To Issue 140
Citation: Doorakkers R, van Huijksloot E, “High-Precision Injection Moulds for Inhalers: Challenges and Solutions”. ONdrugDelivery, Issue 140 (Nov 2022), pp 70–72.
Rob Doorakkers and Erwin van Huijksloot discuss the challenges and solutions of engineering and manufacturing high-precision injection moulds for inhalers.
“Whether inhalers accurately deliver drugs is largely determined by the precision of the moulded actuator.”
The goal of an inhaler is simple: to reliably and efficiently deliver medicine. Efficient drug delivery makes treatments more effective and thus allows patients to extract more successful dosages from a single canister.
Whether inhalers accurately deliver drugs is largely determined by the precision of the moulded actuator. Small differences in the geometry of the actuator can drastically change the medicine’s spray behaviour, also known as bloom. The bloom determines where the medicine is applied in the mouth, which is an important factor in how effective a drug is. For example, some drugs are most effective when administered to the roof of the mouth, while others should reach the back of the throat to be inhaled deep into the lungs (Figure 1).
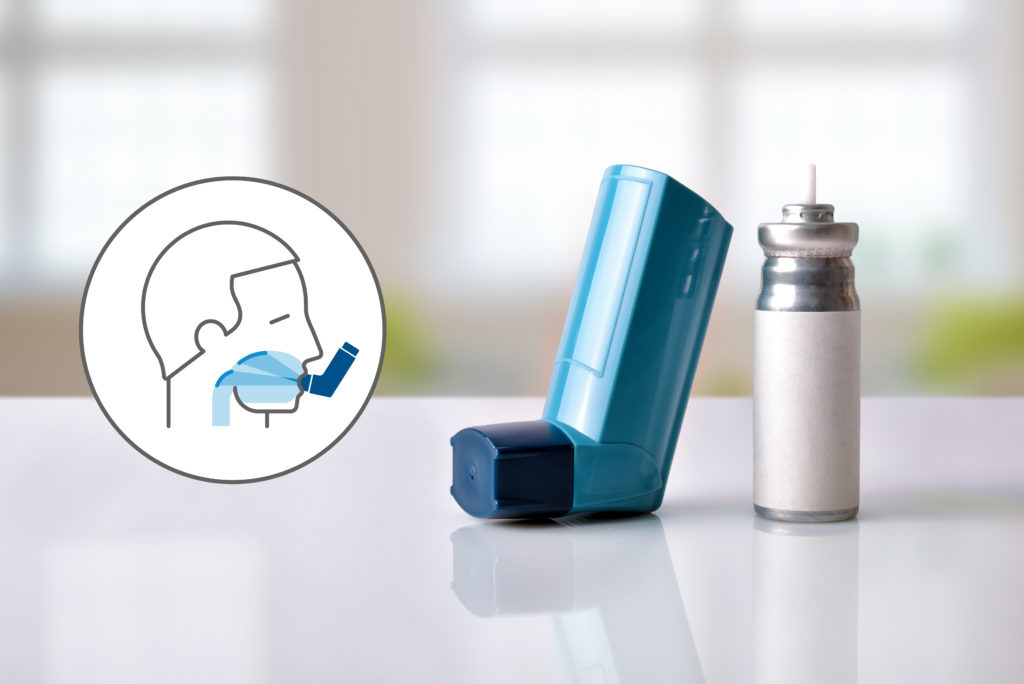
Figure 1: Some drugs must be administered through the roof of the mouth, while others must reach the back of the throat.
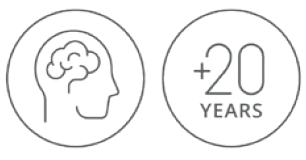
Figure 2: More than 20 years of experience.
IGS GeboJagema has engineered and manufactured injection moulds for inhalers for more than 20 years. In fact, the first inhaler mould the Eindhoven company delivered is still active today. In this article, the authors will discuss the challenges in realising the required degree of precision, as well as some of the most effective solutions developed by the IGS GeboJagema engineering team (Figure 2).
CRITICAL COMPONENTS: THE STEM FIT AND THE ORIFICE
To understand the challenges in manufacturing inhalers, it is first necessary to take a closer look at how these devices are constructed. The device has a right-angled design. The canister is placed in the body of the device, while the medicine is administered through the mouthpiece (Figure 3).
