To Issue 138
Citation: Barichello E, “Realising Reductions in Dead Volumes Within Prefilled Syringes: a Manufacturer’s Perspective”. ONdrugDelivery, Issue 138 (Oct 2022), pp 83–86.
Enrico Barichello considers the benefits of prefilled syringes, including cost and waste reduction, and looks at the impact and challenges of dead volume within the syringe.
“Precision and efficiency are important factors in any manufacturing process but, in the case of pharma, they are absolutely critical for the production of therapies that offer both the maximum patient benefit and the minimum risk of adverse effects.”
As the pharmaceutical industry continues to witness the expediential growth in the development of biologics and biotech drugs, so it also uncovers new challenges.
One area for consideration is the effective delivery of the target volume of these drugs to ensure that the patient receives the optimum dose. As a result, there is currently a very strong focus among pharma partners on understanding the levels of wastage associated with the various container types available. This is particularly pertinent in the delivery of ophthalmic medicines, where the drug volumes delivered are especially low.
This article will first consider the key benefits prefilled syringes (PFSs) bring to the entire healthcare ecosystem in comparison with vials, including those of cost and waste reduction. It will then address the challenge of dead volume – a key concern when dealing with more expensive and low-volume drugs. The measures in place today to mitigate wastage will be reviewed and the results of an internal study by Stevanato Group to assess how the morphology of the glass cone impacts dead volume will be presented.
The findings were delivered by the Technology Excellence Centers (TEC) – an analytical and device testing service that supports development journeys from early-stage concepts to launched combination products. The results were then represented in one of the Stevanato Group primary packaging product lines, SG Alba®, which, with an improved dead volume performance, represents a breakthrough solution for biologics.
Precision and efficiency are important factors in any manufacturing process but, in the case of pharma, they are absolutely critical for the production of therapies that offer both the maximum patient benefit and the minimum risk of adverse effects.
OVERCOMING THE CHALLENGES OF INEFFICIENCY AND WASTE
For certain aspects of the manufacturing process, inefficiency and wastage remain a challenge. Vials, for example, might represent the preferred option for primary packaging as a proportion of the overall market, but they do have some shortcomings in terms of potential drug wastage.
As a container of multiple doses, it is not always possible for the entire contents of a vial to be deployed in full. This leads to situations where residual content must be discarded because the drug has not been used in time or stored in appropriate ambient conditions, compromising the efficacy and safety of the dose.
The same cannot be said for PFSs. This injection format simplifies and accelerates administration by presenting healthcare professionals (HCPs) with a prepared dose, avoiding the intermediary stage of filling the syringe from a vial and therefore minimising drug wastage. With continued improvements to fill-finish capabilities and production capacity, PFSs have grown in importance as an alternative containment strategy to vials. The use of PFSs allows for potentially significant volumes of a drug to be saved over time when the individual instances of drug wastage are multiplied by the number of vials produced at commercial scale. The cost of this waste can be felt particularly keenly in the case of biologics, which represent an increasing share of the landscape and typically carry a high cost-per-dose.
The advantageous combination of high dosing accuracy and low waste, while relevant to all injections, is particularly appealing for therapeutic areas such as ophthalmology. Here, PFSs support the typical profile for parenteral administration, which involves very low and highly specific volumes of valuable, sensitive biologics, with the concern that any variation in the dose will increase the risk of adverse effects.
MANUFACTURING PROCESSES ENSURE CORRECT DOSE VOLUME
While responsibility for priming the PFS and administering the dose rests with the HCP, successfully delivering an accurate dose in this situation is predicated on highly consistent manufacturing processes that ensure that the volume of drug within the PFS is consistent, precise and accurately reflects the expected dose volume indicated by a marker. Of particular importance is the cone element at the shoulder of the glass syringe, as inconsistencies in the morphology of the cone can result in variations in the internal volume, which has implications for dosing accuracy and drug wastage.
The cone is formed in a process that involves the external surface of the glass tube being heated and cooled multiple times. While the external dimensions of the cone conform to the exact specification set out in a reference technical drawing, and as defined by the ISO 11040-4 quality standard, the internal dimensions of the cone do not necessarily conform to a consistent geometry.
