To Issue 165
Citation: Rusch H, van Voorst S, “From Vision to Victory: Building a Hands-on ESG Framework”. ONdrugDelivery, Issue 165 (Sep/Oct 2024), pp 50–53.
Herman Rusch and Steven van Voorst discuss the steps that IGS GeboJagema has taken to provide its environmental, social and governance efforts with a robust structure to build on and how doing so has made those efforts more effective and provided the company with clear, meaningful and measurable targets to work towards.
The role of environmental, social and governance (ESG) factors has significantly transformed in recent years. Consumers, clients, employees, investors and other stakeholders now increasingly expect organisations to align their operations with greater societal interests (Figure 1). This development is reflected in regulatory developments as well, such as the upcoming EU Corporate Sustainability Reporting Directive (CSRD). In short, what was once considered a “nice to have” for companies – corporate social responsibility – has become a critical component of any corporate strategy.
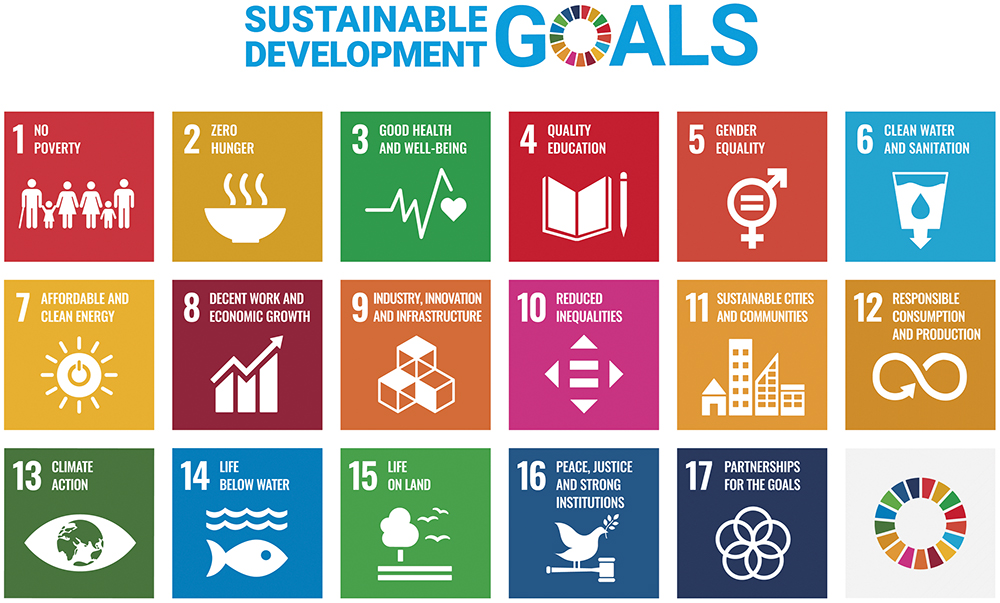
Figure 1: The UN’s sustainable development goals.
For the high-precision mould maker IGS GeboJagema, ESG considerations are not new. Corporate social responsibility has always guided its decisions and actions, whether it concerned being a good employer, reducing carbon emissions or maintaining high standards of ethical behaviour. However, the standards and expectations surrounding ESG have matured significantly. Moreover, IGS GeboJagema has grown rapidly over the past decade, with its team more than doubling in size. Considering these factors, the need arose for a more structured, more comprehensiveapproach. Rather than just addressing immediate and specific issues, this new approach examines IGS GeboJagema’s entire operation to identify the key areas the company should focus on to effectively address ESG topics in the future.
DEVELOPING A STRATEGIC ESG PLAN
The development of a comprehensive, strategic plan to address ESG principles was, of course, not an overnight process. The plan was developed over the course of six months. The first crucial step was to acknowledge the need for increased expertise in ESG matters. To address this, IGS GeboJagema partnered with the specialist consultancy 2BHonest (Hilversum, Netherlands) and hired a dedicated Quality, Health, Safety and Environment (QHSE) Manager.
