Citation: Jarman-Smith M, Salmen A, Devine J, Hupkes E, Freie D, “Connected Devices Challenge: How to Develop Concept Devices with PEEK Polymers”. ONdrugDelivery Online, September 13, 2021.
Marcus Jarman-Smith, Adam Salmen, John Devine, Ernst Hupkes and Dennis Freie discuss the value of PEEK, a high-performance polymer, in drug delivery device design, using two concept devices – an on-body patch pump and vaporiser inhaler – designed by Tricas, an advanced device design consultancy, to illustrate the practical benefits of PEEK.
Drug delivery devices place significant demands on the materials used for their construction. Materials suppliers in the sector need to work even harder to drive innovation, respond to new formulations, and provide enhanced functionality.
Device designers and engineers need more choice in their materials toolkit, and high-performance polymers, such as polyether ether ketone (PEEK), can offer an additional material choice to solve complex device design challenges or for scaling up a device for mass production in a cost-effective way.
One of the easiest ways to understand this complex topic is to view polymers as a pyramid. This identifies three major categories of polymers: high-performance polymers, engineering polymers, and commodity polymers (Figure 1). When your drug delivery application demands multiple engineering requirements, Victrex high-performance polymers can help overcome complex design and engineering challenges.
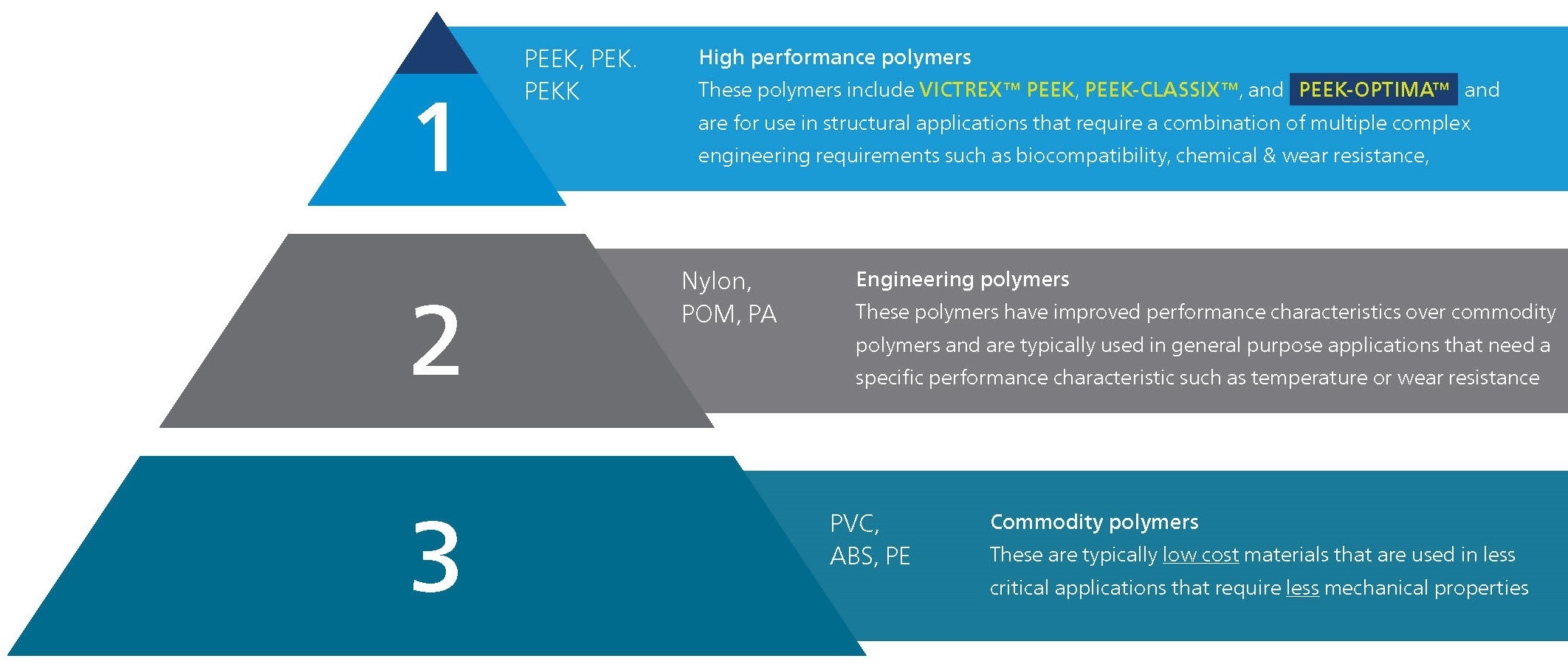
Figure 1: High-performance polymers such as PEEK and PAEKs are used in applications with multiple, often complex engineering requirements.
