To Issue 138
Citation: Beutler M, Meier M “Unlimited Possibilities by Using a Gas-Producing Dry Cell”. ONdrugDelivery, Issue 138 (Oct 2022), pp 48–50.
Marc Beutler and Matthias Meier discuss the myriad advantages of using a gas-producing dry cell as a drive system for injectable drug delivery devices, as compared with spring-based and electromechanical drives.
“simatec is developing a new type of drive that is ideal for applications with prefilled injection systems, cartridges or other container closure systems.”
Existing forms of therapy are increasingly switching to at-home care. This means that new challenges for drug delivery and supply chains are emerging. High-volume delivery systems with remote monitoring also need new approaches to continue to ensure quality performance, patient safety and end-user benefits. The simatec drive revolutionises existing delivery systems, making them more convenient, lightweight, power independent and silent (Figure 1).
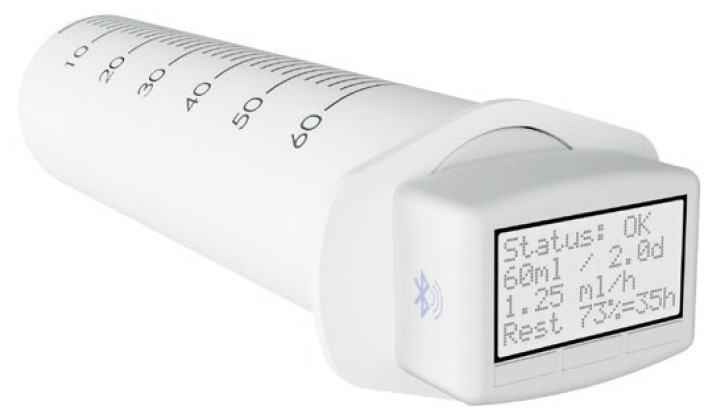
Figure 1: Simatec is developing a new type of drive that is ideal for applications with prefilled injection systems, cartridges or other container closure systems.
For almost 40 years, simatec, based in Wangen an der Aare in Switzerland, has been engineering products and solutions for industry. Innovation and customer focus are two factors of the company’s success, and its existing successful technologies can now also be transferred to the medical industry. In particular, simatec is developing a new type of drive that is ideal for applications with prefilled injection systems, cartridges or other container closure systems.
Through the “design thinking” method, simatec is aiming to provide even wider support for innovations and place its customers’ needs more firmly at the heart of all considerations. Design thinking is based on the basic principles of team, space and process. The English industrial designer Tim Brown defines it as follows: “Design thinking is based on the assumption that problems can be solved better when people from different professions, working together in an environment that inspires creativity, develop a problem together, consider people’s needs and motivations and then create concepts that are tested more than once.”
There are six steps that describe the design thinking process:
- Empathy/Understanding
- Observing
- Defining a point of view
- Finding ideas
- Prototyping
- Testing
- Getting feedback from potential users.
simatec uses agile and iterative creative processes, as well as plenty of interviews, to gather the ideas and wishes of possible future customers. The company is aiming to create new, intelligent solutions and products, customised exactly to the requirements of its customers, and thereby create new business areas.
“Compared with existing products, such as elastomer pumps or spring-operated systems, simatec’s drive offers improved accuracy and reliability.”
FOCUS ON PATIENTS
A number of interviews with doctors, pharmacists, homecare staff and patients have demonstrated an unmet need for affordable and portable dispensing systems that are “simple and smart” to use. Additionally, the tendency to use smaller drive systems is not only born out of a desire to increase comfort, but also a great demand in the areas of paediatrics or at-home treatment for patients with chronic conditions.
While there is currently a demand for some more advanced applications and features in drug delivery devices, such as digital support, there is also a major emphasis on patient centricity and user friendliness that emphasises simple, easy-to-use devices. However, many start-ups in the medical sector are focusing heavily on digital products and services. Which one of these trends will ultimately succeed remains to be determined and, for the present, the topic of digitisation is likely to remain an ongoing concern. As such, simatec is committed to solutions that are modular and meet the specific needs of its customers.
Compared with existing products, such as elastomer pumps or spring-operated systems, simatec’s drive offers improved accuracy and reliability. However, when compared with electromechanical systems, its low cost and convenience are the most significant advantages. The fact that simatec’s gas producing dry cell operates in silence was initially taken for granted by simatec’s specialists. However, for users, this is a massive improvement in comfort during drug delivery in many situations.
