To Issue 156
Citation: Welch B, “Key Considerations for Successful Commercialisation of Drug-Device Combination Products”. ONdrugDelivery, Issue 156 (Jan 2024), pp 24–28.
Bill Welch delves into the key considerations that stakeholders must address to ensure the successful commercialisation of drug-device combination products.
In the rapidly evolving landscape of patient-centred healthcare, the intersection of drug product and medical devices has given rise to a unique drug delivery category of products known as drug-device combination products. The emergence of drug-device combination products, where a large- or small-molecule drug product is integrated with a medical device, has paved the way for novel therapeutic solutions.
“Navigating the regulatory landscape is arguably the most critical aspect of developing and commercialising drug-device combination products.”
Driven by the growing prevalence of chronic disease, such as diabetes, respiratory disease and cancer, advancements in the drug-device combination product market are expected to have a significant impact on the healthcare sector over the coming years. According to a recent report by insightSLICE, the global drug-device combination products market, which was valued at US$109.17 billion (£86.4 billion) in 2022, is estimated to be $236.36 billion by 2033, with an estimated compound annual growth rate of 7.2% between 2024 and 2033.1
These innovative drug delivery solutions offer the promise of enhanced therapeutic outcomes by seamlessly integrating drug products and delivery devices, but their development and commercialisation come with a set of intricate challenges.
REGULATORY LANDSCAPE
Navigating the regulatory landscape is arguably the most critical aspect of developing and commercialising drug-device combination products. Regulatory agencies, such as the US FDA and the EMA, have established specific guidelines to ensure the safety and efficacy of these complex products.
First, companies must determine the regulatory pathway applicable to their product. Understanding the regulatory classification of a drug-device combination product is essential and depends on its principal mode of action. This will dictate whether the product will be regulated as a medical device, a drug or a combination product. This determination influences the type of regulatory submission required and the specific requirements for demonstrating safety and efficacy.
FIVE TRENDS IN DRUG-DEVICE COMBINATION PRODUCT FINAL ASSEMBLY
- Preference of top-opening cartons to hold multiple devices simultaneously: Not only do top-opening cartons provide the benefits of immediate presentation of entire contents for users, superior integration of disparate elements, such as additional needles and small vials, more evident tamper protection and ease of reclosure but, more importantly, they provide ease of access for the patient and aid patient compliance.
- Convergence of packaging engineering and human factors: The convergence of packaging engineering and human factors is propelled by the need to create packaging solutions that prioritise the user experience, safety and usability. This interdisciplinary approach ensures that packaging not only serves its primary function of protecting products but also enhances the overall patient experience, contributing to product success in the market.
- Earlier adoption of devices within the clinical lifecycle: Early adaption is driven by a combination of factors, including a focus on patient centricity, improved clinical data accuracy, safety monitoring, real-world simulation, competitive positioning and regulatory considerations. As the pharmaceutical industry continues to prioritise patient experience and adherence, the use of drug-device combination products in early clinical trials will remain a prominent and strategic choice for many companies.
- Multiple formats for regional presentations: Companies are increasingly bringing different injectable formats to different geographical territories. Often driven by cost and reimbursement, for example, some may commercialise vials with syringes for Eastern European markets but may look to more advanced prefilled syringes (PFSs) with safety devices or autoinjectors or even on-body injectors for the US or Western Europe.
- Testing, testing, testing: Once a secondary consideration with developing a drug-device combination product, testing is now front and centre. Presentation and batch size will shape testing requirements and level of automation.
HUMAN FACTORS AND USER EXPERIENCE
Human factors engineering is a critical aspect of drug-device combination product development. With a patient-centric focus, interaction between users and the product as-received is paramount. Understanding how patients and healthcare professionals interact with the packaging, instructions for use and the device itself is vital for optimising usability, minimising user errors, and enhancing overall safety, efficacy and adherence to gain improved outcomes.
Conducting usability studies and incorporating human factors considerations early in the design process can help to identify potential issues and inform design modifications. Human factors and usability engineering is an integral component of regulatory submissions and essential for demonstrating the product’s usability and user comprehension.
DESIGN CONTROL AND DEVELOPMENT CHALLENGES
The successful integration of a drug and a device requires meticulous design control to address the unique challenges posed by combination products. The compatibility of the drug product and the device, as well as the potential impact on the product’s stability and performance, must be thoroughly assessed during the development phase.
