To Issue 131
Citation: “Technology Showcase: Testing Solutions for pMDI Drug Development”. ONdrugDelivery, Issue 131 (Apr 2022), pp 55–56.
“The insight gained into product performance can be used long after product approval to investigate and resolve any out-of-specification or out-of-trend disruptions to manufacturing.”
Pressurised metered dose inhalers (pMDIs) are a class of combination drug products dependent on the optimisation of a formulation, device design and human usage to deliver an accurate, reproducible dose. In the case of pMDI suspension products, the shaking profile is crucial for accurate dose delivery. Lack of appropriate shaking can deliver a high amount of the drug in the early doses followed by very little or no drug towards the end of the product’s life. Other important influencing factors on pMDI performance include force-to-actuate and hold time to ensure that the metering valve is open long enough to deliver a complete dose. A minimal shake-to-fire delay is another crucial factor for maintaining the uniformity of the delivered dose (Figure 1).
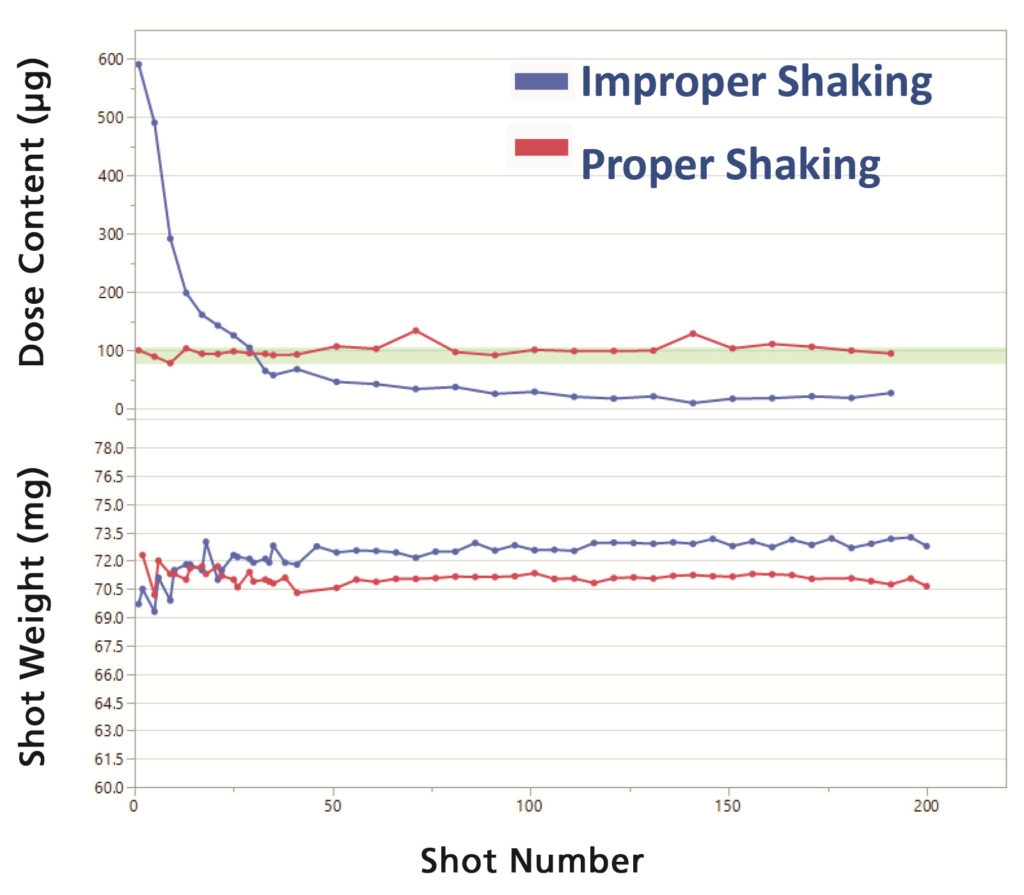
Figure 1: Example of dose content and shot weight for a suspension pMDI product with improper and proper shaking.
