To Issue 168
Citation: Chardonnet A, “Interview: Sustainability at the Heart of Aptar Pharma’s Expansion”. ONdrugDelivery, Issue 168 (Jan 2025), pp 72–76.
Q What is Aptar Pharma’s strategy when it comes to sustainability?
A At AptarGroup, sustainability is at the centre of what we do. Most notably, this has been recognised by leading institutions through a series of awards, including Forbes’ “World’s Top Companies For Women 2024”, Time Magazine’s “World’s Most Sustainable Companies 2024” and USA Today’s “America’s Climate Leaders” in 2023 and 2024. Aptar is also an active member of the UN Global Compact, the Ellen MacArthur Foundation and the World Business Council for Sustainable Development.
Aptar is a global leader in drug and consumer product dosing, dispensing and protection technologies across multiple markets, including pharmaceutical, beauty, food, beverage, personal care and home care. As a leader in the development and manufacturing of more sustainable closure solutions, Aptar is also leading the way in designing innovative drug delivery solutions with our Futurity® platform, which features solutions for improved sustainability, such as recyclable products, waste reduction, CO2 footprint reduction and the use of alternative materials, including bio-feedstock.
The Futurity platform includes pressurised metered dose inhaler technology for low global warming potential propellant use, nasal spray pumps, and ophthalmic and dermal drug delivery solutions that embody our commitment to sustainability and circularity for addressing the waste crisis. Beyond product development, Aptar Pharma is also dedicated to making its manufacturing operations landfill free, saving energy at every step of its manufacturing processes and promoting inclusion, equity and belonging at work.
Q For injectables, how do you align with the company’s global sustainability strategy?
A Contrary to other drug delivery solutions in Aptar’s portfolio, which are mostly plastic based, Aptar Pharma’s injectables solutions are made of rubber (Figure 1). These closure solutions are in direct contact with the drug and must be used in conjunction with glass containers. As these containers come into contact with patients – whether via the intravenous, intramuscular or subcutaneous route – packaging for injectables is considered biohazard waste and treated as such. Under the current pharmaceutical waste management situation, rubber components are highly unlikely to enter any recycling route after being used.
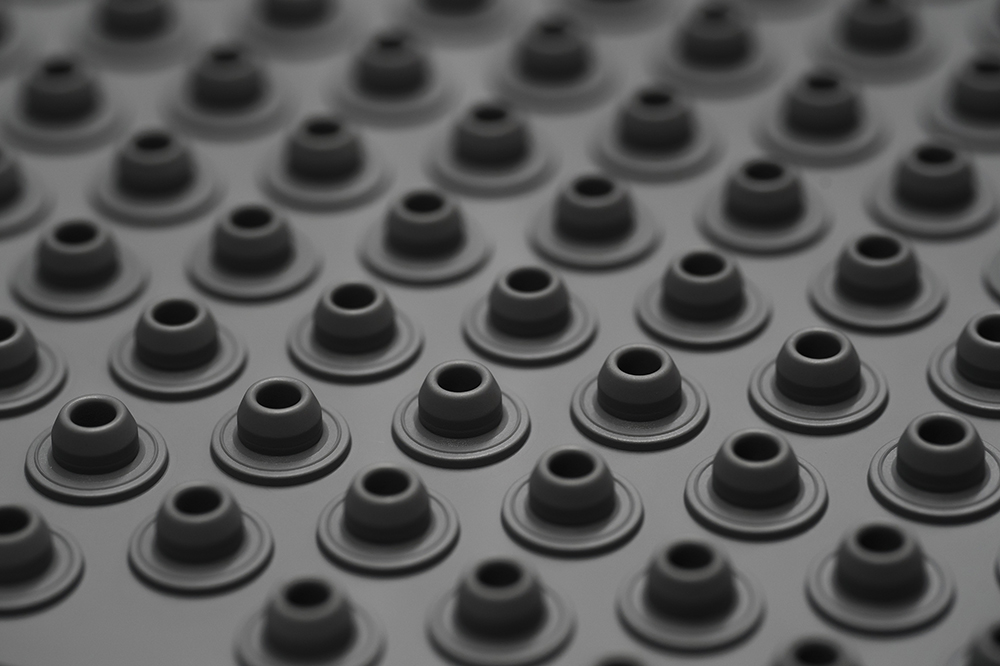
Figure 1: Aptar Pharma vial stopper sheet. Downstream vulcanised rubber scraps enter a recycling network.
“All of Aptar Pharma’s injectables manufacturing sites are certified landfill free through our internal programme, which was achieved through the establishment of a vulcanised rubber waste recycling network, allowing us to recycle at least 90% of our rubber waste each year.”
We must therefore find other levers to fulfil our sustainability objectives, which we do by focusing on ensuring that our operations are more sustainable. All of Aptar Pharma’s injectables manufacturing sites are certified landfill free through our internal programme, which was achieved through the establishment of a vulcanised rubber waste recycling network, allowing us to recycle at least 90% of our rubber waste each year.