The cone’s internal dimensions will therefore define the extent of a “dead volume” within the syringe. This is the space that contains the residual drug from a single dose after the plunger stopper reaches its maximum point of travel at the shoulder of the syringe. The greater the dead volume, the higher the level of drug wastage and the greater the level of inconsistency in the delivered dose.
“With continued improvements to fill-finish capabilities and production capacity, PFSs have grown in importance as an alternative containment strategy to vials.”
ANALYSIS OF THE INTERNAL SHAPE OF THE GLASS AND DOSE CONSISTENCY
Stevanato Group, having acknowledged the cost and risk concerns associated with dead volume, set about understanding this issue in greater detail. Employing the capabilities of the TEC, Stevanato’s analytical and device testing service, the company undertook two tests to analyse firstly the impact that the internal shape of the glass cone has on the observed dead volume, and secondly the consistency of delivered doses across batches of syringes printed with a dose marker.
The first test involved measuring and modelling the internal profile of the syringe’s dead volume, which is made up of the space within both the cone at the shoulder and the cylinder up to the syringe’s tip. A total of five 1 mL STD Luer lock syringes with ITC-West 4023 plungers were assessed using a profile projector at a magnitude of 10x and with a sensitivity of 1 μm. For each syringe, the diameter was measured at seven different distances from the tip, and the results were fed into computer-aided design (CAD) software to create 2D and 3D renderings of the average syringe, including data on the internal volume.
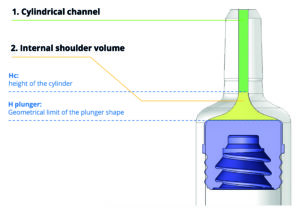
Figure 1: The cone and the shoulder design is a key element to reaching dose accuracy.
The profile projector, which is normally used when processing dimensional controls for bulk products, works by immersing the item to be measured in silicone fluid. Because it has the same refraction rate as air, this allows the item to be observed extremely closely and highly accurate geometric measurements to be taken.
Two of the diameter measurements were critical in calculating the volume of the internal cone: the first – cylinder height diameter (Hc) – is defined as the point furthest from the tip at which the internal channel shape can still be considered a cylinder; the second – plunger height diameter (Hplunger) – reflects the internal diameter of the 4023-plunger stopper’s furthest position at the shoulder of the syringe (Figure 1).
Equipped with these diameter measurements and the distance from the tip at which they were measured, it was possible to separate the total internal dead volume into two parts – the cylindrical channel and the internal shoulder volume. This analysis revealed that from a total dead volume of 41.11 μL, the internal shoulder volume contributed the significant majority – 32.17 μL (78.3%) – with the remainder – 8.94 μL (21.7%) – being made up of the cylindrical channel (Figure 2).
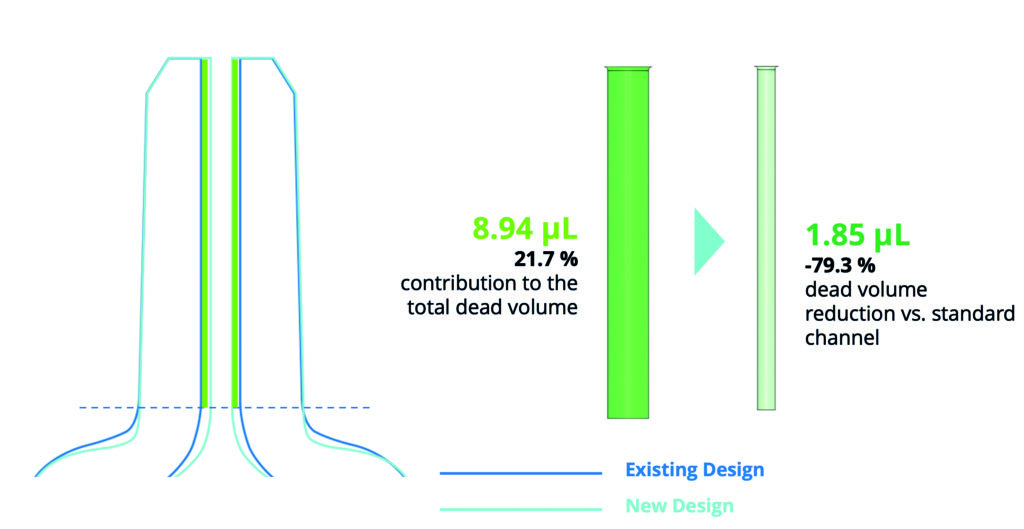
Figure 2: Dead volume reduction by optimising the internal cone design.
