To Issue 142
Citation: Swift J, “The Operations Perspective: Best Practices from 70 Years in Injection Device Manufacturing”. ONdrugDelivery, Issue 142 (Feb 2023), pp 28–30.
John Swift looks at how Owen Mumford has evolved over 70 years, discusses the company’s latest disposable autoinjector, Aidaptus, and considers how it plans to reduce risk in its supply chain.
In 2022, as Owen Mumford celebrated its 70th birthday, the business reflected on its growth from a small, family-run business in Woodstock, near Oxford (UK), to a global medical device innovator. The industry has evolved dramatically during this period. Since the company pioneered the world’s first plastic autoinjector (Autoject) in 1986,1 the market for injection devices has grown, while welcoming increasingly sophisticated products.
“Risk management begins at the design phase when deciding on manufacturing and assembly processes – both manual and automated.”
It is expected that, in 2023 alone, the global injectable drug delivery devices market – comprising conventional injections, prefilled syringes, autoinjectors and pen-injectors – will grow by 9.0%, reaching a value of $43.54 billion (£35.8 billion).2 During the same period, the global autoinjectors market is expected to expand at an even higher rate, 21.4%, reaching a valuation of $23.9 billion.3 With 60% of drugs in the R&D pipeline designed for injectable delivery and a growing number of those for subcutaneous administration, it is likely that the industry will continue to see sustained growth in the coming years.4
With demand high and patients increasingly administering their own medication wherever possible, manufacturers of drug delivery devices must be able to keep up – reliably providing the required volumes, and meeting quality and regulatory standards while continuing to innovate.
SECURING SUPPLY RESILIENCE
A key aim of Owen Mumford’s operations plan is to secure supply resilience, even while development programmes for other products are ongoing. Over the years, Owen Mumford’s operations team has developed best practices to support product launches and growth, ensuring device excellence and optimally managing risk during industrialisation and capacity scale-up.
Risk management begins at the design phase when deciding on manufacturing and assembly processes – both manual and automated. Simplicity is paramount since it inherently reduces risk, but if there are residual risks during manufacturing, the company’s process failure mode effects analysis (PFMEA) tracks and mitigates these. The team proactively assesses updates on a risk register to track changes and their potential impact and the likelihood of risks impacting project delivery timescales. This allows the team to take corrective action swiftly when needed, to manage risk appropriately and ensure continuity of supply.
Alongside this, Owen Mumford has a specific initiative to monitor supply chain vulnerability. Brexit and the global pandemic highlighted risk areas that needed addressing to protect continuity of supply, prompting this new initiative, which supports ongoing supplier management. The company has developed a “virtual factory management” concept, with key performance indicators that enable early detection of vulnerabilities caused by key suppliers’ performance, capability or strategies. To manage suppliers effectively, the company has made sure there are clear roles, responsibilities and governance, an optimal meeting cadence, triggers and escalation procedures. The teams audit and work alongside suppliers, making it easier to check that appropriate systems, equipment, methods and skill sets are in place to deliver to the agreed level of quality.
With so many factors to monitor for supply security, the creation of centres of excellence is invaluable so that each focuses on a particular area of operations, whether this is moulding, assembly, automation or another key function. The company’s approach is to clearly define the skills and tools needed for each individual centre and then create a focused training programme that allows staff to learn continually and upskill. This, in turn, supports staff retention, contributing to a reduced risk profile. Through dedicated centres of excellence, operations teams can develop and implement best practices across all key areas and employ individuals with a variety of backgrounds and experience levels. In fact, they can support risk management in multiple ways, through improved planning and awareness of potential issues or by providing key skill and competency coverage in times of planned or unplanned leave.
Owen Mumford’s upcoming new production facility in Oxfordshire, UK, will become a centre of excellence for automation and assembly, manufacturing the company’s latest medical devices and supporting its global commercial and sustainability strategy. The building itself is designed with excellence in mind and will be certified by the Building Research Establishment Environmental Assessment Method, the world’s leading sustainability assessment method. This certification recognises the highest levels of environmental, social and economic sustainability performance, not only protecting natural resources during the building process but also enhancing the wellbeing of associates who will be located there.
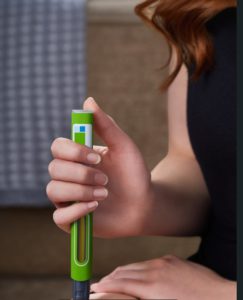
Figure 1: The Aidaptus disposable autoinjector has many of the proven user features of other market-leading autoinjectors but also features novel technologies.
