To Issue 163
Citation: Vaccarella L, “Future-Proofing Your Drug Delivery Device: Considerations for Effective Design”. ONdrugDelivery, Issue 163 (Jul 2024), pp 6–9.
Lorenzo Vaccarella highlights six critical areas to consider early in the drug delivery device development journey. He discusses how strategically investing time during the early stages of the design cycle and throughout development can ultimately save both time and cost down the road when the product is being manufactured and deployed into the market.
DESIGN USABILITY
Injectable drug delivery device designs come in diverse forms, from pen injectors to autoinjectors and wearables. When designing such a device, it can be can be difficult to convey essential user requirements to design engineers in the initial sketches, potentially leading to challenges later in development. Conducting a voice of customer (VOC) exercise early on is crucial to understanding user needs and achieving the most suitable design for patients.
This early engagement provides ample time for necessary design adjustments, thus preventing wasting development time on creating prototypes, testing samples or manufacturing production parts. There have been many projects where design changes have stemmed from VOC exercises. One such project involved a glucose monitoring wearable device where the VOC exercise revealed that a light was required to enable users to view the information displayed by the device in dark or poorly lit areas.
Sometimes, multiple prototype iterations are required to get the best functioning product that meets all user requirements. Paragon Medical has addressed this challenge with its Advanced Surgical Innovation Center (ASIC) in Southington (CT, US) (Figure 1). This facility enables the company to provide early-stage product samples in just 1–2 weeks, facilitating VOC exercises and enabling swift modifications to the design without jeopardising launch schedules.
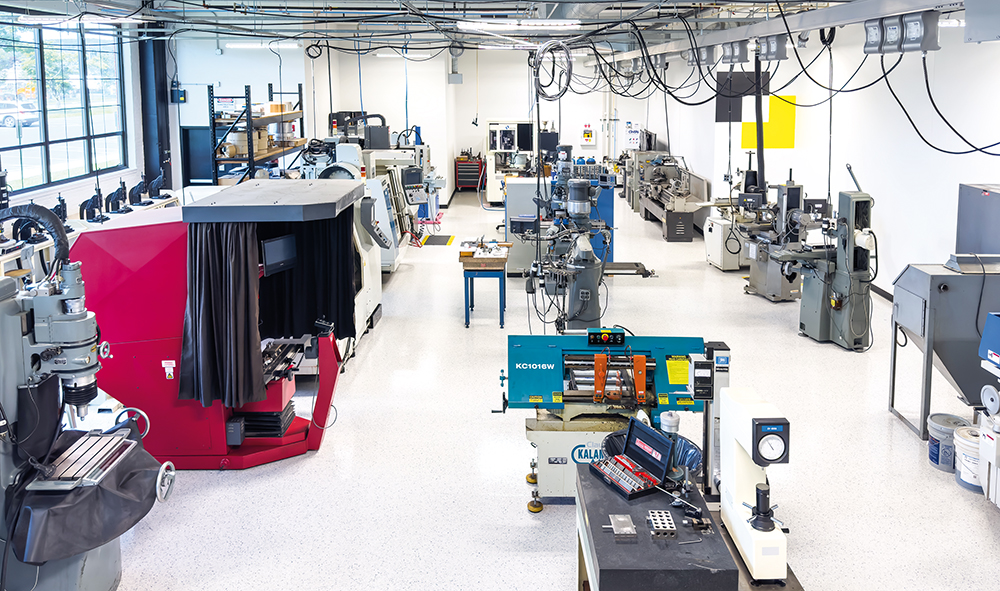
Figure 1: Paragon Medical’s Advanced Surgical Innovation Center (ASIC) in Southington (CT, US) is dedicated to rapid prototyping, process innovation and equipment development.
“Understanding how a drug is to be targeted or delivered is paramount to the overall design of the device.”
When it comes to designing drug delivery devices, understanding how a drug is to be targeted or delivered is paramount to the overall design of the device. Integrating human factors engineering very early on in a project is a critical aspect of drug delivery product development. Another element to understand is how patients and clinicians will interface with the drug delivery device itself, as this will help a designer further optimise the usability aspect of the device, as well as design-in features that will help minimise misuse of the device. Topics such as this are important to discuss with the manufacturer of the drug delivery device so that design optimisations can take place during the concept phase that will result in the most effective and user-friendly design possible.
