To Issue 163
Citation: Rusch H, van den Brand R, “Implementing Industry 4.0: Lessons Learned Over Two Decades”. ONdrugDelivery, Issue 163 (Jul 2024), pp 12–15.
Herman Rusch and Rob van den Brand present four lessons for implementing Industry 4.0 technology and practices in the drug delivery industry, which IGS GeboJagema has learned during its own journey to Industry 4.0 over the past 20 years.
The market for drug delivery devices is skyrocketing, presenting the industry with the critical challenge of keeping pace with the growing demand both efficiently and affordably. This challenge is compounded by a shortage of skilled, technical workers in many countries. All these factors point towards a clear solution – Industry 4.0 (Figure 1). This broad term encompasses the digitalisation of manufacturing, opening the door to new technologies and highly advanced automation. Industry 4.0 (and its 5.0 successor) will become crucial over the next couple of decades for achieving the necessary production capacity to serve a growing world population. Moreover, it will allow the drug delivery sector to reduce costs while maintaining quality, thereby improving accessibility of healthcare to the global population.
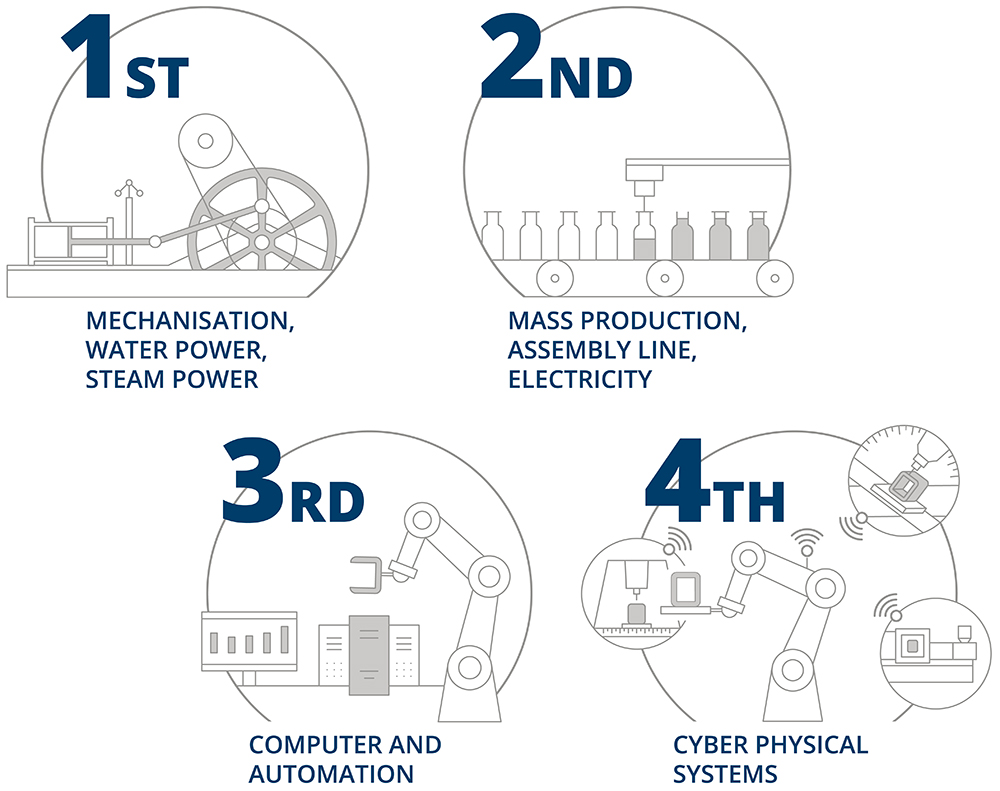
Figure 1: The four industrial revolutions.
IGS GeboJagema was one of the first organisations in the industry to place this insight at the core of its strategy. Over the past 20 years, the company has transformed its facility into a 24/7, lights-out, hands-off factory for the production of high-precision injection moulds. In 2015, the company’s automation reached the level where its factory was more productive outside business hours, after the IGS GeboJagema team had gone home, than it was during the working day. As evidence of this, the company’s revenue per employee is 75% higher than the market average.
Industry 4.0 has been a successful choice for IGS GeboJagema, but its implementation has certainly not been without its challenges. While it is easy to purchase robots and machines, the real challenges lie elsewhere. Implementing Industry 4.0 requires an entirely new way of thinking, a new organisational culture and carefully steering past numerous pitfalls.
