To Issue 164
Citation: Allegro A, Cuccato A, “Unlocking Opportunities in On-Body Delivery Systems Through a Platform Technology Approach” . ONdrugDelivery, Issue 164 (Sep 2024), pp 42–45.
Anna Allegro and Andrea Cuccato discuss how Stevanato Group’s Vertiva® on-body delivery system exemplifies a platform technology approach to device design, with its 3 and 10 mL formats providing the flexibility necessary to accommodate a wide variety of therapies.
On-body delivery systems (OBDSs) present an increasingly powerful opportunity for achieving better patient experiences and outcomes by supporting the ongoing shift from intravenous (IV) to subcutaneous (SC) drug delivery. With expanded treatment options that are able to accommodate larger volumes, as well as more concentrated and viscous formulations, OBDSs can provide the means to reduce injection frequency compared with other lower-volume delivery devices, while also introducing the convenience of wearable technology. These are all factors that, taken together, allow OBDSs to help address the key challenge of medication adherence, which compromises treatment effectiveness for an estimated 30–40% of those with long-term conditions – and an even higher proportion of patients affected by certain other diseases.1,2
Such benefits have intensified the interest in OBDS development in recent years, but this has not necessarily translated into a flood of product launches. Indeed, since July 2016, only five OBDSs with a dose volume of 3 mL or greater have reached the market. At a quick glance, these devices could be mistaken for variants of off-the-shelf products, much like pen injectors can be based on the same underlying technology. However, this type of approach is rarely viable for OBDSs, each of which will be targeted at a specific therapy area and must be uniquely tailored to control the delivery of a specific drug formulation according to a defined injection profile.
While the architecture of an off-the-shelf product might be able to accommodate minor adjustments or component changes to suit the requirements of a specific application, such devices are generally designed for a specific purpose, leaving comparatively little scope for adaptation. Supporting the requirements of an OBDS, meanwhile, requires a necessarily higher level of customisation that can never truly be supported by a pre-determined approach.
“Rather than thinking of OBDS development in terms of platform products, pharmaceutical companies can realise benefits by adopting a platform technology approach, defined by far higher levels of versatility.”
Therefore, rather than thinking of OBDS development in terms of platform products, pharmaceutical companies can instead gain an advantage by adopting a platform technology approach, defined by far higher levels of versatility. Platform technologies are built on a foundation that supports the creation of customisable products tailored to a specific therapeutic requirement. Everything revolves around a consistent core technology that can be reconfigured in terms of its specific functionality according to different delivery profiles and fill volumes. Beyond these reconfigurations, there is also potential to customise the user interface of the device to further optimise the patient experience.
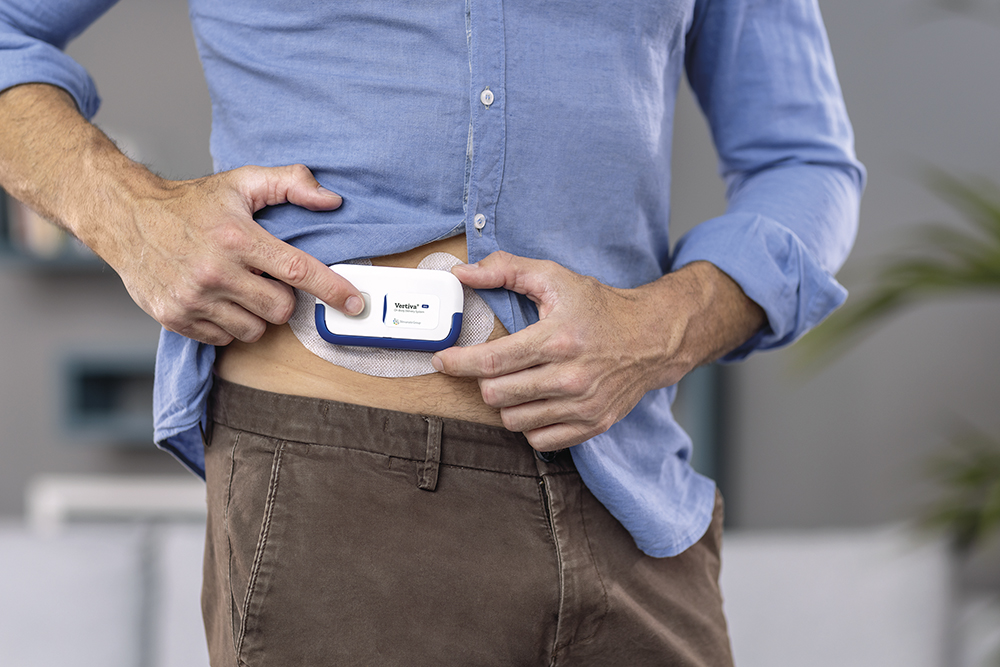
Figure 1: Stevanato Group’s Vertiva® OBDS simplifies drug delivery during at-home self-administration.