Additionally, establishing a robust risk management plan is crucial to identify and mitigate potential issues that may arise during product development. This includes addressing concerns related to drug stability, device functionality and any possible interactions between the two components.
Whether internally at the biopharmaceutical company or the company’s preferred partnering contract development and manufacturing organisation (CDMO), it is imperative that multidisciplinary teams work together across drug product development and packaging design to ensure compatibility.
QUALITY AND MANUFACTURING CONSIDERATIONS
Ensuring the quality and consistency of drug-device combination products is paramount. Manufacturers – whether the biopharmaceutical company or their partnering CDMO – must adhere to good manufacturing practices to guarantee the reproducibility and reliability of the product. This involves implementing rigorous quality control measures at every stage of production, from raw material sourcing and sterile filling of the drug product into the primary container to final drug-device combination product assembly, labelling and packaging.
Validating robust, scalable manufacturing processes and controls is essential to produce combination products with consistent quality and performance throughout the drug-device combination product lifecycle, from clinical trials to commercial market supply.
“Ensuring a robust and secure supply chain is vital for the commercial success of drug-device combination products.”
CLINICAL DEVELOPMENT
The generation of robust clinical evidence is paramount for the successful commercialisation of drug-device combination products. Companies must design and conduct clinical trials that not only demonstrate the product’s safety and efficacy but also provide meaningful real-world data on the interaction between the drug and the device.
The design of clinical studies should align with regulatory requirements and consider the unique challenges posed by drug device combination products. Well-designed clinical trials should consider patient populations and clinical endpoints. Collecting data on both the drug and device components individually, as well as their combined effects, is essential for building a comprehensive body of evidence to support regulatory submissions.
DEVICE STRATEGY – INTELLECTUAL PROPERTY PROTECTION
Forming part of the device strategy, securing intellectual property (IP) rights is a critical consideration in the competitive landscape of drug-device combination products. Companies must navigate patent landscapes carefully to protect their device innovations and establish a strong IP position. This includes considering both the drug and device components, as well as any novel aspects of their combination.
SUPPLY CHAIN MANAGEMENT
Ensuring a robust and secure supply chain is vital for the commercial success of drug-device combination products. Companies should establish strong relationships with suppliers and partnering CDMOs, implement risk mitigation strategies and have contingency plans in place to address potential disruptions. This is particularly important given the interconnected nature of the drug and device components, each with its own set of manufacturing and sourcing considerations.
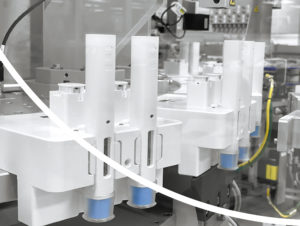
Figure 1: PCI provides specialised advanced drug delivery assembly, testing and packaging support.
ADVANCED DRUG DELIVERY SOLUTIONS AT PCI PHARMA SERVICES
The increasing use of biologics, which often require specialised delivery systems, has contributed to the growth of drug-device combination products and the need for technically advanced sterile manufacturing and specialised advanced drug delivery assembly, testing and packaging support. Committed to being a market leader in the packaging of biologic drug products for its global clients, PCI Pharma Services’ goal is to support its customers in safely and efficiently bringing their novel therapies to patients.
Driven by innovation and patient centricity, the company’s design and development expertise, combined with its device assembly and advanced drug delivery packaging capabilities, offers flexible solutions for a diverse portfolio of conventional and specialty injectable drug-device combination products (Figure 1). PCI has the scalability to handle dynamic volumes, large or small, from niche personalised medicines to large-volume treatments.
EXPERT ADVICE FROM DEVICE STRATEGY TO PACKAGING DESIGN
With a global network of experts with extensive experience in advanced drug delivery, PCI provides guidance at critical milestones to assist its clients in developing an optimum patient-centric drug-device combination product.
The company’s deep industry experience can help to determine the best device strategy for clients’ patients and drug products, from the use of established, well-accepted platforms that have previously received regulatory approval as part of a drug-device combination product – which may be deemed lower risk – to, alternatively, developing a more innovative device approach that may be more attractive for specific patient populations compared with that of more readily available platforms.
