the DuraLac® blend had a higher cohesion index than the FlowLac® and Respitose® blends. Particle analysis of the raw powders, shown in Table 2, revealed that DuraLac® had the broadest size distribution with a larger proportion of fine particles compared with the two other lactose powders.
Name | D50 (μm) | Fraction < 10 μm (%) |
DuraLac® H | 52.89 ± 7.10 | 13.48 ± 1.76 |
Respitose® SV003 | 60.26 ± 3.76 | 3.34 ± 0.07 |
FlowLac® 90 | 73.44 ± 2.96 | 0.54 ± 0.045 |
Table 2: Particle characteristics for three raw lactose powders DuraLac® H, Respitose® SV003 and FlowLac® 90 (three tests, mean±SD).
“The shear-thinning behaviour observed for the DuraLac® blend could come from its larger proportion of fine particles.”
The results from GranuDrum areSince fine powders are known to be more cohesive than powders with larger particles, this could explain the lower density of the DuraLac® blend. Indeed, a high cohesion index means strong interactions between grains that can support the weight of several neighbours, which leads to a large number of voids and therefore a low density, compared with a non-cohesive powder. On the contrary, fine particles have the ability to fill the voids between larger ones, which tends to increase the density and could explain the larger final density of the DuraLac® blend. The voids generated by high cohesion can be rapidly filled by fine particles when successive taps move these particles and densify the system. Regarding the Respitose® and FlowLac® blends, the Hausner ratios are too close to each other with overlapping error bars to be able to differentiate the cohesiveness of the two powders.
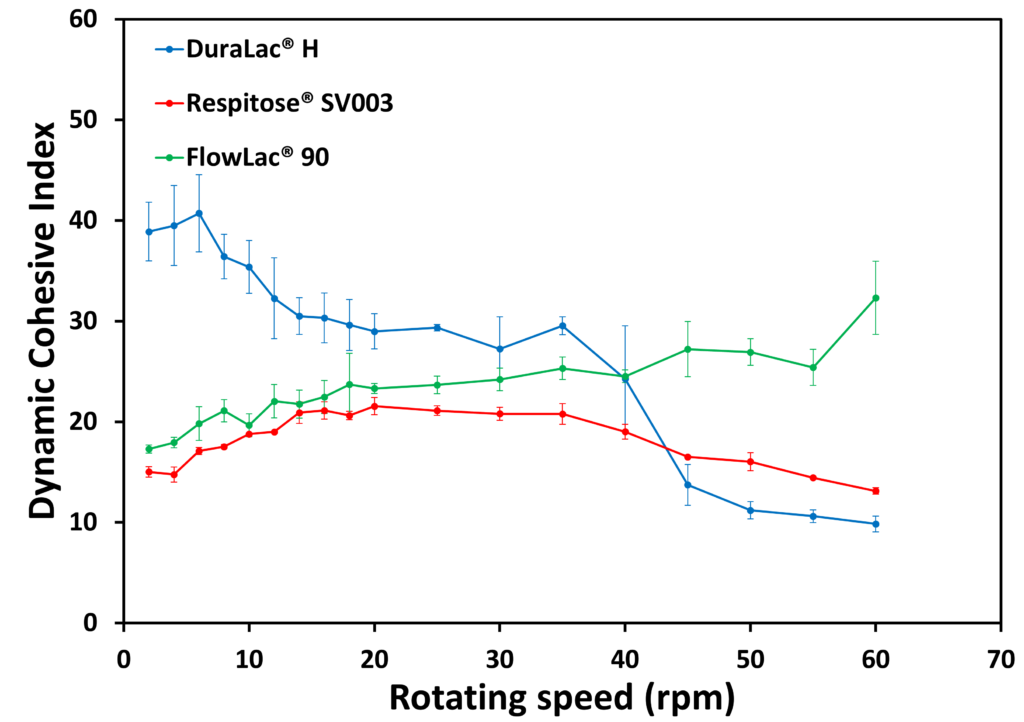
Figure 2: Dynamic cohesive index as a function of the rotating drum speed for the three powder blends.