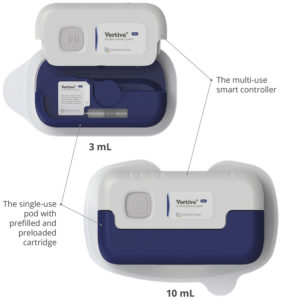
Figure 2: Vertiva®, Stevanato Group’s next-generation OBDS for large-volume drug delivery, available in 3 and 10 mL formats.
STEVANATO GROUP’S VERTIVA® PLATFORM TECHNOLOGY
Stevanato Group has developed the Vertiva® OBDS using a highly versatile platform technology model. For pharmaceutical companies, it provides the strengths of a foundational system with the flexibility to be adjusted and adapted according to patient needs across a diverse range of applications (Figure 1). Two versions of the Vertiva® platform have been developed so far – 3 and 10 mL (Figure 2) – both of which share:
- A core technology comprising a single-use injection unit (the “pod”)
- A reusable smart controller that manages the activation process
- A proprietary magnetically coupled drive mechanism that connects the pod and controller, enabling contactless power transfer between the two.
In both configurations, the mechanical pod is designed to house prefilled and preloaded glass cartridges, which simplifies set-up for the patient by removing the need to manually fill or load the device. During administration, needle insertion and retraction is automated to ensure the safe and accurate SC delivery of the specified dose. At the same time, body-sensing technology prevents premature activation. From a user’s perspective, these intuitive design attributes limit manual intervention and help facilitate treatment initiation.
The reusable controller, meanwhile, can be programmed with relevant delivery profiles, supporting multiple therapy cycles (Figure 3). This dynamic removes the need for the pod to incorporate electronic components, increasing its resilience while also limiting its overall environmental impact. Optionally, data on patients’ device usage can be recorded by the controller and then transferred via Bluetooth.
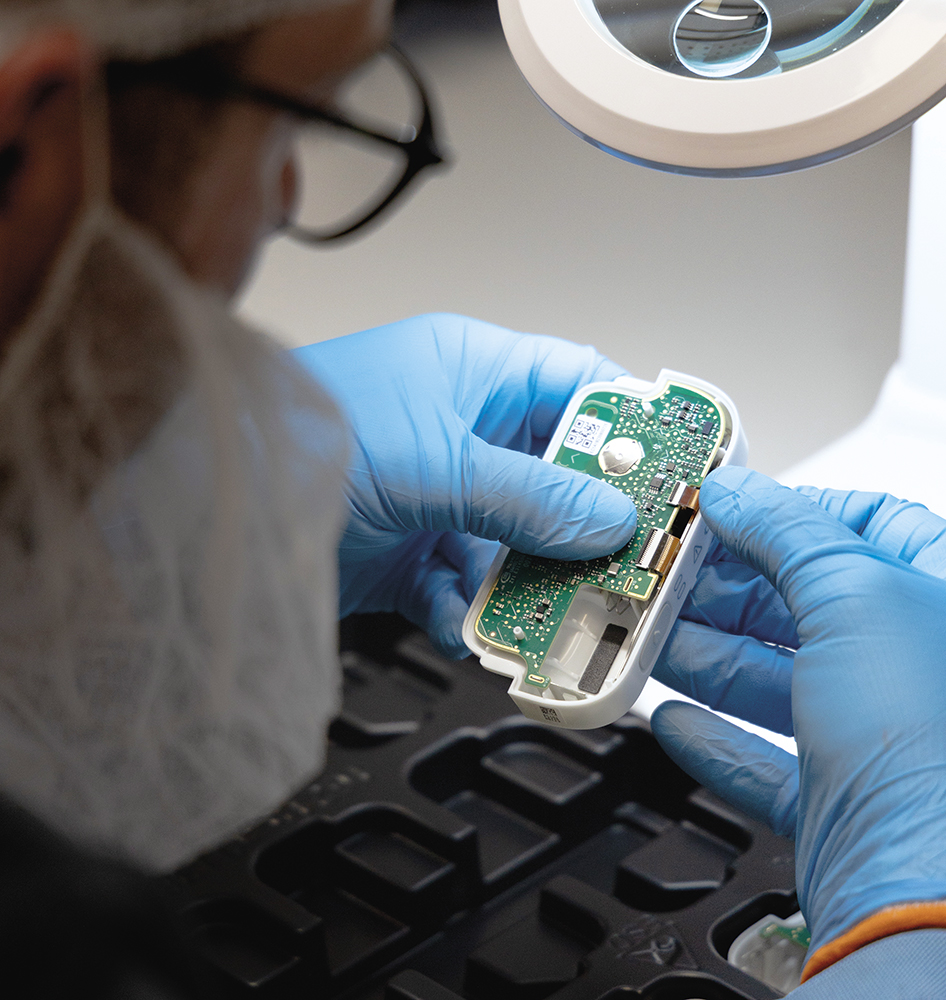
Figure 3: The two-part structure of Vertiva® keeps all electromechanical components in the reusable smart controller.