MATERIALS SELECTION
Once the design concept has been developed, it is crucial to select the appropriate materials. A design engineer must first gather detailed information about the drug that is to be administered. If a material safety data sheet (MSDS) has been published for the drug, information such as proper storage and handling, toxicity and flammability can be easily obtained, which proves to be very useful for selecting the appropriate material. In the absence of a product specification sheet or MSDS, collaboration with customers is required to define these requirements.
Additionally, several other properties must be considered, including the target weight of the device, mechanical strength, chemical resistance, friction, viscosity and wear resistance. For example, when designing the outer shell of a combination product device, it is important to select a durable and cost-effective material that will withstand impact and drop tests without compromising the “feel” of the outer shell. It is also crucial to factor in testing and processes such as transit, accelerated ageing and sterilisation. By thoroughly evaluating these aspects, it is possible to ensure that the product will withstand various storage environments and maintain its integrity and functionality throughout its lifecycle.
“By developing a testing plan early and conducting critical tests on the drug delivery device prototype, it is possible to see early trends of how the device will perform in its final state.”
VERIFICATION AND VALIDATION TESTING
A common pitfall during drug delivery device development is delaying verification and validation (V&V) testing until after the design has been frozen and the V&V test part build completed, only to encounter testing failures that require subsequent design changes. An example of this is performing accelerated ageing testing on the packaging of a medical device and receiving failing test results. This necessitates a redesign of the display box that houses the product. By developing a testing plan early and conducting critical tests on the drug delivery device prototype, it is possible to see early trends of how the device will perform in its final state. The device does not need to be fully developed, nor does the testing need to be exhaustive. Benchmark variations can provide sufficient insight for determining if a design should be re-evaluated before investing in materials and equipment for production-equivalent parts.
Paragon Medical’s design and development team is proficient in a wide range of V&V testing methods and can execute these tests on behalf of customers to expedite the development process. Paragon’s testing services include mechanical, electrical, biocompatibility, transit, accelerated ageing and real-time ageing. The company can co-ordinate any additional tests agreed upon by the design and customer teams. Additionally, it performs design validation testing that simulates real-world conditions, such as animal studies, clinical trials and sterilisation validations (gamma, ethylene oxide, hydrogen peroxide, etc.). The company’s dedicated testing labs are equipped to handle these comprehensive evaluations.
“Once the design has been validated and initial testing completed, it is time to consider how the device will be scaled up for manufacturing.”
MANUFACTURING SCALE-UP
Once the design has been validated and initial testing completed, it is time to consider how the device will be scaled up for manufacturing. When evaluating potential manufacturers, it is crucial to assess their experience and capability in high-volume manufacturing. Knowing that a manufacturing organisation has automation capabilities available within its infrastructure can be very attractive to a customer looking to scale up, as automation allows for the efficient mass production of drug delivery devices to meet increasing demand.
Furthermore, manufacturers with comprehensive capabilities – such as full-scale assembly, in-process testing, sterilisation and packaging – can offer significant added value by accelerating the time to market and reducing complexity in the supply chain. In response to the increased consumer demand for drug delivery devices, Paragon Medical has recently completed the expansion of its campus in Poland by adding another building dedicated to drug delivery device manufacturing (Figure 2). This expansion provides customers with the necessary space to scale up their drug delivery platforms efficiently.
