Citation: Doorakkers R, Plassmann S, “Next-Generation Surface Technologies for Medical Injection Moulding”. ONdrugDelivery, Issue 172 (May 2025), pp 84–87.
Rob Doorakkers of IGS GeboJagema, and Dr Stephan Plassmann of Gloss & Coating, discuss their new Translatio-Coating technology for treating the surfaces of steel parts to achieve microscopic levels of optimisation and open new possibilities for efficiency and quality in drug delivery device manufacturing.
In high-precision injection moulding, every aspect is crucial for efficiency and product quality, from steel parts manufactured with micron-level precision to thermal management, material flow dynamics and optimised process settings. Yet, as injection-moulding technology for drug delivery devices has evolved, one crucial element has remained unchanged – the interaction between molten plastic and steel surfaces. Until now.
THREE LEVELS OF MOULD SURFACE STRUCTURE
Understanding mould surfaces requires distinguishing between three distinct levels of detail. At the highest level, there is the primary structure: the fundamental shape and dimensions defined by computer-aided design data. The secondary structure encompasses the visible manufacturing marks: the patterns left by milling and electrical discharge machining processes, as well as manual finishing processes, such as polishing and bead blasting. But there is a third level that plays a crucial role in the moulding process: the nanostructure.
This nanostructure, typically less than one micron deep, is the actual surface that molten plastic comes into contact with when it fills the mould cavity. For years, it was not possible to adjust this tertiary structure without altering the secondary structure. However, advances in technology now allow us to deliberately modify these nanoscale surface characteristics.
“THE ABILITY TO CONTROL THE NANOSTRUCTURE HAS PROVEN POWERFUL IN OPTIMISING THE DEMOULDING PROCESS.”
WHY ALTER THE NANOSTRUCTURE?
The ability to control the nanostructure has proven powerful in optimising the demoulding process. Most moulded products tend to stick to the mould. By fine-tuning these surface characteristics, mould manufacturers can significantly alter how much a product adheres to the mould surface during release. This delivers two key results.
Firstly, it reduces the forces required to overcome sticking during product ejection. This is crucial because when a product is ejected, its core is still relatively soft and susceptible to deformation. Lower demoulding forces mean less stress on the product, preventing unwanted geometrical changes that can affect product quality.
Second, this smoother ejection process allows for reduced cooling times. As the product can be safely removed from the mould earlier in its cooling cycle, overall cycle time decreases, leading to improved production efficiency.
Furthermore, this technology offers several advantages that make it an excellent choice for high-precision moulding of drug delivery devices:
- The technology performs mechanical surface modification and does not introduce chemical changes to the mould
- The dimensional integrity of the moulded product remains completely unchanged and there is no effect on tool parting lines
- The substantial reduction in demoulding forces is uniform across the product, ensuring even product removal and appearance
- The technology allows for precise control of the optical effect on the moulded product, ranging from no effect at all to distinctly visible changes in appearance.
UNDERSTANDING THE IMPACT OF SURFACE ROUGHNESS
As stated, nanostructure modification can make surfaces either rougher or smoother to minimise demoulding forces. However, the relationship between surface roughness and demoulding force is more complex than one might assume. As illustrated in Figure 1, this relationship can be divided into two distinct regions: adhesion and deformation. The graph shows how demoulding force changes with surface roughness, revealing an optimal point where these forces are minimised.