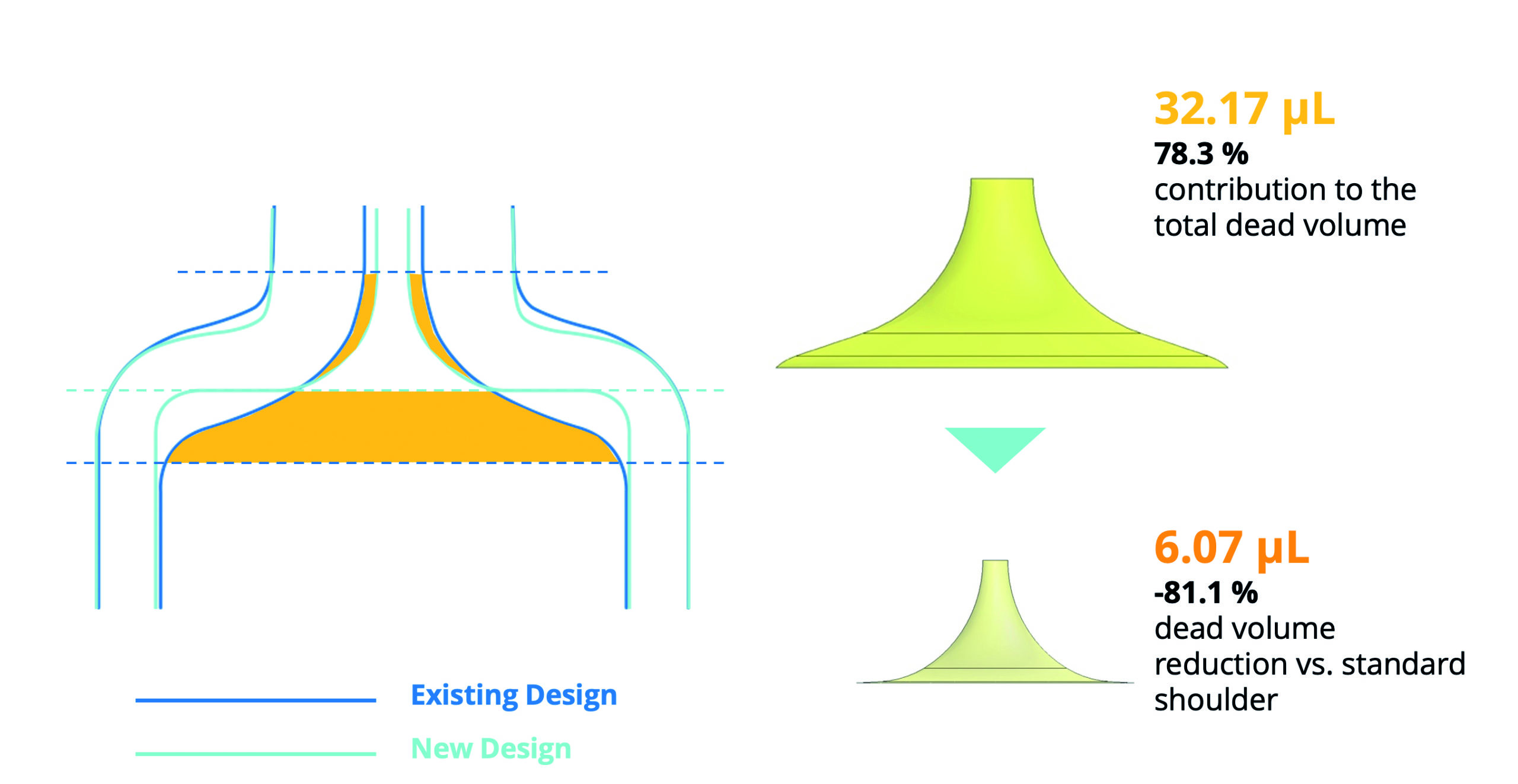
Figure 3: Dead volume reduction by optimising the internal shoulder design.