To create a reference point for setting realistic yet ambitious goals, IGS GeboJagema assessed the wider industry’s level of development in ESG matters. It found that most of its customers were more advanced in their ESG practices, while IGS GeboJagema was ahead of its peers and suppliers. Next, the company conducted a double materiality analysis. This process involves assessing both the financial impact of ESG factors on the company and the company’s impact on environmental and social factors. By identifying and prioritising the ESG themes that were most relevant and impactful for IGS GeboJagema and its stakeholders, the analysis ensured a comprehensive understanding of the areas that required focus.
EU guidelines list 29 key performance indicators from which companies must select those most relevant to their sector and organisation. Based on the double materiality analysis, IGS GeboJagema identified seven key themes where it could make the biggest impact:
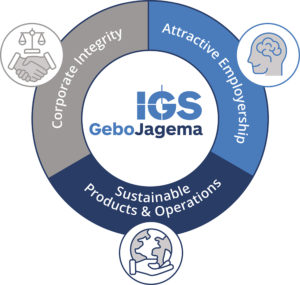
Figure 2: The three pillars of IGS GeboJagema’s ESG framework.
- Greenhouse gas (GHG) emissions related to business activities
- Circular economy practices
- Diversity, equity and inclusion
- Training and development of own employees
- Own working conditions
- Responsible business
- Product accessibility for end users.
These themes were divided into three pillars: environmental, social and governance (Figure 2).
PILLAR 1: ENVIRONMENTAL
GHG Emissions Related to Business Activities
The reduction of GHG emissions is a major goal for IGS GeboJagema, as it should be for any company. This effort began with creating a detailed picture of its carbon footprint across the three emission scopes. Scope 1 covers direct emissions from owned or controlled sources, Scope 2 includes indirect emissions from the generation of purchased energy and Scope 3 encompasses all other indirect emissions that occur in the value chain. This last scope includes categories such as purchased goods and services, capital goods, upstream transport and distribution, business travel, employee commuting and the use of sold products. IGS determined that its GHG emissions were divided across the three scopes as follows:
- Scope 1: 0.27%
- Scope 2: 0.01%
- Scope 3: 99.72%.
The picture that emerged was one of a company that has already made considerable efforts in terms of sustainability. Over the past few years, IGS GeboJagema has targeted much of the low-hanging fruit to reduce emissions, implementing measures such as using state-of-the-art, energy-efficient equipment in its factory, installing LED lighting, adopting electric vehicles, purchasing green energy and using responsibly sourced resources and recycled steel of the highest possible quality. As a result of these targeted efforts, Scope 1 and 2 emissions had already been drastically reduced, with only a minimal contribution to the overall emissions, with Scope 1 accounting for 0.27% and Scope 2 for 0.009%.
Therefore, it was clear that Scope 3 emissions were where the most progress could be made (Figure 3). Within this scope, the category “use of sold products” stood out as the largest contributor, accounting for 82% of the total footprint. Therefore, it was determined that IGS GeboJagema could make the biggest impact by manufacturing innovative, energy-efficient injection moulds. The company has already made progress by developing “green moulds” that prioritise both quality and sustainability. These moulds use smart insulation and efficient equipment, such as thermolators, hot runners and robot systems, to enhance energy efficiency and reduce cycle time.