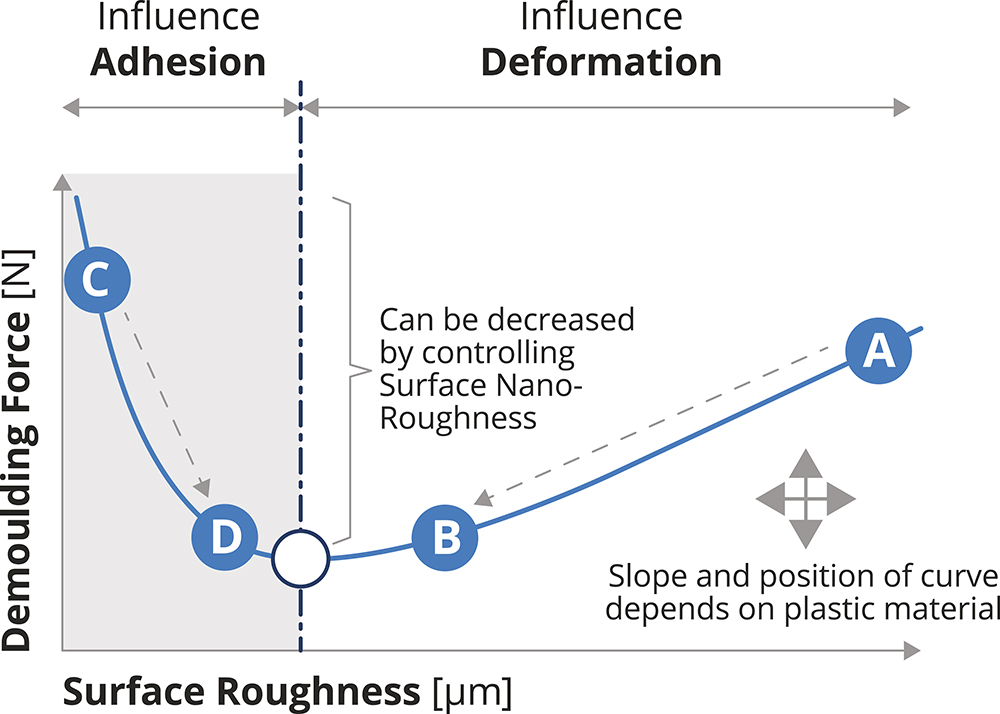
Figure 1: The relationship between surface roughness and demoulding force shows an optimal point where forces are minimised through precise nanostructure control. A – the roughness of a VDI3400 ERO 24 structure. B – the ERO 24 structure nanostructured and thus reduced roughness. C – typical ASPI2 high-gloss finish. D – a nanostructured finish of C. In A–B the roughness is reduced and in C–D the roughness is increased, moving to the sweet spot without compromising the appearance of the plastic parts.
In the adhesion region, extremely smooth surfaces can actually lead to higher demoulding forces due to increased surface contact area. As roughness increases, these forces initially decrease until reaching an optimal point. However, if the surface becomes too rough, it enters the deformation-dominated region, where demoulding forces begin to rise again due to more aggressive interactions between the plastic material and the surface texture.
“THROUGH PRECISE CONTROL OF SURFACE NANO-ROUGHNESS, IT IS POSSIBLE TO ENGINEER THIS OPTIMAL CONDITION, WHERE DEMOULDING FORCES ARE MINIMISED WHILE MAINTAINING PRODUCT QUALITY.”
The key to optimal demoulding lies in finding the sweet spot between these two extremes, indicated by the white circle on the graph. Through precise control of surface nano-roughness, it is possible to engineer this optimal condition, where demoulding forces are minimised while maintaining product quality.
A CASE STUDY ON NANOSTRUCTURE EFFECTIVENESS
Several of IGS GeboJagema’s clients are already using this surface modification technology to gain a significant competitive edge in pharmaceutical manufacturing. While these specific applications are confidential, testing data clearly demonstrate the technology’s transformative impact.
To quantify these benefits, a specialised test tool was used to measure the force required to remove plastic parts from the mould. This tool measures the torque (twisting force) required during ejection to reveal how strongly the plastic sticks to the mould surface. In a comparison of demoulding forces for parts with standard high-gloss polished surfaces (SPI-A2) and those with nanostructure-treated surfaces, the peak torque demoulding force for the treated parts was approximately 40% less than for the parts with polished surfaces. This striking reduction in demoulding force translates directly to less stress on moulded components, faster cycle times and improved product consistency. These results illustrate why leading manufacturers are increasingly adopting this innovation to stay ahead in the demanding drug delivery device market (Figure 2).
