To Issue 168
Citation: Abaroa Martinez R, Pircher D, “Unlock Value: Key Cost Drivers in Spring and Stamping Design”. ONdrugDelivery, Issue 168 (Jan 2025), pp 106–110.
Rolando Abaroa Martinez and David Pircher highlight how a metal parts supplier can help to optimise costs – not only for springs and stampings but also in later production stages of a medical device. With a focus on the design phase, they emphasise that not only the costs associated with the metal product but also the total costs can be managed effectively with the right support from experts.
Medical device design is a complex and highly regulated field. BAUMANN MEDICAL’s value chain begins with the initial customer contact, where foundational ideas and design concepts are discussed collaboratively. This progresses to decisions regarding which types of springs and materials are suitable, followed by process design and series production. The goal is to enhance value creation sustainably.
Partnering with experienced designers can help involved parties to not only develop a successful product but also manage total costs effectively. For example, a spring that contributes to high overall equipment effectiveness (OEE) on the assembly line without issues may result in a much better total cost balance, even if its initial product price is slightly higher.
BAUMANN MEDICAL aims to collaborate, where feasible, in the earliest possible development phase of a new device. It is scientifically proven – using the analogy of project management – that good planning at the beginning of a project can lead not only to success but also to significant cost savings in the development process.
This applies to most situations, whether a new platform is being developed by a design-consulting company, a specific device is being created with a pharma company or replacement products for existing devices are in development. In every design project, everything begins with thorough preparation: the clearer the strategy is at the outset, the smoother implementation will be.
BAUMANN MEDICAL frequently encounters two scenarios: 1) customers either present the company with a finished design for a new product or seek to replicate an existing one or 2) they approach the company at the initial stages of the development process for expert support. These situations significantly impact product costs. In the first scenario, opportunities for optimisation are limited, whereas the second offers substantial potential for cost reductions – sometimes up to 70% compared with the original concepts.
The measures for this are simple but not always clear to everyone involved. Selected focus points include:
- Risk minimisation: thorough planning helps to identify potential risks early and develop strategies to minimise them. This prevents problems that could later become costly
- Better time and cost control: by planning early, the project can be scheduled realistically, avoiding time pressure and unforeseen costs
- Early identification of dependencies: during the planning phase, dependencies and bottlenecks between tasks or teams can be identified and accounted for before they hinder project progress.
WHAT MAKES AN EXPERT?
BAUMANN MEDICAL supports customers in optimally developing their components and associated production processes, knowing that no two springs are exactly the same. Historically, the company’s experience is reflected in successful collaborations with medical device and pharmaceutical companies over more than two decades, working with customers with low- to high-volume devices. Additionally, going further back, for more than 135 years, the company’s springs and stampings have been increasing the health, comfort, efficiency and safety of a considerable number of people.
BAUMANN MEDICAL’s engineering excellence and comprehensive process coverage are what truly set it apart. The company’s team of engineers works closely with clients to develop advanced technological solutions that improve lives (Figure 1). Understanding that each project is unique, BAUMANN MEDICAL adopts a bespoke approach, tailoring its services to meet the specific needs of every client. From the initial concept to serial production, the team meticulously manages and optimises every step of the process. This dedication to customisation and excellence drives the company’s innovation and keeps it at the forefront of the medical device industry.
