To Issue 152
Citation: Pagnoud E, Verger E, Brocco B, “Primary Packaging Considerations for Supporting Compliance to Annex 1 Revision”. ONdrugDelivery, Issue 152 (Oct 2023), pp 98–102.
Edouard Pagnoud, Estelle Verger and Benjamin Brocco look at the new requirements associated with EMA GMP Annex 1 revision regarding injectable primary packaging for ensuring the sterility and safety of medicinal products and consider how Aptar Pharma‘s PremiumFill® can reduce the risk of contamination and defects.
“The EMA’s GMP Annex 1 emphasises the criticality of implementing contamination control and sterility assurance strategies.”
The pharmaceutical landscape is undergoing a transformative phase marked by the emergence of biotech drugs, such as monoclonal antibodies, recombinant proteins and nucleic acids, that promise to revolutionise patient care and address unmet therapeutic needs. Additionally, biosimilars, which are analogous to biologic products, are also gaining traction in the market due to their potential to provide cost-effective treatment alternatives to innovative biotech drugs. However, the sensitive nature of these drugs requires additional care when it comes to packaging and delivery. In addition to maintaining their stability and efficacy, packaging should also ensure the utmost safety for patients and promote ease of use.
The process of bringing a drug to market is intricate, demanding both time and significant financial resources. Given the high stakes, pharma manufacturers are always on the lookout for strategies to optimise their development pipelines, minimise potential risks and avoid costly scraps. This becomes even more pertinent when taking the evolving regulatory landscape into consideration. The recent updates to the European Medicines Agency’s Good Manufacturing Practice (EMA GMP) Annex 1 emphasise the criticality of implementing contamination control and sterility assurance strategies, as particulate contamination and sterility are highlighted as the main causes for US FDA product recall.1,2 While these regulatory evolutions are clearly aimed at improving patient safety, they put pharma manufacturers under pressure to meet these increasing standards of quality.
Primary packaging plays a pivotal role in this context as it is in direct contact with the drug. Any compromise in packaging quality can have direct implications on the drug’s efficacy and safety. Therefore, it is imperative for drug manufacturers to recognise the significance of primary packaging early in the development process. Building partnerships with experts in pharma packaging at the initial stages can be a game-changer, helping to ensure that the drug’s journey from lab to market is seamless and successful.
Aptar Pharma, with expertise in rubber manufacturing and pharma grade processes, is an ideal partner to support drug manufacturers in this crucial aspect of drug development.
DRUG DEVELOPMENT: A COMPLEX AND COSTLY PROCESS
In the pharmaceutical industry, the safety and efficacy of injectable drugs are paramount. However, one of the leading causes of recalls by the FDA for injectable drugs is particulate contamination. Such contaminants can pose health risks to patients and lead to rejection of a dose or batch on the filling lines. As the industry evolves and regulatory standards become increasingly stringent, manufacturers must ensure the purity and safety of their products.
The recent revision of Annex 1 of the EMA GMP, which came into force on August 25, 2023, aims to ensure the sterility and safety of medicinal products. This requires drug manufacturers to implement a pharmaceutical quality system that encompasses the specific requirements of sterile products manufacture, such as the control of microbial, particulate and endotoxin contamination, throughout the product’s life cycle.
The establishment of a contamination control strategy (CCS) is a pivotal element that must be applied across facilities, pinpointing and mitigating potential contamination sources. However, it is not just a directive for drug manufacturers, but rather extends its influence across the entire supply chain. This ensures that every stakeholder, including primary packaging suppliers, adheres to stringent contamination control standards. By integrating the entire supply chain into its framework, the CCS ensures that every step, from initial production to final packaging, is held to the highest standards of product quality and safety.
APTAR PHARMA’S PREMIUMFILL®: QUALITY ASSURANCE FOR YOUR PATIENTS AND OPERATIONAL EFFICIENCY
For decades, Aptar Pharma has been leading the way in developing injectables closure components, leveraging pure formulations and state-of-the-art manufacturing processes (Figure 1). As a key partner to drug manufacturers, Aptar Pharma adapts to evolutions of the market to enable successful drug development. Already a world-leader for rigid needle shields and a key player on ethylene tetrafluoroethylene (ETFE) film-coated solutions for sensitive drugs with PremiumCoat®, Aptar Pharma has been developing new strategies and solutions to meet the increasing needs of the market regarding external contaminations.
