To Issue 168
Citation: Halbherr P, “Interview: Pharmapack Start-up Spotlight: InnoMedica Accelerating Trials with Novel Nanoparticle Filling”. ONdrugDelivery, Issue 168 (Jan 2025), pp 38–40.
Q Tell us about your innovation and what brings you to Pharmapack for the first time?
A We’re a small company based in Switzerland, working with nanoparticles, with two products currently in clinical trials – one for oncology and one for Parkinson’s disease. We faced a big challenge when it came to filling our nanoparticles in vials for clinical samples, as we initially outsourced the fill-finish of our products. However, the long wait times and high costs at contract development and manufacturing organisations were a major challenge and we simply didn’t have the resources or time to wait. The wait times to find a slot were often six months or more, and the requirement to fill large volumes didn’t align with our step-by-step approach to clinical trials. So, with those costs being extremely high, we decided to develop our own semi- and fully automated system within the same budget to better meet our needs.
“The vials stay closed throughout the process, essentially acting as an isolator within another isolator, which ensures that nothing from the environment can contaminate the vial, significantly improving sterility and safety.”
Our platform allows us to fill closed, sterile vials with nanoparticles in a single step (Figure 1). We use a specially designed needle that pierces the vial’s septum without compromising its integrity, eliminating the need for laser sealing or additional sealing steps. This has streamlined the traditional process, where you would normally have to open, fill and reseal the vial, making our approach much faster, safer and more cost efficient. The vials stay closed throughout the process, essentially acting as an isolator within another isolator, which ensures that nothing from the environment can contaminate the vial, significantly improving sterility and safety.
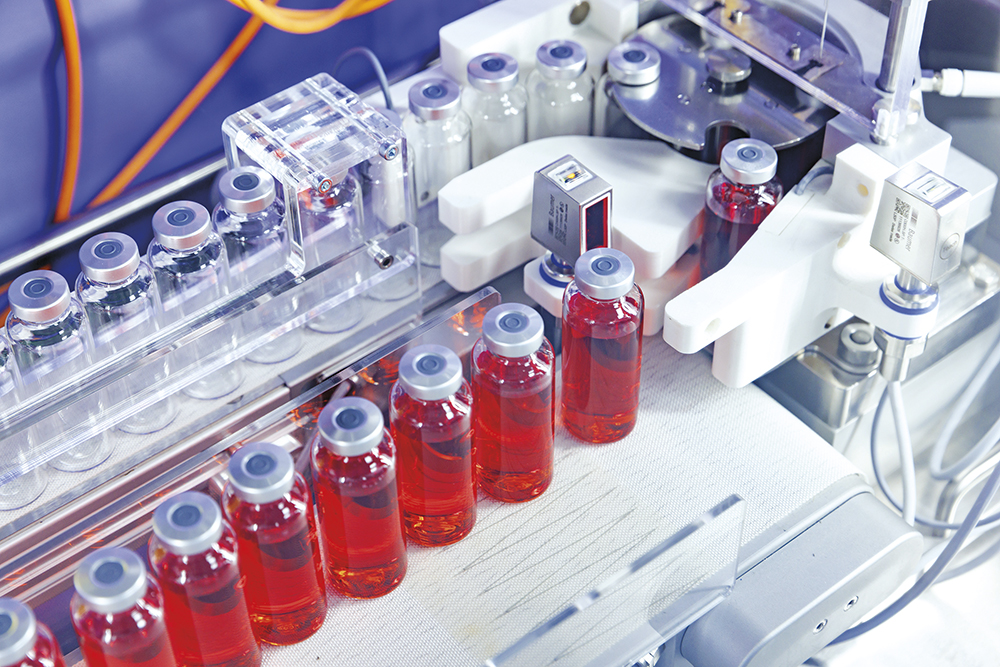
Figure 1: InnoMedica’s innovative closed-vial filling system for clinical and early-market scale production.
To support this technology, we’ve developed two robots – one semi-automated and one fully automated – that can automatically process vials without interruption. While these systems were initially designed for nanoparticle formulations, they’ve proven versatile enough for other liquid pharmaceutical applications as well.
Although the platform is especially beneficial for nanoparticles due to their delicate nature, it can be used for any liquid filling. Crucially, we realised that other biotechs must face similar challenges, and we are ideally placed to help with small and medium batch sizes. That’s why we’re attending Pharmapack – our goal is to help others expedite their new products through clinical trials.
Q How do events like Pharmapack benefit start-ups like InnoMedica?
A Pharmapack provides an excellent platform for showcasing innovations to a targeted audience of industry leaders, potential partners and investors. For us, this is the first time we’re introducing our filling technology to the broader market. It’s an invaluable opportunity to gather feedback, gauge interest and identify potential collaborators. Events like these also foster connections and collaborations within the biotech ecosystem, which is vital for scaling and bringing innovations to market.
Our primary goal with Pharmapack is also to look for buyers for our machines. We developed the technology ourselves because we couldn’t find anything similar in the market that suited our needs. Now that we’ve seen them in action, they are very efficient, fast and compact, which we believe could be of interest to other companies.
Q How do you maintain vial integrity during and after filling and what are the advantages over traditional methods of filling?
