To Issue 132
Citation: Doorakkers R, van Amstel G, “Smart Solutions to Reduce Carbon Footprint.” ONdrugDelivery, Issue 132 (Apr-May 2022), pp 19–22.
Rob Doorakkers and Geert van Amstel discuss why the company decided to become carbon neutral, how it is working to make injection moulding more sustainable and how the organisation is minimising its impact on the environment.
From Apple and Microsoft to IKEA and Unilever, the largest companies in the world have committed to becoming carbon neutral by 2030. The healthcare industry is no exception; all major players have made plans to make their operations planet-friendly. Those ambitions will have a large effect on the rest of the market too, as suppliers will be required to meet sustainability standards more and more often. IGS GeboJagema has been carbon neutral since 2019. Nonetheless, the company feels it still has plenty of work to do.
“With hundreds of moulds being produced at the IGS factory every year, the impact of more energy-efficient moulds could be highly significant.”
DECIDING TO BECOME CARBON NEUTRAL
There are many reasons to go carbon neutral. Of course, the overarching reason is climate change. The effects of the planet warming more than 1.5–2°C would be ruinous. IGS GeboJagema believes that companies need to take responsibility to reduce and offset their carbon footprint to the best of their ability.
But, to play devil’s advocate for a moment, even companies that are less concerned with the effects of climate change would be wise to make plans to reduce their carbon footprint. An organisation’s attitude and actions related to sustainability have a profound effect on its public perception, including that of suppliers, customers and employees. Companies that fail to move towards carbon neutrality will face increasing difficulties recruiting top talent and attracting new customers. Case in point: several clients have audited IGS GeboJagema through the Ecovadis sustainability assessment. By becoming a more sustainable company, IGS GeboJagema has been able to support its clients as they move towards a measurably and certifiably green supply chain.
In addition, the world is moving towards stricter CO2 laws and regulations, such as carbon taxes. From this perspective, reducing carbon emissions today is nothing more than preparing for upcoming legislation. In short, IGS GeboJagema believes that any serious plan for the future should include a plan to minimise CO2 emissions.
CARBON OFFSETTING
While IGS GeboJagema is carbon neutral, that does not mean the organisation does not emit any CO2. It means that steps are being taken to reduce emissions as much as possible while offsetting the organisation’s current carbon footprint. There are many ways to compensate for carbon emissions. IGS GeboJagema works with Land Life Company (Amsterdam, the Netherlands), which is arguably the fairest and most impactful way to offset emissions. Land Life grows forests in plots of degraded land all over the world, from Europe to Africa, and from Australia to North America. In addition to capturing CO2 from the air, its reforestation efforts positively impact local communities by stimulating their economies, measurably decreasing the temperature and restoring flora and fauna (Figure 1).
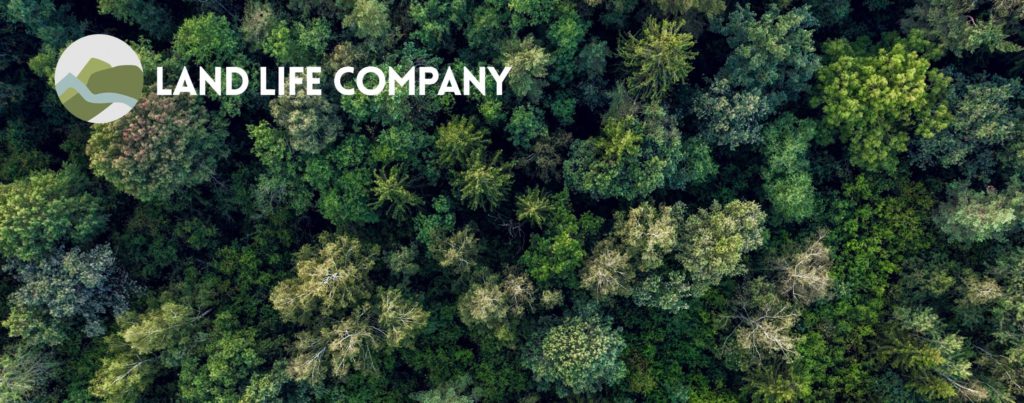
Figure 1: Land Life Company grows forests in plots of degraded land worldwide.
“In total, the difference between the baseline test and the optimised test was an impressive 77%.”
ENERGY-EFFICIENT INJECTION MOULDING
Of course, CO2 compensation is not a long-term solution. While reforestation can delay some of the harmful effects of climate change, it is critical for organisations to reduce their carbon footprint as much as possible. As a mould maker, IGS GeboJagema can make the biggest impact by helping its customers to do exactly that.
Injection moulding requires a lot of heat, making it an energy-intensive process. Depending on its type and size, an injection mould can use between 135,000 and 240,000 kWh per year (assuming an uptime of 95%). To put that into perspective, that is the same amount as 49–86 Dutch households.1 It translates to 72–126 tonnes of CO2 emissions a year.2 With hundreds of moulds being produced at the IGS factory every year, the impact of more energy-efficient moulds could be highly significant.