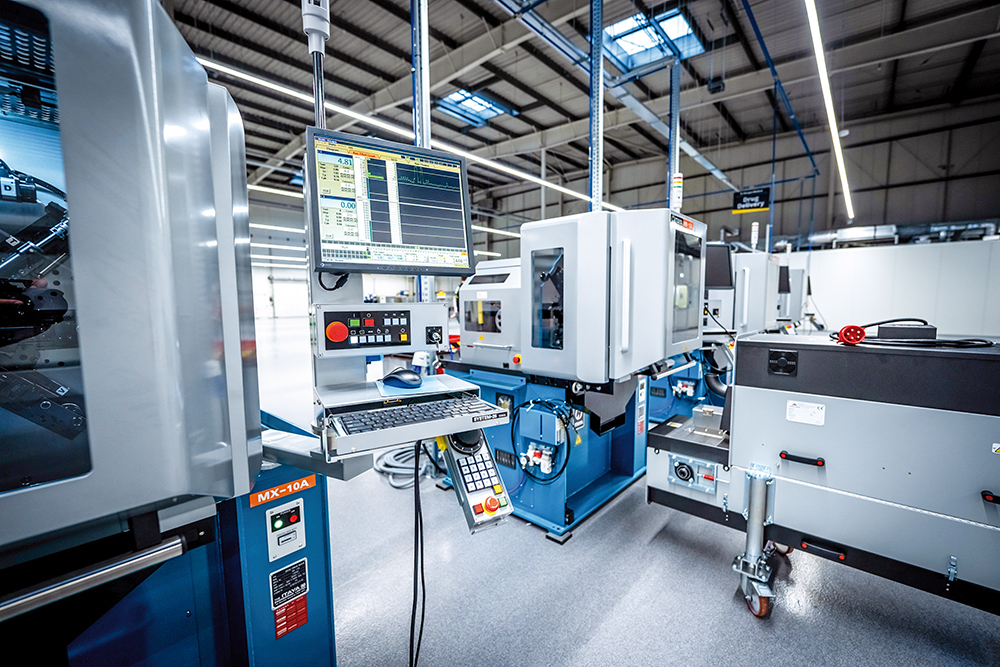
Figure 2: Paragon Medical’s new 65,000 square foot manufacturing facility in Siechnice (Poland) dedicated to serving drug delivery device customers.
“Evaluating the manufacturing process early on can help identify high-cost operations and opportunities for efficiency.”
Evaluating the manufacturing process early on can help identify high-cost operations and opportunities for efficiency. At this stage, the development team can brainstorm modifications to the device design, such as performing a design-for-manufacturing evaluation to understand which parts can be injection moulded or fabricated out of metal. It is crucial to conduct these evaluations during the development phase, before the design is frozen and testing is completed, to avoid timeline delays and budget overruns from change orders during production. With this in mind, Paragon Medical engages its new product introduction (NPI) team, which focuses on manufacturing, alongside its new product development (NPD) team early in the product development phase. Involving manufacturing teams from the outset ensures that they understand the product thoroughly and are well prepared to devise effective manufacturing strategies.
REGULATORY REQUIREMENTS
The ever-changing regulatory environment continues to present the biggest challenge for medical device companies working on bringing drug delivery devices to market. The primary question to address is how to evaluate the safety and efficacy of such combination products. Therefore, it is crucial for manufacturing organisations to involve a regulatory consultant early in the project. This allows the regulatory team to participate in the product development process and assess regulatory implications as the project evolves.
SUPPLY CHAIN MANAGEMENT
Balancing the demands of meeting market expectations while also capitalising on emerging opportunities can be a significant task. Moreover, managing a supply chain in today’s complex environment adds another layer of challenge. Manufacturing organisations must inspire confidence and trust among their customers by maintaining a robust and secure supply chain, especially knowing that procuring the required drug media is crucial for the commercial success of the drug delivery device.
“It is essential to ensure that all materials are sourced cost effectively and meet customer requirements for timelines, quantities and quality.”
To support mass production, it is essential to ensure that all materials are sourced cost effectively and meet customer requirements for timelines, quantities and quality. Supply, inventory and operations planning (SIOP) teams should collaborate closely with customers to facilitate conversations that drive cross-functional alignment and effective planning. A comprehensive SIOP process can help to foresee and eliminate obstacles and ensure that launch objectives are met.
CONCLUSION
It is of the utmost importance to maintain a flexible mindset early in the development phase of a drug delivery device. Conducting prototyping in the concept phase, engaging in VOC research, performing benchmark testing, reviewing the manufacturing process and consulting with regulatory affairs all contribute to a comprehensive understanding of the requirements for a successful drug delivery product. Delaying these essential exercises until after the design has been frozen can lead to prolonged redesign processes, significantly impacting budgets and timelines. By investing extra effort in due diligence during the early stages of product development, companies can confidently progress towards full-scale commercialisation better equipped to navigate challenges and capitalise on opportunities in the dynamic landscape of drug delivery device innovation.
Find out more about Paragon Medical’s offering in the drug delivery devices space, here.