Citation: Wiglenda M, “From Idea to Mass Production: Rapidly and Safely Industrialising Innovations”. ONdrugDelivery, Issue 163 (Jul 2024), pp 48–53.
Michael Wiglenda describes Gerresheimer’s approach to the industrialisation of drug delivery devices, using the production of the company’s Gx Inbeneo® cartridge-based autoinjector as an example.
As a full-service provider, Gerresheimer Medical Systems provides comprehensive support to its customers throughout all phases of the development process, from the initial conception of an idea to series production. Gerresheimer possesses extensive experience and expertise, as well as the accompanying technical infrastructure, in large-scale production across all stages of the product development process. The company maintains substantial resources in the development, industrialisation and manufacture of delivery systems and components for a wide range of APIs, including inhalers, pen injectors, autoinjectors and glass or plastic syringes.
Whether customers want to implement an initial product idea, further develop an existing development state or have a fully developed product optimised for materials and mass production, Gerresheimer has the expertise to deliver. The company’s core competencies also include injection moulding, including further processing, and worldwide logistics. Through standardised processes, Gerresheimer creates products that meet the specific requirements of an API and the needs and demands of users and patients, including the functional technical and technological production requirements, user-friendliness and appealing design.
“Gerresheimer’s state-of-the-art measuring and analysis equipment, including industrial CT scanners, enables faster and more cost-effective development of drug delivery systems.”
Gerresheimer’s state-of-the-art measuring and analysis equipment, including industrial computed tomography (CT) scanners, enables faster and more cost-effective development of drug delivery systems. By integrating design for manufacturing (DfM) principles from the outset, the company is able to reduce development times and costs. Gerresheimer is a well-established expert in processing the two primary materials of the drug delivery industry: glass and plastics. This expertise enables pharmaceutical customers to ensure that their primary packaging and the drug delivery device come from a single source and are optimally co-ordinated.
Gerresheimer’s Technical Competence Centers (TCCs) play a significant role in the company’s offering and deliver specialised services that ensure high-quality and efficient production processes. Worldwide, over 600 engineers, technicians and designers in the TCCs use simultaneous engineering to streamline the entire product development process and ensure that products are designed for mass production from the outset. Among the key services offered by the TCCs are:
- Development and construction of small-series and large-scale moulds and special-purpose assembly equipment
- Development and construction of measuring equipment
- Sampling and process engineering
- Material-specific, physical and chemical analysis
- Optical and tactile measurements
- Functional measurements
- Qualification and validation of moulds and assembly equipment
- Production of development samples, clinical samples up to small-batch production in accordance with ISO 14644-1 ISO classes 7, 8 and 9 or GMP classes C and D, respectively.
The internationally located TCCs also co-operate with each other. For example, the industrialisation expertise of the TCC in Wackersdorf (Germany) is also used for Gerresheimer’s platform solutions. The “Innovation Center Smart Devices/Digitalization” in Olten (Switzerland) has developed a disposable autoinjector for subcutaneous administration in co-operation with Midas Pharma (Ingelheim, Germany). This platform solution has now been optimised and industrialised at the TCC in Wackersdorf.
DISPOSABLE AUTOINJECTOR PLATFORM SOLUTION: GX INBENEO® AUTOINJECTOR
The Gx Inbeneo® autoinjector is a cartridge-based autoinjector system based on pressurised cartridges (Figure 1). During storage, there is no contact between the needle and the medication, ensuring that the needle remains dry. The disposable autoinjector is also compatible with cartridges that have a baked-on silicone coating.
