To Issue 172
Citation: Gutierrez A, “Vytal – One Step into the Future of Container-Closure Systems”. ONdrugDelivery, Issue 172 (May 2025), pp 76–81.
Ana Isabel Gutierrez looks at advancements in sterile and aseptic filling methods in the pharmaceutical industry, introducing H&T Presspart’s Vytal® snap-fit container-closure system, which is designed to meet the growing regulatory demands of the pharmaceutical industry.
The biopharmaceutical industry is experiencing significant transformation driven by technological advancements and the emphasis on specialised therapies. There is an increasing demand for specialised biological products, including biologics and biosimilars. According to a Global Biologics Market Research Report by Insight Ace Analytic, the global biologics market was valued at US$402 billion (£313.6 billion) in 2023 and is predicted to reach $717 billion by 2031, at a 7.76% compound annual growth rate. This growth is fuelled by the expiration of patents on major biologics and the necessity for innovative treatments for complex diseases.
Advancements in sterile and aseptic filling methods are essential for maintaining product sterility. Robotics and automation significantly reduce the risk of contamination, while advanced isolator technologies enhance sterility assurance and operational efficiency. These innovations enable manufacturers to meet strict regulatory requirements and deliver high-quality products, which accelerate drug development timelines and enhance the accuracy and efficacy of therapies, thus promising significant improvements in patient care.
Ready-to-use (RTU) containers play a crucial role in improving production efficiency and sterility. These containers are pre-sterilised and are prepared for aseptic filling, minimising contamination risks. Snap-fit closure systems facilitate rapid assembly without additional equipment, preserving the sterile barrier. These systems are essential in environments where high precision in required, such as in the production of monoclonal antibodies or messenger RNA-based drugs. They allow for design flexibility to meet diverse product needs, which is crucial for customisation.
The integration of RTU systems with snap-fit closures is revolutionising the industry by reducing costs, improving production efficiency and enhancing product safety. As regulatory demands increase, these systems provide solutions to meet global quality and safety standards, enabling rapid delivery of safe and effective biopharmaceutical products to the market.
RTU SNAP-FIT CLOSURE SYSTEM: INNOVATION WITH VYTAL
Vytal Snap-Fit Technology
To meet increasing regulatory demands and the stringent requirements of the pharmaceutical industry, H&T Presspart has introduced Vytal, a new snap-fit container closure. Vytal effectively handles biologics and complex drugs, is compliant with ISO13485 and GMP Annex I, and is compatible with multiple sterilisation methods.
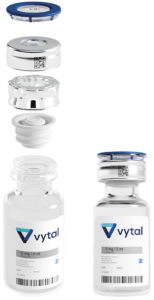
Figure 1: Vytal’s snap-fit closure.
Single-Step Vytal System Advantages
Vytal offers a single-step design that optimises sealing with three security areas, reduces residual volume, and features tamper evidence and laser marking for enhanced security and traceability (Figure 1).
Operational Efficiency and Risk Reduction
Vytal enhances efficiency, it streamlines the closure process, reduces the likelihood of human error and seamlessly integrates into existing workflows. Its compatibility with both glass and cyclo-olefin polymer (COP) containers helps to minimise contamination risks.
Comparison with Traditional Systems
Vytal’s snap-fit technology reduces particle generation and material degradation, enhancing container integrity even at low temperatures (-80°C) compared with traditional systems. Vytal is compatible with standard closed-system transfer devices (CSTDs), setting a new benchmark in aseptic pharmaceutical processes.
CCI AND COMPATIBILITY WITH GLASS AND COP VIALS
Manufacturers of complex and biologic pharmaceuticals encounter significant challenges regarding container-closure integrity (CCI) during the vial filling process. Maintaining CCI is crucial for safeguarding against contaminants and preserving the product’s sterility throughout storage and distribution. Any breach in CCI can jeopardise the drug’s safety and effectiveness, posing health risks to patients and potentially subjecting the manufacturer to legal liabilities.
CCI is especially critical for biologics because they are sensitive to environmental factors such as light, temperature and oxidation, which can lead to the degradation of proteins and complex molecules (Figure 2).
