To Issue 168
Citation: Thiesson I, Sander J, “Tub & Nest – Precision and Efficiency in Drug Delivery”. ONdrugDelivery, Issue 168 (Jan 2025), pp 112–114.
Ivana Thiesson and Jörg Sander discuss the benefits of Fischer Söhne’s “Tub & Nest” format for packaging prefilled syringes, including design flexibility and precise cleanroom manufacturing.
Fischer Söhne, a Swiss plastics specialist with over 100 years of experience, is widely known for its innovative solutions in the life science market. The company’s “Tub & Nest” system is a prime example of its commitment to precision and efficiency in drug delivery. Designed to address the growing demand for prefilled syringes (PFSs), Tub & Nest offers a streamlined approach to aseptic handling, ensuring the sterility and integrity of injectable therapies. According to Iwan Tresch, Chief Executive Officer of Fischer Söhne, “Fischer Söhne’s rebranding marks a new era for our company. With over 100 years of expertise, we’re focused on the future of life sciences and committed to delivering innovative solutions for the life science industry.”
THE RISE OF PREFILLED SYRINGES
PFSs are rapidly gaining popularity due to their advantages for precise dosing, ease of use and reduced risk of contamination. However, these advancements require sophisticated packaging solutions to maintain product integrity throughout the supply chain (Figure 1). Fischer Söhne’s Tub & Nest system directly addresses these challenges.
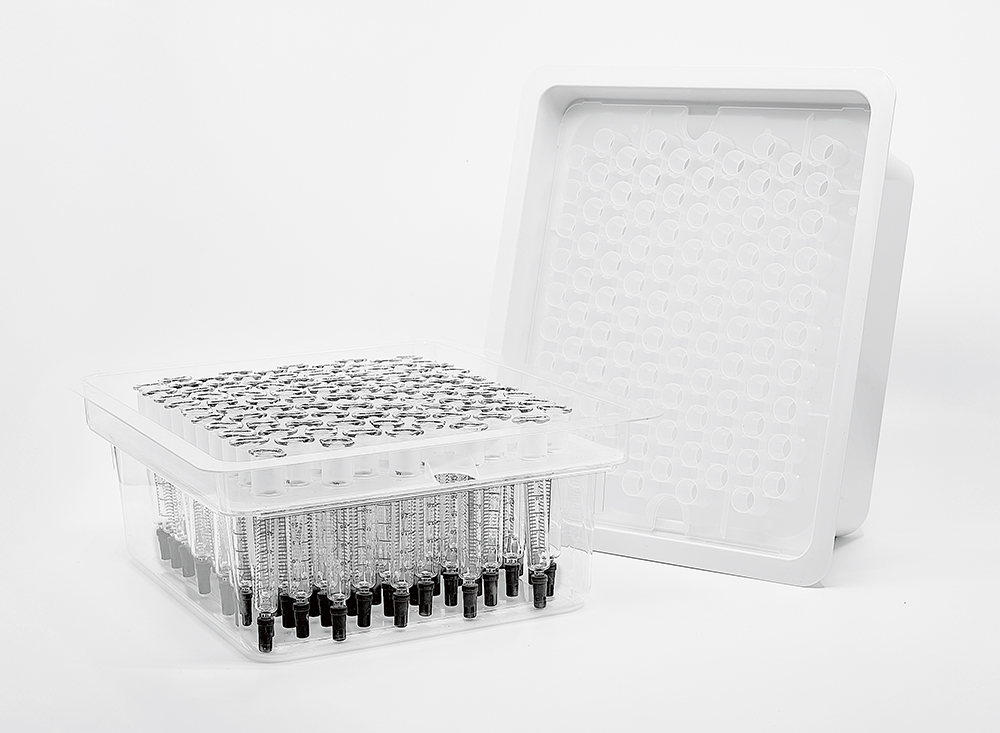
Figure 1: Tubs and nests for medical syringes.