Additionally, all of the electricity we use within our injectables sites comes from renewable sources. Most importantly, as part of our global expansion, we have been implementing energy-saving initiatives, aiming to reduce natural gas consumption at our facilities worldwide. These changes have resulted in significant reductions in natural gas consumption at some of our sites, reducing the greenhouse gas emissions associated with our operations.
Q How do you manage your energy use at the site level?
A In order to meet our energy targets, we set up dedicated teams and launched a series of projects around four key pillars. First, we performed comprehensive energy assessments at the site level. During these assessments, tracking indicators were defined for all our processes and benchmarked against other manufacturing sites within the company and the industry. We then developed an energy-saving culture within our factories and implemented short-term action plans to reduce unnecessary energy use throughout the factories.
To take this initiative further, we brought in external agencies to perform an energy audit for us to identify long-term energy-saving opportunities and prioritised high-impact actions. At some of our sites this was done in collaboration with the French CertiNergy agency, a governmental partner that supports French-based industries in transitioning towards cleaner manufacturing.
Based on this audit, we identified new technologies with high energy-saving potential and launched a series of projects to modernise our utilities. Once again, the CertiNergy agency partnership played a central role in supporting the implementation of these new utilities and ensuring that results were in line with expectations.
Q Can you provide an example of an energy savings project and the results you have seen?
A One of the most energy-intensive processes in our factory is the production of hot water to transport heat. This is used for both the production of water for injection (WFI), which is the primary element for washing all of our rubber components, and for heating the factory during the cold months of the year.
In our Granville (France) factory, this process was handled by two independent boilers, which were replaced by a single state-of-the-art steam boiler. In addition to having twice the capacity of previous boilers in tonnes of steam produced per hour, it is also digitally regulated to optimise energy consumption. Most importantly, new air compressors and chillers were installed and equipped with heat recovery mechanisms, allowing the heat to be redirected to the primary boiler to further reduce the consumption of natural gas.
By reducing the number of boilers, modernising our utilities and implementing heat-recovery mechanisms, we reduced the consumption of energy for building heating by 99.7% and for WFI production by 15%. This energy was formerly coming from natural gas, so these savings equated to an estimated reduction of 814.5 tonnes of CO2.
“Following the success of this project, we have initiated a similar project for upgrading the boiler systems in our other manufacturing site in Brécey and are continuing to upgrade our utilities to eliminate energy waste.”
Following the success of this project, we have initiated a similar project for upgrading the boiler systems in our other manufacturing site in Brécey (France) and are continuing to upgrade our utilities to eliminate energy waste. This is a key objective of our global expansion, and we are committed to growing sustainably.
Q Could you offer further insight into how Aptar Pharma is expanding?
A In October 2022, Aptar Pharma announced a global expansion to address the growing needs of the injectable market. This growth relates to both the number of injections administered globally and to the quality of packaging required for increasingly sensitive drugs. This expansion was initiated by upgrading our existing manufacturing sites in Granville and Brécey, with the notable addition of an extension to the Granville factory, dedicated to the production of PremiumFill® and PremiumCoat® injectable components. Our manufacturing site in Congers (NY, US) was also expanded to increase the production capacity for PremiumCoat® film-coated solutions.
Most importantly, Aptar Pharma’s expansion programme includes the construction of a new 19,000 m² factory in Granville, dedicated to the production of vial and prefilled syringe components All the knowledge and experience acquired with the expansion and upgrading of the existing sites has been applied to make our new factory the flagship for Aptar Pharma’s sustainable manufacturing (Figure 2).
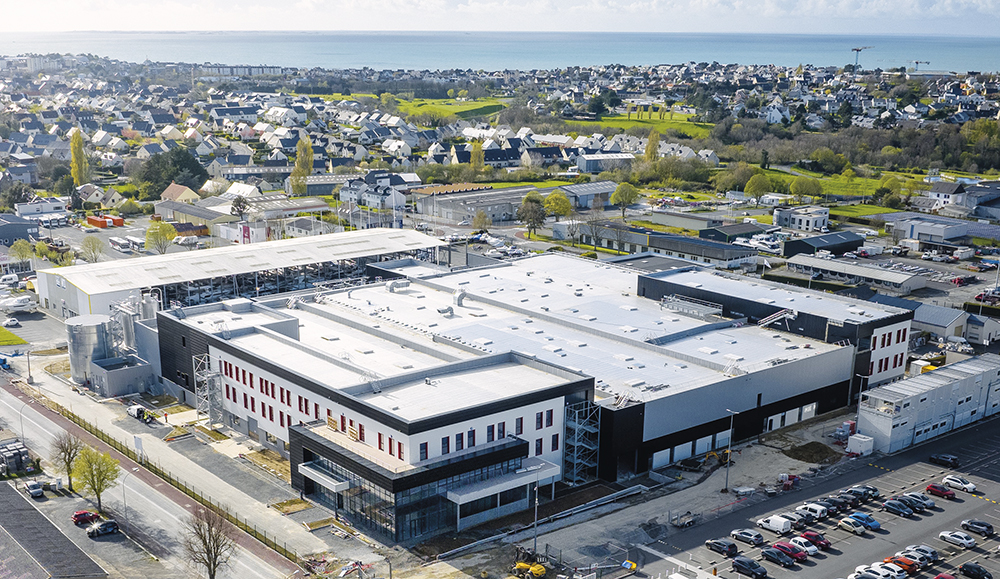
Figure 2: Aptar Pharma’s new factory is intended to be a flagship for sustainable manufacturing.