Close analysis of the cylinder revealed its compliance with the product’s reference technical drawing, confirming a diameter of 1.1 mm. The CAD software then provided an opportunity to manipulate the cylinder diameter in a virtual environment and to measure the impact of any change on the cylindric dead volume. This analysis revealed that a 0.5 mm reduction in diameter would result in the cylindrical dead volume being reduced by 79.3% from the original measurement of 8.94 μL down to 1.85 μL.
In terms of the cone area, the test results highlighted how adjustment to the PFS design would present an opportunity for a reduction in the dead volume observed within the internal shoulder area. The dominant limiting factor here is the lack of geometric correlation between the profile of the plunger stopper and the PFS shoulder. Essentially, the tapering of the cone towards the cylinder means that the plunger stopper is limited in the distance it can travel into the shoulder, creating more dead volume.
This finding paved the way for design changes to the internal geometry of the SG Alba® syringe, resulting in a more squared shoulder profile that better corresponds to the plunger stopper profile without compromising on the product’s physical strength. In tests, this new design resulted in a reduction in the dead volume of 81.1% compared with the standard shoulder design, with the volume measured to be 6.07 μL, compared with the original volume measurement of 32.17 μL (Figure 3).
The TEC is planning to augment this study by exploring the impact of a variety of factors in greater detail. This includes an assessment of the behaviour of the plunger stopper, including its elastic movement into the dead volume shoulder area during the last phase of drug extrusion, and any potential variance in behaviour resulting from different rubber formulations or coatings. Modelling of the needle hub also has the potential to reveal factors that influence the overall dead volume. This all underlines further the importance of multi-stakeholder collaboration to secure continued reductions in dead volume.
ANALYSIS OF DOSE PRECISION
In the second of the tests carried out by the TEC, the accuracy of the dose mark printed on the SG Alba® syringe and its influence on dose precision were analysed. This reference point is critical to healthcare professionals in the priming phase, identifying the point to which the plunger should be advanced in the syringe channel prior to injection. Therefore, inconsistency in the dose mark position has the potential to result in the final dose diverging from the desired volume.
The test was designed to evaluate the dose accuracy and dead volume performance of 0.5 mL Luer lock cone syringes serigraphed with a 50 μL dose mark. Samples were drawn from three separate syringe batches to assess the potential for variability.
In the tests, conducted at room temperature, each syringe was manually filled with 150 μL of Milli-Q water using a calibrated pipette. Following a 24-hour storage period, the sample was primed and any air bubbles dislodged before the plunger was gently advanced to the dose mark. The dose was then automatically extruded using a universal tensile machine, which collected the removed liquid. The syringe components, collection components and samples were all weighed pre- and post-test to allow the dose and residual dead volumes to be calculated.
The results recorded the average extruded dose for the three sample batches at 49, 50 and 51 μL, with a standard deviation across the samples of 2–3 μL. They also highlighted that, while there was a degree of variability, the extruded doses were closely aligned to the 50 μL target dose. In the case of dead volumes, each sample batch registered an average of 7 μL with a standard deviation of 1 μL, showing the high degree of consistency in dead volume levels across all samples (Figures 4 and 5).
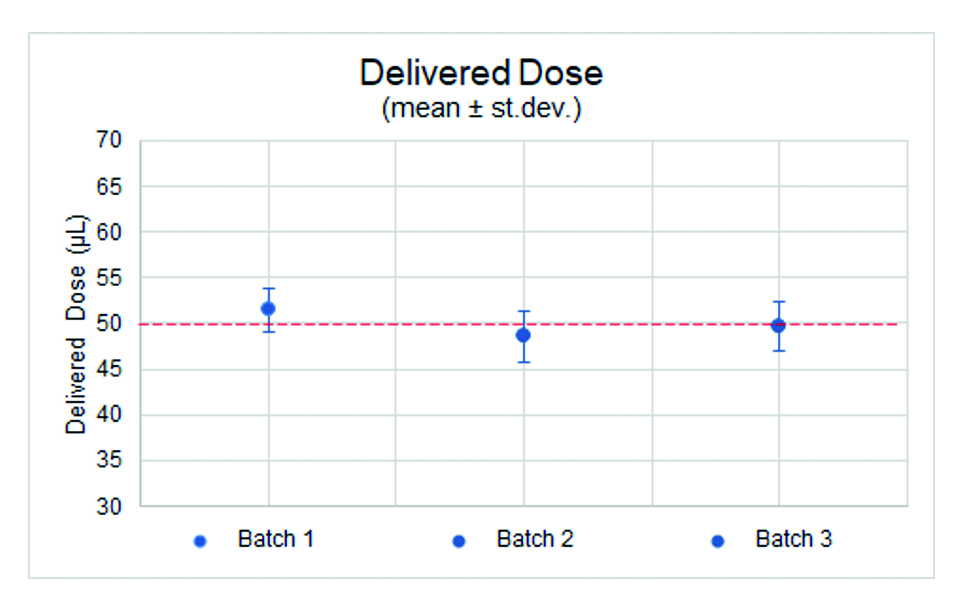
Figure 4: High degree of consistency of the delivered dose across three batches.
