To Issue 140
Citation: Lastow O, “Why are Inhalation Devices so Difficult to Develop?” ONdrugDelivery, Issue 140 (Nov 2022), pp 28–32.
Orest Lastow discusses the challenges of developing inhalation products and how best to keep costs down and prevent project delays.
Today, many conditions are managed with inhaled pharmaceuticals. The best route of administration for a pharmaceutical product is determined by the target organ for the drug and other considerations for optimal uptake of the product in the body. An inhaled drug is typically delivered to the nose, airways or lungs using an inhalation device. The main two diseases treated using this route are asthma and chronic obstructive pulmonary disease (COPD), with the drug in either a liquid or dry-powder formulation.
“A low-cost single-use device requirement is not compatible with advanced feedback features.”
There are currently three main device types for inhaled pharmaceuticals – pressurised metered dose inhalers (pMDIs), dry powder inhalers (DPIs) and nebulisers. DPIs can come as either a multidose or single-dose inhaler. DPIs and pMDIs are portable inhalers, whereas nebulisers are typically stationary inhalers used in hospitals or at home. There are, however, some smaller portable nebulisers on the market. These are typically more advanced and expensive, and their market share is relatively small. What all inhalation devices have in common is that they convert a dose of formulation into an aerosol of respirable particles in the size range of 1–5 μm.
The development, manufacturing and registration of an inhalation product is associated with several major difficulties that deter pharmaceutical companies from investing in such development. There are a few major pharma companies that have a strong track record of commercialising successful inhalation products, but the list is fairly short compared with other dosage forms. This reflects how the market is structured, with a few major players dominating the market. This remains true even though the patents of many major inhaled pharmaceuticals have long since expired, presenting an opportunity for generic substitution on the market. For a new player, the threshold to enter the market is high and very few even try.
Even major generic companies, with an extensive product portfolio, find it difficult to build the very eclectic team required to successfully develop an inhalation product and bring it to market. Even for an experienced and well-equipped company, such development has proved to be costly – with lengthy development times. Perhaps the most significant deterrent is the significant risk of major delays and increased development cost.
There are four major challenges when developing an inhalation product:
- Conflicting user requirements
- Product complexity
- Inextricable performance
- The delicate balance between regulatory and manufacturing requirements.
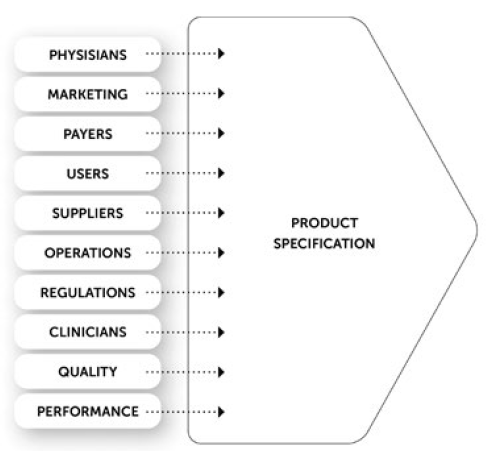
Figure 1: Requirements from users and stakeholders.
USER REQUIREMENTS AND CONFLICTING INTERESTS
The first key challenge in the development of an inhalation product is to produce a good and balanced specification that voices the demands from users, payers, healthcare professionals and other stakeholders. The specification should be comprehensive and all the requirements must be compatible. All the implications of the requirements should be well analysed and understood. Internal company stakeholders and functions should also be included – i.e. operations; marketing; the chemistry, manufacturing and controls (CMC) documentation team; and the clinicians that will conduct the clinical trials (Figure 1).
The different stakeholders, users and customers will, in many cases, have strongly conflicting requirements. Balancing these different needs when compiling a comprehensive specification is very demanding. When a high-level specification is drafted, several specific technical questions must be answered to select appropriate technical solutions. The questions include, for example:
- DPI or pMDI?
- Active or passive?
- Electronic or mechanical?
- Pre-metered or reservoir?
- Simple formulation or advanced formulation?
- Large dose or small dose?
- Relative humidity (RH) protection or not?
- A few user steps or many user steps?
- Dose counter or dose indicator?
These decisions will provide a foundation for future compilation of the specification.
User Studies
The next step is to map out how the patient uses the inhalation product and what drives the different aspects of use. The outcomes of user studies typically give some clear unambiguous results, however, some of these results can also be mutually conflicting. In some cases, the user has an inconsistent perception of their own personal use and preferences.
The highest ranked features are often the various feedback functions; the user requires reassurance from the inhalation device that the dose has been correctly delivered. It should also clearly show exactly how many doses remain in the device. However, some users perceive too much feedback as complicated and hard to understand, whereas others want as much feedback as possible.