Based on this underlying structure, which is common to both configurations of Vertiva®, Stevanato Group has optimised the current 3 and 10 mL platform versions for two different application types. In the case of Vertiva® 3 mL, this platform version has been developed as an OBDS infusion pump ideal for the delivery of complex small-molecule therapies, where drug product volumes are comparatively low. In particular, the device can be configured to discreetly deliver micro-precision non-monotonic basal delivery, with the additional option of on-demand boluses restricted to a limited number over a given period. In its 10 mL form, the Vertiva® OBDS has been developed as an OBDS injector optimised to support the delivery of full-content bolus injections of highly viscous large-volume biologics.
These figures underline some of the key differences between Vertiva® in its 3 and 10 mL configurations, even though the devices are based on the same core platform. Achieving this variance demands careful consideration of multiple device characteristics and components for Vertiva® to be optimised in the form of either a small-molecule infusion pump or an OBDS injection device for biologic delivery.
TAILORING VERTIVA® FOR INDIVIDUAL THERAPIES
Optimisation of the Vertiva® platform is achievable thanks to its inherent flexibility, which allows the device to support various therapy profiles within physical dimensions that meet the acceptable thresholds for an OBDS. There are, however, important technical considerations when accommodating the continuing trend of drugs with increasingly higher viscosities. For example, where large boluses of very viscous drugs are to be delivered in a short timeframe, and therefore at a high flow-rate, more electromechanical power is required. While a potential solution would be to upscale the device components, this would conflict with the imperative to restrict device dimensions. Power must therefore be transferred with maximum efficiency from the electromechanical drug delivery sub-system without compromising the overall range of flow rates possible, as this would restrict the therapy profiles that can be supported.
The core Vertiva® platform technology has been developed by Stevanato Group to allow the electromechanical subsystem to be optimised in light of these requirements. Thanks to the precise design of the motion transmission gearing stages, the efficiency of the electrical motor is maximised at peak power demand, where design constraints are most limited because the gearing torques and rotational speeds are highest. This has been achieved without narrowing the overall range of drug viscosities and delivery flow rates that can be supported within a single OBDS version.
This process is exemplified by the Vertiva® 10 mL platform OBDS version. Here, the efficiency of the drug delivery subsystem has been optimised to allow for the delivery of a 10 mL single bolus of a drug solution with a viscosity of 25 cP within five minutes. The same device, however, remains capable of supporting the delivery of a broad range of drug viscosities, from aqueous-like solutions in the lower range up to highly viscous products of 100 cP and above.
However, customisation of the Vertiva® platform is not exclusively focused on expanding the discrete bolus injection profile – the platform has also been designed to accommodate the contrasting requirements of the basal micro-dosing profiles typical of infusion pumps. Here, as well as the requirement to maximise power efficiency, there is a parallel requirement to control delivery of small drug volumes with a very high dose accuracy. These delivery approaches often have conflicting drivers for the design of the mechanical gearing subsystem, introducing a duality that can present a technical challenge. In the development of a 3 mL infusion pump version of the Vertiva® platform technology, however, Stevanato Group has been able to accommodate these needs, with targeting of basal infusions possible over an up-to-24-hour period and with a single basal pulse resolution as small as a few microlitres.