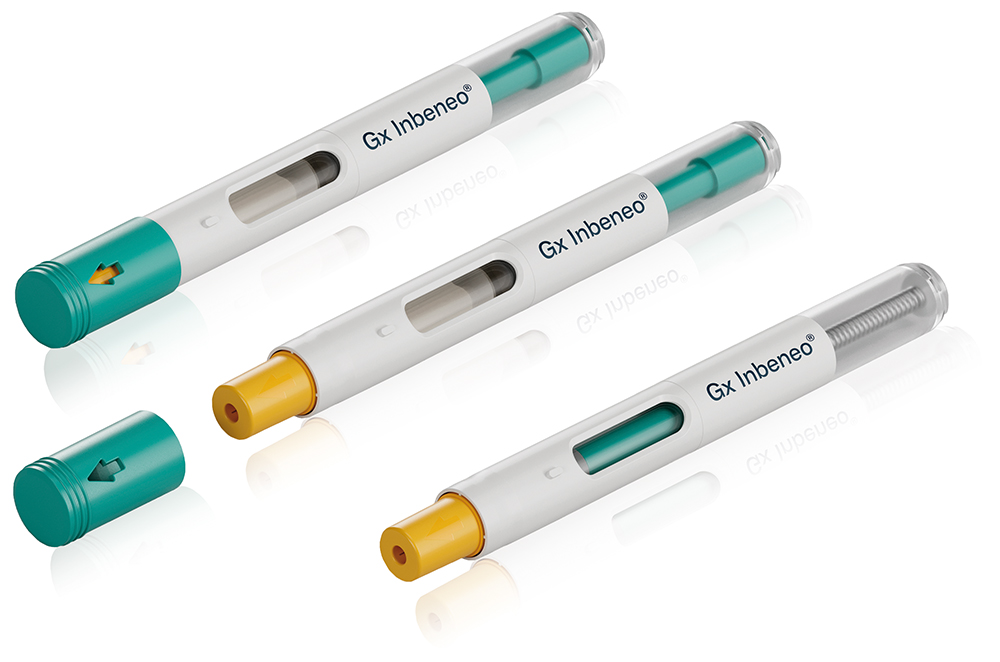
Figure 1: Gerresheimer’s Gx Inbeneo® autoinjector – a next-generation solution for subcutaneous drug delivery.
The Gx Inbeneo is centred on the patient experience, featuring a push-on-skin activation mechanism instead of a trigger button, a partially transparent housing that allows for real-time visualisation of the injection progress and a protected needle both before and after injection. The platform solution is suitable for needles with different diameters for subcutaneous applications, is compatible with spring forces of up to 100N and can be adapted for both 1.5 and 3 mL ISO cartridges.
Step by Step to Large-Scale Production
At the beginning of industrialisation, the basic concept of the Gx Inbeneo was optimised by the product development department in Wackersdorf in co-operation with Gerresheimer’s experts in its moulds and automation sectors, both in terms of design and function, including the addition of some features and consideration of design for large-scale production. Production processes were developed and validated, among which was the development of the sterilisation process. Furthermore, a sterile packaging system was developed and implemented and joining processes were defined and validated.
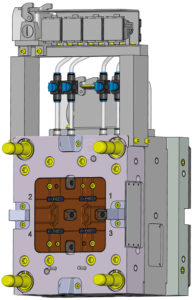
Figure 2: Cannula mould design.
Production Equipment Design and Construction
The Gx Inbeneo consists of two assemblies with a total of 12 injection-moulded components, meaning that 12 moulds need to be designed and qualified in-house by Gerresheimer’s moulds division. In this case, moulds with two-to-four cavities were built. Among them were moulds for over-moulding cannulas (Figure 2).
In the case of the mould for over-moulding the cannulas, the cannulas are inserted into the mould fully automatically with the “double grind” (cannulas sharpened on both sides). The automated tool takes over control of the cannulas from the robot and they are fixed in the mould by means of vacuums. The position of the inserted cannula is continuously monitored using sensors, ensuring a high level of process reliability.
Before the mould was built, a proof of principle (PoP) was carried out to ensure that the envisaged tool function sequence (cannula positioning, cannula fixation and monitoring) was expedient and feasible. The result of this PoP was so promising that the technology for positioning and fixing the cannula was used not only in the tool but also in end-of-arm tool handling in an almost identical way.
In preparation for production, a DfM package was created in co-operation with the development department. The component design was comprehensively evaluated for feasibility in the mould and production reliability to ensure the stable manufacturability of the components. This early co-ordination reduced the throughput time of the moulds, as the mould design began with optimised component data.
CONCURRENT PROJECT PHASES FOR FASTER IMPLEMENTATION
This project implemented an innovative approach by parallelising project phases II and III. This meant that the DfM phase and mould-making ran concurrently. While the feasibility of components and specifications was being co-ordinated between the moulds and development departments, the moulds were already being designed.
“This parallel approach necessitated close and intensive communication and co-ordination between all involved departments but, by parallelising the project phases, a significant reduction in project lead time was achieved.”