INDUSTRY 4.0 IS ALL OR NOTHING
It is true that implementing Industry 4.0 can lead to enormous efficiency gains; however, it is crucial to be aware of its “all or nothing” nature. Every component in the production chain must work together flawlessly. A single weak link will disrupt production and negate the many possible benefits that Industry 4.0 can provide. This reality stresses the importance of precision and reliability in every part of the process. All systems, machines and tools, down to clamps and holders, must meet the highest standards. Constant monitoring and regular maintenance are essential to ensure that everything performs reliably, every second of every day. Achieving this requires a culture within the organisation of meticulous attention to detail and high quality standards. For most organisations, this requires a significant shift in culture.
PRIORITISE PROCESS
The real power of Industry 4.0 lies not just in cutting-edge technology, but in the processes that underpin it. As discussed, achieving a flawless production process is paramount. The key word here is “flawless”. Implementing Industry 4.0 is about systematically removing any room for error in the production process, from start to finish. For this reason, IGS GeboJagema did not start its implementation on the factory floor, but instead initially focused its knowledge and expertise on the engineering department.
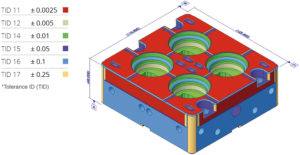
Figure 2: Model-based definition.
First, the company prioritised the manufacturability of its moulds, with the IGS GeboJagema team designing all new moulds not only to meet customer requirements but also to be easier to manufacture. This upfront investment prevented many possible complications during production. Second, the organisation made the switch from traditional 2D drawings to model-based definition (MBD). MBD uses 3D models that hold all necessary product information (Figure 2), eliminating the interpretation and communication issues that are inevitable when using 2D drawings. MBD creates a single source of truth that is accessible to all relevant departments and machines and allows for further automated programming in computer-aided manufacturing (model-based manufacturing) and metrology (model-based inspection).
In short, the first step is not to purchase machinery, but to lay the groundwork for a comprehensive Industry 4.0 ecosystem. This transformation demands a holistic organisational shift, making Industry 4.0 more akin to a new operational ethos than a technological solution (Figure 3).
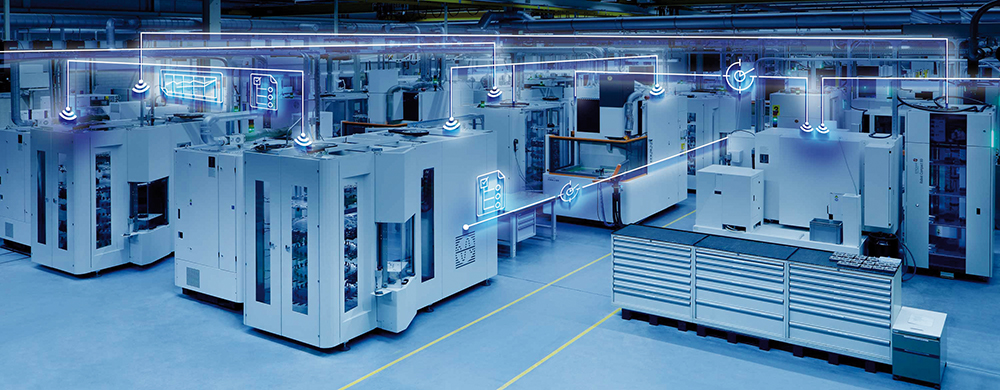
Figure 3: Industry 4.0 is more than a technological solution, it requires a shift in organisation-level thinking.
INVOLVE THE ENTIRE TEAM IN THE TRANSITION
“Companies that innovate and invest in automation become more competitive, thereby strengthening their employees’ job security.”
Industry 4.0 changes the way the entire organisation works. While some employees may welcome these changes with enthusiasm, many team members will be sceptical and have concerns. It is crucial to communicate to all employees why the shift to Industry 4.0 is necessary and what they can expect. One fear for employees is, of course, that their jobs will be replaced by machines, putting their livelihoods at risk. In truth, the opposite is the case. Companies that innovate and invest in automation become more competitive, thereby strengthening their employees’ job security. IGS GeboJagema is a prime example of this, having more than tripled its revenue over the past 10 years while also expanding its workforce.
Industry 4.0 will also change the nature of many jobs. The biggest shift will occur on the factory floor. In traditional factories, craftsmen use their technical skills to create a component from start to finish. In an automated production environment, on the other hand, these craftsmen use their expertise to focus on logistics, quality and production management. Their work involves using an enterprise resource planning system and 3D files to ensure that their part of the production process is executed flawlessly.