The results from GranuDrum are presented in Figures 2 and 3. Figure 2 shows σf as a function of rotating drum speed. At low speed, one observes that the DuraLac® blend is the most cohesive powder as indicated by the Hausner ratio. This result is consistent since the measurement of σf is close to a quasi-static condition as undergone by the powder with the GranuPack. The three powder blends can be ranked from the most cohesive to the least cohesive as follows: DuraLac® > FlowLac® > Respitose®.
“Measurements in a dynamic state can be more relevant than quasi-static measurements.”
Conversely, at higher rotation speeds, between 45 and 60 rpm, the DuraLac® blend is observed to be the least cohesive. Indeed, the powders exhibit different rheological behaviours: while the DuraLac® blend shows shear thinning, the FlowLac® blend exhibits shear-thickening behaviour, and the Respitose® blend shows a constant cohesion, changing the classification that can be made at low-shear stress conditions. From the most cohesive blend to the least cohesive, one has: FlowLac® > Respitose® > DuraLac®. The shear-thinning behaviour observed for the DuraLac® blend could come from its larger proportion of fine particles (Table 2). Indeed, fine particles are known to increase cohesion but it has also been observed that a small number of fine particles in the presence of larger ones can lead to shear-thinning behaviour.4
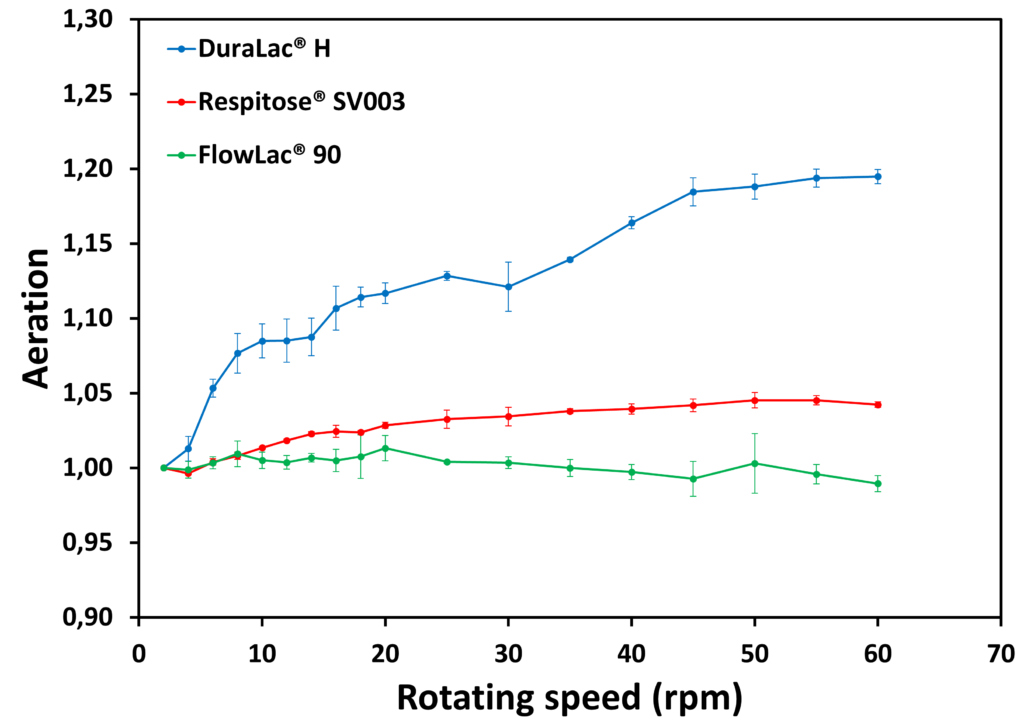
Figure 3: Aeration index as a function of the rotating drum speed for the three powder blends.
In Figure 3, aeration index as a function of rotating drum speed is presented. For the DuraLac® blend, a large increase in aeration index versus rotation speed can be seen, compared with the Respitose® and FlowLac® blends. Air incorporated in the DuraLac® blend due to mechanical agitation could decrease the amount of contact and and the number of interactions between particles, which could also explain the decrease in cohesion of this blend. Both aeration and fine particles may play a role in the shear-thinning behaviour of the DuraLac® blend. One can see that the Respitose® blend has an intermediate ability to be aerated, while the FlowLac® blend presents the worst propensity to be aerated, particularly at higher speeds, where the aeration ratio is gently decreasing with the rotation speed.