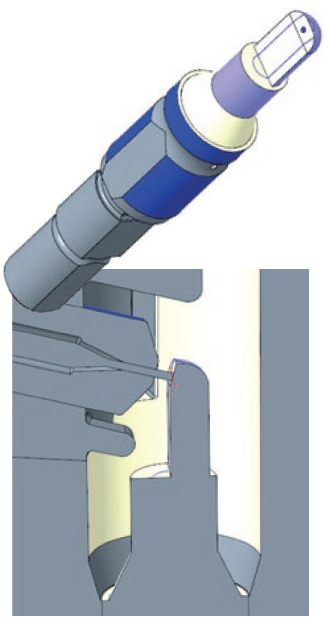
Figure 3: The stem fit.
“Applying too much pressure on the orifice pin will cause it to deform.”
Two components are absolutely critical for accurate drug delivery: the stem fit and the orifice. The stem fit is where the medicine canister and the plastic device connect. The orifice is the opening through which the medicine is sprayed into the patient’s mouth.
The geometry of the stem fit and orifice determine the device’s bloom. Consequently, this is where all IGS GeboJagema’s injection mould expertise can be found. For example, during the validation phase, the IGS GeboJagema team extensively tests the bloom of different device dimensions. Ink is placed in the device, which is then sprayed at a “dartboard” to confirm that the drug will reach the correct location in the mouth (Figure 4).
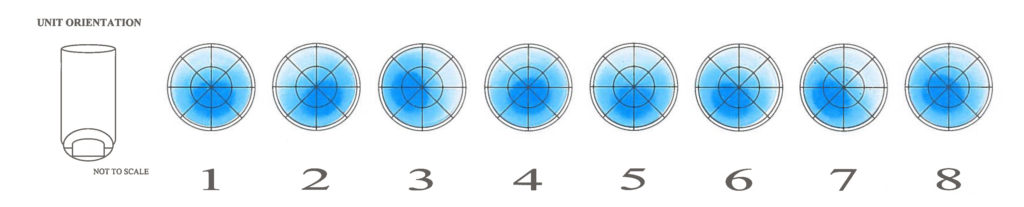
Figure 4: The tests of the bloom during the validation phase.
Having determined which device dimensions are necessary for accurate drug delivery, the next step is to create an injection mould for the device. Over the past two decades, IGS GeboJagema has developed a range of solutions for common challenges and client requirements in this process.
1. Fast Stem Fit Variations for Optimal Uptime and Higher Mould Output
The stem fit is of vital importance for accurate drug delivery. It must be perfectly in line with the body and mouthpiece to create the optimum spray direction. If this is not the case, the “aim” will be off and medicine will be unnecessarily lost. Moreover, the geometry of the stem fit affects the bloom of the medicine. So, by using a different stem fit, a different bloom can be realised.
During the injection-moulding process, a stem fit insert is used to mould this part of the plastic product. In what could be called the standard injection mould for inhalers, it is possible to change the stem fit insert. However, the process is time consuming, as the mould must first be removed from the moulding machine. For contract manufacturing organisations (CMOs) that produce limited variations of their product, this is not an issue. But for medical device manufacturers that need to produce many different variations, a better solution is necessary.
For these clients, the engineering team at IGS GeboJagema created a solution where the stem fit insert can be removed while the mould is still on the machine. Via the side of the mould, a system can be activated to remove or mount the stem fit insert. This easy system saves a lot of time and improves the uptime of the mould, which allows for higher mould output.
2. Orifice Precision to Avoid Flash in the Shut-Off Area
The orifice is the opening in the mouthpiece through which the medicine passes. It is, of course, essential that this opening remains perfectly “clean”. For example, no plastic film (also known as “flash”) must be left behind in the orifice. IGS GeboJagema has developed a special technique to mould the orifice. In its moulds, a spring keeps sufficient pressure on an “orifice pin” in order to realise a clean “shut-off area”: the area where the stem fit insert and the orifice pin meet. This prevents flash in the orifice, which could otherwise potentially be inhaled by the patient.
This technique requires a high degree of precision. Applying too much pressure on the orifice pin will cause it to deform and result in a “mushroom effect”. Moreover, placing too much pressure on the orifice pin will also create an indent on the stem fit insert, which can also create flash. As a solution, in the past, hard materials were used for this component. But, as these hard materials proved susceptible to breakage, today IGS GeboJagema uses a tough steel-grade component with a carbide centre in the shut-off area.
“The ideal mould design depends on a project’s exact requirements.”