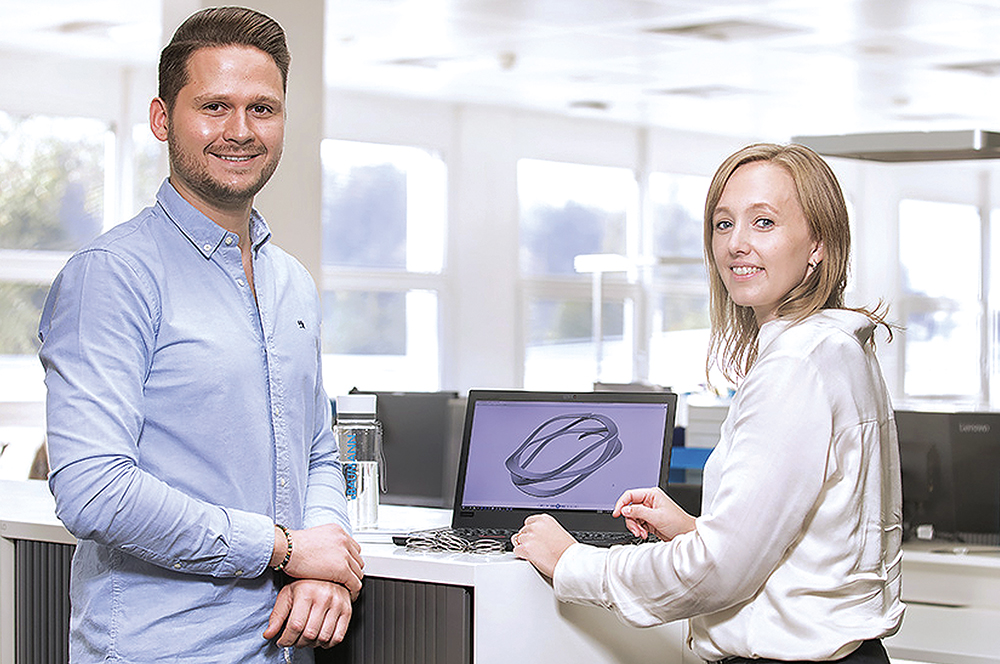
Figure 1: Experts at work.
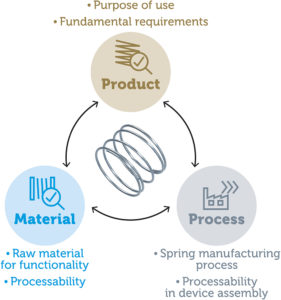
Figure 2: High-level trigger points for a cost-efficient design.
DESIGN FUNDAMENTALS
One of BAUMANN MEDICAL’s areas of expertise is advising and supporting clients during the design iterations between spring/stamping design and the development of medical devices. To achieve the best results, reduce risks and identify dependencies, this process ideally occurs as a collaboration between the device designers and the spring/stamping designers.
In addition to many other important factors in the development of springs and stamped parts for medical devices, this article focuses on three main aspects of the design process: raw materials, product design and process design. Each of these areas presents opportunities to identify cost advantages, which are explored further (Figure 2).
“The choice of raw material depends on factors such as geometric boundary conditions, corrosion resistance, relaxation And the number of use cycles.”
RAW MATERIALS
All types of springs and stamped components can be produced using either stainless or carbon steel. The choice of raw material depends on factors such as geometric boundary conditions, corrosion resistance, relaxation and the number of use cycles. The cross-sectional shape is determined by the spring type or other required properties. Generally, it can be assumed that over 50% of the volume of springs and stamped parts in medical devices could be made from carbon steel.
However, in practice, stainless steel is often specified due to a general consensus that medical devices and equipment should be made from this material, primarily because of cleanliness concerns. When specifying materials, several factors must be considered, including exposure to liquids or humidity, storage conditions and duration, shininess and contact with other materials or patients. Nevertheless, the main driver for material selection remains the relaxation of the spring (Figure 3).
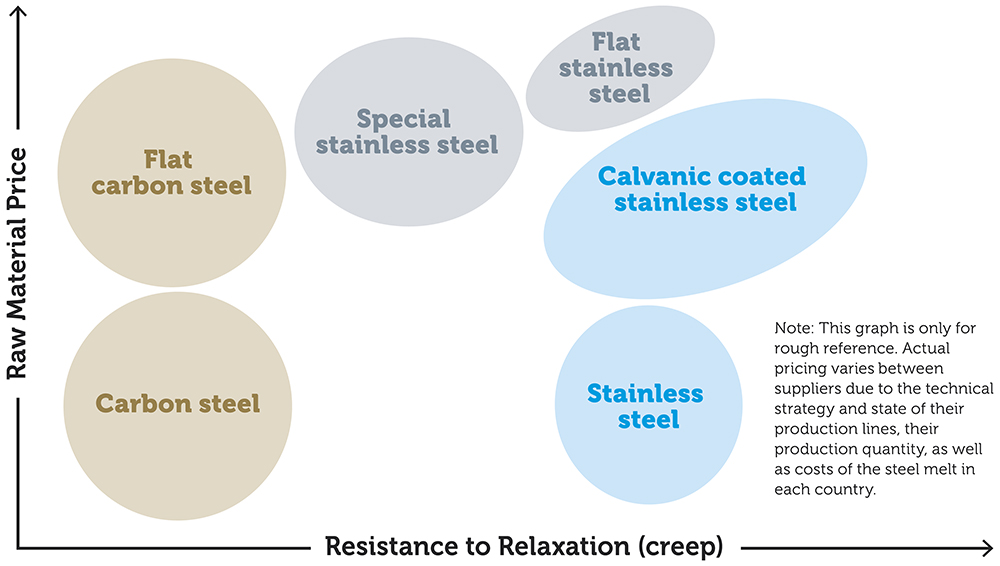
Figure 3: The main driver for material selection remains the relaxation of the spring.