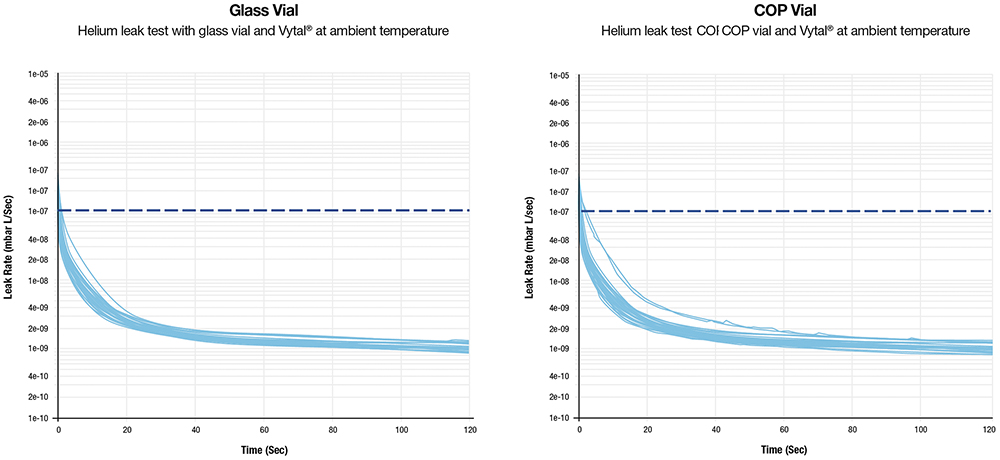
Figure 2: CCI with Vytal and glass vial (left) and Vytal and COP vial (right) at ambient temperature.
Common problems with CCI arise from failures in vial sealing, which can be caused by defects in rubber stoppers, imperfections in glass vials or errors during the sealing process. Innovations in aseptic filling technologies, along with the development of snap-fit closures, are addressing these challenges. These advancements enhance automation and precision, reducing contamination risk and improving CCI.
Snap-fit closures provide a more efficient and secure sealing method by eliminating the need for traditional crimping, thus simplifying the process and minimising errors.
Vytal is pioneering advancements in CCI assurance at ultra-low temperatures (up to -80˚ C), which are crucial for preserving temperature-sensitive biologics. Such technological advancements substantially enhance the safety, efficacy and integrity of complex biologic pharmaceuticals (Figure 3).
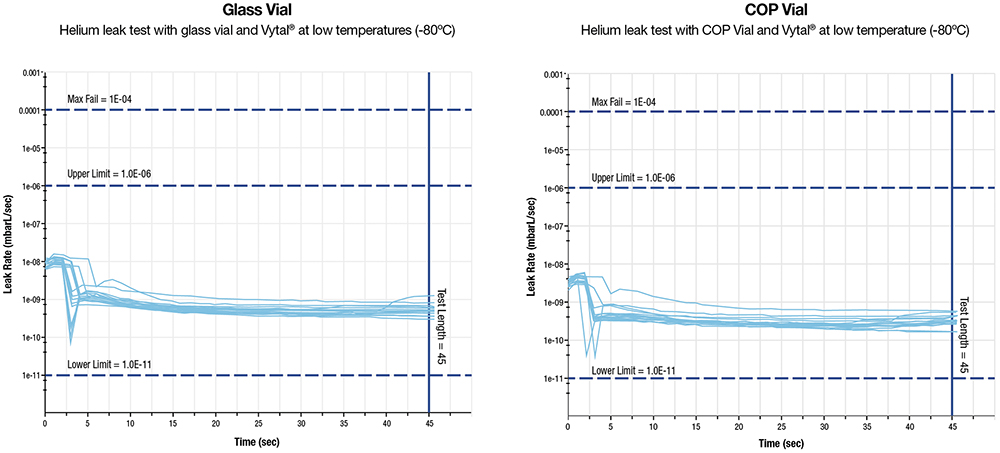
Figure 3: CCI with Vytal and glass and Vytal and COP at low temperature.
H&T Presspart’s Vytal performs exceptionally well with both borosilicate glass and COP containers. Its adaptive sealing mechanism effectively accommodates dimensional variations, ensuring consistent CCI. Stress analysis confirms that there are no localised tension points that could compromise CCI, highlighting the system’s reliability in diverse pharmaceutical packaging applications.