Polymers can open up new options without the material being new – PEEK is tried and tested, having been commercialised by Victrex in the early 1980s. Many of PEEK’s properties that are already being exploited in industries such as oil and gas, aerospace, electronics, medical and automotive are relevant to the increasingly complex and multi-component systems we see in modern drug delivery devices (Table 1).
Conditions | Test Method | Units | Typical Value | |
Tensile Strength | Yield, 23°C | ISO 527 | MPa | 98 |
Tensile Elongation | Break, 23°C | ISO 527 | % | 45 |
Tensile Modulus | 23°C | ISO 527 | GPa | 4.0 |
Flexural Strength | At 3.5% strain, 23°C | ISO 178 | MPa | 125 |
At yield, 23°C | 165 | |||
125°C | 85 | |||
175°C | 19 | |||
275°C | 12.5 | |||
Flexural Modulus | 23°C | ISO 178 | GPa | 3.8 |
Compressive Strength | 23°C | ISO 604 | MPa | 125 |
120°C | 70 | |||
Charpy Impact Strength | Notched, 23°C | ISO 179/1eA | KJ m-2 | 1.0 |
Unnotched, 23°C | ISO 179/1U | n/b | ||
Izod Impact Strength | Notched, 23°C | ISO 180/A | KJ m-2 | 8.0 |
Unnotched, 23°C | ISO 180/U | n/b |
Table 1: Table of material properties of VICTREX™ PEEK 450G unfilled PEEK polymer.
CONCEPT DEVICES DESIGNED WITH PEEK
“To demonstrate the potential of PEEK in innovative drug delivery device design, Victrex challenged the product design engineers at Tricas, who have a broad knowledge of materials, to design two concept devices made with performance-enhancing PEEK components.”
There are a variety of ways in which PEEK can be integrated into drug delivery devices. To demonstrate the potential of PEEK in innovative drug delivery device design, Victrex challenged the product design engineers at Tricas (Zwolle, Netherlands), who have a broad knowledge of materials, to design two concept devices made with performance-enhancing PEEK components. These concept devices consider the limitations of materials such as metals and commodity polymers and apply the performance advantage of high-performance polymers to solve commonly encountered challenges.
High-Performance Polymers
Firstly, let’s look at the material itself. PEEK is a high-performance polymer. PEEK is part of a larger class of semi-crystalline thermoplastics called polyaryletherketones (PAEKs). PEEK has many properties that are attractive for the medical sector, including drug delivery device designers and manufacturers, such as biocompatibility and chemical resistance, as well as enabling integrated functionality and streamlining manufacturing processes for smaller, thinner, lighter devices. As a result, PEEK has the potential to drive cost savings for the manufacturer.
Designers often have a long list of requirements and selecting a material that can address them all can be challenging. Unsurprisingly, the more requirements a designer has, the shorter the list of materials able to meet all of them. As such, designers are increasingly looking to the field of high-performance polymers for answers. For example, implantable PEEK can offer all the benefits of non-implantable PEEK, such as VICTREX™ PEEK, but in addition has biocompatibility and, with specific grades, radiolucency. Without a doubt, PEEK is one of the highest performing polymers on the market, able to support multiple key engineering requirements. PEEK is used to enable design freedom and offers excellent mechanical properties, such as stiffness, toughness and durability as well as chemical resistance and the ability to be repeatedly sterilised, without degradation.
