Citation: Drexler S, “Automating Under Uncertainty – Good Practices”. ONdrugDelivery Magazine, Issue 96 (Apr 2019), pp 22-26.
Simon Drexler discusses lessons learned and good practices when dealing with uncertainty at the various stages of automation development for drug delivery device manufacturing.
Making decisions whilst dealing with uncertainty is a challenge we all face every day in both our personal and professional lives. Such decisions can be even more taxing when capital expenditure is involved, which is often the case when driving growth initiatives and is nearly always the case when investing in automation.
One could make the argument that we deal in more uncertainty today than we have ever before. Information travels instantly, therefore our local area of influence is impacted by events that occur around the world. The ongoing trade dispute between the US and China impacts two of the world’s largest economies, creating uncertainty around the world. The EU is working through its own uncertainty with the ongoing Brexit negotiations. While these events are occurring, mainstream news organisations are consistently speculating on which event will pull the world economy into its next recession.
The challenge then is that, even in these uncertain conditions, business leaders cannot be content with the status quo.
“The end vision for automation is especially important as it affects
the foundational technologies chosen and processes developed.”
They must continue to strive for growth and drive towards what is best for their stakeholders and shareholders. Therefore, they are tasked with finding opportunities to strengthen and grow business. The main difficulty is to ensure that the uncertainty present in the marketplace does not drive them to make a wrong turn. “By definition there are no longer any ‘best practices’ that can guarantee success for an organisation; there are only good practices that we can stumble upon through experimentation.” This excerpt from Alison Randle’s article, “Three Proven Ways To Navigate Uncertainty”, effectively frames the fact that there is no silver bullet to solve a problem, only hard-earned lessons that can be applied from those that have experienced similar situations before.
Uncertainty in automation, as seen in Figure 1, is driven from one of three sources:
- Product: Largely due to the changes and revisions that occur through the design lifecycle. For instance, a dry powdered inhaler design may still be evolving in response to user feedback to design concepts or subcomponent manufacturing capabilities.
- Process: Evolving how production occurs at different volumes, with each stage bringing unique challenges. For instance, at different production volumes of an inhaler, a semi-automated or fully automated process could be justified over a manual process step, but each may have a different process verification step.
- Forecast: The difficulty in predicting the market conditions for the product you are producing. For instance, there is uncertainty around how closely the actual production launch volumes of a new respiratory device will match the marketing team’s projections.
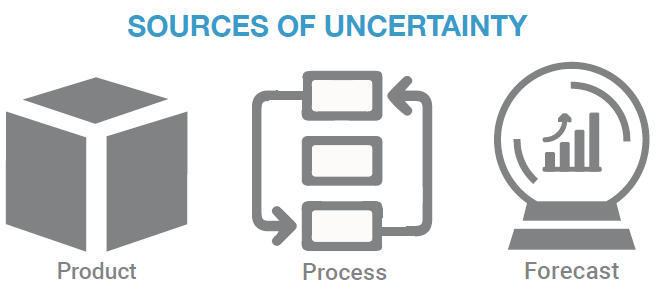
Figure 1: Uncertainty in automation is derived from product, process or forecast.
There are several good practices to apply when determining a path to automation while in uncertain conditions. Each of them sounds simple on paper but each is difficult to apply in practice – easy to say, hard to do.
AUTOMATING UNDER UNCERTAINTY: GOOD PRACTICES
Good Practice 1 – Focus on the Finish Line
In the development phase it is critical to understand the end vision, or finish line, in order to make good decisions in the short term. This also happens to be one of Steven Covey’s “7 Habits of Highly Effective People” from his bestselling book. He says: “Begin with the End in Mind means to begin each day, task, or project with a clear vision of your desired direction and destination, and then continue by flexing your proactive muscles to make things happen.”
The end vision for automation is especially important as it affects the foundational technologies chosen and processes developed. The challenge here is that it is often hard to see the forest for the trees when you are working towards a launch or next deadline. You may not be thinking of the ultimate end, but only about a successful next step – a common mistake.
“Each of the good practices outlined work in conjunction with each other, similar to the project management triangle.”
Good Practice 2 – A Stable Foundation
Borrowing wisdom from the construction industry, the foundation is the most important selection you can make. The biggest reason for this is that any mistakes you make in the foundation will only get worse as you go up, known as compounding defects. In practice, selecting a foundation that adapts to the ever-changing needs of the business is in the best interests of all parties, even if at the beginning it seems to be more than is required.
Good Practice 3 – Re-align the Wheel
“Don’t reinvent the wheel, just re-align it” is a quote from Anthony D’Angelo. In the manufacturing and automation world, you should try to not re-invent something if you don’t have to, as doing so takes capacity away from things that are core to your process and adds additional risk. The “re-alignment” part of the quote is very important – often you only need a tweak to an existing design rather than a fundamentally novel approach. It is often worth taking an impact to expected performance to use an off-the-shelf (OTS) piece of equipment. In all cases, you’ll get to where you are going faster if you can use proven components.