COMPATIBILITY WITH CSTDs
In handling hazardous drugs, CSTDs are crucial for protecting healthcare professionals from toxic exposure. Vytal has been tested successfully with standard marketed CSTDs, as the integration of these devices with snap-fit container closures is of paramount importance for several fundamental reasons:
- Safety: CSTDs, when combined with snap-fit closures, form a robust barrier against hazardous drug aerosols and vapours, protecting healthcare professionals in hospitals and labs .
- Product Integrity: CSTDs maintain drug stability by providing a hermetic seal that protects against contamination, ensuring medications remain safe and effective until use.
- Regulatory Compliance: Compatibility with snap-fit systems helps healthcare facilities meet international CSTD regulations, preventing legal issues and ensuring compliance.
- Operational Efficiency: Snap-fit systems compatible with CSTDs streamline medication handling, reduce errors and optimise workflow, allowing more time for patient care.
Vytal’s compatibility with CSTDs is essential for ensuring safety, integrity, compliance and efficiency. Drug manufacturers adopting these technologies prioritise the protection of healthcare personnel and patients while meeting regulatory standards – all while simplifying processes and ensuring drug safety (Figure 4).
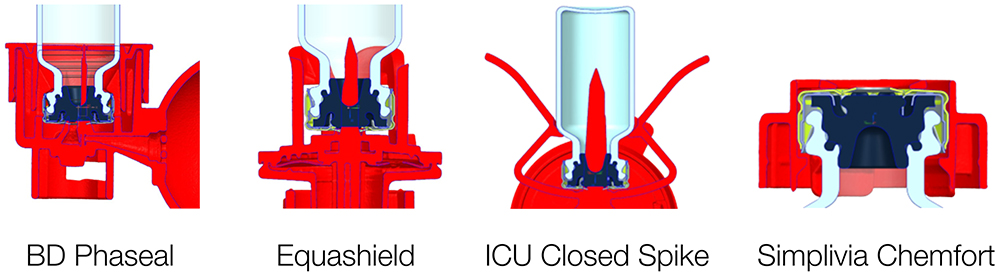
Figure 4: Compatibility with standard marketed CSTDs.
RESIDUAL VOLUME OPTIMISATION
When dosing drugs from vials, optimising residual volume is vital, especially for highly sensitive medications. These drugs often involve complex production and filling processes, leading to high costs.
Vytal is designed as a snap-fit concept for container-closure systems, preserving the traditional look by maintaining a complete view of the vial’s neck. This design strategy addresses several key areas:
- Economic Impact: Reducing residual volume helps to minimise medication waste, leading to substantial cost savings for healthcare providers and pharmaceutical companies, particularly with costly drugs.
- Technical Solutions: Vytal’s closure system enhances syringe access and improves the efficiency of drug extraction by providing a clear view of the vial neck, thereby effectively reducing residual volume.
- Benefits for Patients and Healthcare Providers: By ensuring complete dosing, patients receive all of their prescribed treatment, thereby enhancing therapeutic outcomes. Healthcare providers also benefit from cost reductions and increased efficiency in resource allocation.
- Comparative Efficiency: Vytal, with its unobstructed vial neck visibility, outperforms traditional systems by minimising waste and enhancing the efficiency of drug retrieval (Figure 5).
Overall, Vytal’s innovation underscores its value by ensuring economic efficiency, enhancing medication administration efficacy and reinforcing patient safety within healthcare settings.