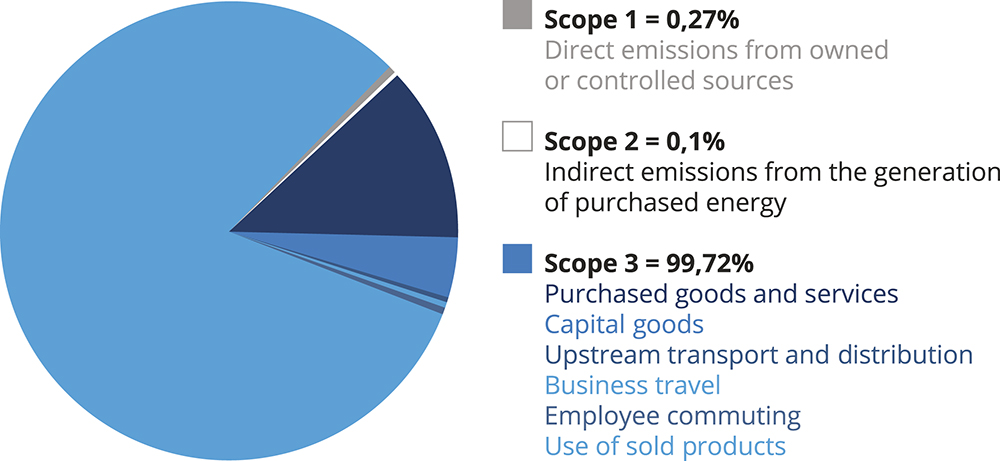
Figure 3: Scope 3 accounts for the vast majority of emissions for IGS GeboJagema.
Moreover, the mould maker’s engineering team can make a huge impact on GHG emissions in the product design phase. For example, for a product in the ophthalmic market, the team managed to reduce wall thickness of a component by 15%. This resulted in a faster cycle time, allowing for greater output with the same energy consumption. It also reduced waste material, which further reduced the product’s GHG emissions. This is just one example of how smart engineering solutions can enhance sustainability, providing value in five areas: time, material, energy, waste and emissions.1 In light of this, IGS GeboJagema has set the following key performance indicators:
- By 2030, the company aims to reduce Scope 1 emissions by 20% compared with 2023 levels
- By 2030, the company aims to reduce Scope 2 emissions by 20% compared with 2023 levels
- By 2030, the company aims to reduce Scope 3 emissions by 40% compared with 2023 levels.
Circular Economy
IGS GeboJagema is committed to integrating circular economy practices into its operations, focusing on reducing waste and promoting the use of recycled materials. It has determined two goals in this area:
- By 2027, all packaging materials used are to be recycled and certified, meeting the Forest Stewardship Council’s packaging standards
- By 2030, 85% of the total weight of the steel used for critical components is to come from recycled material – the company already uses recycled steel and aims to increase this percentage by sourcing the highest quality steel from Uddeholm (Hagfors, Sweden), which consists of 85–95% recycled materials.
Additionally, encouraging clients to use recycled plastic seems like a logical step for an injection mould maker. However, due to the strict regulations within the medical sector, widespread adoption of this practice is not expected in the short term. Another hurdle is the current use of different types of resin for various device components, such as polypropylene (PP) for caps, polybutylene terephthalate (PBT) for housings, and acrylonitrile butadiene styrene (ABS) or polyoxymethylene (POM) for technical parts. Design houses and original equipment manufacturers are working towards standardising these materials to make devices easier to recycle.
Despite these obstacles, IGS GeboJagema expects that market demands and regulations will eventually lead to the use of recycled material in the medical field as well. The company is proactively developing expertise and knowledge with which to advise its customers on this matter and is taking steps to be ready to implement these sustainable practices when the time is right.
“IGS GeboJagema aims to be an attractive employer by fostering a diverse and inclusive workforce and a work culture that promotes professional growth and employee wellbeing.”
PILLAR 2: SOCIAL
IGS GeboJagema aims to be an attractive employer by fostering a diverse and inclusive workforce and a work culture that promotes professional growth and employee wellbeing. This objective encompasses three key themes, for each of which IGS GeboJagema has set a measurable goal:
- Diversity, equity and inclusion: IGS GeboJagema strives for a gender composition that reflects technical education graduates in the Netherlands, aiming for at least 15% female representation.
- Training and development of employees: IGS GeboJagema has established a concrete budget per year per employee for training and education. The goal is for at least 70% of employees to use these training opportunities.