The device should also be very simple, ergonomic and intuitive to use. It should provide good ergonomics for both children and the elderly. It should be safe against inadvertent opening or actuation when carried in a pocket or purse but also be easy to open and actuated by a person with impaired vision and dexterity. In general, all users agree that the operating sequence should require as few user steps as possible, ideally just open-inhale-close. There should also not be any requirement to clean the device – but it should still be simple to clean, if so desired.
“The device and the formulation are intimately interlinked and must be developed and optimised together.”
Design, Cost and Lifetime of the Device
Another common requirement is that the device should be small, discrete and attractive. This clearly conflicts with the ergonomics and hygiene requirements. Furthermore, a low-cost single-use device requirement is not compatible with advanced feedback features. A disposable device is usually preferred for simplicity, but the perception of the reusable device is that it is more environmentally friendly. However, a reusable device is more complicated to use, as it needs reloading and cleaning. A reusable device is also more technically advanced – thus more expensive. The overall cost break-even point for disposable versus reusable device depends on how many times the device will be reused, which is difficult to predict. The logistics of the refills also need be factored in.
An important factor is the perception that the device is safe and reliable. A more clinical and hygienic design comes across as more reliable than a device with a more consumer-product appearance. The clinical and hygienic design is, on the other hand, less attractive. The device should preferably be attractive to all age groups, from children to octogenarians. A typical market lifetime of an inhalation device is at least 10–20 years, which means that a design should appeal to all ages and sexes over a very long period.
A typical feature sought by patients and doctors is electronic feedback and monitoring. The real benefit of this feature is, however, unclear. The device could, for example, remind the patient to take the medicine, monitor the lung function and automatically upload the data to the prescribing doctor. Although this seems to be a useful feature, it is easy to imagine the patient being annoyed by the constant reminding and seeing the data uploading as an invasion of privacy. Furthermore, not all doctors can be expected to appreciate the benefit of receiving gigabytes of patient information.
PRODUCT COMPLEXITY
When the product specification has been agreed, the multidisciplinary product development project can begin. An inhalation product is very complex and comprises multiple fundamental parts that each present their own challenges. The development of the different parts requires very different sets of skills and is often done by different teams. The number of parts can, of course, be debated but, for the purposes of this article, the product has been split into six fundamental parts (Figure 2).
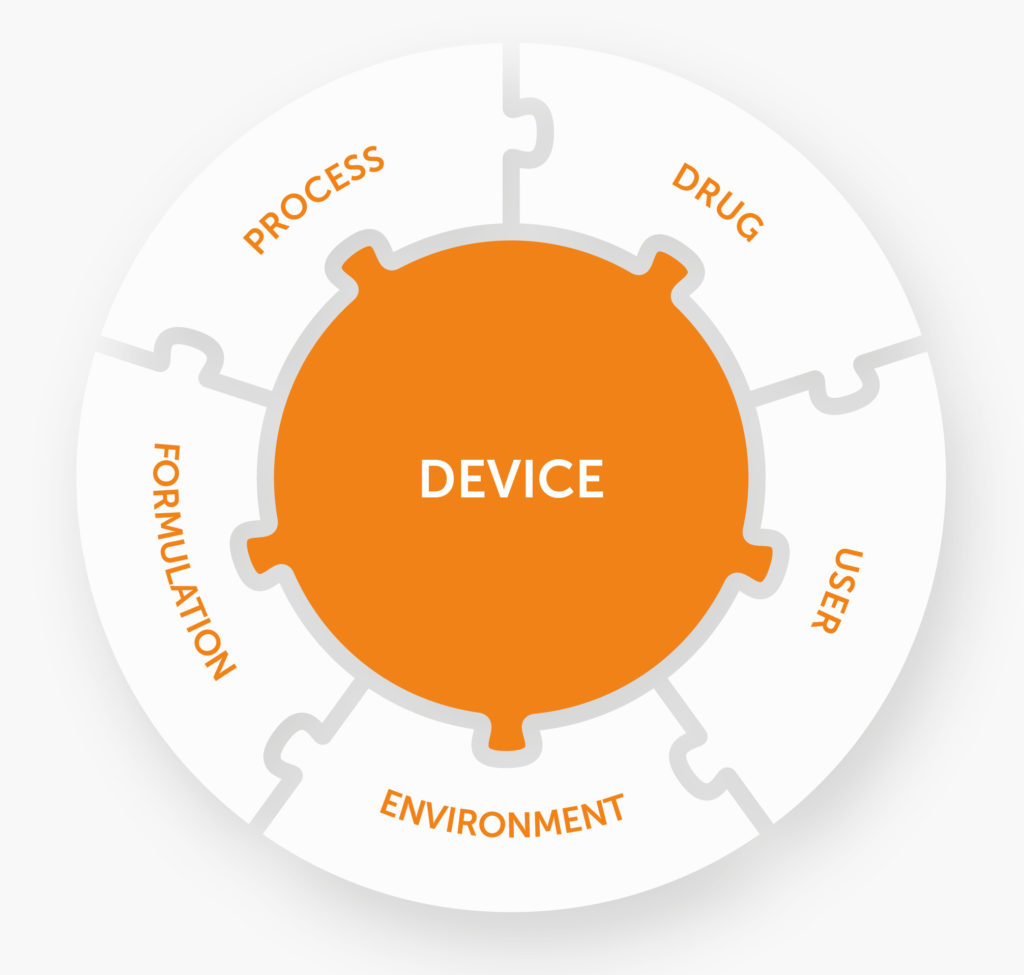
Figure 2: Parts of the multidisciplinary product development project.
