Citation: Jaworski W, Gunner M, “Relentless Precision Delivers Value in Needle-Handling Automation for Combination Products”. ONdrugDelivery, Issue 125 (Oct 2021), pp 56–59.
William Jaworski and Michael Gunner discuss the precision and complex manipulation of needles required for the latest combination medical products.
The ageing global population, combined with the burden of chronic disease and new investment in novel pharmaceutical therapeutics, has led to dramatic growth in parenteral drugs over the last decade. Syringes are still commonplace in drug delivery. However, the global demand for complex injection devices is growing rapidly.
Today’s drug delivery devices are elaborate. It does not matter if the device is a peripheral venous catheter, a syringe, a pen injector, an autoinjector or a wearable injector (pump), the most common element in each device – and arguably the most important – is the needle. In fact, although it begins as a blank stainless-steel rod, by the time a patient uses the injection device, the needle has undergone a dramatic transformation.
The wide variety of needle customisations presents a unique challenge. Blank needles are not very precise products. They are a raw commodity with imprecise lengths, uneven wall thicknesses, varying bevel angles and other imperfections. Many needles are bowed or have a preset bias due to how they are formed during the metal drawing process. Typically, they are mass produced and have been historically used at the end of a simple syringe. For most syringe applications, slight variations have not traditionally been of much concern.
“The latest medical devices require significantly greater precision and complex manipulation of needles.”
The latest medical devices, however, require significantly greater precision and complex manipulation of needles. Due to the high demand, mechanical complexity and ever-decreasing size of these advanced medical devices, manufacturers have turned to automation to aid in their assembly. A variety of needle handling capabilities that may be required for complex medical devices is summarised in Box 1 (below).
Based on the customer’s design, the length, gauge and tip of the needle will vary widely from device to device. Some require systems that handle needles as fine as 31 gauge (0.261 mm in diameter) or about twice the thickness of a human hair, while others are built around significantly larger needles, such as 16 gauge (1.651 mm). The bevel angle on the tip of the cannula is also customised based on a customer’s specific design. This becomes critical, as the bevel of a needle in most complex devices becomes a key reference for the assembly. Mikron systems account for the smallest of bevel inconsistencies among thousands of blank needles.
In a typical automation solution for the assembly of drug-delivery devices, thousands of needles must be processed in order for the system to attain the required production rate. Needles are typically fed into the system via a hopper or a specifically designed cartridge and then readied for individual selection. One method of creating this “singulation” is by means of a rotating drum which provides the means to select one needle into well-defined grooves with a vacuum assist. This allows Mikron to present individual needles to the system at speeds of up to 2,000 needles per minute. Through years of experience, Mikron has developed technology to optimise the hopper and drum design to compensate when needles are warped or stick together from surface lubrication or from simple static electricity.
“At Mikron, even the “simple” process of feeding the prepackaged needles into the machines is scrutinised for precision to ensure meticulous automated assembly.”
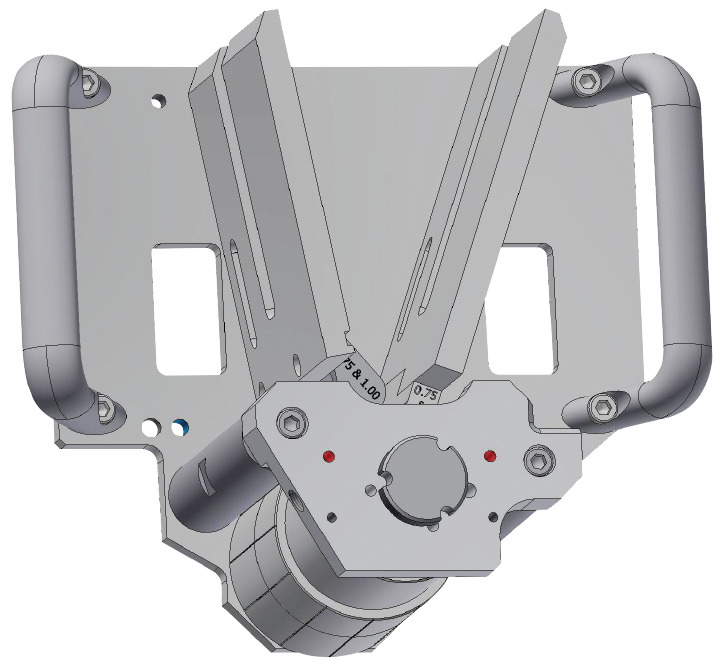
Figure 1: An example of a cannulator with V-shaped hopper for singulation of bulk needles.
