To Issue 139
Citation: Vicenzetto S, “Sustainable Design for Medical Devices”. ONdrugDelivery, Issue 139 (Oct/Nov 2022), pp 14–17.
How do you meet environmental and sustainability objectives when designing medical devices? And what design considerations enable the technical cycles, known as the 4R loops of circular economy: reuse, repair, remanufacture and recycle? Stefano Vicenzetto explores the Flex approach to design for environment for medical devices.
“Linear product lifecycles are giving way to circular models that are healthier for the environment.”
As companies comply with growing consumer and regulatory demands to meet sustainable targets, they are conscious that sustainability starts from the cradle. Design for environment (DfE), once considered a value add, is quickly becoming a necessity for medical product companies, and a top priority for designers.
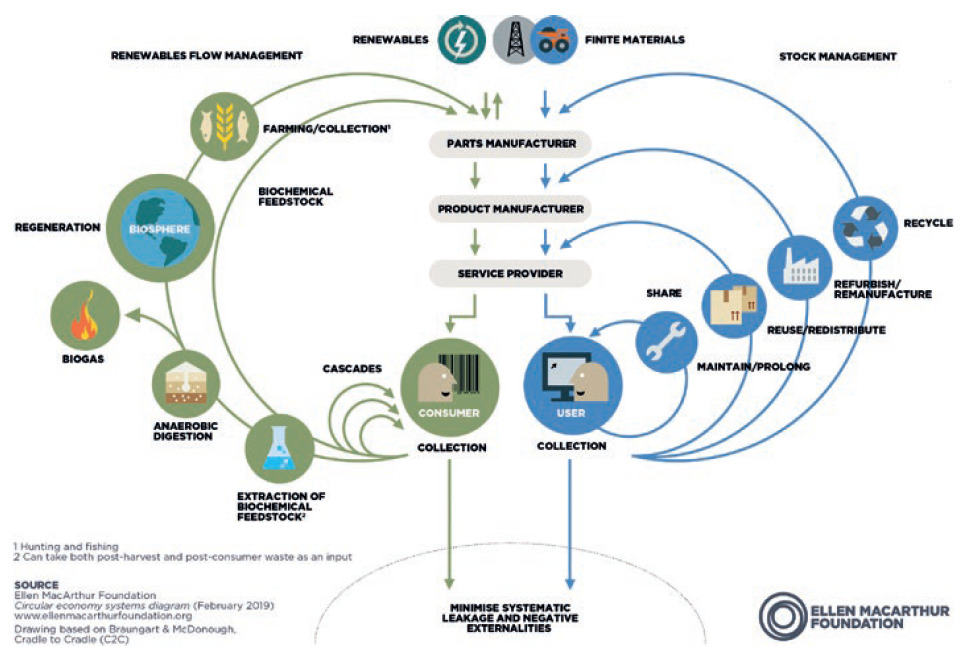
Figure 1: Technical cycles (4R loops on the right) of the circular economy.
“Each product is designed to be durable, minimising the need to repair or replace the device.”
Linear product lifecycles are giving way to circular models that are healthier for the environment. Sustainable new product design should require less raw material extraction, produce less waste and target the 4R loops: reuse, repair, remanufacture and recycle (Figure 1), all of which extend the lifespan of products, offering environmental and economic upsides.
DESIGN FOR ENVIRONMENT FRAMEWORK
For medical devices, Flex’s approach is to consider DfE through three activities (Figure 2):
- Lifecycle assessment
- Eco-value analysis (on existing products)
- Environmental value engineering (on new products).

Figure 2: Flex’s design for environment service portfolio.
“The implementation of effective 4R loops requires products that can be efficiently and economically disassembled and reassembled.”
The Lifecycle Assessment
The first step is to evaluate the environmental impact of a product, based on the analysis of several parameters, including:
- CO2 emissions
- Energy consumption
- Water consumption
- Recycling rate (percentage of material recycled)
- Recovery rate (percentage of material used to generate energy when the product reaches the end of life).
The assessment can be performed on medical devices already in-market to calculate a baseline of their environmental impact – or on new medical products under development to verify if the proposed design meets sustainability requirements (Table 1).
Waste type | Weight (g) |
CO2 Emissions (g) |
Energy consumption (MJ) |
Water consumption (m3) |
Battery | 50.0 | 278.4 | 5.1 | 0.0034 |
LCD | 4.3 | 911.1 | 14.4 | 0.0162 |
Metal (aluminium) | 0.8 | 7.0 | 0.1 | 0.0001 |
Metal (brass) | 8.0 | 36.1 | 0.6 | 0.0006 |
Metal (stainless steel) | 21.7 | 93.4 | 1.6 | 0.0015 |
Metal-plastic (motors) | 25.0 | 203.0 | 2.9 | 0.0027 |
PCBA | 25.0 | 5297.3 | 83.5 | 0.0940 |
Plastic (POM) | 1.5 | 6.4 | 0.1 | 0.0000 |
Plastic (PC) | 8.3 | 75.0 | 1.3 | 0.0002 |
Plastic (PC-ABS) | 88.2 | 715.0 | 13.5 | 0.0020 |
Total | 232.8 | 7631.8 | 123.2 | 0.1207 |
Table 1: Lifecycle assessment example for a medical device. (LCD = liquid crystal display; PCBA = printed circuit board assembly; POM = polyoxymethylene; PC = polycarbonate; and PC-ABS = polycarbonate/acrylonitrile butadiene styrene.)
The Eco-Value Analysis
Existing medical devices, already in-market, can be analysed against the following criteria:
- Materials used
- Product durability
- Energy efficiency
- Ease of disassembly and reassembly
- Ease of maintenance and repair.