It is a common misapplication to look at each good practice in isolation. However, each of the practices outlined work in conjunction with each other, similar to the project management triangle. Knowing the finish line helps when choosing the right technologies, and knowing the right technologies helps to define the finish line and select the right foundation.
APPLYING GOOD PRACTICES
Development Phase
The product development phase is the most challenging phase for automation because uncertainty is high in all three of product, process and forecast. Typically, something is being attempted for the first time whether it be a new product, process or market:
- Product is in development, waiting for information from various groups to complete the first market-ready revision. Sourcing, manufacturing, product testing, design or all of the above are making decisions before the product is complete as the team is trying to move fast to take advantage of the opportunity identified.
- Process is uncertain because no products have been made in volume for market. The lack of definition on the product itself leaves a number of questions about the process of putting it together.
- Forecast is relatively unknown because, without response and adoption from the end user, it is difficult to pinpoint your production levels.
Starting with the end in mind, choose technology that you can grow from development quantities to high volume. Any lessons learned, intellectual property (IP) generated or skills fostered in the workforce can now be applied later in the production process. As shown in Figure 2, a component of a high-volume concept can be used for product and process development – in this case, to build process knowledge on the equipment for the future.
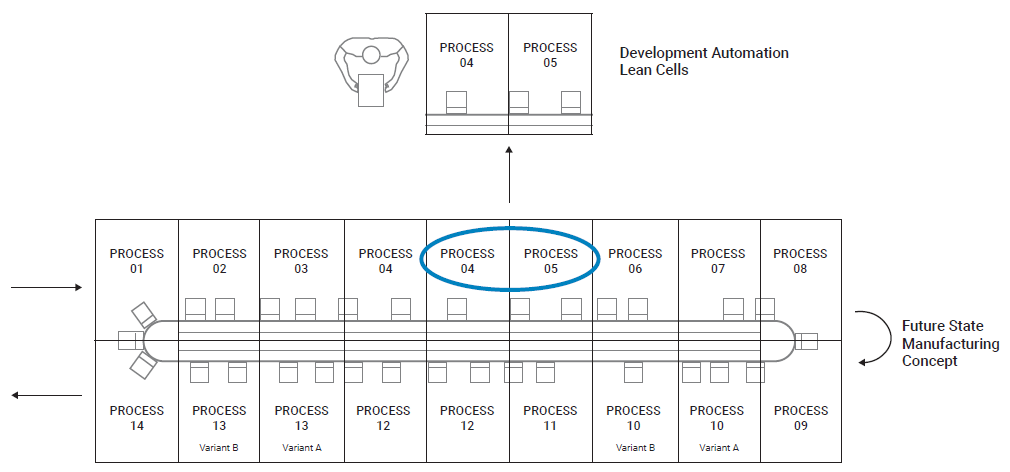
Figure 2: With the finish line in mind, select appropriate technologies and automation early to assist with the development phase.
Flexibility in foundational technologies is the most important decision you can make in the development phase.
Uncertainty is high; therefore, make choices that give you room to adapt as the picture becomes clearer. Stability is equally important in development so that time and effort is not wasted on troubleshooting, keeping the focus squarely on building your IP. While development is underway, it is helpful to mix manual and automated processes, as shown in Figure 3. An appropriate balance minimises capital investment, promotes discovery, provides control of critical processes, and facilitates quick responses to product and process changes.
There is a bias towards developing custom systems out of the gate. However, even if the OTS component is performance limited, it is better to work with it in the development phase. The reason is the uncertainty level is high so even if you build something custom-made it may not be the right thing. Using OTS components helps you to learn more about product and process, as well as giving time for forecasting.
It is best to select platforms and technologies that interface well with standard automation components and practices. This allows you to build up your expertise by focusing on the parts of the process that are underdeveloped while relying on proven technologies where possible. Note that OTS technologies may drive some design decisions for you as you work through the production process.
In the development stage it is critical to have an end vision in mind, so select flexible and stable foundational technologies and avoid developing custom process technology while so much uncertainty remains present. The aim is to dedicate all efforts to product and process development to remove uncertainty, using automation to execute common steps and processes that cannot be done manually. The goal is to work with the same technologies now that are planned for use in later phases.
This will save time and money.