3. Flexible Orifice Moulds for Improved Uptime and Mould Output
As discussed, the bloom of an inhaler can be modified by changing the stem fit. However, for some devices it is necessary to change the orifice as well, as different drugs require a different orifice length and diameter. For these projects, IGS GeboJagema has implemented a quick-change system that allows replacement of the orifice pin while the mould is mounted on the injection-moulding machine. As with the system to quickly change stem fit inserts, this saves time and improves the uptime of the mould – and thus optimises mould output. For even more switching speed, the engineering team at IGS GeboJagema developed a second solution, which gives CMOs the option to adjust the jet length of the orifice in seconds using a control built into the mould.
4. Long-Life Orifice Pins for Highly Reliable Product Quality
The orifice diameter is usually between 0.2 and 0.5 mm. The orifice tends to have a length between 0.2 and 1 mm. That means the orifice pin required to mould this component will be very thin as well. Considering the large amount of pressure placed upon the orifice pin during the moulding process, it should be no surprise that these pins are at risk of bending or breaking over time. The bending of the pin is a particularly pernicious problem, as it can slowly affect the accuracy of the actuator and thus the bloom. Considering the trend of orifice diameters becoming smaller and smaller, this could become a more prevalent issue for medical device manufacturers if no countermeasures are taken.
The root cause of these problems is the force released when the injection mould closes and opens again. This force causes the orifice pin to move slightly which, over time, can cause the issues described above. To prevent this, IGS GeboJagema developed a solution where a servo-driven system retracts the orifice pin to a safe position before the clamp is released and the mould is opened. The system then returns the orifice pin to its original position once the mould is closed again and the clamp force has already been applied. This solution extends the lifetime of the pin and prevents bending and breaking problems.
A PASSION FOR PRECISION
This article has presented several solutions that the engineering team at IGS GeboJagema has developed over the past two decades. Of course, the ideal mould design depends on a project’s exact requirements. The mould features described in this article can help to meet those project requirements through greater uptime, fewer problems and a lower total cost of ownership (Figure 5).
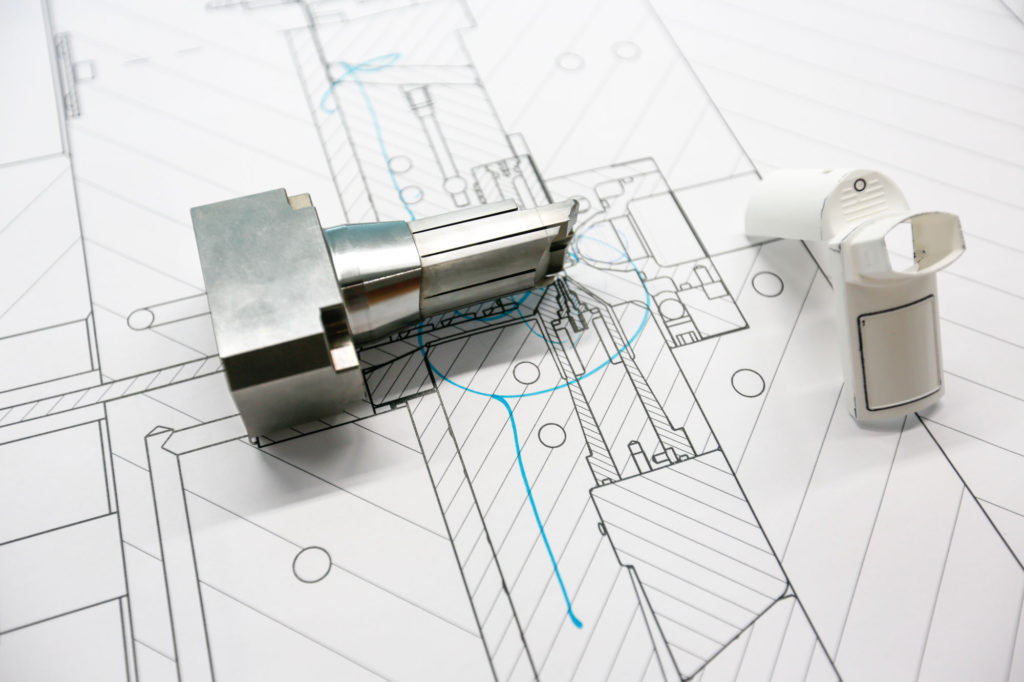
Figure 5: Innovation through passion.
Through smart technical solutions, moulds can minimise loss of medicine in the device. It allows patients to rest assured that exactly the right amount of medicine is being administered. It is just one example of how IGS GeboJagema’s passion for precision touches billions of lives every day.
Previous article
CLIPhaler – INHALATION DEVICE DESIGN REDUCED TO THE MAXIMUMNext article
ENGINEERING EXPERTISE: DESIGN FOR EXCELLENCE