COMPLETE SUITE OF pMDI TESTING SOLUTIONS
Proveris by Design
Based on the quality by design (QbD) approach endorsed by the US FDA, Proveris by Design first provides the basis of experiments to identify the range of human usage parameters of a pMDI according to current regulatory guidelines for in vitro testing. Next, it offers strategies to test the range of design spaces and gain an understanding of the control space: which of these factors have the most impact on product performance? Lastly, it identifies the target operating space and control for key influencing factors in a tight range during the in vitro testing. One of the deliverables of the approach is a sensitivity map based on the design of experiments which shows how much influence certain factors identified in the design space have on the overall performance of the product.
In the R&D phase, clients engage Proveris Laboratories to perform tests using this method to produce consistent, high-quality data efficiently during product development and for preparation of regulatory submissions. The results show an overall reduction in approval timeline and minimised queries from regulatory agencies. Moreover, the insight gained into product performance can be used long after product approval to investigate and resolve any out-of-specification or out-of-trend disruptions to manufacturing (Table 1).
Typical Influencing Factors for pMDI Products | Screening Experiments Category | |
Formulation | Morphology of API (size and shape) Formulation form (suspension/solution) Propellent Excipients |
Performance testing |
Device | Metering valve Actuator (sump geometry) Assembly process |
Component characterisation |
Human Usage | Shaking and shake-to-fire delay Hold time Product actuation force Actuation velocity |
Functional testing |
Table 1: Typical influencing factors for pMDI products and Proveris by Design screening experiments.
Ergo Studies
As a contract test service, Proveris Laboratories offers human-realistic actuation studies performed using proprietary Ergo technology to quantify accurately how trained testers in the targeted population actuate the product. Client device candidates, and/or reference products in the case of generic drug development projects, are evaluated to obtain key actuation parameters, such as stroke length, velocity, acceleration and hold time. This data is fully transferrable to Proveris Vereo automated actuators to enable reproducible actuations in a human-realistic way.
Vereo SFMDx Actuators
As with any pharmaceutical product, it is important to perform in vitro tests with repeatable, reproducible and robust methods for a smoother product development process. Vereo actuators provide fully controllable and repeatable shaking and actuation for commonly required regulatory tests, controlling up to six critical actuation parameters and four additional parameters related to shaking for pMDI devices. The flexible SFMDx actuator fits seamlessly into multiple testing workflows with identical actuation parameters implemented across all tests, ensuring data integrity and accuracy (Figure 2).
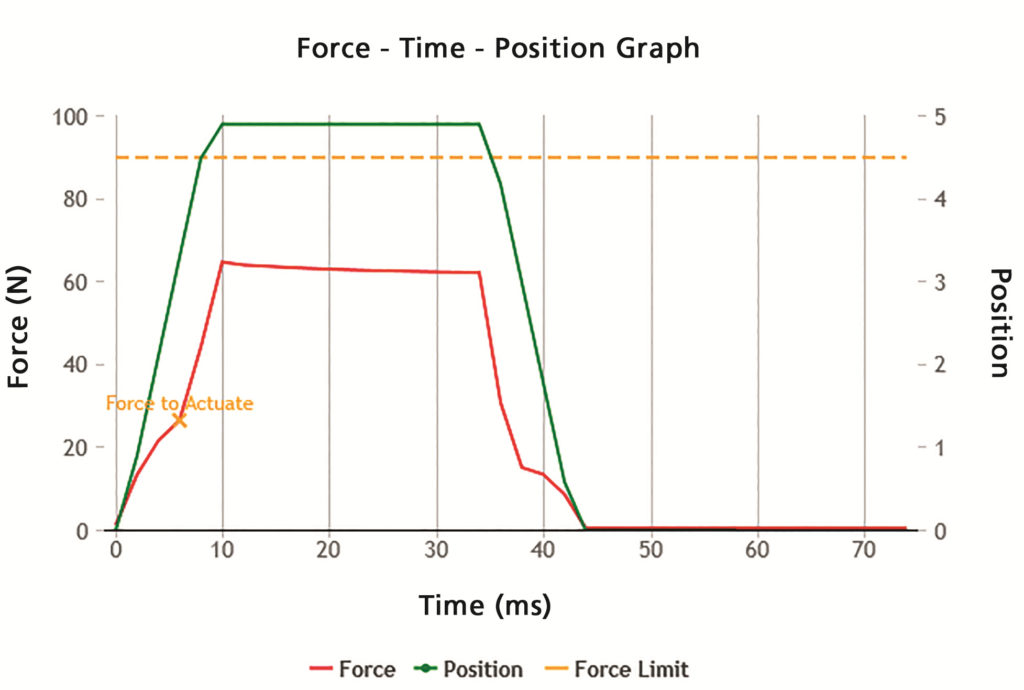
Figure 2: Proveris instrument users can create and evaluate products using force/position versus time plots generated by the system software.