Taking inspiration from that thought, IGS GeboJagema started a research project. The objective was to investigate whether energy consumption could be reduced by 20% while still retaining product quality and cycle time. A baseline test revealed that two factors made up over 80% of energy consumption:
- Thermolater pump power
- Thermolater heating.
With that in mind, the team investigated several optimisations. First, the team determined that the water flow rate could be reduced from 72 to 26.3 litres per minute, without affecting product quality or cycle time. This allowed for the installation of a less powerful thermolater pump. The amount of energy saved was quite dramatic: a reduction of 45%.
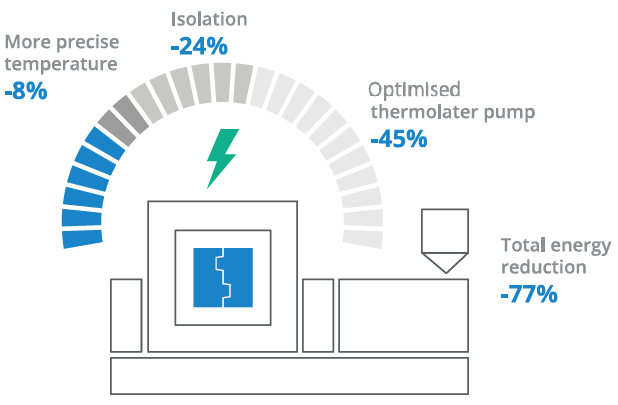
Figure 2: In the optimised test, an energy reduction of 77% was achieved.
Second, to reduce the power used to heat the thermolater, the team wrapped isolating material around the moulds and placed isolation plates between the bed plates. This reduced energy usage by 24%.
Finally, the team found that further savings could be realised by lowering the mould temperature. Plastic suppliers provide a material data sheet that defines a temperature window for their product. Usually, this window is about 20°C. For the baseline test, the temperature was set in the middle of that window. But the team found that it could lower the temperature without affecting cycle time or product quality. This reduced energy consumption by another 8%.
In total, the difference between the baseline test and the optimised test was an impressive 77%. While such dramatic results cannot be expected on all moulds, this research shows that large reductions can be achieved.
IGS GeboJagema is already putting the results of this research into practice. For example, it has developed a method to minimise the energy consumption of its moulds, which will be a standard part of the validation stage going forward. Moreover, the first mould with isolation has already gone into production (Figure 2).
STEPS TOWARDS MINIMAL EMISSIONS
While the move to “green moulds” can have the biggest overall impact, IGS GeboJagema is also taking action to minimise its own carbon footprint. Many of the measures taken might be common sense but are important nonetheless. LED lighting with motion sensors prevents unnecessary energy consumption. Lease vehicles will all be electric going forward. And, as with the rest of the world, since the pandemic the IGS team has started to work from home more.
Moreover, because of constant investments in state-of-the-art machinery, energy efficiency in the factory is high. Case in point: despite significant expansion of the factory and a drastic increase in output over the past 10 years, its energy consumption in 2020 was at the same level as in 2010 (Figure 3).
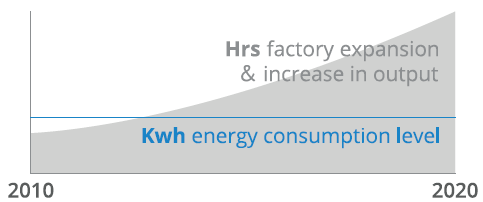
Figure 3: While output increased significantly, energy consumption remained at the same level in the IGS GeboJagema factory.
Technology Instead of Travel
It is well known that flying has a large impact on our carbon footprint but the numbers are still surprising. At IGS GeboJagema, air travel accounted for 51% of all travel-related emissions in 2019. Clearly, flying less is a very effective way to reduce carbon emissions. The pandemic has proved to the world that many in-person meetings can be conducted online. In fact, it saves hours of travel time. Of course, some in-person meetings are harder to replace with a standard video call, such as validation meetings or technical after-sales support. IGS GeboJagema has been working on several smart technical solutions to move these meetings online as well, whenever it is convenient for clients.
Virtual Factory Tour
IGS GeboJagema is proud of its state-of-the-art factory in Eindhoven, and regularly gives prospective clients a tour of the premises. The company now also offers a virtual tour of its headquarters. Through high-quality, 360-degree images, the virtual tour allows clients to see every part of the factory: the modern measuring tools, a newly expanded validation centre and the recently renovated offices (Figure 4).
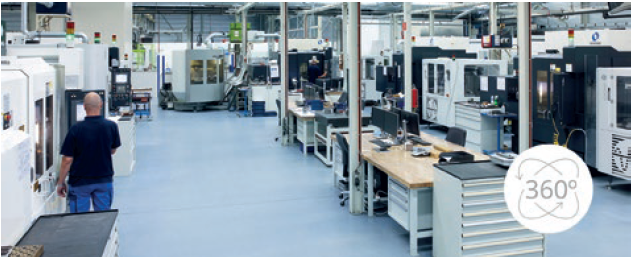
Figure 4: IGS GeboJagema provides factory tours through 360-degree images.