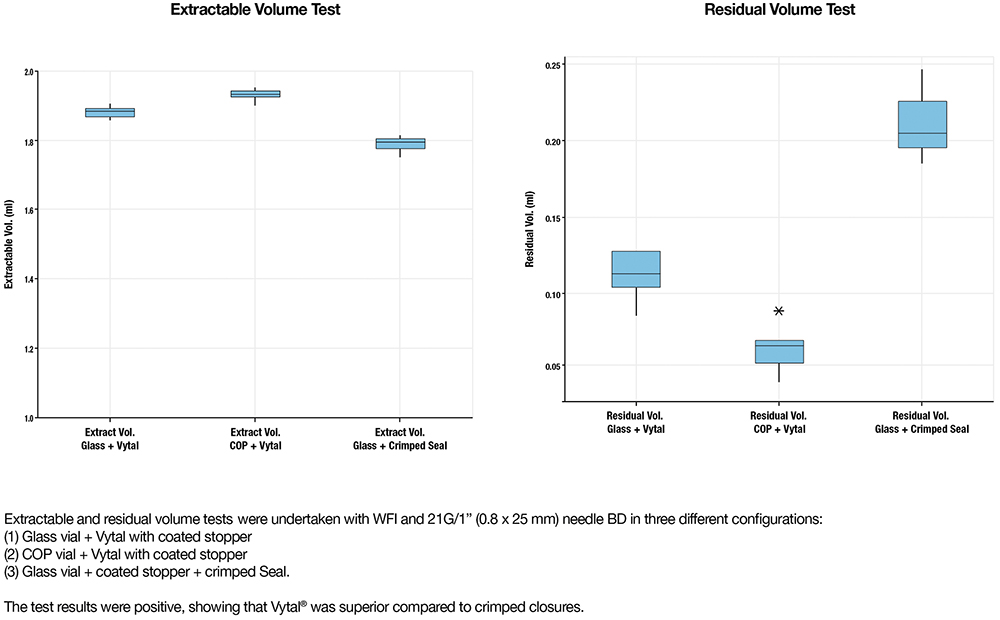
Figure 5: Extractable and residual volume with Vytal.
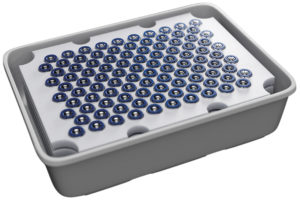
Figure 6: Vytal nested.
NESTED AND BULK FORMATS
Vytal offers flexibility with both nested and bulk formats. The nested option allows for the efficient closure of 100 vials simultaneously using current technologies, thereby enhancing operational efficiency. Meanwhile, the bulk format, available in ported bags, is designed for compatibility with automatic filling machines in controlled environments, such as isolators. This versatility ensures that Vytal meets varied processing needs while optimising throughput and maintaining high-quality standards in pharmaceutical applications (Figure 6).
PARTICLE CONTROL AND QUALITY
Snap-fit container-closure systems offer significant advantages over classical crimping systems, particularly in reducing particle generation, which is crucial in pharmaceutical manufacturing and safety.
Reduced Mechanical Action
Snap-fit systems use a straightforward snapping mechanism, minimising mechanical stress and reducing particle generation compared with the substantial force required in crimping (Figure 7).
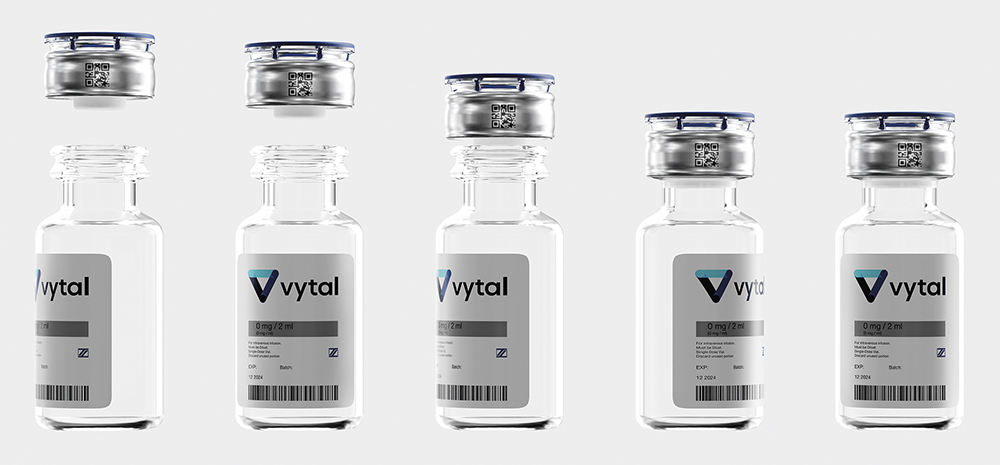
Figure 7: Vytal snap-fit closure.
“SNAP-FIT SYSTEMS SUBSTANTIALLY REDUCE PARTICLE GENERATION – ENHANCING PRODUCT QUALITY AND COMPLIANCE – WHILE SUPPORTING CLEANER ENVIRONMENTS ESSENTIAL FOR PHARMACEUTICAL MANUFACTURING.”