CONCEPT DEVICE 1: SMART WEARABLE PATCH PUMP
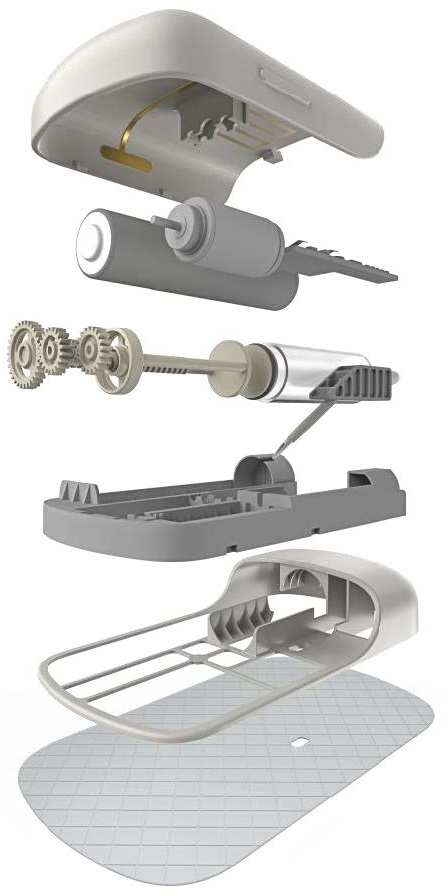
Figure 2: Concept for a next generation wearable patch pump device, designed by Tricas using smart technology made with VICTREX™ PEEK components. (Image © Copyright 2021 Victrex PLC)
The first device developed by Tricas is a smart, wearable patch pump that is semi-reusable and is worn on the body (Figure 2).
“Some of the challenges that on-body patch pumps currently present come from developing a high-precision dosing system, integrating a large or complex printed circuit board (PCB), and employing materials that are biocompatible and able to sustain frequent wear over a long period of time. There are multiple ways in which PEEK polymers could conceptually overcome these challenges.”
Some of the challenges that on-body patch pumps currently present come from developing a high-precision dosing system, integrating a large or complex printed circuit board (PCB), and employing materials that are biocompatible and able to sustain frequent wear over a long period of time. There are multiple ways in which PEEK polymers could conceptually overcome these challenges.
Subcutaneous Delivery and Skin Contact Components
The drug container is biologically inert, resistant to a variety of chemicals and concentrates, and has good dimensional stability – even at high temperatures, thanks to its low moisture absorption. By using a medical grade PEEK, it is possible to design a biocompatible cannula that can pierce the skin and safely be in contact with a range of human tissue types for an extended period without the risk of releasing leachables or toxins into the patient (Figure 3).
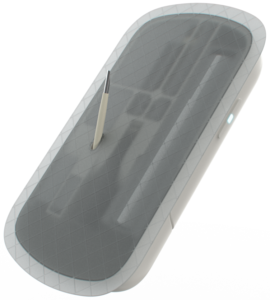
Figure 3: Biocompatible cannula system designed by TRICAS made with VICTREX™ PEEK films and polymers. (Image © Copyright 2021 Victrex PLC)
Victrex’s medical grades of PEEK (PEEK OPTIMA™ and PEEK CLASSIX™) have an extensive master file of clinical evidence. More than 13 million devices have been made with PEEK-OPTIMA™ polymers, including load bearing spinal fusion cages that sit close to the spinal cord and metal-free active implantable electronic medical devices such as neuromodulators.
Plunger and Gear Drive System
The plunger system is the driving force behind the patch pump’s dosing mechanism. Here, it’s a PEEK spindle construction with gears. The system is able to function without any stick-slip or wear and tear, which means that it can operate for a long time without risk of particulation or sloughing-off. The PEEK components are highly accurate for precise dosing, but are also able to be miniaturised through injection moulding. PEEK is a well-suited material for this function due to its tribiological characteristics and chemical resistance.
PEEK also has a low coefficient of friction, so is resistant to wear and abrasion when used for moving components such as micro-gear systems. Victrex PEEK is used in high-wear applications such as bushings, bearings, seals and rollers, and can retain dimensional stability during repetitive use, even in extreme environments. Furthermore, when fillers such as polytetrafluoroethylene (PTFE) and carbon fibre are added to PEEK, the wear performance is further enhanced and can be applied to components that operate at high speed or under high load (Table 2).
Natural PEEK | Wear-grade PEEK | Implantable PEEK | |
Use case | Standard flow for injection moulding and extrusion for complex parts. | Filled with carbon fibre, graphite and PTFE for components that operate under high speed or load conditions. | Radiolucent high-performance polymers that will be in contact with or implanted into the human body. |
Application areas | Drug cartridges, casings, electronics | Gears, pumps | Cannula systems, skin patches, oral delivery systems |
Table 2: Impact on wear performance when additives are added to PEEK polymer compounds.