The ability to overcome these challenges and bring such versatility into the platform stems from the highly accurate modelling of the electromechanical subsystem by Stevanato Group’s engineering team. Following initial development, each individual sub-system involved in the drug delivery process is subject to subsequent refinement through iterations of characterisation and optimisation, which encompass both the parameters of the model and the model itself.
All considerations relating to power and efficiency for the bolus injection are centred on the energy source, which is typically a battery for an OBDS. High demands are placed on the capabilities of this internal electrical energy storage, driven by the combination of high formulation volumes and viscosities, short delivery times and the need to serve a range of therapies with a single controller. In device development, this can open discussions around whether to equip the device with either a replenishable energy source, achieved through either battery recharging or replacement, or a non-replenishable one. Because either option could represent the optimal solution depending on a customer’s needs, Stevanato Group has ensured that the Vertiva® platform technology has been developed with both in mind.
Such decisions involve weighing up a variety of factors. Employing an updateable energy source, for example, can improve the reusability of the controller element and, therefore, its sustainability – the use of a rechargeable battery brings further benefits in this area. However, it is also clear that in applications where an OBDS has a low energy demand – as would be the case for treatments involving a limited number of therapy cycles, low-viscosity drugs or low delivery flow rates – the use of an embedded non-rechargeable battery can bring advantages in terms of reducing device dimensions and design complexity.
With the Vertiva® 10 mL version, Stevanato Group has been able to demonstrate the capability to address extended therapy models through the addition of battery rechargeability. Indeed, the controller can support dozens of injections spread over up to two years of continuous treatment. For patient convenience, quick charging was investigated as a key feature of the platform technology, with the aim of making the device ready for injection within 15 minutes from a low-battery condition. Wired charging via a USB-C connector simplifies this task for patients, ensuring an intuitive and reliable user experience.
“Stevanato Group’s production proposition for both the 3 and 10 mL Vertiva® device configurations is significantly strengthened by its collaboration with Thermo Fisher Scientific.”
CONCLUSION
From product design to manufacture, assembly and lifecycle management, there are clearly many elements to consider in the development of an OBDS. And as an integrated solution provider whose end-to-end offering extends from primary packaging to device design, development and manufacture, Stevanato Group has the breadth and depth of expertise to support pharmaceutical partners at all stages of product development as part of a risk-managed production process. The company’s scalable services in precision component supply and device sub-assembly are underpinned by a strong supply chain and a structure that allows for direct integration with a pharma partner and/or a CMO. However, Stevanato Group’s production proposition for both the 3 and 10 mL Vertiva® device configurations is significantly strengthened by its collaboration with Thermo Fisher Scientific (Waltham, MA, US).
Together, Stevanato Group and Thermo Fisher can provide a streamlined, integrated and fully scalable framework for orchestrating the manufacture of a complete combination product system, from the first stages of formulation development and compounding through to aseptic filling of pre-sterilised EZ-fill® cartridges, final device assembly, serialisation and packaging. This has been supported with investment in a low-volume final assembly line at Thermo Fisher’s site in Ferentino (Italy) for final assembly of both 3 and 10 mL devices, with minimal changes required to the manufacturing equipment components when switching between the different device configurations.
For pharmaceutical companies pursuing on-body drug delivery opportunities, Vertiva® represents a versatile end-to-end OBDS solution, whether employed for a particular application or as a platform that can sustain a pipeline of OBDS innovation. From the same core technology platform, Vertiva® has the flexibility to support a range of drug molecules, viscosities, volumes, delivery times and profiles. And, with established compatibility between drug containment solutions and fill-finish techniques implemented as part of an integrated approach, the production and assembly process can be made smoother, accelerating time to market. Looking to the future, the growth of OBDS applications looks set on an upwards trajectory. However, it is only by adopting a truly versatile platform approach that pharmaceutical companies can expect to unlock these opportunities in a way that delivers performance, impact and value.
REFERENCES
- Garfield S, Judah G, “Learning from successes: designing medication adherence intervention research so that we can learn what works and why”. BMJ Qual Saf, 2022, Vol 31(2), pp 83–85.
- Hichborn J et al, “Improving patient adherence through data-driven insights”. McKinsey & Company, Dec 2018.