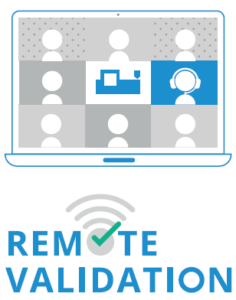
Figure 5: Remote validation was introduced by IGS GeboJagema in 2020.
Remote Validation
In 2020, IGS GeboJagema introduced remote validation (Figure 5). Remote validation makes it possible for clients to join the IGS team in the workshop from wherever they are in the world through a high-quality video stream and several smart technical solutions. Of course, a big reason to start offering this service was to speed up the validation process for customers. But it is also a great way to reduce CO2 emissions (Figure 6).
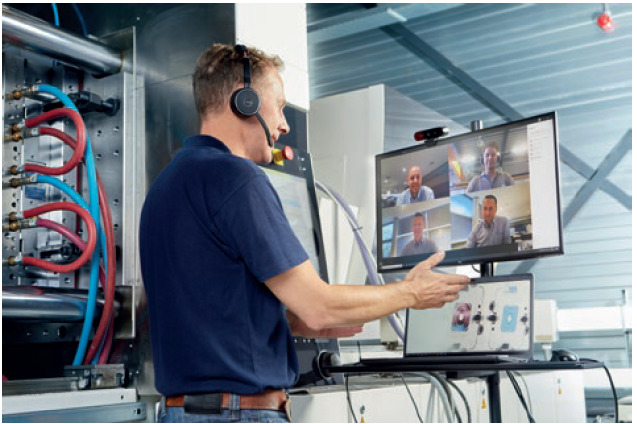
Figure 6: The IGS operator communicates through a headset.
Mixed Reality Support
IGS GeboJagema provides assistance on-site whenever necessary, such as during the site acceptance test or as part of its after-sales service. To make it faster and easier to assist when customers need help, the company also offers support through a Microsoft HoloLens 2. The HoloLens features a full-HD camera for crisp video footage and smart microphones that work even in noisy factories. It’s as close as one can get to being physically present on-site. A unique advantage of the HoloLens is that it can project interactive holograms such as 3D-mould models, mould manuals or other files. With all relevant information at one’s fingertips and the IGS team providing live guidance, the experience of using the HoloLens for support is both surprisingly easy and highly intuitive (Figure 7).
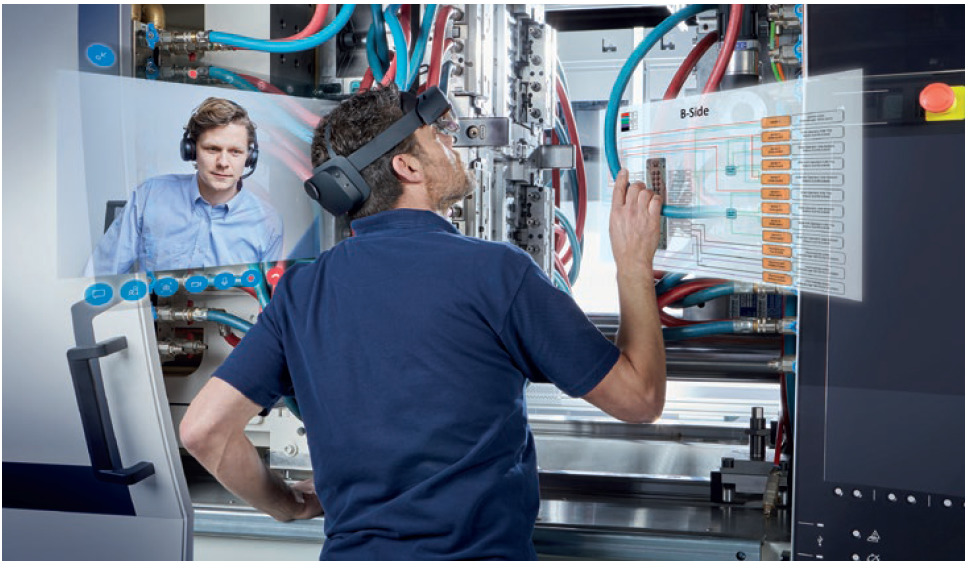
Figure 7: The HoloLens can project interactive holograms such as 3D-mould models, mould manuals and other files.
TOWARDS A MORE SUSTAINABLE FUTURE
Urgent action is necessary to avoid the worst effects of climate change. Over the next decade, markets will continue to change and adapt around this reality. IGS GeboJagema expects that organisations that fail to significantly reduce their carbon emissions will find it challenging to retain clients, recruit new talent and keep their cost structure competitive. By contrast, there will be great opportunities for companies that are ahead of the curve. IGS GeboJagema will continue to develop innovative solutions with its partners to make the healthcare industry more sustainable together.
FOOTNOTES
- Assuming 0.53339 CO2 per kWh. Greenhouse Gas Protocol, GHG Emissions Calculation Tool, Accessed Mar 2022.
- Assuming 2,760 kWh per household. Central Bureau for Statistics, Energieverbruik particuliere woningen. Accessed Mar 2022.