This parallel approach necessitated close and intensive communication and co-ordination between all involved departments but, by parallelising the project phases, a significant reduction in project lead time was achieved. Cross departmental, integrated project planning was carried using cPlace (Munich, Germany) management software. The high degree of standardisation designed into the moulds also contributed to increased efficiency. Standard parts were preferentially used to shorten mould-making timelines and improve maintainability.
This project introduced ground-breaking advancements in mould-making through the implementation of “digital part drawings”, with product manufacturing information dimensioning performed by the development department. These digital drawings enable clear surface allocation with the associated part dimensions, revolutionising the process of creating measuring programmes in the measuring room.
Additionally, article toleration was largely carried out by means of geometrical product specification (GPS) toleration. This method describes not only simple attributes, such as diameters, but entire geometric surfaces. This approach requires increased precision in the creation and optimisation of injection-moulding tools, as well as in process discovery and control. To be able to carry out appropriate tool optimisations for GPS-tolerated geometries, “reverse engineering” was sometimes used. This technique made it possible to correct the geometries and surfaces in three dimensions.
PRODUCT-SPECIFIC, HIGH-PERFORMANCE AUTOMATION SOLUTIONS FOR CLEANROOM PRODUCTION
Together with the development and construction of the special-purpose equipment required for moulds, Gerresheimer offers its customers high performance automation solutions (Figure 3). In the pharmaceutical industry, automation, precisely co-ordinated with the product, project and processes, can have a decisive influence on the quality and economic efficiency of production. Gerresheimer’s 120-member automation team supports product development with automation competency, develops automation solutions and specifies, designs, builds, procures and qualifies automation lines.
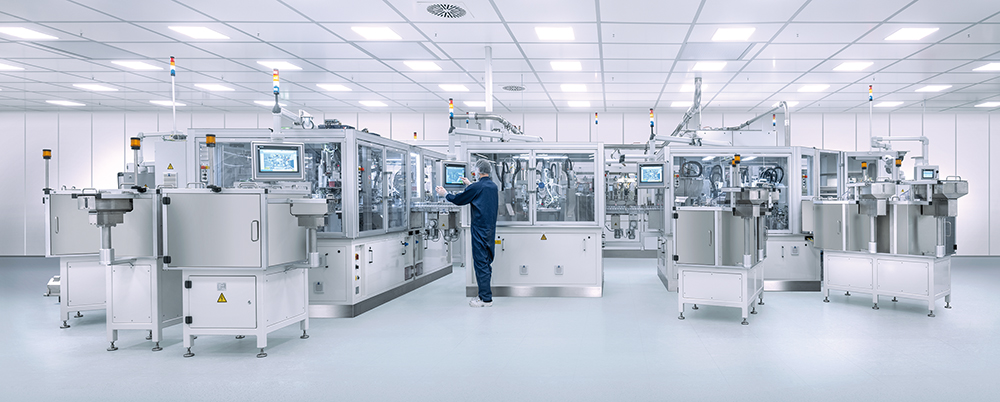
Figure 3: High-volume drug delivery device assembly room in an ISO Class 8 cleanroom in Pfreimd (Germany).
Gerresheimer not only covers the plastics sector with customer-specific assembly lines, testing systems (including pressure, flow, optical features and force displacement measurement systems), robots for inserting and removing parts, packaging systems, pre-series equipment and pharmaceutical assembly systems, it also develops innovative technologies for glass forming and automation. This has resulted in a new generation of glass-forming systems for syringe production at the TCC in Wackersdorf, which includes patented processes and offers faster cycle times and higher production accuracy.
“At Gerresheimer, automation is not an afterthought; it is an integral part of the product and process development journey.”
At Gerresheimer, automation is not an afterthought; it is an integral part of the product and process development journey. This proactive approach ensures that automation expertise and know-how are embedded from the very beginning, shaping the product concept throughout the design phase. This means that Gerresheimer does not wait until mass production to develop automation solutions, but instead develops them in the prototype and preseries phase, which leads to significant time savings in the industrialisation phase.
The creation of high-volume assembly lines is carried out by Gerresheimer’s internal machine builder in co-operation with renowned external machine builders. Product inspection is completed by intelligent inspection systems, some of which are developed internally by Gerresheimer.