Figure 4 shows a gear that is designed according to standard gear design principles, with teeth, central bearing and connecting ribs. Tricas used finite element analysis to show that, when stress or force is applied, a lot of the material is not used to transfer these forces. When optimised with PEEK, there are much smaller ribs connecting the outside ring to the central bearing, resulting in a nice flow of force through these tiny ribs. For reference, the ribs themselves have a cross-sectional area of 0.3 mm by 0.5 mm – with the potential to go even smaller.
These gears are extremely small and, because the device is designed to be worn on the human body, minimising its weight is important. In this example, by using PEEK it is possible to achieve a 20% reduction in weight.
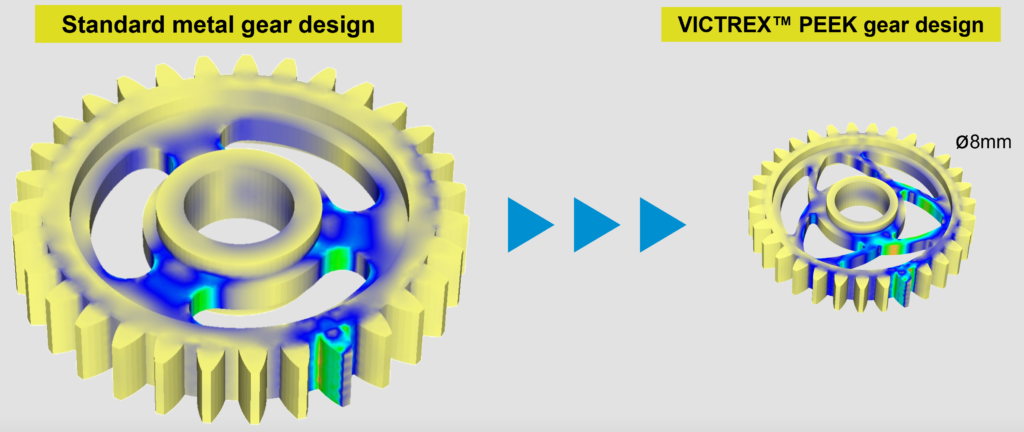
Figure 4: Tricas comparative analysis found that PEEK creates a 20% volume reduction, and improved force distribution when compared with a metal gear design.
Integrated Structural Electronics
Integrated structural electronics is a space-saving concept that uses Laser Direct S-sintering (LDS) into a compatible material. This technology is often used by the innovation team at Tricas to integrate communication or intelligence into devices. In this concept, the electronics are sintered directly into the casing to create an antenna to communicate wirelessly via Bluetooth. This eliminates the need for a PCB, thereby increasing the available space within the device so that it can hold larger volumes of drug or be further miniaturised.
In the antenna, PEEK has good dielectric properties with a very low dissipation factor, with only small amounts of electrical energy absorbed by the PEEK material. This makes PEEK radio transparent and allows the design to have an antenna on the inside for connecting to a smartphone or other device.
The advantage of adding antenna tracks directly onto the surface of the material, as shown in Figure 5, is that these antennas have great operational stability. They are not in a separate component with its own assembly tolerances, but instead are part of the device’s casing with a consistent thickness of material between them and the outside world.
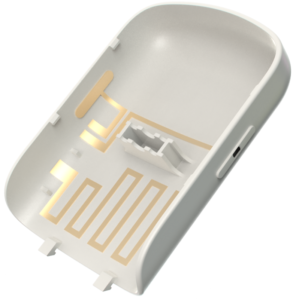
Figure 5: Structural electronics integrated into a PEEK enclosure, eliminating the need for PCB. This enclosure is designed by Tricas to maximise the potential of VICTREX™ PEEK. (Image © Copyright 2021 Victrex PLC)
Sensor and Capacitive Switch
For many years PEEK film (such as Victrex’s APTIV™ film) has been used to create tactile switches and touch sensors. Again, the dimensional stability of PEEK makes switches reliable, able to retain their strength even after repetitive depressions. In the patch pump concept, the touch sensor could be used to dispense the drug precisely, using pressure to dictate the strength or volume of drug to be released. By applying PEEK film behind an LED, the capacitive switch could be made into a smart switch, perhaps by blinking to notify the user of changes to temperature, battery life or connectivity.