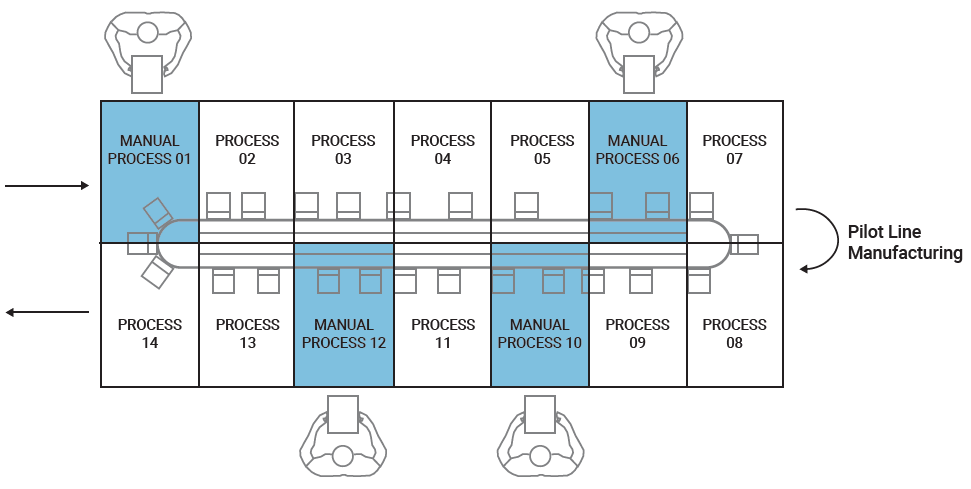
Figure 3: Combining manual and automated processes will minimise capital investment but promote development of a manufacturing platform that will be representative of the final commercial solution.
Commercialisation Phase
Time is very important as we shift into the commercialisation stage, where it is all about speed. Uncertainty begins to decline, while market traction and knowledge increases. The most important thing to know as you scale-up is that you may need to make adjustments to your plan. Regardless of the amount of preparation, the reality is that the physical interaction of product and equipment might not go as expected as speed and volumes increase. The positive thing to note about this phase is that some of the risk will start to subside:
- Product is now in a mature form as we prepare for launch.
- Process for manufacturing is defined but higher-volume manufacturing may dictate changes.
- Forecast is the highest source of uncertainty, as lessons for market adoption have not yet been learned in volume.
For the finish line, it is most important to define the long-term manufacturing strategy. Centralised manufacturing will drive different decisions than a decentralised local-for-local approach. This decision will have the most significant impact on the scale-up of an automation system. Volumes change significantly between the two options, which drives component selection and process development decisions.
Maintaining flexibility is a key consideration. You have uncertainty in process design, you need to leave room for iteration. This is where the major advantage of a flexible foundation benefits machine builders and their partners. Understanding that things are unlikely to go exactly as planned, technology that allows processes to be re-ordered, replicated, adjusted or swapped out leaves room for product demand increases, product changes or variant introductions, efficiency improvements, etc, as shown in Figure 4.
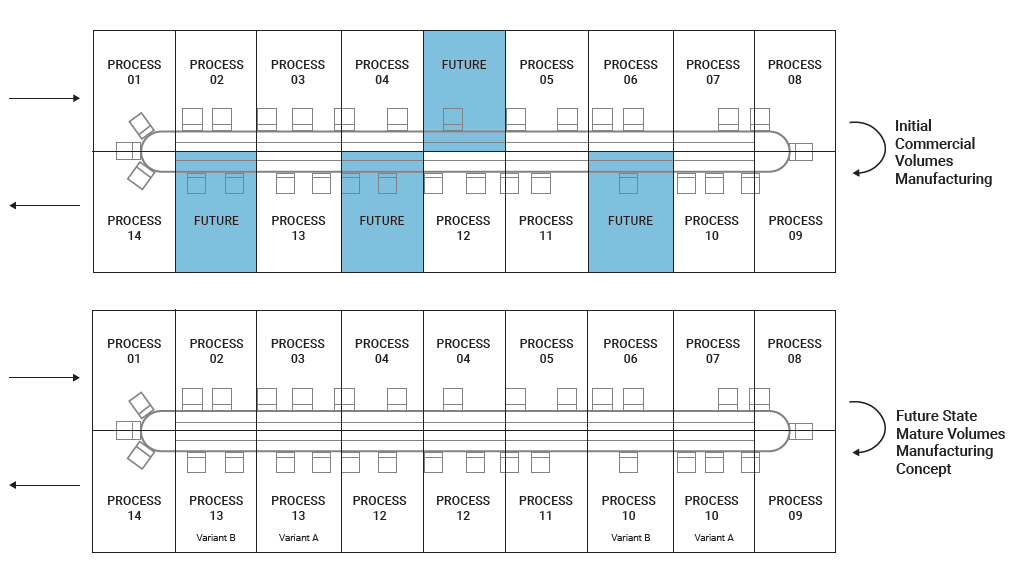
Figure 4: Flexible technology that allows processes to be re-ordered, combined, replicated, adjusted, or swapped-out, anticipates volume increases, product changes or variants, and efficiency improvements.