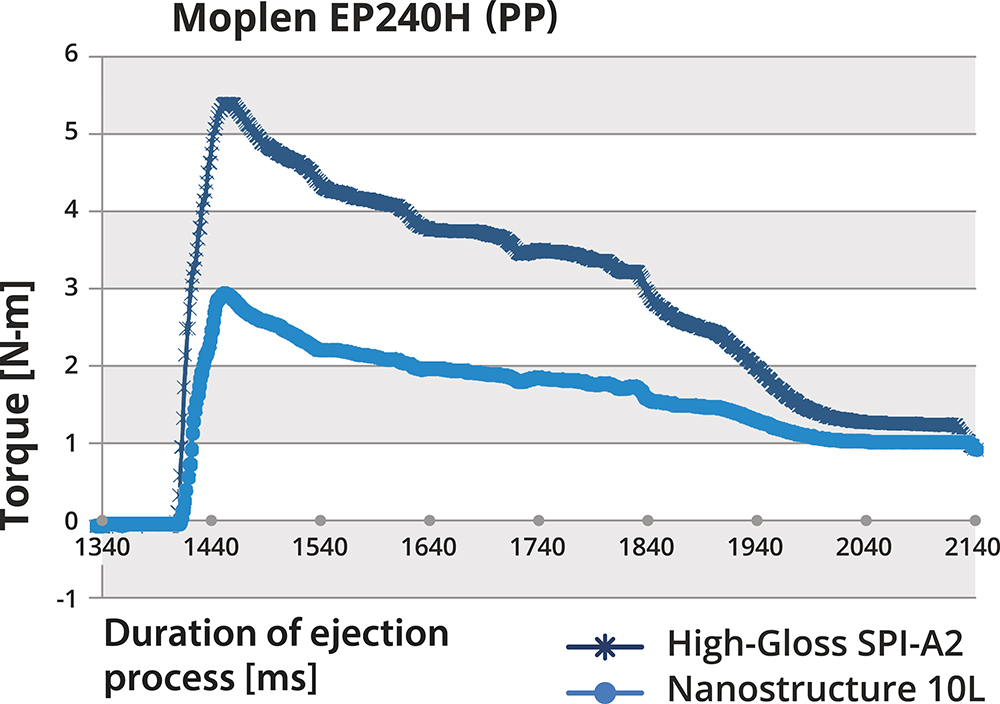
Figure 2: Nanostructure-treated surfaces require 40% less force during ejection than standard high-gloss surfaces.
OPTIMISING SURFACE CHEMISTRY
In addition to modifying the nanostructure, a second innovation can help to further reduce demoulding forces as well as residue formation: the Translatio-Coating. Coatings have been used in the industry for many years, and the challenges are well known. Traditional coatings typically add around 2 μm of thickness to tool surfaces – a factor that must be accounted for during the initial engineering phase. This becomes particularly problematic when demoulding issues arise during validation or throughout the tool’s operational lifetime. Applying additional coating to a mould that is already operational is extremely challenging, if not impossible, without compromising the tool’s critical dimensions and tolerances.
Temperature limitations present another significant barrier. Many coating processes require high-temperature application, which might exceed what the tool can endure without having a detrimental effect on the quality of the steel.
THE NOVEL TRANSLATIO-COATING
The development of the Translatio-Coating started from the observation that new moulds typically require a ‘run-in’ period of several hours to days before reaching optimal production conditions. During this time, a nanometre-thin layer of plastic gradually builds up on the tool surface until reaching a steady state where deposition and removal rates balance. This observation raised the question, what if it were possible to deliberately create this optimised surface layer from the start, using the same plastic material that forms the final product? In other words, what if a specialised coating could be applied?
“TRANSLATIO-COATING ELIMINATES THE BIGGEST CHALLENGES OF COATINGS. BECAUSE IT IS ULTRA-THIN, IT DOES NOT AFFECT TOLERANCES, AND IT CAN BE APPLIED WITHOUT SIGNIFICANT HEAT. THIS ALLOWS THE TRANSLATIO-COATING TO BE RETROFITTED ONTO ANY MOULD AT ANY POINT.”
The Translatio-Coating is the answer to this question. This technology deliberately applies an ultra-thin layer (140–150 nanometres) of the product’s plastic material onto the mould surface. During testing, this “native” coating proved to significantly reduce demoulding forces, as can be seen in Figure 3. Critically, this new technology eliminates the biggest challenges of coatings. Because it is ultra-thin, it does not affect tolerances and it can be applied without significant heat. This allows the Translatio-Coating to be retrofitted onto any mould at any point. It provides advantages to both existing and new moulds:
- Immediate Production Readiness: Tools achieve full production capacity from the first shot, eliminating run-in time.