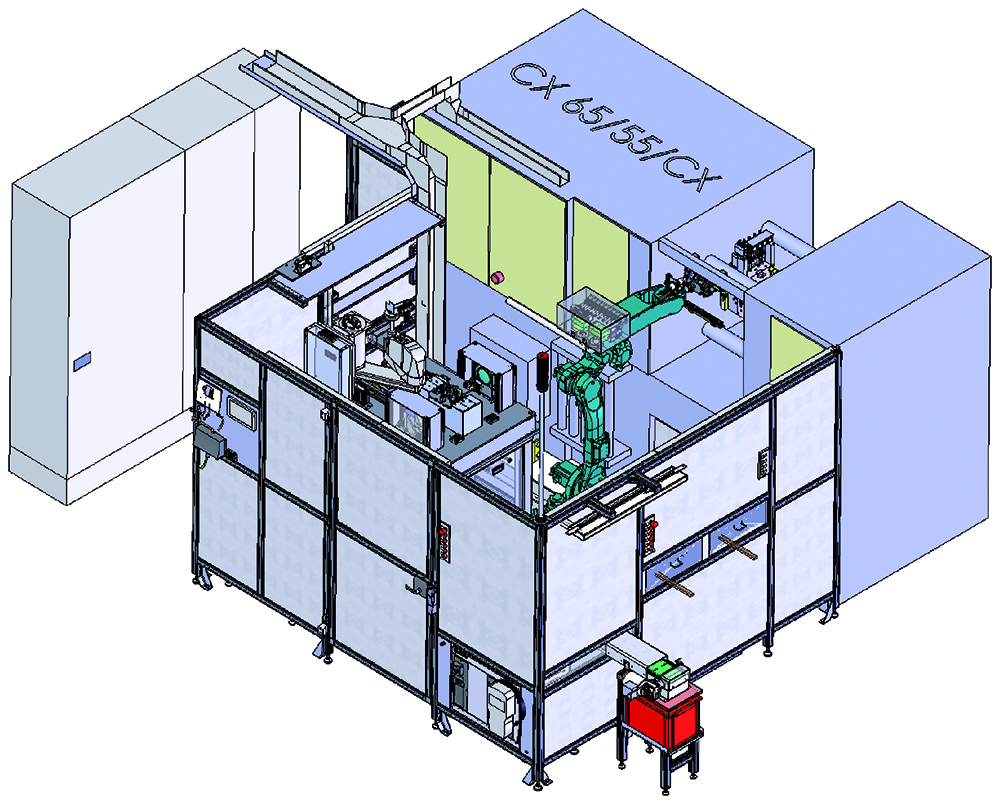
Figure 4: Handling system for cannula singulation, cannula insertion and finished part removal.
To meet the demanding production requirements of the Gx Inbeneo autoinjector, Gerresheimer built a highly sophisticated handling system (Figure 4). To facilitate the assembly of plastic components for the Gx Inbeneo autoinjector, Gerresheimer built three semi-automated assembly lines (Figure 5), in which the processes used for high- and low volume productions are equivalent.

Figure 5: Gerresheimer built three semi-automated assembly lines.
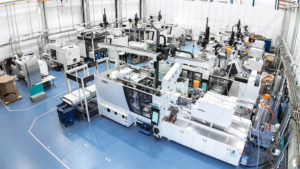
Figure 6: Small-batch production sampling facility in Wackersdorf, Germany.
Sampling
In 2023, Gerresheimer established a “small-batch production sampling” area in its Wackersdorf TCC, where “drive-in parts” – samples for running-in systems – can be produced in series quality (Figure 6). The establishment of this area reflects Gerresheimer’s adaptation to the evolving project landscape, characterised by an increasing prevalence of larges-cale industrialisation projects involving numerous moulds and complex automation systems. Industrialisation projects require a large number of drive-in parts in documented series quality at a very early stage for their high-volume assembly systems, which the small-batch production sampling area addresses perfectly.
Automated Handling of Tools
In contrast to development projects, industrialisation projects for high-volume production demand automated tool handling. This is essential to achieve the required cycle times, tool usage and production flexibility. The equipment in the small-batch production sampling area reflects this necessity. Currently, the area is equipped with 10 injection-moulding machines with clamping forces ranging from 175 to 420 tonnes.
QUALITY LABORATORY: SAFETY FIRST IN DRUG DELIVERY SYSTEMS
Recognising the paramount importance of safety in drug delivery systems, Gerresheimer meticulously conducts comprehensive testing throughout all stages of product development. This rigorous approach encompasses material analysis, geometric evaluation and functional assessments. Gerresheimer has a measurement laboratory for the geometric measurement of components, assemblies and finished products, a laboratory for material analyses and a laboratory for functional tests with product-specific testing equipment.