PCI’s pharmaceutical packaging design department provides an innovative and value-added service. The company’s in-house team of specialists delivers insightful packaging design and practical knowledge to deliver differentiated and cost effective packaging solutions (Figure 2). Working with client partners as early as possible during their drug products clinical phases, PCI’s design team – together with a cross-functional network of experts in sterile drug product manufacturing, engineering, operations and approved vendors – develop expert design processes focused on human-factors engineering and technical functionality to deliver patient-centric designs optimised for manufacturability, scalability and automation. This seamless solution ensures that key considerations are addressed at the right time, leading to both cost and time efficiencies and, ultimately, ensuring speed to market.
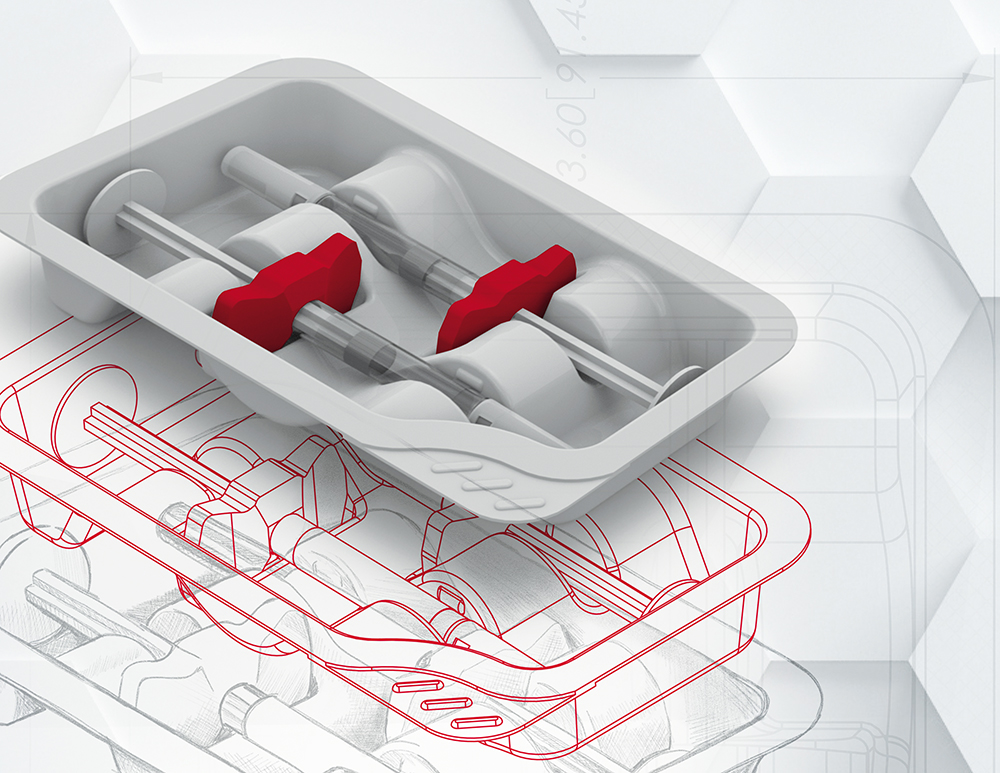
Figure 2: PCI’s expert packaging design team, using three-dimensional modelling can facilitate rapid prototype design and an expedited response to enable speed-to-market.
EXPANSION OF DRUG-DEVICE COMBINATION PRODUCT CAPABILITIES AND CAPACITIES
Complementing the continued growth and investment across PCI’s sterile manufacturing network, the company continues to expand its European, North American and UK Centers of Excellence for clinical and commercial packaging. These state-of the- art facilities are equipped with advanced drug delivery packaging technologies for the assembly and labelling of vials, cartridges, standard PFSs, advanced safety syringes, autoinjectors and pen devices complete with integrated top-load cartoning and serialisation.
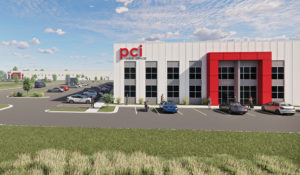
Figure 3: PCI is investing to expand its Rockford (IL, US) site to meet the growing biologic market need for specialised assembly and packaging of injectable drug-device combination products.