- Enhanced Product Quality: The system improves both demoulding characteristics and geometric conformity.
- Reduced Maintenance: Significant decrease in plastic residue formation on tool surfaces, which lengthens the mould maintenance cycle.
- Regulatory Compliance: Unlike any other coating, the Translatio-Coating is automatically US FDA and EMA approved because it is made from the same resin as the moulded product itself (as confirmed by Fourier transform infrared spectroscopy measurements), which eliminates additional certification requirements for medical injection moulding processes.
- Reduced Cycle Time: Shorter production cycles increase overall manufacturing efficiency.
- Improved Mould Filling: The coating enhances material flow by 20–30%, resulting in more consistent part quality and reduced defects.
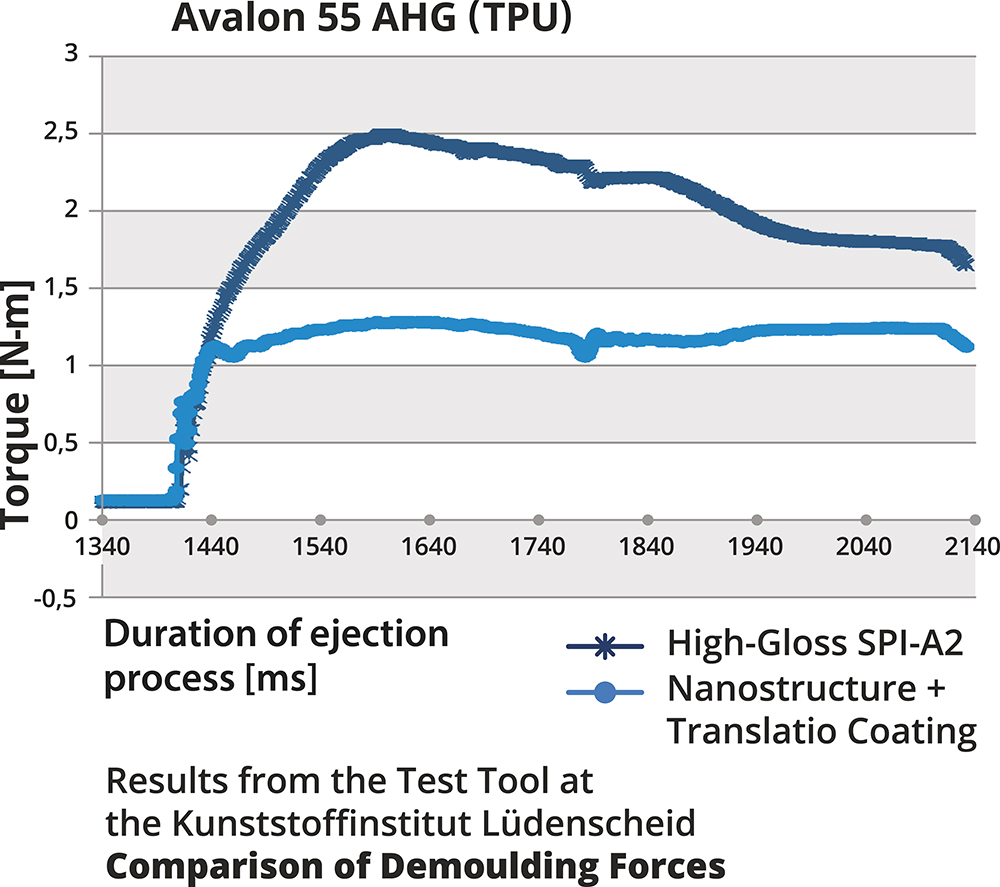
Figure 3: Nanostructure modification combined with Translatio-Coating significantly reduces demoulding forces compared with standard high-gloss surfaces.
CONCLUSION
The convergence of nanostructure modification and Translatio-Coating technology marks a milestone in injection-moulding capabilities. These innovations address long-standing challenges in medical device manufacturing, offering manufacturers increased control over product quality while improving operational efficiency.
What makes these developments particularly significant is their practical implementation. Both technologies can be applied to existing tools, allowing manufacturers to enhance their current production capabilities. As the medical industry continues to evolve, IGS GeboJagema’s surface optimisation technologies not only solve current manufacturing challenges but also set the bar for future injection moulds for medical devices.