At Mikron, even the “simple” process of feeding the prepackaged needles into the machines is scrutinised for precision to ensure meticulous automated assembly – a standard in keeping with the celebrated tradition of exceptional Swiss watchmaking. The feeding system (Figure 1) features operator handles for transportation and manual loading, as well as a V-shaped hopper that feeds blank needles through the cannulator.
After singulation, the individual needle is presented and tested by a vision system that inspects needle attributes including – but not limited to – length, needle position, bevel angle and seam location. Mikron, as an industry leader in machine vision, deploys accurate and repeatable vision solutions with its in-house experts, using the latest technology, such as 21 MP cameras, providing micron-level precision (Figure 2). The results of the vision inspection are important assembly requirements as the needle is transformed into a precise medical device.
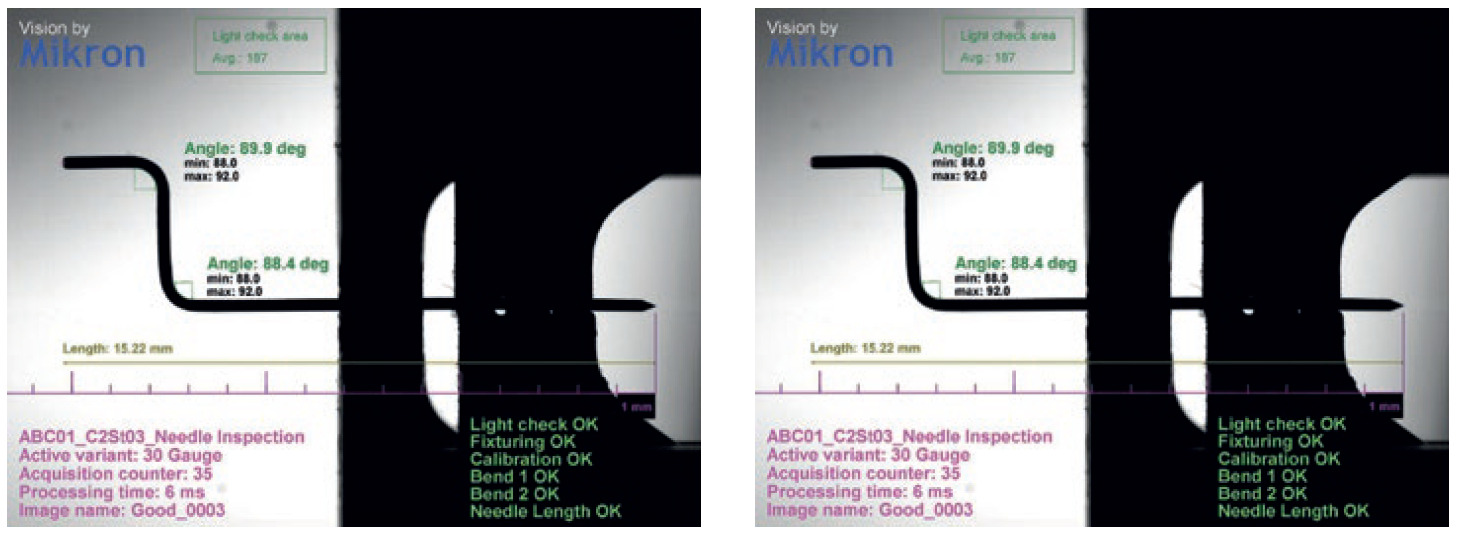
Figure 2: Mikron has become a leader in machine vision and the deployment of high-speed inspection systems to verify needle processing.
The next operation of a single cannula for a complex device is often to change its shape dramatically. However, the bending of a needle presents its own set of complexities. Due to their initial forming through the drawing process, stainless-steel needles undergo intense strain hardening and become extremely hard. Specialised tooling must be designed for parts of the system that handle and come into contact with the cannula to minimise premature wear, thus ensuring long-term performance.
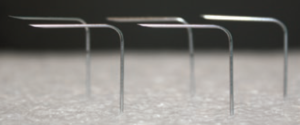
Figure 3: To ensure 100% safe use and functionality of the medical device, precise and repeatable needle bending needs to accommodate the input of imprecise bulk needles.