Optical and Tactile Technology and Industrial CT Scanning The use of a measurement laboratory with the most modern measuring equipment available ensures that complex mould inserts and filigreed injection-moulding parts or assembly units can be measured with extreme precision. For the Gx Inbeneo, all components were measured in this laboratory, and the industrial CT scanner was used to identify and address potential issues in the mechanical interaction of components early in the design process. The laboratory’s equipment includes various multi-sensor co-ordinate measuring machines for optical and tactile component measurements, universal co-ordinate-reading microscopes and an industrial CT scanner for the destruction-free measuring and testing of individual components or entire assemblies (Figure 7).
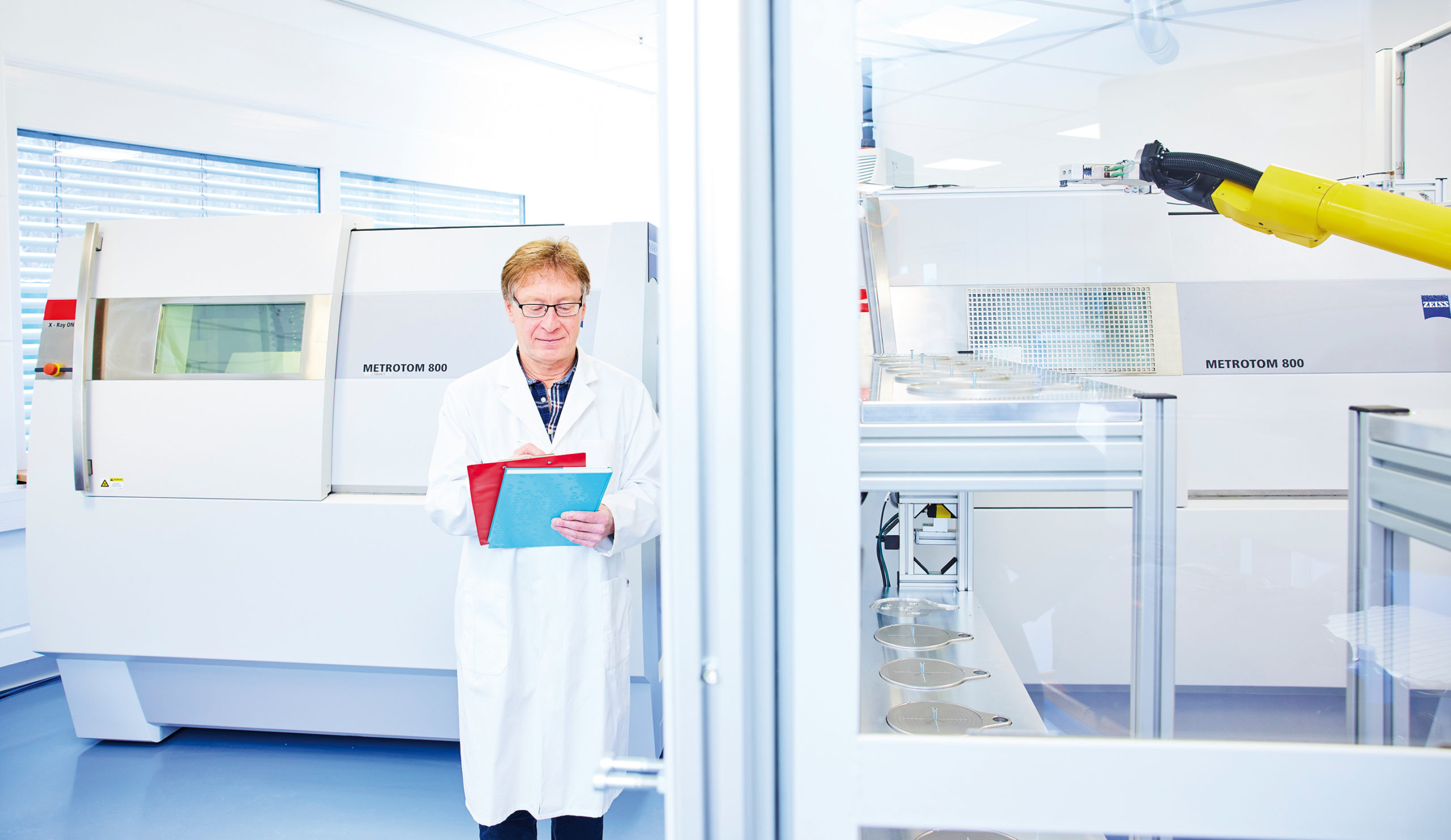
Figure 7: Industrial CT scanner for the destruction-free measuring and testing of individual components or entire assemblies.