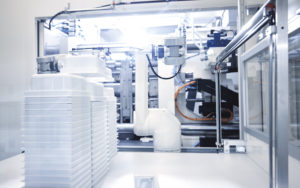
Figure 2: Cleanroom production facility.
Tub & Nest: A Comprehensive Solution
The Tub & Nest system simplifies the aseptic handling of PFSs while ensuring their sterility and integrity. By offering a packaging system that seamlessly integrates into automated processes, Fischer Söhne supports the industry’s move toward more efficient injectable solutions.
TECHNICAL CAPABILITIES AND CLEANROOM STANDARDS
Fischer Söhne’s state-of-the-art cleanroom production facilities are ISO 13485 certified, ensuring top-tier quality (Figure 2). Fischer Söhne operates injection moulding machines with clamping forces of up to 500 tons, enabling efficient multi-cavity moulding and manufacturing of both standard and customised packaging solutions. This versatility allows for handling complex projects, such as syringe plungers ranging from 0.5–50 mL, and both customised and standard Tub & Nest configurations (Figure 3).
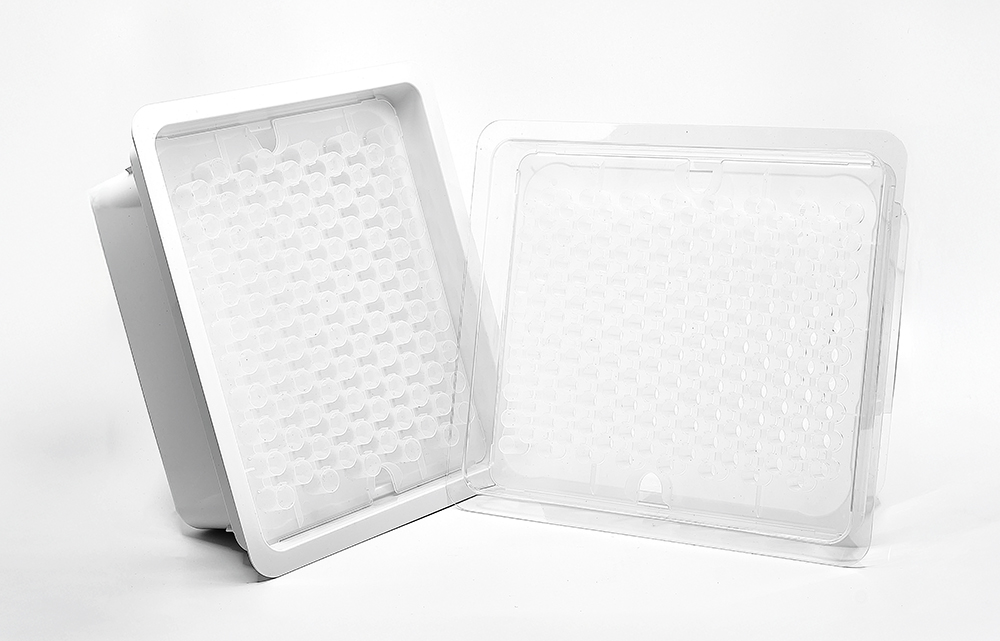
Figure 3: Standard Fischer Söhne Tub & Nest configuration.
Unmatched Precision and Cleanroom Manufacturing
Fischer Söhne’s Tub & Nest products are manufactured under strict GMP Class C (ISO 7) cleanroom conditions (Figure 4), ensuring the highest standards of cleanliness and reliability. Their low-particle, scratch free and unbreakable design provides exceptional protection for sensitive pharmaceutical products, such as PFSs. In the initial phase, the tubs and nests are equipped with glass or polymer syringes in a highly automated process, then sealed and sterilised. Once sterilised, these filled tubs and nests are delivered to pharmaceutical companies or their contract fillers.