The different parts are intimately interlinked, and all contribute to the function and performance of the product. The device, drug and formulation are physical parts of the product, whereas the user, operating environment and manufacturing processes are more abstract parts.
Drug
The main objective of an inhalation product is to deliver the drug to the patient’s nose, airway or lungs. Therefore, the drug drives many of the other features and requirements. The chemical and physical properties, together with the pharmacodynamic and pharmacokinetic properties of the drug, are the key selection criteria when developing the product. These factors also have a strong impact on the most suitable formulation and type of device. The potency of the drug drives the dose size and drug content in the formulation. The drug also dictates what kind of protection is required from the device – moisture, light, oxygen, etc.
“A key challenge is to set up a relevant and comprehensive product
specification for the inhalation product.”
User
Another aspect to consider is the user or patient. The patient population with diseases commonly treated by the delivery of a drug to the lungs is very heterogeneous and expected to be even more so in the future. On the one hand, patients with asthma, who are traditionally treated by inhaled drugs, often start using inhalation devices in childhood. Patients with COPD, however, are often introduced to inhaled therapy at a mature age. When developing inhalation products for this wide, heterogeneous and sometimes multi-disease patient population, patient needs and preferences must be thoroughly investigated and understood. This includes not only hard parameters like inhalation effort and inhaled volume, but also soft parameters such as handling, dexterity and user interface.
The best way of collecting this type of information is to conduct extensive user studies. Such studies should include both practical tests of usage of different inhalation devices and interviews. The test groups must be sufficiently large and representative in terms of age, gender, disease and prior inhaler experience. The studies should preferably be conducted in all countries where the product is intended to be launched. In addition to patients, healthcare professionals should also be included to give their perspective. It is obvious that such an extensive study will be very costly and time consuming. The study can be reduced if a body of knowledge is available within the company, which has been gained by long tradition and experience from products on the market. A great deal of information can also be accessed in the literature. However, there is an obvious risk associated with a too-retrospective approach when developing new products for new patient groups.
Operating Environment
An inhalation product will be used in many different climates in terms of RH and temperature. The product will also be stored at these conditions for an extended period. Many products have a shelf life of two years and an in-use life of several months. The drug and formulation must thus be chemically and physically stable during this period and the device must provide sufficient protection from adverse environments. The question is whether the device provides sufficient humidity protection or if an additional over-wrap is required. There could even be a need for a desiccant in the device or in the wrap. A critical question is whether the device should be adapted or if the moisture sensitivity can be managed by formulation modifications.
Formulation
The formulation is, in a sense, the “blood” of an inhalation product. The function of the formulation is to enable the handling and delivery of the drug to the patient. The formulation is very sensitive to the quality of the various ingredients, the properties of the drug and the composition. The development of a formulation also includes the selection of process equipment (e.g. the mixer) and the optimisation of all the running parameters. When developing an inhalation product, the ambition is often to use the same type of formulation with many different drugs in the same device. There are many different types of formulations, and they each require the appropriate device. The device and the formulation are intimately interlinked and must be developed and optimised together.
Device
The device is what brings all the other parts together. The device should accommodate all the requirements of other parts, including ergonomics, performance, stability, robustness and manufacturing. The role of the device is to house and protect the formulation and meter-disperse-deliver the dose. The design of the device is also the user interface and defines the user sequence. Industrial design is used to develop the exterior shape, graphical design, texture, visual expression and so on. All the mechanical requirements, such as tolerances, assembly sequence, manufacturing processes and materials, are also defined by the device.
It is obvious that a thorough knowledge of all the other five parts is required in the development of the device. Developing a device includes all the traditional mechanical design tasks that are common to all complicated plastic devices. However, in an inhalation device, several tasks and challenges are added. Things like flow resistance, drug retention on the surfaces and fluid dynamics must be included and addressed. To succeed with such a multidisciplinary development, a very eclectic team must be formed
Manufacturing Process
When the formulation is put into the inhalation device, filling equipment is always needed. The filler must be compatible with both the formulation and the device. It should also be compatible with variations of the formulation for when a different drug is used. The filling, and other processes like heat sealing, will be a strong contribution to the manufacturing yield and capacity.