Q What makes the new factory different?
A Only one boiler, with a capacity of three tonnes per hour, was installed in the new factory. Heat recovery was implemented by default on all relevant equipment, as well as digital tracking of all energy expenditure. Additionally, 2,500 m² of solar panels were installed on the roof of the factory, enabling the production of electricity corresponding to the yearly consumption of 100–200 households. Rainwater collection has also been implemented and would allow the saving of the equivalent of 300 m3 of sanitary water each year.
In order to promote wellbeing at work, the factory was also designed to maximise the use of natural light and focus on ergonomics, improving the health and safety of our employees. During building design, all processes were rethought to reduce the need for carrying heavy loads, exposure to powders and repetitive tasks (Figure 3). This was greatly enabled by the implementation of state-of-the-art automation at all stages of the manufacturing process.
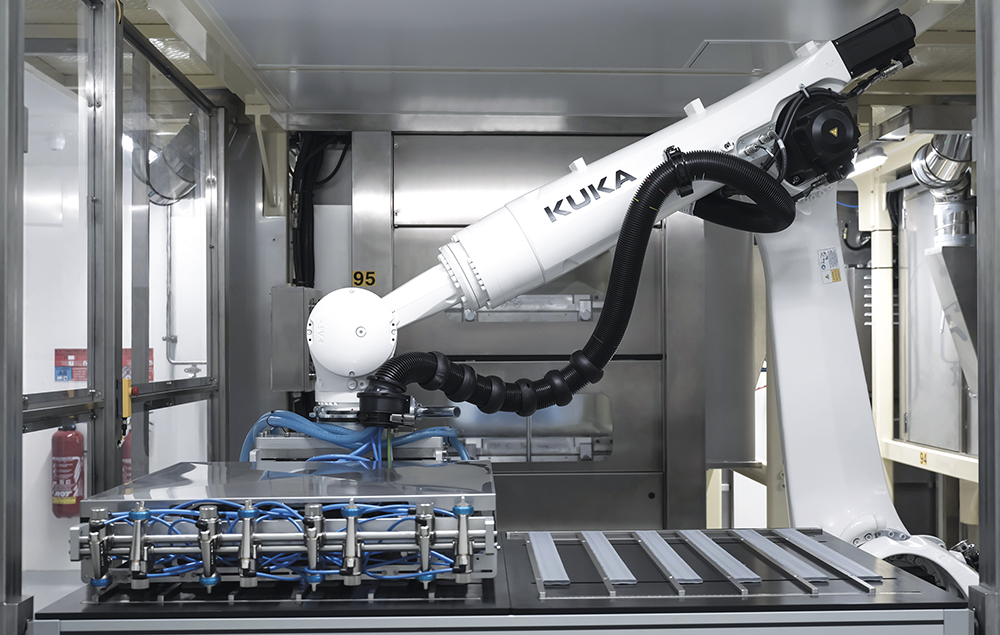
Figure 3: Automation and ergonomics are key features of Aptar Pharma’s expansion plan.
All these sustainability initiatives were recognised by the US Green Building Council’s Leadership in Energy and Environmental Design (LEED) rating system with the silver certification.
Q What is LEED certification and how did you obtain it?
A LEED is a green building certification that promotes lower impact material selection and energy efficient systems and architecture. The LEED certification is a globally recognised symbol of sustainability achievement, backed by an entire industry of committed organisations and individuals paving the way for market transformation in building design and construction. To achieve LEED certification, a project must earn points and address key areas of sustainability, such as carbon, energy, water, waste and transportation, all of which were considered for this expansion project.
The LEED certification also considers the type of land used for building new facilities. Our new factory was built on land that was previously occupied by another factory and therefore did not require the conversion of agricultural or natural fields, demonstrating Aptar’s commitment to reducing the project’s environmental impact.
Q Do you have any concluding remarks?
A As Aptar Pharma continues to expand its injectables manufacturing capabilities worldwide, sustainability remains at the heart of our projects. Beyond manufacturing, we are continuing to develop internal expertise in conducting lifecycle assessments leveraging Aptar’s own Eco Design Tool. This capability supports discussions and preliminary work with customers, helping us collectively identify key levers for enhancing environmental efficiency and create action plans to reduce the environmental footprint of our products.
Whether it is by working on new product designs, sourcing of raw materials or mass balance approaches, we are committed to reducing our impact on the environment so that we can continue to deliver life-saving solutions to patients around the world responsibly.