Gerresheimer boasts a proven track record of applying CT technology to support numerous development projects, including the Gx Inbeneo autoinjector. This advanced imaging technique provides valuable insights into the mechanical stresses and resulting deformations experienced by a drug delivery device’s components. CT analysis helps to improve the understanding of force and pressure influences, as well as necessary safety distances and the required piercing depth. This technique makes it possible to optimise prototypes without physically damaging the components.
The advantages of CT scanning are manifold – it provides non-destructive testing and detailed analysis of components, ensuring exceptional product quality and increasing product reliability and safety. In particular, full device assemblies can be tested while assembled. There is no need for time-consuming disassembly, which could also potentially lead to a false result. Early fault detection reduces the need for costly adjustments in later phases of industrialisation and increases cost-efficiency. After all, the earlier errors in product design are detected by CT scanning, the less complex adjustments are to implement.
This makes design process optimisation possible, especially for simultaneous engineering tasks. The implementation of CT technology in the standardised Gerresheimer phase model leads to a common basis and consistently comparable consideration of results, starting in the concept phase and ending in series production. The accelerated exploitation of results can then be integrated into the product development process.
Product-Specific Functional Testing
In the functional testing lab, Gerresheimer develops and qualifies test methods to guarantee compliance with product-specific requirements. The company ensures more safety for patients through comprehensive testing of the physical product characteristics, product-specific performance tests and statistical data analysis during the product development cycle. For example, functional tests were conducted for Gx Inbeneo and aspects such as its spring forces, user forces and dosing times were measured.
SMALL-BATCH PRODUCTION WITH LARGE-SCALE PRODUCTION STANDARDS
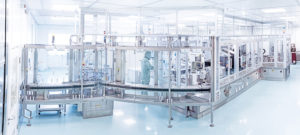
Figure 8: Small-batch production glass in a GMP Class C cleanroom in the TCC in Wackersdorf, Germany.
Prior to series production, drug delivery devices are put through an exhaustive approval process for which small numbers of units need to be repeatedly produced, such as for clinical samples, development samples or stability batches. Gerresheimer’s TCCs offer their customers their own production systems for this task, on which the quick and uncomplicated production of development samples, clinical samples or small-series units is possible at any point during a project (Figure 8).
Gerresheimer’s small-batch production also extends to primary packaging. In most cases, these are syringes and cartridges for sophisticated biologic drugs. Gerresheimer also covers the entire value chain and can produce clinical samples for approval or prototypes for process and technology development.
The Gx Inbeneo autoinjector is currently undergoing small-batch production at Gerresheimer’s Wackersdorf small-batch production facility. Small-batch production in this context refers to quantities in the single-digit millions range. Despite the smaller production scale, the small-batch production of the Gx Inbeneo adheres to high-volume standards. This means that the processes employed in small-batch manufacturing are equivalent to those used for subsequent high-volume production, production environment, data acquisition and documentation as well. In small-batch production, injection-moulding of the single plastic parts, semi-automatic and automatic assembly, and production tests and optical inspections are conducted as normal. The product is printed and packaged. Additionally, Gerresheimer performs sterilisation by means of irradiation, fumigation or autoclaving.
CONCLUSION
The successful industrialisation of a drug delivery device hinges on a synergistic combination of robust technical infrastructure, streamlined processes and a team of experienced specialists with a wealth of knowledge from past projects. Gerresheimer stands out as a premier partner in this regard, offering a comprehensive suite of technologies and services that span the entire product development and industrialisation lifecycle.
Early integration of DfM principles and the use of cutting-edge technologies, such as industrial CT scanning, are paramount for achieving time- and cost-effective development of high-quality drug delivery products. Gerresheimer prioritises these aspects from the outset, ensuring that products are designed with mass production in mind and tailored to meet the specific needs of the pharmaceutical industry. This applies from the initial idea development to series production and all phases in between.