Minimisation of Material Wear
Unlike crimping, which can cause abrasion and generate metallic particles, snap-fit systems interlock smoothly without intensive material contact, reducing wear and particle contamination.
Enhanced Cleanliness
With fewer steps and less equipment, snap-fit systems again limit particle formation, reducing contamination risks compared with complex crimping equipment.
Compliance With Stringent Regulations
Snap-fit systems naturally meet stringent regulatory requirements, like those from the US FDA and EMA, by offering a cleaner sealing method. In summary, snap-fit systems substantially reduce particle generation – enhancing product quality and compliance – while supporting cleaner environments essential for pharmaceutical manufacturing.
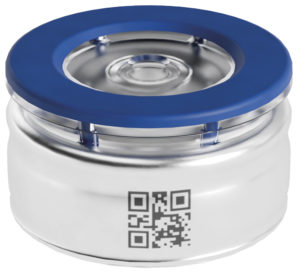
Figure 8: Anti-counterfeiting laser marking.
ANTI-COUNTERFEITING
Vytal’s container-closure system incorporates advanced anti-counterfeiting features to combat pharmaceutical counterfeiting. The aluminium cover seal supports laser coding, enabling serialised 2D matrix codes for unit-level traceability and integration with global track-and-trace systems (Figure 8).
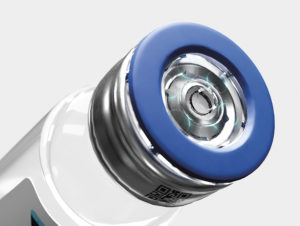
Figure 9: Anti-counterfeiting tamper evidence.
A patented transparent window in Vytal’s plastic button provides instant tamper detection. Users can see any breach in closure integrity, as broken aluminium bridges are visible through the window (Figure 9).
These features comply with WHO guidelines and regulatory standards, such as the FDA’s Unique Device Identification system and the EU’s Falsified Medicines Directive, enhancing authenticity and integrity in the pharmaceutical supply chain.
REDUCING TIME TO MARKET
Vytal is designed to seamlessly integrate with both well-established, high-speed filling machines and emerging modular filling machine concepts. Modular options are becoming more prominent due to their suitability for producing biological drugs, which often require small batch sizes of multiple drug variants.
These machines provide a significant advantage by reducing time to market, thanks to their availability and faster manufacturing and qualification processes when compared with traditional high-speed lines – a crucial factor for achieving competitiveness in the pharmaceutical industry.
Moreover, these machines offer remarkable flexibility, allowing for rapid transitions between different drugs, vial sizes and even other formats without the downtimes typically associated with conventional equipment modifications.
“VYTAL OFFERS THE FLEXIBILITY TO CHOOSE EITHER TRADITIONAL
LINES OR THE MOST ADVANCED OPTIONS FOR PRODUCING SMALL TO MEDIUM BATCHES.”
This adaptability is essential for accommodating a wide range of products efficiently and cost effectively. Consequently, Vytal offers the flexibility to choose either traditional lines or the most advanced options for producing small to medium batches.
CONCLUSION
Vytal is establishing itself as the new benchmark in aseptic fill-finish processes for biologics and complex pharmaceuticals. The snap-fit closure adheres to rigorous containment and safety standards, rendering it particularly suitable for advanced therapeutic products. Developed in compliance with ISO13485 and GMP Annex I, Vytal is versatile in its sterilisation compatibility, accommodating ethylene oxide, X-ray, gamma and steam post-capping methodologies.
The system features three sealing areas to ensure superior CCI and includes a visible withdrawing area designed to minimise residual volume, thus addressing contemporary requirements for efficiency. Its tamper-evident capabilities and laser marking potential enhance security and traceability, which are crucial amid increasingly stringent regulatory frameworks.
With compatibility across D13 closures and 2R vials in both glass and COP formats, Vytal offers significant operational flexibility while maintaining a conventional appearance, ensuring seamless integration with ISO standards and existing CSTDs.
In conclusion, Vytal is optimally positioned to serve as the standard in aseptic processing, meeting both current and forthcoming industry imperatives for quality and operational efficiency.