The FPM of the DuraLac®, Respitose® and FlowLac® blends was investigated and the results are presented in Table 3.
Name | 100 L/min | 60 L/min | 28 L/min |
DuraLac® H | 0.80 ± 0.10 | 0.72 ± 0.01 | 0.62 ± 0.01 |
Respitose® SV003 | 0.74 ± 0.02 | 0.60 ± 0.04 | 0.38 ± 0.01 |
FlowLac® 90 | 0.20 ± 0.06 | 0.13 ± 0.02 | 0.01 ± 0.00 |
Table 3: Fine particle mass of SBS, determined with the NGI at different flow rates (three tests, mean±SD).
It can be seen that airflow has an impact on FPM. Indeed, higher airflow leads to higher FPM. The DuraLac® blend has the highest FPM, followed by Respitose®, while the FlowLac® blend had the lowest FPM.
The quasi-static measurements are not able to predict the performance of the powder blends. Based on the measurement of the Hausner ratio, a differentiation is not possible between the Respitose® and FlowLac® blends, while a clear difference can be observed between these two blends in terms of FPM. Likewise, the measurements recorded by the GranuDrum at low speeds rank the powder blends from the most cohesive to the least as follows: DuraLac® > FlowLac® > Respitose®. This does not correlate well with the performance classification given by FPM, from the highest to the lowest: DuraLac® > Respitose > FlowLac®. On the contrary, the cohesion characterisation made at high rotating speeds allows correlation between σf and FPM. The DuraLac® blend is observed to be the least cohesive powder at high rotating speed and has the highest FPM. On the other hand, the FlowLac® blend shows the highest cohesiveness with the lowest FPM, and the Respitose® blend exhibits intermediate behaviour in terms of cohesiveness and FPM.
Moreover, considering that in a capsule-based inhaler the powder is released by a pierced capsule rotating at high speed (around 1,000 rpm),2 one could legitimately suppose that a measurement made at high shear stress, as performed by the GranuDrum at high rotating speeds, is more relevant than a measurement made at low shear stress, as performed by quasi-static measurements. While quasi-static measurements are generally used for powder characterisation to predict DPI performance, complex rheological behaviours, such as shear thinning, exhibited by the DuraLac® blend, or shear thickening, exhibited by the FlowLac® blend, completely reverse the classification that can be made under quasi-static conditions. In this study, the lower the cohesion, the higher the FPM.
CONCLUSION
Three powders composed of a mixture of SBS with different lactose grades were analysed in this study regarding rheological properties and in vitro aerosolisation performance. The Hausner ratio, generally used to classify powder in terms of cohesiveness, is unable to differentiate between the Respitose® and FlowLac® blends in terms of cohesiveness, and the dynamic cohesive index at low rotating speeds is not well correlated with the FPM, representing the DPI performance.
However, it was highlighted with the GranuDrum that the three powder blends exhibit different rheological behaviours: shear-thinning for the DuraLac® blend, shear-thickening for the FlowLac® blend and a constant cohesion for the Respitose® blend. Considering σf at higher rotating speeds, classification of the blends in terms of cohesion is completely different from that obtained from quasi-static measurement. With dynamic measurement performed by the GranuDrum at a high rotating speed, closer to the shear state that a powder can undergo during aerosolisation, one obtains a classification in terms of cohesiveness that can be correlated with the FPM obtained with the NGI. These results have demonstrated that measurements in a dynamic state can be more relevant than quasi-static measurements.
REFERENCES
- Neveu A, Crowley M, McGorisk T, “Characterisation of lactose powders for DPI applications”. ONdrugDelivery, Issue 119 (Apr/May 2021), pp 46–50.
- Benque B, Khinast JG, “Understanding the motion of hard-shell capsules in dry powder inhalers”. Int J Pharm, 2019, Vol 567, p 118481.
- Pinto JT et al, “Understanding carrier performance in low-dose dry powder inhalation: An in vitro–in silico approach”. Pharmaceutics, 2021, Vol 13(3), p 297.
- Janssen PH et al, “ Impact of Powder Properties on the Rheological Behavior of Excipients”. Pharmaceutics, 2021, Vol 13(8), p 1198.