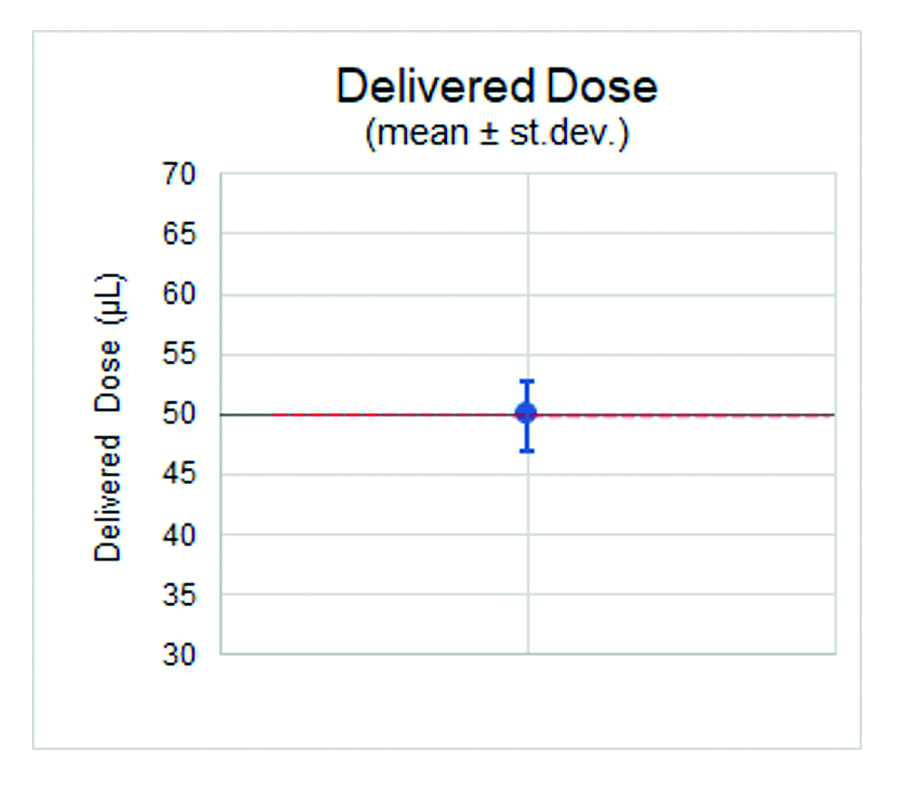
Figure 5: The extruded doses closely aligned to the 50 μL target dose.
The findings of both tests provide a clear indication of the role of dead volume in PFSs and how product design and manufacturing accuracy are crucial in limiting this element to deliver repeated accurate doses. This is particularly beneficial in ophthalmic applications, where the physical design of the SG Alba® syringe protects against unnecessary wastage of high-value biologics. At the same time, SG Alba® ensures the integrity of these sensitive drugs is protected against silicone migration through the inclusion of a proprietary internal coating, which forms a chemical bond with the glass surface to promote stability.
It is the combination of all these factors that supports the needs of patients requiring low-volume doses administered in precise quantities. To arrive at this point, it is critical to acknowledge, analyse and understand the exact nature of possible variations and inconsistencies so that they can be addressed through continued innovation and improvement.
SG Alba® is a registered trademark of Stevanato Group and/or its affiliates in one or more jurisdictions.