Once an evaluation of these factors is complete, it is possible to envision where the medical product can be better designed to improve the environmental impact and the economic value of materials, parts and product recovered.
Environmental Value Engineering
For a new device, Flex integrates the product development process for a new medical design, subjecting it to the same analysis and design guidelines adopted in the eco-value analysis to meet the sustainability requirements of new products:
- Guarantee compliance with specific environmental regulations
- Minimise carbon footprint (i.e. carbon footprint lower than a predefined target)
- Enable circular economy (design for reuse, repair, recycling)
- Sustainable packaging, where possible.
Other considerations
DfE applied to medical devices must also consider specific challenges, such as biohazardous waste, which can limit the opportunity for product reuse, and biocompatibility requirements that may inhibit the use of recycled materials.
“The lifespan of the medical device can be further extended where a modular design has been used.”
MEDICAL DESIGN GUIDELINES
Materials Selection
The medical design teams at Flex consider multiple aspects when selecting the right materials. Initially, they factor in and comply with regulations – such as the Restriction of Hazardous Substances and the Registration, Evaluation, Authorisation and Restriction of Chemicals – that restrict the presence of hazardous substances. Governments and standards bodies around the world are regularly updating regulations to increase the variety and volume of materials that can be used. Prudent product companies stay ahead of the regulations by expanding the list of restricted materials themselves.
The next step is to examine materials for their weight, durability, ease of recycling and ability to support effective 4R loops.
A material’s carbon footprint is also considered. For example, climate-neutral polycarbonate can be used when designing innovative plastic solutions that are generated by virgin biomass (vegetation) and cooking oils. In some cases, these thermoplastic materials can reuse the tooling previously designed to host standard fossil resins and therefore avoid the need for additional investment.
Product Durability
Flex’s design for reliability approach for medical devices means each product is designed to be durable, minimising the need to repair or replace the device. By increasing the reliability and modularity, some parts may be reused to support refurbishment or redeployment of those parts to other devices.
Reusable parts are typically components with a longer lifetime and lower failures in time. They are activated when required within the device and, like all the other subsystems, may include a self-test/ diagnostic mechanism to flag up a fault in the device.
Energy Efficiency and Batteries
The energy efficiency of the medical device is equally important. In battery-powered devices, smaller and more efficient batteries will mean less-frequent charging cycles and, as batteries are hazardous waste, a lower impact on the environment when the batteries are replaced. For some devices, Flex uses disposable printed batteries, based on non-toxic materials like zinc. This allows the batteries to be disposed of in regular domestic waste bins, where local regulations allow. Any battery used should conform to safety standards such as the CE mark.
There are several power reduction elements that can be applied to medical devices, including adopting low-power technology, implementing low-power modes when not in use and separating the power supply for different parts of the product, depending on use.
Ease of Disassembly and Reassembly
The implementation of effective 4R loops requires products that can be efficiently and economically disassembled and reassembled. In this sense, it is important to minimise the use of glues and welds that can be difficult to remove without damaging parts of the product and that could contaminate other materials in the device. It is also important to ensure the design facilitates both automated assembly and manual disassembly.
Ease of Maintenance and Repair
While a firmware upgrade can increase device longevity and is a normal part of device maintenance, the lifespan of the medical device can be further extended where a modular design has been used. A modular design can allow easier access to each module, including the battery for testing, repair, replacement or upgrading, as necessary. It also ensures hazardous substances are isolated.
CONCLUSION
DfE services support medical device companies through cost-effective lifecycle assessment, environmental impact evaluation, material selection, durability testing, energy efficiency and ease of disassembly of the product and its parts (Figure 3).
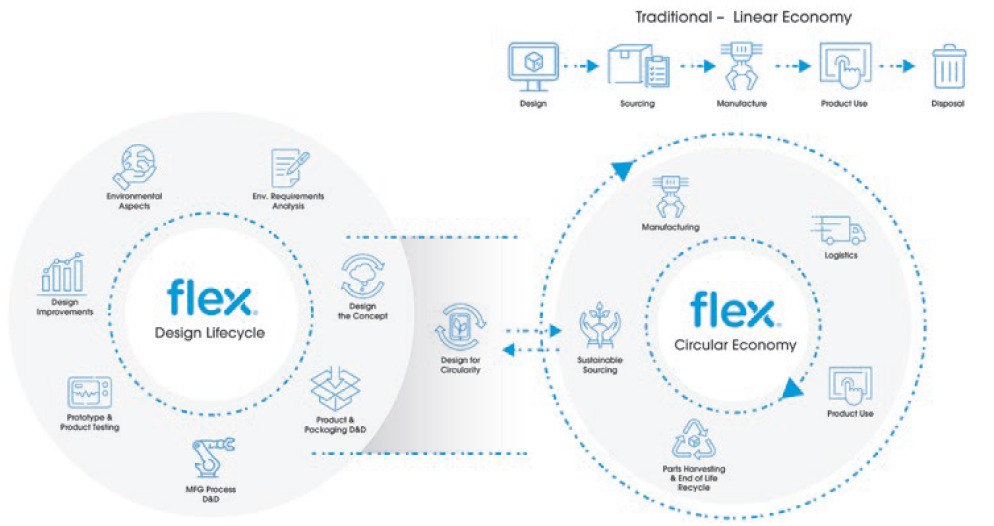
Figure 3: Linear versus circular economy.
The result is a medical device that is optimised for sustainability and uses low-power technologies, less hazardous substances and advanced non-toxic battery technology that allows for ecological disposal. Smart and sustainable design also allows for efficient assembly and disassembly to allow repair, refurbishment and reuse of parts, and easy upgrades to firmware and hardware. These elements combine to deliver a medical device with a minimised carbon footprint.