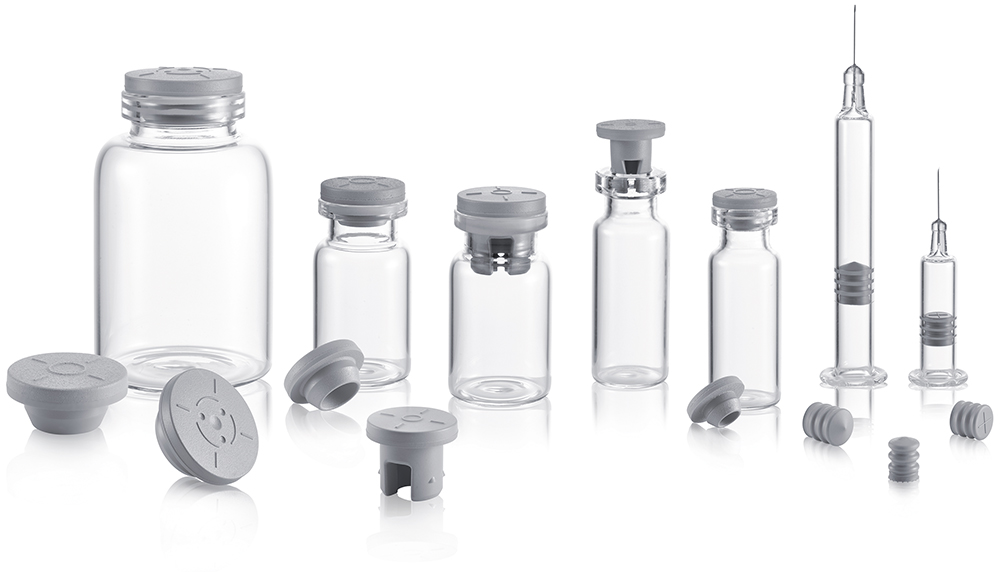
Figure 1: Aptar Pharma range of PremiumFill® closure solutions.
“Aptar Pharma experts have evaluated that switching to PremiumFill® would not require re-approval, making PremiumFill® a quick and easy way to further support compliance with the requirements of Annex 1.”
PremiumFill® solutions for vial stoppers and syringe plungers provide pharma partners with higher quality closure components with tighter specifications on key contamination criteria. These specifications cover contamination from biological origin, particulates (including foreign, metallic or rubber embedded) and fibres, with an overall improved particulate count index.
PremiumFill® uses the same market-proven rubber formulations and component designs, and leverages Aptar Pharma’s Ultraclean 6 finishing technology. The improved specification is achieved by performing all the moulding and trimming steps in an ISO 7-classified cleanroom, thereby limiting the risk of introducing external particles onto or within the rubber. In addition to cleanroom manufacturing, the PremiumFill® process includes high-precision robotisation during the moulding steps, mitigating the risk of introducing particles through human interaction, while also enhancing reproducibility and consistency (Figure 2).
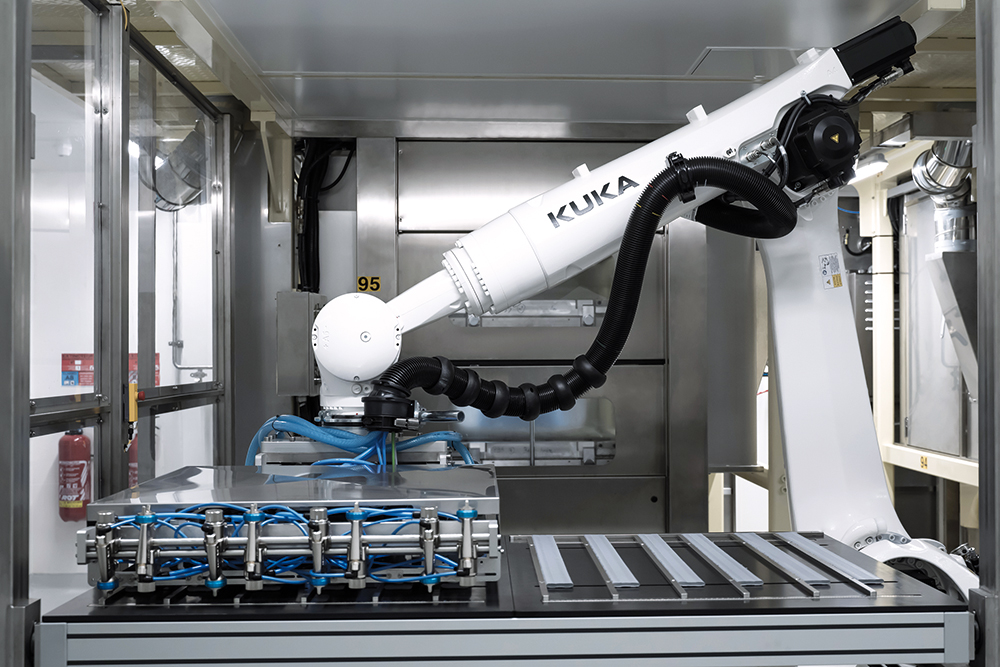
Figure 2: A. Ready-to-use lyophilisation stoppers in their packaging with irradiation indicator. B. Aptar Pharma vial stoppers and syringe plungers in four RTP bags among the models available.