A The key lies in the special needles we developed. These needles are thin enough – less than 0.8 mm in diameter – to pierce the septum without compromising its integrity. We’ve conducted rigorous integrity testing, which Swiss medic has approved (Figure 2). This design ensures that the vial remains intact and sterile even after multiple piercings. The entire process is done with filling robots, so is very quick. Our machine can be operational within 30 minutes, making it incredibly time-efficient for smaller clinical batches compared with traditional systems, which often require lengthy set-up times and are optimised for massive production.
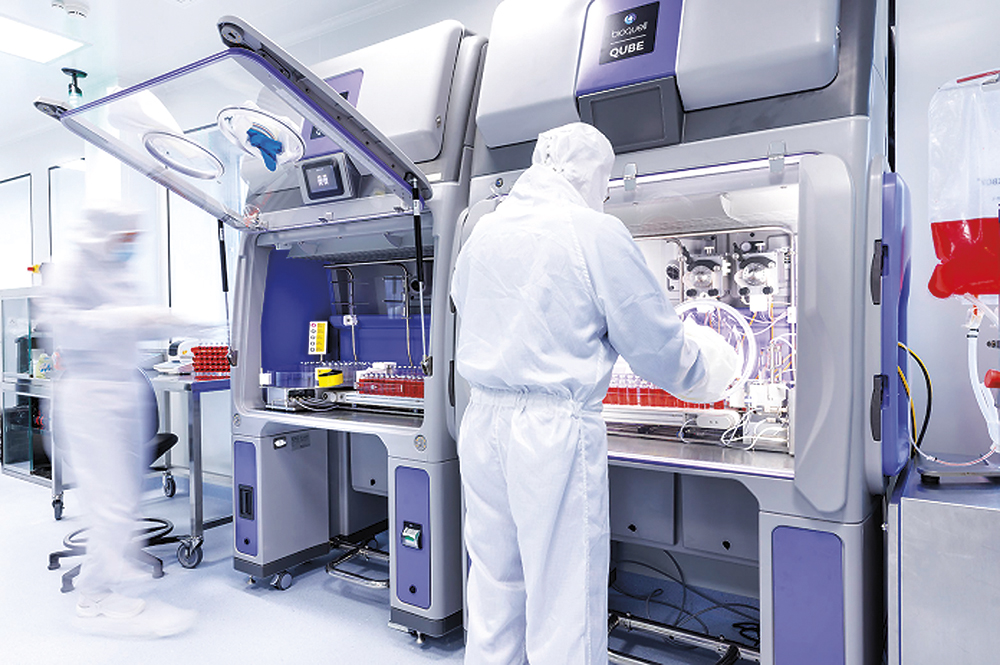
Figure 2: The closed vial filling system can pierce a vial’s septum without compromising container integrity.
The main advantage is that the single step closed-vial filling ensures that the vial’s integrity remains intact while preventing any risk of contamination. The machine’s footprint is also notably smaller, which is crucial, since isolator surfaces are among the most expensive in pharmaceutical manufacturing. Additionally, the isolator we use – made from cost-efficient Bioquell plastic instead of the standard stainless steel – further reduces costs. As a result, the platform is a compact, highly efficient solution that’s ideal for small-to medium batch production in Phase I or II clinical trials.
Q Given the novelty of this method, how do you see regulatory agencies reacting to it and what is the long-term potential of this platform? Could it be scaled for larger production runs or commercial use?
A Closed vial filling is significantly safer than open vial systems but, because it’s relatively new, regulators might need time to adapt their frameworks. Our process is designed to meet existing regulatory standards, but we believe it could eventually pave the way for a shift in how regulators approach filling technologies.
Currently, we’re focused on clinical trials, but the technology has the potential for scaling. For example, we currently handle 20 L batches with ease, and scaling to 50 L batches for market production would be no issue for our fully automated machine. Extremely large batches – such as 200 or 500 L – would require further developments, such as larger isolators or additional filling pathways. Most nanoparticle-based products don’t require massive batch sizes, so our system is well suited for both clinical and early-market applications.
Q What are your goals for next year and hopes for the drug delivery and device industry moving forward into 2025 and beyond?
A In 2025, we’re aiming to scale our technology to meet growing demand for efficient, cost-effective filling solutions, moving beyond clinical trials to early-market production. Securing patents for our needle and process is a key goal, as is forming partnerships to help bring therapies to market faster and more affordably. Our pipeline, of course, remains a priority, with our oncology and Parkinson’s products advancing to pivotal studies.
“Right now, there’s a lot of focus on incremental improvements for patent extensions, but there’s so much untapped potential in repurposing and improving existing drugs – especially those with safety concerns, like cardiac toxicity.”
I’d love to see the industry shift towards more meaningful innovation in drug delivery and manufacturing, with a focus on patient outcomes. Right now, there’s a lot of focus on incremental improvements for patent extensions, but there’s so much untapped potential in repurposing and improving existing drugs – especially those with safety concerns, like cardiac toxicity. Our liposomal doxorubicin, for example, significantly reduces cardiac toxicity, which could have a big impact, particularly for children
We’re also excited to see the continued interest in RNA-based nanoparticle formulations, especially post pandemic. But to really make these therapies successful, we’ll need to address their side effects.
Pharmapack Europe 2025 will take place at Paris Expo, Paris, France, January 22-23, 2025. For more information, visit: www.pharmapackeurope.com.