Many employees enjoy working with cutting-edge technology and find that it enriches their work. In particular, IGS GeboJagema has learned that it has become easier to recruit young talent who find it more appealing to work in a high-tech environment. Between 2012 and 2023, the average age of the company’s employees dropped from 48 to 38. Of course, the reality will be that a number of team members will find the new way of working does not suit them. However, with abundant and clear communication, IGS GeboJagema has found that this is the case for only a small minority of employees.
INDUSTRY 4.0 REDUCES FLEXIBILITY
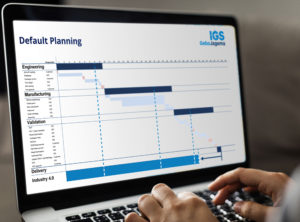
Figure 4: Standardisation is an essential part of Industry 4.0.
Standardisation is key for Industry 4.0 to succeed (Figure 4), but standardisation inevitably also makes a production environment more rigid and inflexible. One challenge for IGS GeboJagema has been to make room for quick responses to emerging issues. For instance, if, during validation, it is discovered that a mould requires adjustments in the milling department, this extra work can disrupt the entire production process.
To navigate this challenge, IGS GeboJagema has established a dedicated quick-response manufacturing department. This separate, flexible and multifunctional team is focused on addressing immediate and unforeseen needs. It ensures that rapid adjustments and validations can be handled without disturbing the main production flow. This approach not only preserves the efficiency and standardisation of the automated process, but also introduces an essential layer of flexibility.
BEYOND INDUSTRY 4.0: THE FUTURE OF THE HEALTHCARE INDUSTRY
Industry 4.0 is not without its challenges and adopting it is not an overnight process. However, IGS GeboJagema believes that this direction offers enormous potential for the industry. The benefits of the transition have been proven, and there are still many opportunities to explore for the company, ranging from automated milling corrections and automated guided vehicles to artificial intelligence (AI).
But Industry 4.0 is not the endpoint – the transition towards Industry 5.0 has already begun (Figure 5). This next phase is centred on the synergy between humans, technology and the environment. It promises to enhance not only the efficiency but also the sustainability of production methods, through technologies such as autonomous mobile robots and further integration of AI, not only in production but also in office operations.
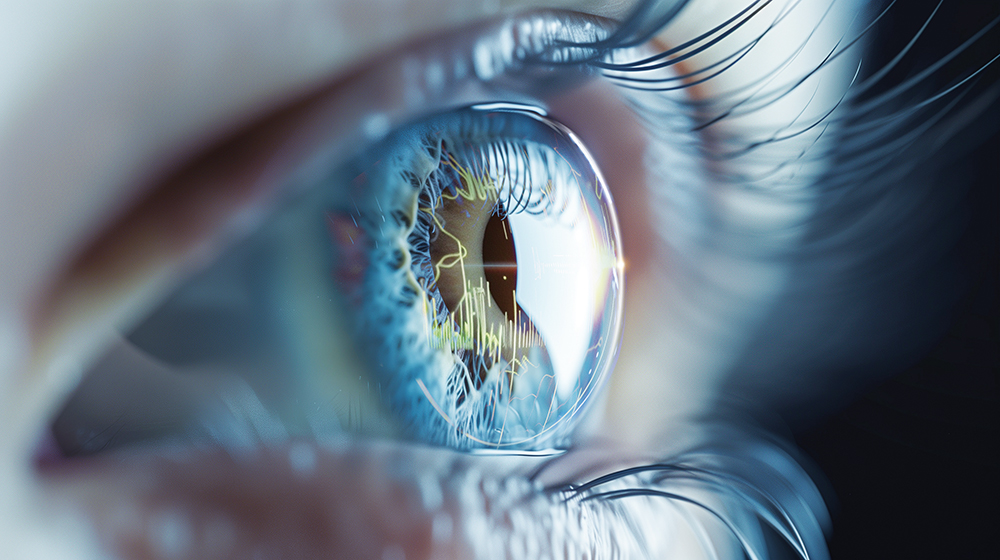
Figure 5: The transition to Industry 5.0 has already begun.
IGS GeboJagema believes that it is critical for the drug delivery industry to embrace these technological advancements. The transition to Industry 4.0 and 5.0 is how the industry will ensure that healthcare becomes more affordable and accessible to the billions of inhabitants of the planet.
Discover more about IGS GeboJagema’s mold-making expertise in the drug delivery sector and the wider healthcare industry, here.