“To limit the risk of contamination during this step, section 4.18
of the Annex 1 revision strongly recommends the use of isolators or the RABS in conjunction with RTP bags.”
All these technologies have been integrated into PremiumFill® with one objective in mind – providing higher quality to Aptar Pharma’s customers and their patients. This is part of the company’s commitment to improving patient safety while also supporting regulatory compliance. The Ultraclean 6 finishing process, which is an integral part of PremiumFill® is covered by a Type V FDA Drug Master File (DMF) to facilitate the customer’s regulatory filing. Furthermore, since PremiumFill® uses the same rubber formulations, product designs and finishing process as standard products, Aptar Pharma experts have evaluated that switching to PremiumFill® would not require re-approval, making PremiumFill® a quick and easy way to further support compliance with the requirements of Annex 1. PremiumFill® products have demonstrated their benefits in the market for years. Aptar Pharma improves PremiumFill® to guarantee more stringent specifications and higher quality for its customers worldwide.
CASE STUDY: PREMIUMFILL® REDUCED SCRAP LEVELS BY OVER 20% ON A CUSTOMER’S FILLING LINE
By offering higher quality with tighter specifications, PremiumFill® can also help reduce the risk associated with contamination or product defects to improve fill-finish operational efficiency by limiting the risk of rejection on the filling line. This was demonstrated through a case study performed at a customer’s facility.
The pharma manufacturer switched from a standard Aptar Pharma vial stopper to the corresponding PremiumFill® vial stopper. It is important to note that upgrading to PremiumFill® did not require any process adaptation nor additional product filing. As the formulations and designs are strictly identical, the product could be processed as efficiently on existing filling lines.
Over a period of nine months of operation with PremiumFill®, Aptar Pharma’s partner reported a reduction in their scrap rate of over 20%, and there were no quality complaints related to PremiumFill® products. The main defect reductions reported were for fibre contamination and rubber stains, which are both included in the PremiumFill® specifications.
In addition to helping the customer comply with stringent regulatory standards, PremiumFill® demonstrated its efficacy in improving operational efficiency. Significantly reducing scrap levels illustrates the potential for PremiumFill® to reduce the costs linked to product rejects, which, in turn, reduces the total cost of ownership for closure components, while also helping customers meet their sustainability targets.
COMPLEMENTARY SOLUTIONS TO SUPPORT OPERATIONAL EFFICIENCY AND REGULATORY COMPLIANCE
When tackling particulate and biological contamination, the cleanliness of the primary packaging itself is only one of the levers that can be activated, as it only pertains to one of the sources of contamination. Other steps in the fill-finish process may cause external contamination, such as particles coming from the bags that contain the primary packaging, or even from the human intervention when introducing the primary packaging items into the filling line.
Another lever would be to switch from non-sterile ready-to-sterilise (RTS) closures to ready-to-use (RTU) gamma sterilised components. In addition to being the only solution guaranteeing sterility at the time of use, RTU also avoids the use of Tyvek, which has been suggested to be a source of fibres.3 Aptar Pharma RTU solutions use only soldered polyethylene bags, with or without a rapid transfer port (RTP), which helps pharma manufacturers to meet both the sterility assurance requirements and contamination control requirements of the Annex 1 revision. Additionally, using an RTU solution can prove operationally efficient by saving the time, cost and footprint associated with sterilisation equipment and its validation (Figure 3).