Most recently PCI announced an investment of $150 million in a new 200,000 sq ft facility at its Rockford (IL, US) site to meet the growing biologic market need of specialised assembly and packaging for injectable drug-device combination products. With over 20 dedicated suites, the new facility will support the assembly and packaging of vials, PFSs, autoinjectors, on-body injectors and pen cartridges, such as those for glucagon-like peptide 1 agonists for the treatment of diabetes and obesity, as well as those needed for oncology treatment and autoimmune diseases (Figure 3).
FLEXIBLE, SCALABLE AUTOINJECTOR ASSEMBLY
As a leading global CDMO, PCI Pharma Services provides highly flexible, reliable advanced drug delivery packaging solutions to meet the dynamic needs of its clients. Meeting the exponential growth in the development and use of autoinjectors, PCI continues to invest in innovative scalable autoinjector assembly, labelling and packing technologies.
Although many autoinjectors have similar components, their design varies in terms of size, material and shape. With true customer focus and flexibility at the core of the company’s injectable packaging service offering, its technologies can adapt to the unique requirements of each global market from concept to commercialisation.
For example, PCI’s small-to-mid-scale autoinjector assembly lines provide multi-platform autoinjector solutions, including Ypsomed’s Ypsomate, SHL Medical’s Molly and BD’s Physioject, alongside other platform devices. They also have the capability to assemble and label needle safety device platforms, such as BD’s Ultrasfe/Plus and Nemera’s Safe & Sound, making them ideal for development studies, clinical trials and niche orphan drugs.
Providing integrated scalable solutions, PCI’s larger-scale technologies can also accommodate various autoinjector types to support product launches and commercial market supply. Providing true customisation, its larger-scale lines can easily and cost-effectively be retooled for future new autoinjector types, allowing the company to respond quickly and efficiently to technological changes and future innovation.
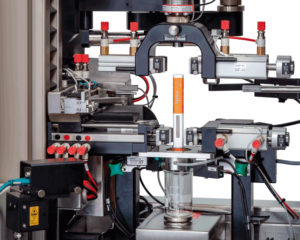
Figure 4: PCI provides a range of onsite device functional testing for drug-device combination products, according to ISO 11608, ISO 11040 and ISO 7886. Image courtesy of PCI’s partner ZwickRoell.
SEAMLESS MANUFACTURING, PACKAGING AND TESTING SOLUTIONS
At PCI, ensuring life-changing medicines reach those who need it most is the highest priority. As a truly integrated global CDMO, the company is an expert in manufacturing, packaging and supply chain, harnessing its experience and expertise to deliver seamless solutions with the ultimate aim of improving the lives of patients.
Providing expert sterile fill-finish and lyophilisation solutions from development to commercialisation, together with integrated custom assembly and packaging solutions for sterile injectables, allows for ultimate knowledge sharing and communication between teams to ensure the drug product packaging is optimised for the product, patient and production.
“Providing integrated scalable solutions, PCI’s larger-scale technologies can also accommodate various autoinjector types to support product launches and commercial market supply.”
With in-house laboratories, PCI provides a range of packaging and analytical services to support clients’ development, clinical and commercial supply of medicines globally. From product identity testing, method transfer, release and stability testing to autoinjector system testing with ISO 11608 functional tests, such as cap removal force, activation force, extended needle length, dose accuracy, injection time and lockout force, the company ensures that clients’ life-changing therapy meets regulatory guidelines and is safe for patient use (Figure 4).
CONCLUSION
Successful commercialisation of drug-device combination products requires a multidisciplinary holistic approach, combining expertise in drug product and medical devices. By addressing the key considerations outlined above and when needed, partnering with an expert CDMO, such as PCI Pharma Services, manufacturers can navigate the challenges along the journey to commercialisation, ensuring the successful integration of drug and device components and, ultimately, delivering life-changing therapies to patients.
REFERENCES
- “Providing expert sterile fill-finish and lyophilisation solutions from development to commercialisation, together with integrated custom assembly and packaging solutions for sterile injectables, allows for ultimate knowledge sharing and communication between teams to ensure the drug product packaging is optimised for the product, patient and production”. insightSLICE, Aug 2023.
Previous article
AN ECO-FRIENDLY AND ECONOMICAL APPROACH TO AUTOINJECTORSNext article
DISCUSSION PRIMER: PHARMAPACK