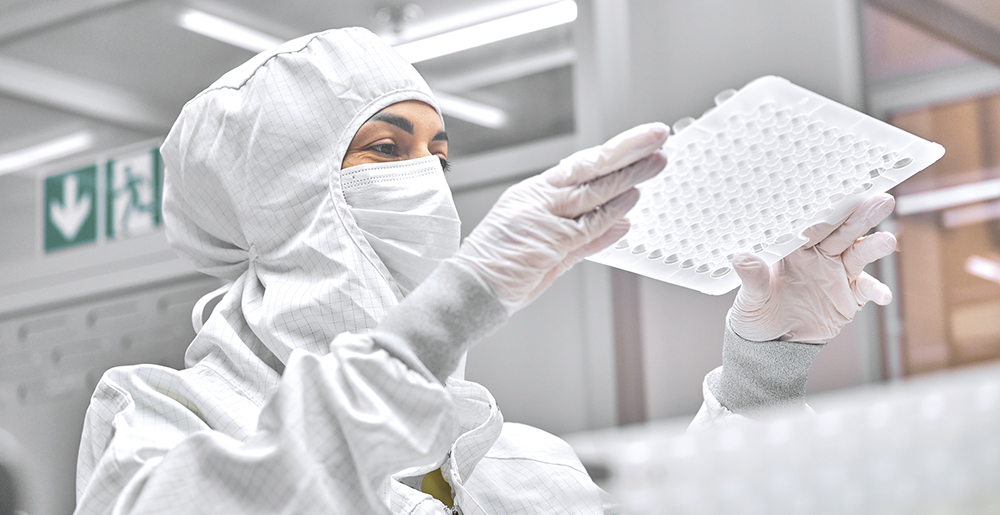
Figure 4: Nest during cleanroom production.
When delivered to their destination, the tubs and nests can be opened under sterile conditions and the syringes filled with the intended drugs. These packaging solutions are directly integrated into customer pick-and-place machines, allowing for sterile filling and aseptic packaging processes. To further enhance quality, Fischer Söhne uses advanced polymer materials like polypropylene and polystyrene, which are highly durable and compatible with various sterilisation methods.
EXCELLENT DIMENSIONAL STABILITY
The Tub & Nest system reduces the risk of glass breakage, particle contamination and scratch marks during production. This precision facilitates smoother operations, enhances the processing speed of automated systems and maximises overall efficiency and output. The system’s innovative design ensures that syringes remain securely in place during transportation, preventing damage or misalignment. Additionally, Fischer Söhne collaborates closely with its clients to optimise the dimensional stability of its Tub & Nest products for specific syringe formats. This ensures seamless integration into existing processes and equipment, minimising downtime and operational costs.
Flexible and Certified Solutions
Available as standard items with short delivery times, Fischer Söhne’s Tub & Nest products are compatible with common filling and loading systems, making them versatile and cost-effective. Certified according to ISO 13485 and designed in adherence to ISO 11040-7 standards, these solutions ensure unparalleled quality and reliability while complying with GMP requirements. Iwan Tresch added, “Our cleanroom production runs around the clock. That’s why we are always ready to deliver, for smaller and also for very large quantities.”
PARTNERING FOR SUCCESS
Fischer Söhne’s customer-centric approach goes beyond delivering high-quality products. The company’s technical team works closely with clients to provide tailored solutions, from initial concept development to production and delivery. Offering both standard Tub & Nest systems with short delivery times and the ability to develop customer-specific nests, Fischer Söhne ensures flexible solutions that meet individual requirements.
The company’s expertise extends to designing entire systems, including trays and lids, delivering versatile, cost effective products that are compatible with common filling and loading systems. By leveraging decades of experience and a deep understanding of industry trends, Fischer Söhne empowers its partners to stay ahead in a competitive market.
CONCLUSION
With its Tub & Nest solutions, Fischer Söhne demonstrates its commitment to innovation, quality and sustainability in the pharmaceutical packaging sector. As the market for PFSs and injection devices continues to grow, the company remains a trusted partner for pharmaceutical manufacturers worldwide. Fischer Söhne’s unique combination of advanced technology, customer focus and environmental responsibility positions it as a leader in life science packaging solutions.