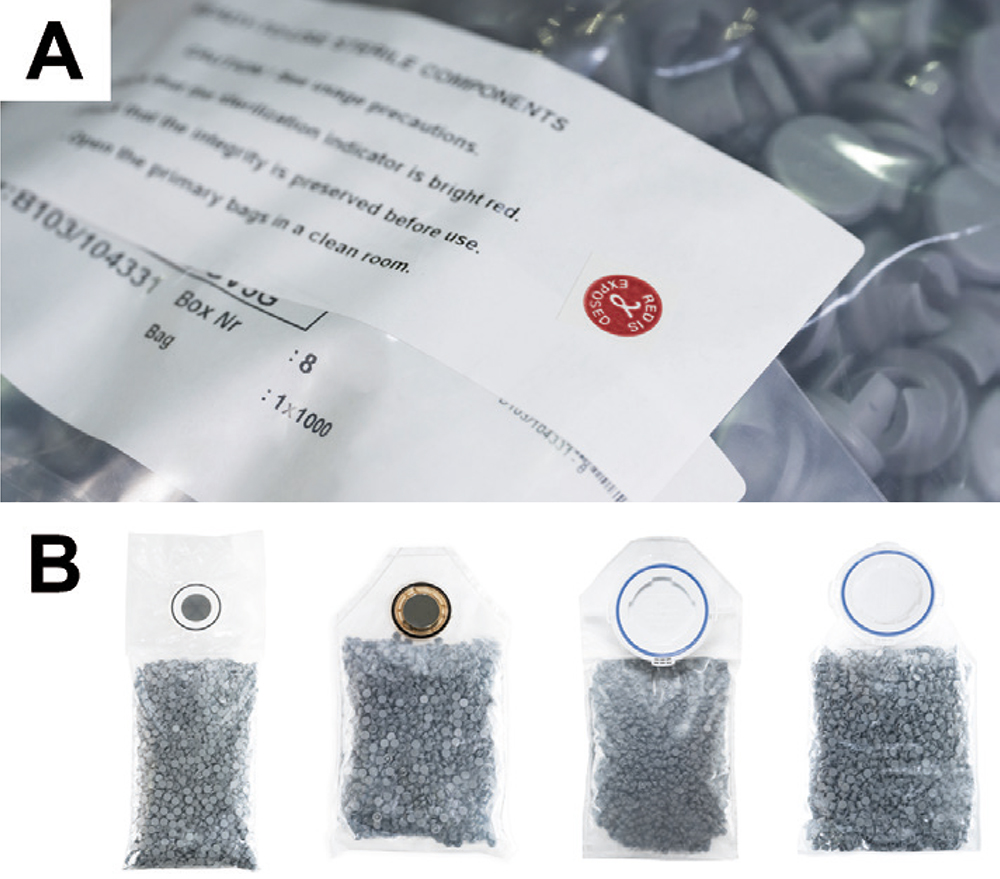
Figure 3: Ready-to-use lyophilisation stoppers in their packaging with irradiation indicator (A). Aptar Pharma vial stoppers and syringe plungers in four RTP bags among the models available (B) .
When primary closure components are introduced on the filling line, there is a risk of biological or particulate contaminants inadvertently entering the restricted environment of the filling line, which could lead to potential issues. To limit the risk of contamination during this step, section 4.18 of the Annex 1 revision strongly recommends the use of isolators or the reduced access barrier system (RABS) in conjunction with RTP bags.
To facilitate Aptar Pharma’s partners’ compliance with the Annex 1 revision on sterility assurance and CCS, Aptar Pharma combines various strategies:
- Limiting the risk of closure component-related particles and defects with PremiumFill® components
- Favouring RTU gamma-sterilised components to guarantee sterility at the time of use and limit the risk of particle generation potentially linked to the use of Tyvek bags
- Selecting RTPs in conjunction with isolators to avoid the accidental introduction of contaminants on the filling line.
In addition, by minimising contamination risks and supporting compliance with the Annex 1 revision, this combination of solutions has the potential to reduce both rejection rates and the operational footprint of the fill-finish operation, promoting efficiency and cost savings on equipment and validation costs.
CONCLUSION
The pharmaceutical sector is undergoing significant changes with the promise of addressing unmet therapeutic needs, but this also brings challenges in packaging and drug delivery due to the sensitive nature of biotech drugs and biosimilars. While ensuring the stability, efficacy and safety of these drugs remains the key priority, accelerating the journey from drug development to market and ensuring a smooth production process are essential for pharma manufacturers to meet their profitability objectives.
Recent regulatory updates, such as the EMA GMP Annex 1, highlight the importance of contamination control and sterility assurance. These regulations place manufacturers under increased scrutiny to meet stringent quality standards, and the importance of partnering with primary packaging experts becomes critical to support the drug development process. Aptar Pharma, staying abreast of the latest trends, adapts its PremiumFill® solutions to align more closely with regulatory requirements and market needs, emphasising its commitment to quality.
To further mitigate contamination risks during the fill-finish process, a comprehensive approach is recommended for ensuring compliance with regulatory standards and optimising operational efficiency. This includes the adoption of RTU gamma-sterilised components to guarantee sterility at the time of use, in conjunction with RTPs to further limit particulate contamination risks.
As the pharmaceutical landscape continues to evolve, manufacturers must prioritise both product quality and operational efficiency. Collaborative efforts with forward-thinking partners, like Aptar Pharma, can provide valuable insights to ensure the highest standards of patient safety, regulatory compliance and rapid time-to-market.
To learn more about Aptar Pharma’s PremiumFill® and PremiumCoat® visit: www.aptar.com/pharmaceutical/deliveryroutes/ injectables.
REFERENCES
- Tawde S, “Particulate Matter in Injectables: Main cause for Recalls”. J Pharmacovigil, 2015, 03, 01.
- “Recalls, Market Withdrawals, & Safety Alerts”. US FDA, 2020.
- Berggren J, Deuthschlet G, “Winning combination: reducing particles in RTU packaging by aligning lid material, adhesive and sealing parameters in a holistic approach.” A3P, Jul 2020.