ADVANTAGES OF GAS-PRODUCING DRY CELL
By working together with its customers as partners, simatec is inspired to help implement its gas-producing dry cell into innovative devices that not only meet, but exceed, today’s requirements. simatec encourages all potential partners to approach the company with any enquiries – simatec is the specialist for drives powered by the gas-producing dry cell.
Fewer Components, Lower Cost, Increased Sustainability
The simplicity of the gas-producing dry cell drive is not only valuable in terms of purchasing and assembly costs, but also in terms of sustainability. Lowering the component requirement of a drug delivery device means that it consumes fewer resources, which is directly reflected in an improved sustainability profile (Figure 2).
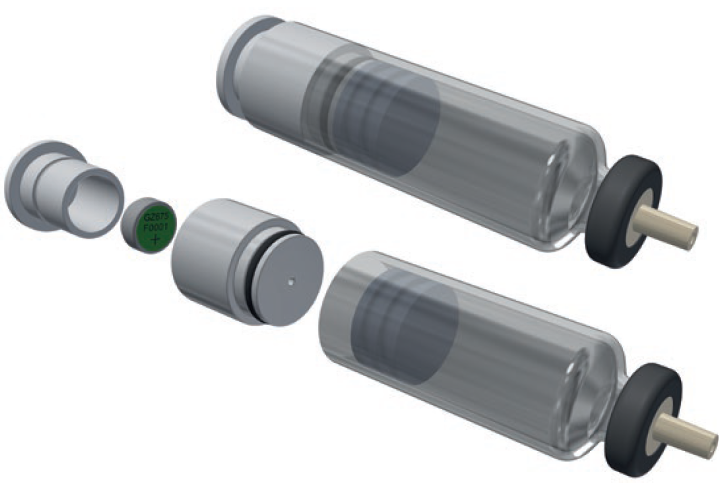
Figure 2: “Simple and smart” design, also suitable for paediatric medical devices.
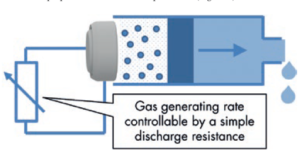
Figure 3: The gassing rate is directly proportional to the electrical current flowing through the gassing cell.
Very Straightforward Operation
The gas-producing dry cell looks very similar to a standard button cell battery. To activate it, the circuit between the positive and negative pole is closed via a defined electrical resistor. Hydrogen gas is generated in proportion to the flowing electric current. Using a modifiable resistor, the precise rate of gas production can be adjusted at any time via a simple control loop. Start-stop operation can also be implemented (Figure 3).
Excellent Functionality with High-Viscosity or Fine Needles
The gas-producing dry cell is excellent for small but accurate dispensing rates. For example, a single cell can generate gas at a rate of up to 10 mL/h at standard atmospheric pressure; with a required overpressure of 1 bar in front of the needle, the gas-producing dry cell can achieve a rate of 5 mL/h. This speed can be multiplied by connecting several single cells in series. The system can generate pressures of up to 25 bar if required, making it ideal for applications where more force is needed to dispense the medium due to higher viscosity or a small needle diameter. It is even possible to handle paste-like materials.
Wide Application Temperature Range
The gas-producing dry cell can be used at temperatures between -20°C and +55°C, covers a very wide range of applications and is ideal for drugs that require cold chain storage. Its functionality is unaffected by long-term storage. This has been proven in an industrial environment for years.
Free of Air Bubbles in the Drug
Dispensing drugs by displacement has a significant benefit over systems that use vacuum: no vacuum is generated, which prevents the formation of air bubbles.
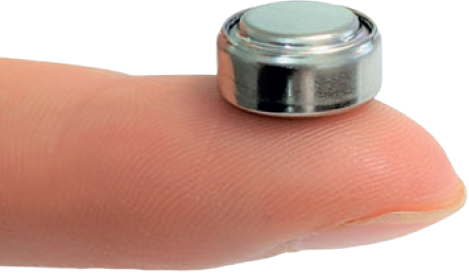
Figure 4: The gas-producing dry cell looks like a standard button cell battery. The size is smaller than a fingertip.
High Level of Safety and Toxicologically Harmless
The molecular hydrogen produced by the gas-producing dry cell is highly pure. Hydrogen gas is toxicologically harmless to the human body in small quantities. Products with the gas-producing dry cell can be approved in all areas where explosion-proof protection is required due to the low electrical output. With a size of Ø11.6 mm by 5.5 mm, the gas-producing dry cell is capable of producing up to 140 mL of pure hydrogen (1 atm at room temperature). Compared with other systems, the high power-density it achieves is unique (Figure 4).