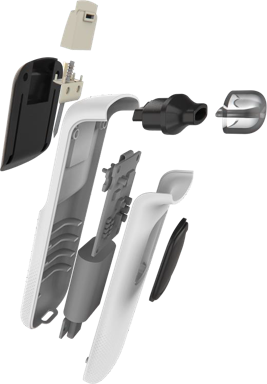
Figure 6: Concept for a next generation inhalation device, designed by Tricas using smart technology made with VICTREX™ PEEK components. (Image © Copyright 2021 Victrex PLC)
CONCEPT DEVICE 2: ADVANCED VAPORISER INHALER
The vapouriser has a much smaller drug container than the patch pump concept, with thin walls, that is changed more regularly and therefore needs both to have good mechanical stability and to maintain precise dosing even when in close proximity to a heated environment. Nearly all the components in the device have the potential to be made with PEEK. Here we will look at the three components where PEEK would have the most significant performance advantage over metals or commodity polymers. The second concept device that Tricas designed is a next-generation inhaler (Figure 6). Unlike the patch pump concept where the liquid drug is delivered subcutaneously via a mechanical system, this device uses heat as the drug delivery method to vapourise the drug concentrate for inhalation.
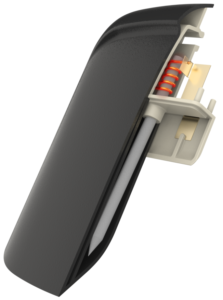
Figure 7: TRICAS designed components with VICTREX™ PEEK thin-walled housings in close proximity to a heating element part of a vapourising inhaler system. (Image © Copyright 2021 Victrex PLC)
PEEK is a thermal insulator and doesn’t degrade when exposed to heat like other polymers. Normally, to cope with proximity to the vapouriser’s heating element, operating at 100–200°C, the device would need to be made bigger to allow for heat distribution across a larger surface area and increase the distance between the heating elements and the housing. Since PEEK is designed to function in extreme environments, it is possible to reduce the size of the device by miniaturising it and by designing thinner walls (Figure 7). These valuable space and weight savings present an interesting opportunity to improve the ergonomic design, and potentially aesthetic, design to make the device more appealing to patients.
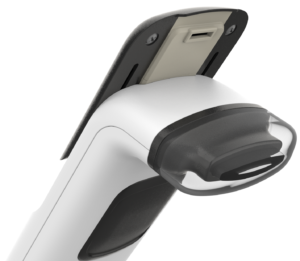
Figure 8: Concept designed by TRICAS for a mouthpiece made with biocompatible PEEK polymer that can cope with repeated use under hot, wet conditions whilst maintain secure airflow. (Image © Copyright 2021 Victrex PLC.)
Biocompatible Mouthpiece
Similar to the patch pump’s cannula, the mouthpiece is going to be in direct contact with human tissue (Figure 8). In the inhaler, the vapourised drug will pass through the mouthpiece, so material selection becomes of key importance.
It’s critical that the mouthpiece retains good dimensional stability under repeated use and heat to create a secure airflow channel between the vapor inhalation chamber and the mouthpiece, otherwise condensation will become a problem – having the potential to be absorbed by many materials and create unwanted vortices in the airflow. PEEK has very low moisture absorption, so designing with PEEK could eliminate any concerns here.
Chemically Resistant Drug Cartridge
In the inhaler concept device, the drug cartridge is designed to slide onto the back of the device. As such, it needs to be able to move up and down, be taken off and be put back on – and not always at room temperature. With this device it is important to consider that, when changing the drug cartridge, part of the system may still be warm or moist from the vapor, and so sliding action still needs to be smooth even under these circumstances.
In drug delivery devices, degradation of the reservoir is unacceptable. PEEK offers a safe alternative to commodity polymers, metals and glass which can potentially leach or extract chemicals. Furthermore, if mechanical strength is required, then PEEK parts can be designed to meet this key engineering requirement.
PEEK is inert and, as was key to the patch pump concept, has little to no leachables, which allows it to be in contact with aggressive chemicals or drugs without unwanted chemical interactions occurring. This remains true whether PEEK is used in the form of packaging or as a part of the drug delivery pathway. Additionally, PEEK can handle the extremes of liquid drugs at various viscosities, including new-generation biologics.
CONCLUSION
There are many ways in which PEEK polymers can be integrated into next generation drug delivery device designs, or used to optimise existing systems. Also, because it can be processed by injection moulding, it is possible to deliver very small parts with an exceptionally high degree of accuracy with tight tolerances, making it a competitive option for a wide range of drug delivery applications.
Whilst there are materials that can address some of the individual engineering requirements discussed, such as weight or electrical insulation, when multiple features are needed to push a design to its limits – then high-performance polymers could help solve the challenge.