For an approximate idea of potential cost savings – depending on the volume purchased – consider that a basic soap-coated carbon steel costs around €3.50 (£2.80) per kg, compared with stainless steel at €7 per kg (lowest price found on October 9, 2024). In this context, it is useful to critically evaluate and challenge the choice of raw material to achieve cost efficiency. The following example of spring relaxation for carbon steel demonstrates the implications.
“Factors such as temperature, duration of load and initial stress state influence the extent of a spring’s relaxation.”
Spring relaxation is the phenomenon in which a spring, after being deformed and held in that state for an extended period (shelf life), loses some of its stored energy and, consequently, its ability to return to its original shape or length. Due to its inherent material properties, carbon steel has a higher relaxation rate compared with stainless steel. Factors such as temperature, duration of load and initial stress state influence the extent of a spring’s relaxation.
The implications for performance and, ultimately, costs are as follows:
- Consistency: if a spring relaxes too much, it may not perform as expected in its application, leading to reduced load-bearing capacity or changes in spring rate
- Design considerations: engineers must account for potential relaxation when designing springs for specific applications to ensure that they maintain their performance over time.
In summary, relaxation in springs refers to a gradual loss of tension, which can affect the performance and reliability of the final product. Understanding this phenomenon is crucial for designers and engineers to ensure the long-term functionality of springs in their intended applications.
PRODUCT DESIGN
Beyond material selection, the spring and stamping type and design are critical cost factors. Key questions include aspects such as stiffness-to-weight ratio, natural geometric variations during serial production and performance during energy release. Designs often have oversized springs, which not only increase costs but also result in bulky products that complicate transport and raise sustainability concerns. By refining these elements, BAUMANN MEDICAL helps to optimise both performance and cost efficiency.
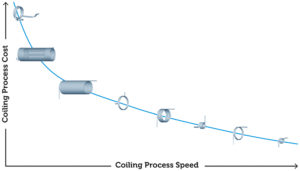
Figure 4: Visualisation of the dependency of coiling costs versus production speed.
Using a torsion spring as an example of the key points that indicate an optimum design for minimum coiling costs, torsion springs featuring a small coil ratio, few coils, tangential legs and closed coils are the most cost effective in terms of coiling. However, several factors affect production speed (Figure 4):
- Wire length: longer wire results in slower production speeds
- Leg complexity: more intricate leg designs reduce manufacturing speed
- Spring body complexity: a more complex spring body also contributes to slower production
- Radial stiffness: lower radial stiffness in the coils slows down production
- Coil ratio and pitch: a large coil ratio combined with a small pitch ratio results in lower radial stiffness, further affecting speed
- Spring length: the longer the spring, the lower the production speed.
The following are real-life product design examples:
- Detangling behaviour: spring geometry may lead to the tangling of springs with different modes and depth. The degree of detangling success has a direct impact on the assembly line OEE.
- Deformation behaviour during assembly: a certain geometry can create challenges during subassembly of the spring. Geometry-related non-linearities during the loading operation in the assembly process may lead to lower assembly machinery performance, as the spring being deflected must be controlled. PROCESS DESIGN The journey from early-stage product development to industrialisation is a crucial process. BAUMANN MEDICAL excels in creating and designing unique solutions from scratch or enhancing the performance of existing parts to improve medical device performance and total costs. Its product engineers, in co-ordination with the development team, create production processes that meet client needs, ensuring the most efficient process.
It is useful to critically reflect on a few points where the basic design influences the process design. Cost drivers in spring production offer a different degree of automation. Or vice versa – the more complex a product, the more process steps and the higher the costs.