The total cost of the product is also strongly dependent on the manufacturing processes and the process equipment. Much of the CMC documentation is related to the various processes that require extensive validation and verification. Due to the high cost of development, the same inhalation device and manufacturing equipment is often intended for many different drug products. This gives another layer of complexity to the development.
A major challenge is the journey from simple bench-top technical equipment used during development to the GMP equipment used to produce the clinical trial supplies – and, finally, to high-capacity commercial equipment. It is a delicate task to balance development risk against financial risk. From a development point of view, it is advantageous to scale up the process as soon as possible to reduce the risk. From a financial point of view, it is preferred to delay the investment as much as possible to reduce the financial risk.
INEXTRICABLE PERFORMANCE
The different parts discussed above interact and together give the performance of the product. The interaction between the physical product parts is very complex and their individual contributions to the performance are inextricable. On top of which, the interaction with the user is an additional factor – pharmaceutical products are highly regulated, and the inhalation product must deliver the same performance independently of the user’s inhalation effort and inhalation profile.
The dose from an inhaler can be described in terms of delivered dose, respirable dose and respirable fraction. To maintain the same respirable fraction, the particle-size distribution must be the same for every dose. To achieve consistent particle-size distribution, the formulation must be consistent and the device geometry variations very small. To have a high delivered dose uniformity, the properties of each individual dose must be the same for each inhalation, each patient and each manufactured batch. It must also remain the same over time, independent of the storage conditions. When an inhalation device is intended as a platform for many different drug products, the performance should be the same for all drugs and all dose strengths. Needless to say, it is extremely challenging to meet all these performance requirements – and performance testing is the most labour-intensive task during development.
REGULATORY VERSUS MANUFACTURING REQUIREMENTS
The regulatory requirements have a strong focus on patient safety and consistency of performance. The patient should always get the same dose, irrespective of how the inhalation product is used and how it has been stored. The regulatory requirements drive the complexity and quality standards of the inhalation product. When designing the mechanics of an inhalation device, there are two sets of regulatory requirements.
One set is the functional requirement – i.e. the mechanical function of the device. This requirement has the nature of pass or fail – either the inhalation device fits together and works according to specification or it does not. If the design fails these tests, the product cannot be approved and launched. The mechanical function can be tested and verified without the formulation. The design should be robust enough to be able to accommodate small dimensional variations without failing. The allowed dimensional variations are defined as tolerances. To reach a high yield or process capability (Cpk), which is desirable from a manufacturing and cost point of view, the tolerances should be as wide as possible.
The other set of requirements is the performance requirements. Performance requirements must be tested with the formulation and include delivered dose uniformity, fine particle dose, chemical stability and physical stability. The actual value in the requirement is not absolute and is a matter for clinical trials and discussions with regulatory agencies. There are guidelines to adhere to, but many performance requirements are not covered in the guidelines.
There is a conflict emanating from the two sets of requirements. For instance, some dimensions in the inhalation device require one tolerance for the mechanical function and a different tolerance for the performance. As an example, the functional tolerance could give a high Cpk of 1.8. This is the process capability of a mechanically functioning inhalation device – i.e. no formulation included and no pharmaceutical performance tested. This variation in dimension could, however, lead to a high variability in performance.
This could, for example, be the gap between two parts forming a duct. The duct has no mechanical function but governs the dispersion of the formulation and the inhalation resistance. To achieve acceptable performance uniformity, this tolerance must be tighter. However, the new tolerance will decrease the Cpk to, for example, 1.5. It could then be the case that the uniformity could be improved even more, decreasing the Cpk to 1.0. A low Cpk will lead to a high manufacturing cost. The increased manufacturing cost will, in the end, reflect on the price and profitability of the product. The higher cost will eventually be covered either by a lower profit margin for the producer or a higher cost for the payer. The sponsor is facing a delicate trade-off between performance and cost.
CONCLUSION
The development of an inhalation product poses many serious challenges. Most of the challenges have their origin in the complex interaction between the different parts of the inhalation product. To keep down the development costs and minimise project delays, it is important to have a thorough understanding of the inhalation product. This requires an eclectic combination of skills, including pharmacy, engineering, chemistry and physics. A good understanding of the regulatory requirements, together with clinical and pharmacological experience, is also very valuable. This required skill base should be considered when forming project teams.
A key challenge is to set up a relevant and comprehensive product specification for the inhalation product. It is time well spent to have a thorough analysis of the various consequences of each requirement. An incompatible or over-ambitious set of requirements can have tremendous ramifications on the development. The consequences may not become obvious until late in the development and then lead to extensive redesign and delays.
Previous article
STEPS TO SUCCESS IN NOSE-TO-BRAIN DRUG DELIVERYNext article
COULD VIVERA BE THE NEXT MEDTECH UNICORN START-UP?