To Issue 138
Citation: Morgan V, Kurtz E, “Reaching a New Zenith in Protecting Larger-Volume Sensitive Molecules, from Filling To Self-Administration”. ONdrugDelivery, Issue 138 (Oct 2022), pp 34–36.
Victoria Morgan and Eric Kurtz, discuss how West Pharmaceutical Services‘ Daikyo Crystal Zenith™ insert needle prefilled syringe system meets the needs presented by the healthcare sector’s shift to home-based care and the increasing prevalence of biologics in the pharmaceutical pipeline.
In recent years, the healthcare sector has witnessed a sustained shift of treatment location from hospitals to the home, accelerated by the practical difficulties imposed by the covid-19 pandemic. However, even prior to 2020, there were strong market forces at play driving the growth of the self-administration market – patient demand for greater convenience, double-digit growth in specialty and biologic drugs and the value of autoinjectors becoming increasingly recognised across multiple therapy areas.
“Even before the pandemic, patients – particularly older patients − indicated their support for at-home drug administration, with research pointing to an overall preference for avoiding medical facilities and taking their medication at home.”
For some pharma and biotech partners, this opportunity has perhaps been somewhat suppressed by compatibility issues with the available glass primary packaging options, most notably that some sensitive biologic drug formulations become unstable when exposed to silicone oil. Siliconised glass syringes can also pose a risk to the supply chain and the patient due to challenges around aggregation, contamination and breakage.
This article charts the progress of an alternative polymer-based portfolio of vials, syringes and cartridges that have been designed to overcome the challenges posed by glass container systems. It also introduces the latest evolution – a 2.25 mL insert needle syringe system designed to deliver higher volumes. In support, this article presents the results of a customer case study where the polymer-based platform was shown to quickly and safely overcome the challenges posed by the glass alternative.
THE DEMAND FOR HOME-BASED HEALTH
Over the years, much has been written about the shifting focus of healthcare provision and the building of momentum behind home-based health and self-care. The ability for patients to take greater control of their conditions within their own home satisfies many challenges currently facing the traditional model of clinic based care. It not only provides patients with greater autonomy and convenience, but also frees up the valuable time of healthcare professionals (HCPs). It can also help reduce the overall cost to payers – a critical consideration in the context of the increasing pressure that an ageing society is placing on healthcare systems.
Even before the pandemic, patients – particularly older patients − indicated their support for at-home drug administration, with research pointing to an overall preference for avoiding medical facilities and taking their medication at home.1 The influence of covid-19 only served to cement this feeling among patients, at the same time as HCPs sought to maintain limits on unnecessary face-to-face engagement in the interests of treatment efficiency and reducing the spread of infection.
“Potential barriers remain for some biologic formulations where the
material used for their primary packaging is glass.”
Separate studies have shown that the broader area of self-care has the potential to improve outcomes where patients are equipped with the means to self-manage conditions. This is true both in the sense of improving their knowledge of their symptoms and treatments, and in empowering them to self-administer their medicine, advised by an HCP where it is appropriate.2 Typical applications here are for the management of chronic conditions, such as diabetes, or those used to alleviate acute situations, such as anaphylactic shock. Sustained success in these areas has resulted in the emergence of a well-established market for autoinjectors, delivering therapies at a frequency and volume that is readily acceptable and manageable for patients.
Against this backdrop, innovators in the pharmaceutical and biotechnology sectors have continued to explore new areas where autoinjectors have potential, aiming to support increasing cohorts of patients with the ability to effectively self administer their medication. One such example is the expansion of the potential drug volume delivered via autoinjectors from the typical dose of 1 mL up to 2.25 mL and even 5 mL.
THE NEEDS OF BIOLOGICS
This development has been driven by various factors, one of which is the growth in demand for biologic formulations, which often require higher volumes to deliver the desired effect. Another is the emergence of results from human factors studies that have demonstrated patient tolerance for injection durations of up to 15 seconds, a notable increase from the previously accepted threshold of 10 seconds. The combination of these two factors opens the door to self administration of a wider range of biologic therapies via subcutaneous injection for applications that would previously have required multiple injections or intravenous delivery within a clinical setting.
These developments hold significant promise for further advances in the field of self-administered care. However, potential barriers remain for some biologic formulations where the material used for their primary packaging is glass. Here, the siliconisation process coats the glass barrel within the prefilled syringe (PFS) container system with silicone oil so that the desired gliding forces are achieved when the plunger is deployed. While the presence of silicone oil is not typically a cause for concern, in the case of some sensitive biologics it can be the catalyst behind protein aggregation. These elements can lead to diminished efficacy and safety in the delivered dose.3
DAIKYO CRYSTAL ZENITH®
For biotech companies, the question in these circumstances is how to protect the integrity of a larger-volume, highly sensitive, and highly valuable biologic formulation in a non-glass-based container without compromising the cleanliness and robustness required of the primary packaging.