INNOVATION, INNOVATION, INNOVATION
While continuing to provide its existing products, Owen Mumford is constantly looking ahead and designing new devices, always with the aim of improving the patient experience while maintaining ease of use. Its latest innovation, the Aidaptus disposable autoinjector, has many of the proven user features of other market-leading autoinjectors but also features novel technologies (Figure 1). These technologies help provide flexibility for pharmaceutical companies during their drug development and lifecycle management.
As well as accommodating both 1 and 2.25 mL syringes in the base form, Aidaptus’s novel auto-adjust plunger technology can dynamically adjust to different fill volumes with no change parts. The plunger automatically adjusts to the required stopper position during final assembly of the device with no requirement for special equipment. Essentially, this means that the same device can be used irrespective of formulation changes. This has advantages in reducing work such as additional verification testing, human factors studies and regulatory documentation. Therefore, it can help to reduce risk for the company’s pharma partners as well as reduce time to market in combination product development.
For Aidaptus, Owen Mumford has chosen to collaborate with Stevanato Group with the aim that the combined resources, expertise and manufacturing capabilities of both companies will help to reduce complexity, minimise supply-chain risk and simplify final assembly for pharma customers. Both parties are currently making investments in building the capacity for Aidaptus scale-up, and equipment will be installed at both companies’ production sites. For Owen Mumford, the new assembly equipment will be installed at its new state-of-the-art facility in the UK, which is due for completion in 2023 (Figure 2). This approach to dual sourcing options is another example of how the company is actively planning to reduce risk in its supply chain.
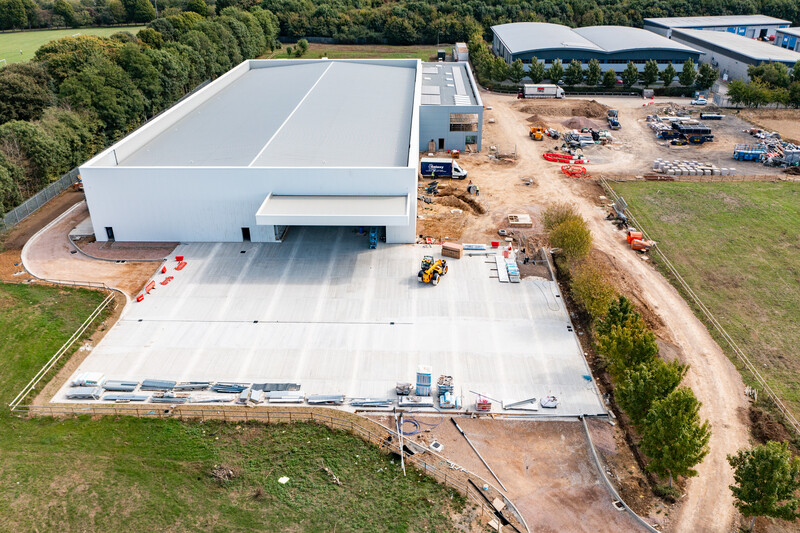
Figure 2: For Owen Mumford, the new assembly equipment will be installed at its new state-of-the-art facility in the UK, which is due for completion in 2023.
REFERENCES
- “Auto-injectors for intramuscular and subcutaneous administration”. Company Web Page, Owen Mumford. (https://www.owenmumford.com/en/drug-delivery/auto-injectors, accessed Jan 2023.)
- “Injectable Drug Delivery Devices Global Market Report 2023 – By Type (Conventional Injectable, Pre-Filled Syringes, Auto-Injectors, Pen-Injectors), By Application (Autoimmune Diseases, Hormonal Disorders, Oncology, Orphan Diseases, Pain Management, Respiratory Therapy, Other Applications), By End User (Hospitals And Clinics, Home Healthcare Settings, Pharmaceutical And Biotechnological Companies, Research Laboratories, Other End Users) – Market Size, Trends, And Market Forecast 2023-2032”. Research Report, The Business Research Company, Jan 2023.
- “Auto-Injectors Market Outlook (2022-2032)”. Research Report, Future Market Insights, Sep 2022.
- “Percentage of drugs in R&D pipeline worldwide by delivery route as of 2022”. Research Report, Statista, May 2022.