In vitro tests performed using Vereo SFMDx actuators (Figure 3) include:
- Delivered dose uniformity (DDU)
- Single actuation content uniformity (SAC)
- Valve/pump delivery (shot weight)
- Aerodynamic particle size distribution (APSD)
- Droplet size distribution (DSD)
- Spray pattern and plume geometry
- Priming and repriming
- Product wasting for through-life testing
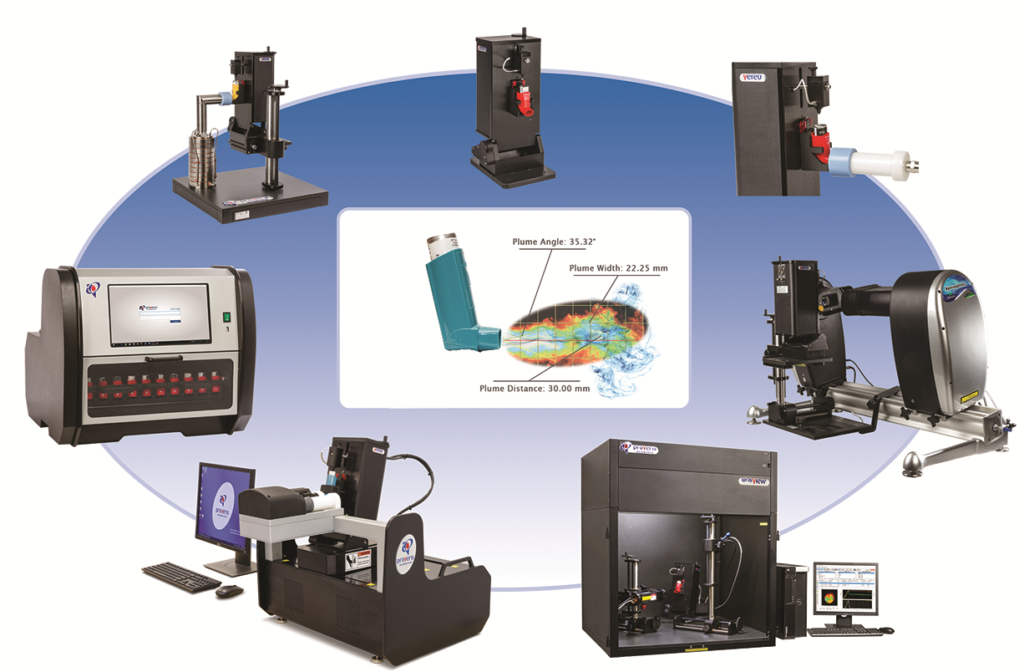
Figure 3: Proveris precision instruments and test workflows incorporate Vereo actuator technology for testing of pMDI products.
New Kinaero Cx pMDI Collection System
The newly introduced Kinaero Cx system easily integrates into DDU and APSD test workflows to automate parameters including shaking, actuation and dose/sample collection in a reliable, repeatable manner using proven Vereo actuator technology. To automate the whole workflow, users can run the Kinaero Cx alongside the Kinaero High-Throughput pMDI Fire-Down System for through-life testing, using a powerful common software platform consistent with full regulatory compliance (21 CFR Part 11).