- Working conditions: Ensuring a supportive and motivating work environment is a priority. The company aims to achieve an employee satisfaction score of at least 70%, outperforming the annual employee engagement average of 70%.2
In addition to these goals, IGS GeboJagema is working towards certification as a “Great Place to Work”. This certification is not seen as an end goal but as a natural outcome of the company’s efforts to implement effective actions and create a positive workplace. By focusing on these areas, IGS GeboJagema aims to cultivate an environment where everyone feels welcome and at home, allowing them to thrive and contribute to the company’s success.
Finally, IGS GeboJagema recognises its social obligation to keep its products accessible to people worldwide. The company achieves this by adhering to all governmental and EU regulations, ensuring compliance and maintaining the accessibility of its products to end users worldwide.
PILLAR 3: GOVERNANCE
Effective governance is essential for maintaining the integrity of any organisation. The right framework of policies and processes can ensure that an organisation operates in a transparent, ethical and accountable manner, while fostering trust among stakeholders, mitigating risks and ensuring compliance with legal and regulatory requirements. It is the best way to address the key theme “responsible business”.
For regulatory requirements, IGS GeboJagema works with an external consultancy to map out all applicable laws and regulations, confirming that the company is fully compliant. This partnership also ensures that the organisation stays updated on any changes in regulations. In addition, IGS GeboJagema aspires to maintain the highest ethical standards, for which it has set the following key performance indicator: zero cases of corruption and bribery per year.
IGS GeboJagema has also updated its code of conduct for both internal and external operations. These policies clearly communicate the company’s expectations of itself and its suppliers. Detailed information about the external code of conduct can be found on the company’s website.
IMPLEMENTING THE STRATEGY
IGS GeboJagema believes in a practical, hands-on approach to implementing its ESG strategy that embeds it into the fabric of the organisation. This means that ESG initiatives are not just top-down directives but are supported and carried out by employees at all levels as part of their day-to-day tasks.
To achieve this, IGS GeboJagema has established several working groups, each dedicated to one of the three ESG pillars. These groups comprise members from across the organisation, such as human resources (HR), works council members, management and other employees, ensuring diverse input and broad engagement, as well as relevant expertise, in every group. Each group has a team lead with a relevant function in the organisation. The QHSE manager leads Environmental, the HR manager heads Social and the Chief Financial Officer is team lead for the Governance group.
IGS GeboJagema believes this grassroots engagement is crucial for the successful implementation and sustainability of its ESG strategy, making it a living part of the organisational culture and ensuring continuous progress. Through this approach, the company aims to improve its performance on the EcoVadis sustainability assessment every year to reach the EcoVadis Gold status, which is awarded to the top 5% of companies assessed. This commitment reinforces IGS GeboJagema’s leadership position as the mould maker sets a benchmark for sustainability in the industry.
THE POWER OF STRUCTURE
A large number of initiatives related to ESG were already in place within IGS GeboJagema, but the absence of a structured approach limited their effectiveness. By developing a comprehensive and strategic ESG framework, the company can now operate more effectively and consistently to ensure that ESG principles are systematically integrated into all aspects of the organisation’s activities and become part of the fabric of the company culture.
“IGS GeboJagema does not view ESG as obligations to comply with, but as the cornerstone of a lasting, sustainable future for the company and its employees.”
IGS GeboJagema does not view ESG as obligations to comply with but as the cornerstone of a lasting, sustainable future for the company and its employees. Its systematic and structured approach to ESG ensures that IGS GeboJagema meets the evolving demands of customers in this area, reaffirming the company’s position as a front-runner in the market. It is the key to making regular, measurable progress to achieve sustainability goals and create a lasting positive impact on society and the environment.
REFERENCES
- Jansen A, Cisliek R, “Green Thinking: How to Become a More Sustainable Organisation”. ONdrugDelivery, Issue 153 (Oct/Nov 2023), pp 22–25.
- “State of the Global Workplace”. Report, Gallup, 2024.