As this specialised tooling firmly grips the needle, the system will carefully bend the cannula around the tooling or mandrel to form the required bend angle (Figure 3). Through its experience and understanding of the steel’s elastic properties, Mikron knows precisely how much to overbend the cannula so that it can then relax to exactly the desired angle. Some designs require multiple bends of the needle, and others may require bending in several dimensional planes, resulting in a very complex shape with compounding tolerances (Figure 4). The complexity and precision are even further challenged by the speed of the system, which can achieve up to 40 cycles per minute.
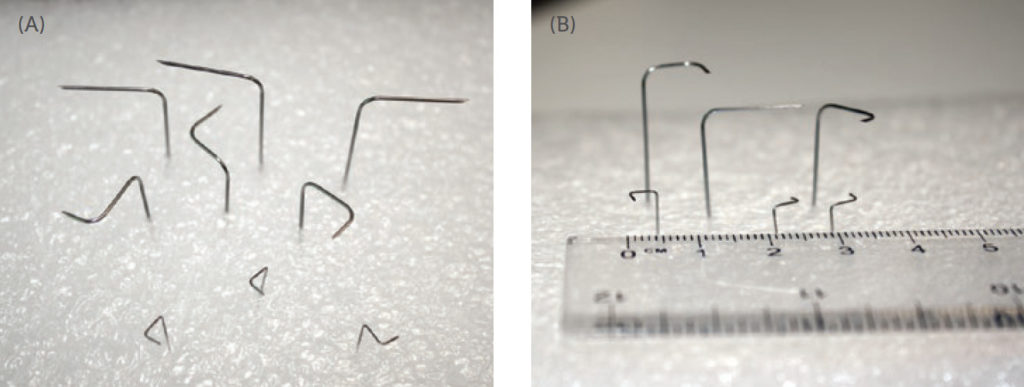
Figure 4: Complex geometries (A) and thinner and smaller cannulas (B) mean that needle handling is challenging and demands expertise for the design of the process station.
Verifying the quality – that the process step completed was successful and within specifications – can be just as challenging as the operation itself. At this point in the process, Mikron verifies that no damage has occurred during needle transformation, verifying through vision, for example, that the needle tip has not been damaged.
Other types of in-process checks, such as occlusion and flow tests, also be deployed to ensure quality. These checks verify the integrity of the newly transformed needle and the fluid path prior to assembling the formed needle into the main device. This process helps confirm that the pharmaceutical formulation will travel uninhibited through the needle to its intended destination.
As part of a drug-delivery device design, needles in many instances require the application of a coating that, for example, may minimise patient discomfort. Mikron has leveraged its experience in microdispensing of fluids to apply a fine and homogenous coating of these required substances to needles. In many ways, this precise process is one of the more intimate, as it is where the system can impact the patient’s experience with the device the most.
“Transforming an imprecise cannula into one with complex geometries with fine dimensional tolerances of up to ±200 microns has become a differentiating strength of Mikron.”
Not only are these processes intricately challenging but the need for ever-sophisticated device designs is also growing rapidly. Transforming an imprecise cannula into one with complex geometries with fine dimensional tolerances of up to ±200 microns has become a differentiating strength of Mikron. Its specialised knowledge and process understanding helps ensure its systems repeatably produce quality needle products for complex drug-delivery devices.
“Mikron supplies precision-focused automation solutions with the highest productivity.”
Mikron has more than 100 years of experience in designing and creating dependable automated solutions. Today, Mikron has not only become a global leader in terms of scale and volume – it has also become a preferred option for the most difficult, complex and unique projects. Mikron supplies precision-focused automation solutions with the highest productivity, meeting the needs of some of the largest medical device and pharmaceutical customers worldwide.
Rooted in the Swiss culture of precision and innovation, Mikron Automation enables its customers’ success through expertise in optimising product development, deploying scalable manufacturing solutions and providing post-installation care.
BOX 1: NEEDLE HANDLING
Mikron Automation has experience with the following needle assembly requirements:
- Format: bulk, “sushi rolls”, cassettes
- Speeds: 1–1000 ppm
- Gauges: 16–31
- Lengths: 0.625–3.0” (1.588–7.62 cm)
Final geometry:
- Straight/standard
- Single bend
- Multiple bend
- Multiple planes
- Push-pull test
- Flow test
- Leak test
- Occlusion test
- Microdispensing adhesives
- LED UV spot curing
- UV tunnels
- Platform:
– Cognex
– Keyence
– Shaman - Typical inspected attributes:
– Needle length
– Bend length
– Needle orientation
– Seam location
– Gauge verification
– Bevel dimension
– Tip quality