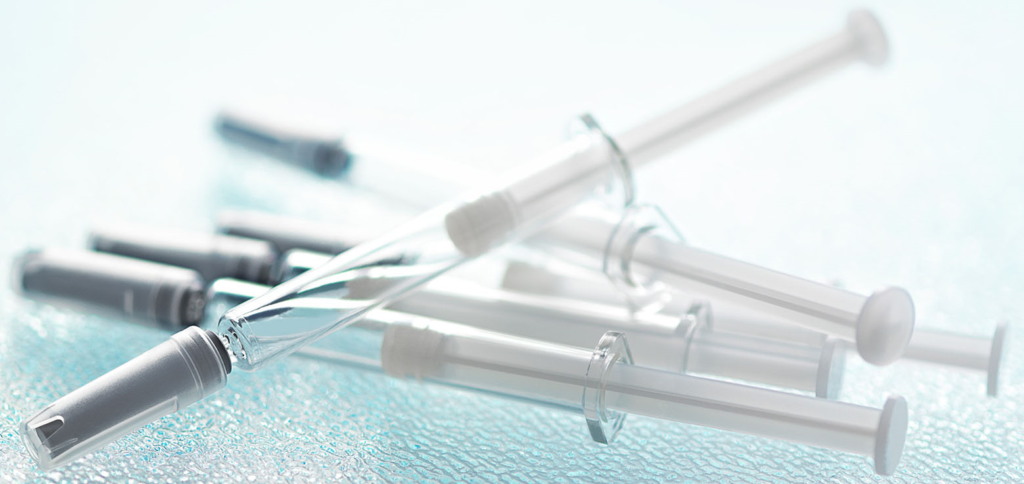
Figure 1: Daikyo Crystal Zenith® insert needle syringe system.
“The results found the drug to be stable within the CZ system, which outperformed glass and alternative polymer-based systems for sub-visible particles.”
An alternative to siliconised glass can be found in the Daikyo Crystal Zenith® (CZ) component portfolio from West, which includes a 2.25 mL insert needle (IN) PFS system (Figure 1). CZ is a cyclic-olefin polymer that presents a sterile containment system for silicone oil-sensitive drug formulations. The elastomeric plunger used in the CZ PFS system is coated with an inert FluroTec® barrier film, which reduces the risk of leachables from the elastomer and prevents absorption of the formulation. By supporting syringe functionality, the film also avoids the need for additional silicone oil to be used, dramatically reducing exposure to the key source of protein aggregation. Indeed, studies conducted by West on a randomised selection of syringe samples detected no silicone oil down to 1 ppm extracted from the assembled CZ PFS.
In further evidence of CZ’s credentials for safeguarding formulation integrity, the precision injection-moulding process used to engineer CZ polymer syringes facilitates a 4-log reduction in endotoxin levels while also enabling needles to be attached free of tungsten or glue, which are additional possible sources of drug contamination. Break-test data recorded during tests carried out by West also demonstrate how CZ mitigates against the risk of breakage. This is not only an important consideration in relation to the fill-finish process, where breakages result in costly downtime, but also in transportation environments and for the activation of the autoinjector itself, where higher forces can be required to deliver large-volume or high-viscosity injections.
REAL-WORLD CASE STUDY
In the case of one pharmaceutical customer, the benefits of the materials science incorporated within CZ helped resolve an acute packaging challenge that caused costly delays to the development schedule for a drug used within an autoinjector application. Here, the customer employed a platform approach to packaging, with the formulation development team opting to contain a new biologic within a previously used large-volume glass syringe system.
In analytical tests to assess the stability of the formulation, the results provided a clear indication of the drug’s sensitivity to the silicone present within the “default” glass containment option. This was the cause of poor stability over time, with silicone particles and protein aggregation both present within the drug product after a period in storage.
Having lost critical time early in drug development, the customer was prompted to seek out an alternative primary containment solution that would avoid the risk of protein aggregation through exposure to unacceptable levels of silicone oil. The solution also had to demonstrate physical properties that answered the demands of an autoinjector use-case, which incorporated not only container closure integrity (CCI) and breakage resistance, but also the ability to operate within specific tolerances for break loose, extrusion and gliding forces, injection force and rigid needle shield removal force.
Having identified the potential of the CZ 2.25 mL IN PFS system, the customer conducted a series of tests to verify the performance of the system in accordance with these demands. The results found the drug to be stable within the CZ system, which outperformed glass and alternative polymer-based systems for sub-visible particles. The CZ system also conformed to USP <1207> for CCI testing; the forces registered were within the defined tolerance range, and no syringe breakage was exhibited.
This case study highlights the potential for materials such as CZ to be deployed in biologic applications where there are potential silicone interaction risks that can negatively influence development schedules, increase costs and delay time-to-market. At a more fundamental level, it underlines that, while the continued innovation in biologics is opening up new treatment pathways for patients, the complex nature of these formulations, in terms of volume and physicochemical properties, requires continued innovation in containment solutions to ensure the delivered dose will achieve the desired effect.
CONCLUSION
As has been discussed, there is evidence that the paradigm of the relationship between patients and HCPs is continuing to shift. This does not diminish the essential advice, guidance and education provided by trained HCPs, but it does mean that devices such as autoinjectors must continue to evolve to meet the highest levels in performance, drug integrity and safety if, more frequently, the person administering the medication is expected to be the patient and the point of delivery increasingly closer to home.
FluroTec® is a registered trademark of West Pharmaceutical Services, Inc. in the United States and other jurisdictions. Crystal Zenith® is a registered trademark of Daikyo Seiko, Ltd. FluroTec and Crystal Zenith technologies are licensed from Daikyo Seiko, Ltd.
REFERENCES
- Landers S et al, “The Future of Home Health Care”. Home Health Care Manag Pract, 2016, 28(4), pp 262–278.
- Anderson AH, Martin LA, Mate KS, “The Value of Teaching Patients to Administer Their Own Care”. Harvard Business Review, Jun 2017.
- Gerhardt A et al, “Protein Aggregation and Particle Formation in Prefilled Glass Syringes”. J Pharm Sci, 2014, Vol 103(6), pp 1601–1612.