Key factors in spring design that ensure an efficient production process include material selection, precise tolerances, and a design that reduces complexity and machining effort. However, customer requirements must not be overlooked. For example, adding inactive coils at the ends of springs increases material consumption and costs but, at the same time, it simplifies handling for the customer during spring feeding and eases BAUMANN MEDICAL’s production process. Another example involves spring wire: stainless wire with drawing soap has lower costs and is more readily available than polished wire. For the manufacturing process, “impure” wire is more economical and easier to handle in coiling; however, it can cause soap residue build-up on customers’ assembly lines, leading to production downtime. Therefore, it is crucial to have a detailed conversation with the customer on these issues early in the process to reach a consensus between both parties and outline mutual dependencies. This ensures that the spring manufacturing process is as efficient as possible without neglecting customer requirements (Figure 5).
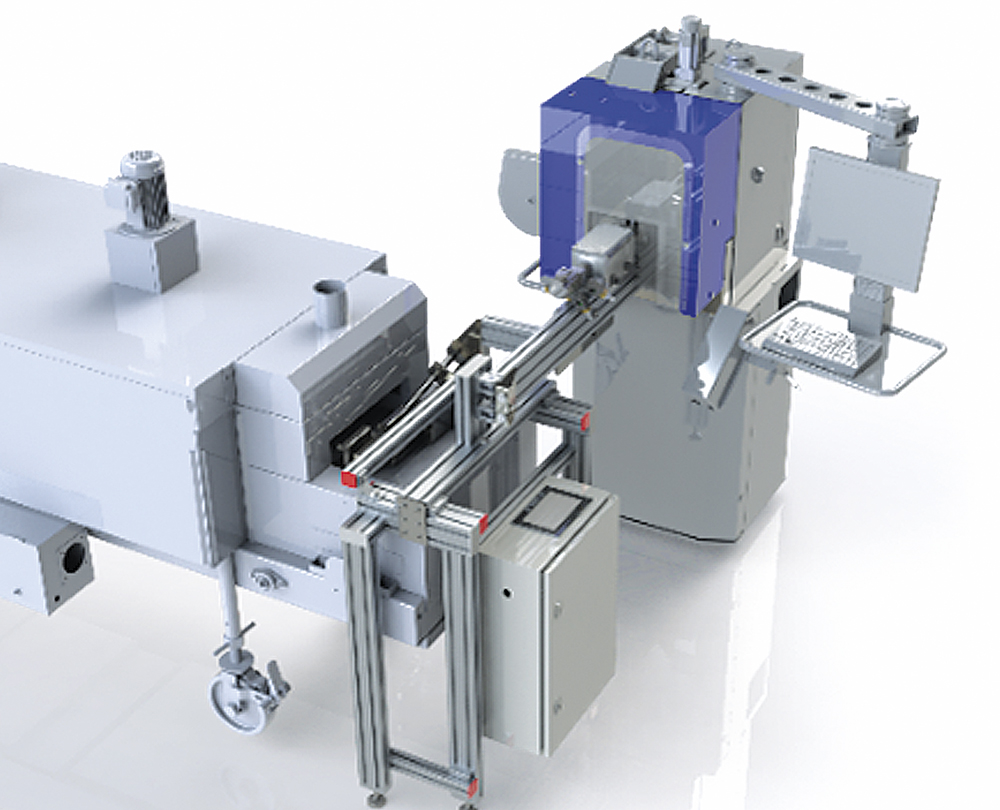
Figure 5: Process design for fully automated sorting.
BAUMANN MEDICAL’s extensive expertise in process, machine building, process optimisation, manufacturing and quality management ensures a seamless and precise shift from prototypes up to triple-digit production. With global manufacturing capabilities across the North American Free Trade Agreement region, Europe and Asia, the company can support projects locally while providing the same high standards at all locations.
CONCLUSION
Spring production involves various cost drivers, each offering different levels of automation. As the complexity of the requirements increases, so does the production process. The key factors influencing spring production costs include:
- Wire costs: the cost of the wire depends on several factors, including the type of alloy used, the shape of the cross-section, and the surface quality and coating of the wire. Smart material selection can save up to 50% of pure material costs.
- Product design and geometric factors: these influence both the feasibility of production and the speed at which springs can be produced. An integral and well-thought-out design of the springs can save more than 30% of total costs.
- Process costs: these are driven by the type of spring, process complexity, geometric factors and specific features, such as cleanliness, surface conditions or the envelope, hooks and legs. With a customised and streamlined process, it is possible to achieve double-digit percentage savings in total costs.
By understanding these factors, manufacturers can better manage production efficiency, costs and risk mitigations.