Technologies that are future proofed in this way are extremely advantageous. In scaling up production we want to avoid re-aligning the wheel where possible, but on the other hand there is more scope to do so. As volumes increase, the case for custom process technologies increases, but duplicating OTS equipment or re-aligning components may still be a viable approach.
A manufacturing platform that can accommodate various process technologies in both process control and accuracy is important for keeping options open.
Throughout commercialisation, speed is the critical driving factor. A clear understanding of the overall manufacturing strategy will drive the correct decisions to reach the finish line faster. Flexibility in the chosen technologies remains critical because volume drives new assembly interactions that are unlikely to unfold as expected.
Continued use, and even replication, of the OTS technologies used in development shares lessons where possible, progresses automation development faster and, most importantly, allows focus to be on production.
Mature Phase
The greener pastures of decision making under uncertainty is the high-volume phase.
We’ve gone through the difficulties of product and process developments and are now benefitting from the smart decisions made in earlier stages. It is time to grow volume in less uncertain conditions:
“Moving through the stages of development, the benefits
of focusing on the finish line, choosing flexible and stable
foundational technologies, and re-aligning not re-inventing
the wheel are realised in both time and resources expended.”
- Product is proven in market; iterations are fewer and further between.
- Process is known from commercialisation efforts.
- Forecast is largely known but susceptible to uncertainty from external factors.
When applying good practices, the focus shifts from development to lifecycle management. Stability and easy-to-use technologies become more important as the process experts are re-deployed to other areas of the business. Manufacturers require flexibility in capacity only as they seek to balance a level loaded production volume with surge capacity. Custom processes now bear fruit due to volume and the lack of uncertainty in other areas.
CONCLUSION
The ideal automation progression from development through high volume is shown in Figure 5. The process begins with a development cell that is a component of the concept for high-volume automation.
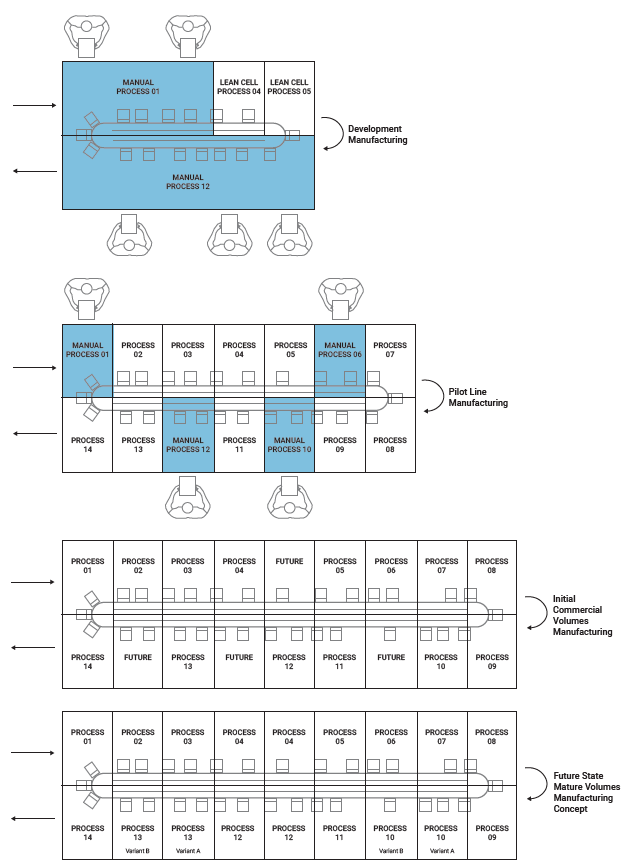
Figure 5: Start with the end in mind – automation progression from development through to mature manufacturing.
The move from low-volume to high-volume occurs using foundational design standards and building blocks to efficiently build the automation cell. Figure 5 illustrates the main advantage of starting with the end in mind. Selecting the right foundation allows you to travel down either the centralised or decentralised path. Modular foundations enable growing a centralised foundation, whether it be by physically growing it or investing in incrementally larger systems while re-deploying the smaller systems to other products. A decentralised manufacturing strategy requires that the platform aligns with the skillset of the support network where the system will be deployed, whether that be the control system or other components. Asynchronous foundations allow for straightforward replication of technology within a larger cell, but custom development is not discouraged in mature volume stages. There is no need to make performance concessions here as the level of uncertainty is low.
Moving through the stages of development, the benefits of focusing on the finish line, choosing flexible and stable foundational technologies, and re-aligning not re-inventing the wheel are realised in both time and resources expended. To reach our end goal as quickly as possible and begin realising the full benefit of automation, we must focus on making incremental progress towards the finish line every step of the way. We all have an incredible opportunity in front of us with the advancements in automation technology – do not let a little uncertainty get in the way.